This article provides a comprehensive examination of heat-treated A2 tool steel and stainless steel, helping decision-making for heat treated steel.
Introduction
Heat treatment for steel is basically controlled heating and cooling to transform its internal structure, like a metal makeover for strength, hardness, or other desired properties.
A2 tool steel and stainless steel are distinct alloys with different strengths. A2 tool steel offers toughness and wear resistance for tools like knives, while stainless steel prioritizes corrosion resistance for applications like cookware.
Fundamentals of Heat Treatment
Defining Heat Treatment and Its Objectives
Heat treatment is a controlled process of heating and cooling steel to alter its physical and mechanical properties. It involves a precise three-step process:
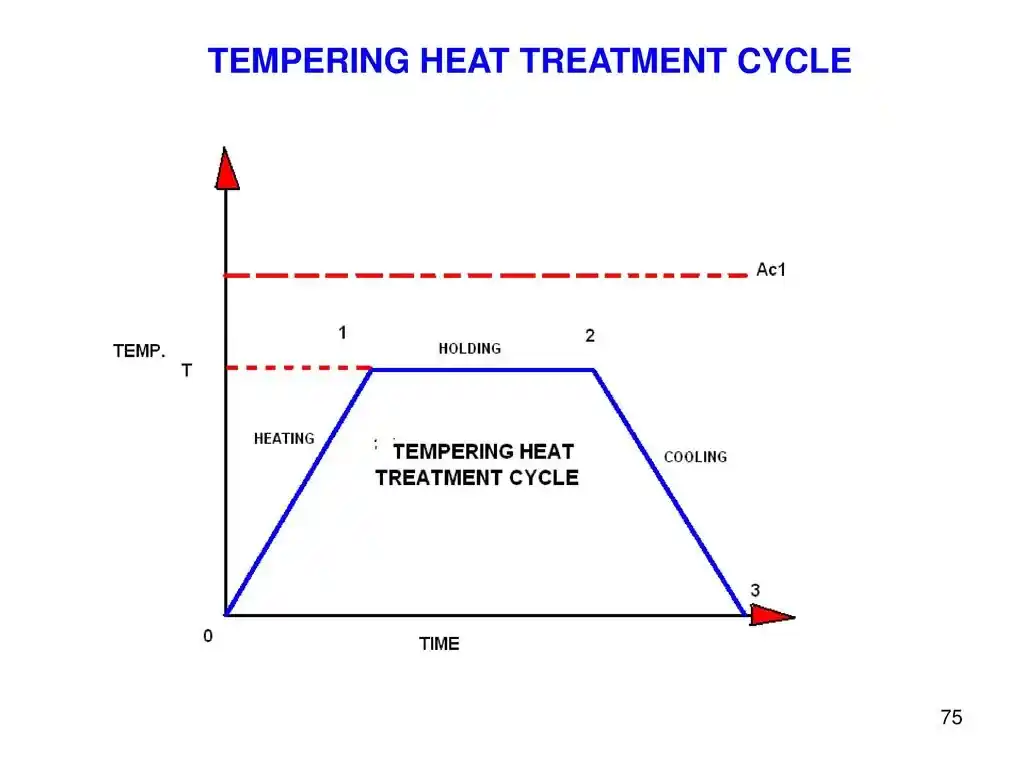
Source: slideplayer.com
- Heating: The steel is raised to a specific temperature based on the desired outcome. This temperature alters the internal atomic arrangement of the steel.
- Holding: The steel is held at this elevated temperature for a predetermined time to ensure uniform heating throughout the material. This allows the desired atomic rearrangements to occur fully.
- Cooling: The steel is then cooled at a controlled rate, which plays a crucial role in determining the final properties. Different cooling methods, like air cooling, quenching in water, or furnace cooling, are employed to achieve different results.
The primary objectives of heat treatment are to:
- Enhance Strength and Hardness: This is crucial for tools, machinery, and building components that need to withstand heavy loads and wear.
- Improve Ductility and Toughness: Heat treatment can make steel more bendable without breaking (ductility) and more resistant to shattering (toughness), important for components that absorb impact or need shaping.
- Optimize Machinability: By adjusting the microstructure, heat treatment can make steel easier to cut, drill, and shape.
- Achieve Specific Properties: For a given application, the ideal steel might require a balance of hardness, toughness, and other properties. Heat treatment allows for fine-tuning to meet these exact needs.
Critical Parameters of Heat Treatment
The success of heat treatment relies heavily on three critical parameters:
- Temperature: Heating the steel to a specific temperature range triggers the desired changes in its microstructure.
- Time: Holding the steel at that temperature for a sufficient time ensures uniform transformation throughout the material.
- Cooling Rate: The rate at which the steel cools after reaching the target temperature dramatically affects its final properties. Rapid cooling (quenching) can lead to hardening, while slower cooling allows for a more balanced structure.
Phase Transformation Behavior in Heat Treated Steel Alloys
Steel is an alloy primarily composed of iron and carbon. During heat treatment, the high temperature causes these elements to rearrange themselves and form different crystal structures called phases.There are several key phases in steel:
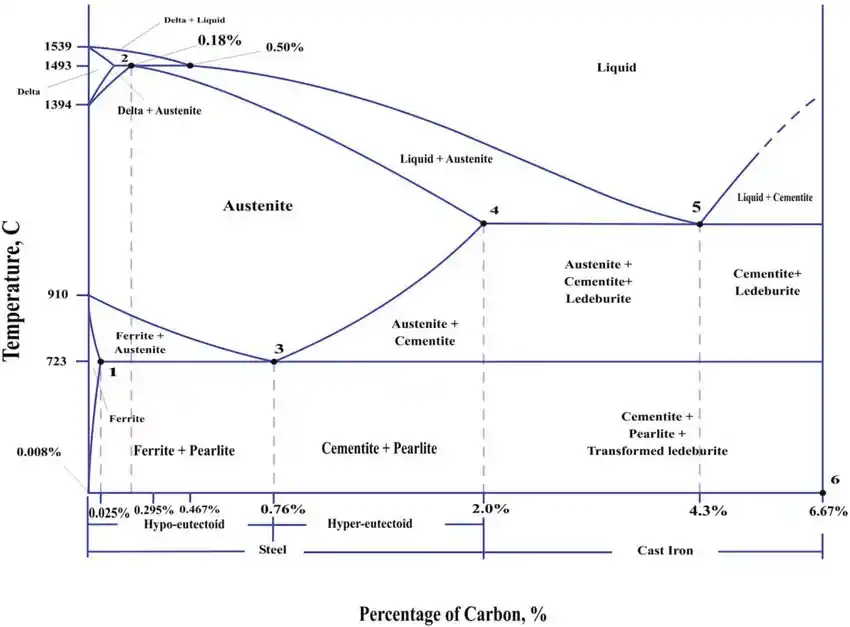
Source: researchgate.net
- Ferrite: A soft, ductile phase of iron.
- Austenite: A high-temperature phase of iron that can dissolve a significant amount of carbon.
- Cementite: A hard, brittle iron-carbon compound.
- Pearlite: A lamellar structure composed of ferrite and cementite, offering a balance of hardness and toughness.
Heat Treating A2 Tool Steel
Step 1. Preheat Preparation
Surface Inspection and Cleaning: Before heating, thoroughly clean the A2 tool steel to remove any dirt, oil, or contaminants that could affect the heat treatment process. These can lead to uneven heating or surface defects.
Annealing as Needed: If the A2 steel is in a pre-hardened state from previous use or machining, it might benefit from a pre-heating annealing step to soften it and ensure consistent response to the following hardening process.
Step 2. Austenitizing
Heating Procedures and Temperature Range: Heat the A2 tool steel slowly at a rate not exceeding 400°F (222°C) per hour to a temperature range of 1725-1800°F (941-954°C). This slow heating minimizes warping and cracking.
Proper Soaking Time: Once at the target temperature, hold the steel for a specific duration to ensure uniform heating throughout its thickness.
A common rule of thumb is 30 minutes per inch (25.4mm) of maximum thickness, with a minimum hold time of 2 hours.
Step 3. Quenching
Choice of Quenching Medium: A2 tool steel is air-hardening, meaning still air is a suitable quenching medium.
However, for thicker sections or for achieving deeper hardening, faster quenching methods like pressurized air or interrupted oil quenching can be used.
Techniques for A2 Tool Steel Quenching: When air quenching, ensure the steel is placed in a location with minimal air movement for a consistent cool-down.
For faster quenching methods, specific techniques are required to avoid cracking. Consulting a heat treatment professional is recommended.
Step 4. Tempering
Purpose and Temperature Range: After quenching, the steel will be very hard but also brittle. Tempering involves reheating the steel to a lower temperature range (375-425°F / 190-220°C) and then cooling it again. This reduces brittleness while retaining some hardness.
Duration and Cooling Techniques: Hold the A2 tool steel at the tempering temperature for a set time (often 1-2 hours) and then cool it in air or a slow cooling medium like still air or a furnace. The specific holding time may vary depending on the tool size and desired properties.
Heat Treating Stainless Steel
Unlike A2 tool steel, heat treating stainless steel involves more considerations due to the various stainless steel grades and their unique properties.
Step 1. Preheat Preparation
Surface Cleaning and Degreasing: Remove any dirt, oil, or grease to ensure even heating and prevent surface imperfections.
Removal of Surface Contaminants: Certain contaminants like heavy oxides or scale can be detrimental during heat treatment. Depending on the severity, techniques like sandblasting, pickling, or grinding might be necessary.
Step 2. Austenitizing
Optimal Heating Parameters for Stainless Steel: Different stainless steel grades require specific austenitizing temperatures. Heating too high can lead to grain coarsening, while heating too low might result in incomplete austenitization.
Preventing Sensitization: Some stainless steel grades are susceptible to sensitization, a phenomenon where chromium carbides form at grain boundaries during heating. This reduces corrosion resistance. Rapid cooling after austenitizing helps minimize this risk.
Step 3. Quenching
Medium Selection and Control of Cooling Rates: The selection of the quenching medium (water, oil, or air) and the cooling rate significantly impact the final properties of stainless steel.
Faster quenching leads to a more martensitic structure, which is harder but less ductile. Conversely, slower cooling promotes a more ferritic or austenitic structure, offering better corrosion resistance and ductility but with lower hardness.
Achieving Desired Hardness and Microstructure: The interplay between austenitizing temperature, quenching medium, and cooling rate dictates the final microstructure and, consequently, the hardness and other mechanical properties of the stainless steel.
Step 4. Tempering
Tempering Temperature Range: Similar to A2 tool steel, tempering stainless steel involves reheating to a lower temperature range (specific to the grade) to improve toughness and reduce brittleness obtained from quenching. The tempering temperature significantly influences the final properties.
Influence on Stainless Steel Properties: Tempering alters the microstructure of stainless steel, impacting its hardness, toughness, and corrosion resistance.
Higher tempering temperatures result in a softer but more corrosion-resistant material, while lower tempering temperatures retain more hardness but might compromise some corrosion resistance.
Pros and Cons of Heat Treated Steel
Heat treatment offers a powerful tool for manipulating the properties of steel, but it’s not without its drawbacks.
Pros | Cons |
---|---|
Enhanced Strength and Hardness | Increased Processing Costs |
Improved Ductility and Toughness | Dimensional Changes |
Optimized Machinability | Potential for Brittleness |
Tailored Properties | Expertise Required |
Applications of Heat Treated Steel
Heat treated steel’s strength and versatility make it crucial to many fields.
- Tool and Die Making: Punches, dies, and cutting tools rely on heat treated steel’s toughness and wear resistance.
- Automotive Industry: Engine and drivetrain parts benefit from heat treated steel’s strength, fatigue resistance, and wear resistance.
- Aerospace Sector: Lightweight yet strong airframe components and high-temperature resistant engine parts are made from heat treated steel.
- Construction: Heat treated steel strengthens concrete structures and provides reliable structural components for buildings and bridges.
- Engine Parts (Beyond Automotive): Engine components across various industries use heat treated steel for its strength, wear resistance, and durability.
Conclusion
Heat treatment transforms internal structure of metal, unleashing a range of desirable properties. A2 tool steel and stainless steel are distinct alloys, each with its own specialty.
Understanding the distinct properties of A2 tool steel and stainless steel, along with the transformative power of heat treatment, allows us to unlock their full potential and create the perfect material for each specific need.
Achieve the Potential of Your Design with Unionfab
Take your project to the next level with Unionfab’s complete Finishing services.
Additionally, Unionfab provides a range of manufacturing solutions, including 3D Printing, CNC Machining, and Vacuum Casting. With our extensive material selection and expert guidance, you can choose the perfect fit for every project stage.
Whether it’s rapid prototyping with adaptable resins or high-volume production using robust metals, Unionfab empowers you to fully realize your design potential.
