- Introduction
- CNC Machining Basics
- Aerospace Applications of CNC Machining
- Materials Used in Aerospace CNC Machining
- CNC Machining Technologies in Aerospace
- Advantages of CNC Machining in Aerospace
- Challenges & Solutions of CNC Machining in Aerospace
- Quality Assurance and Certification
- Future Trends in Aerospace CNC Machining
- Case Studies and Industry Examples
- Conclusion
- Unionfab: Powering Aerospace with Precision CNC
Explore the significant role of CNC machining in the aerospace sector, highlighting its impact on precision, efficiency, and innovation.
Introduction
CNC, or Computer Numerical Control, translates 3D designs into instructions for machines to precisely cut various materials, enabling the production of intricate, high-strength components that can withstand the demanding conditions of flight.
This technology is crucial for the aerospace industry due to the vast variety of parts needed, the critical requirement for consistent quality and tight tolerances, and the overall efficiency it brings to modern aircraft and spacecraft manufacturing.
CNC Machining Basics
Definition of CNC Machining
CNC machining, or Computer Numerical Control machining, is a subtractive manufacturing process where computer control dictates the movement of cutting tools to remove material from a solid block, ultimately creating a desired final part.
Principles of CNC Machining
- Computer-Aided Design (CAD): The first step involves generating a 3D model of the part using CAD software. This model defines the exact geometry and dimensions of the final component.
- Programming: The CAD model is then transformed into a set of instructions, known as G-code, that the CNC machine can understand. This G-code meticulously details the movements of the cutting tools along various axes.
- Machining: The CNC machine reads the G-code and controls the cutting tools accordingly. These tools remove material from a solid block (workpiece) based on the programmed instructions, gradually shaping it into the final part.
Types of CNC Machines Used in Aerospace
The aerospace industry utilizes various CNC machines to accommodate the diverse shapes and sizes of its components.
Using rotating cutting tools to remove material from the workpiece, milling machines can create complex 3D geometries by moving the tool and the workpiece along multiple axes (X, Y, and Z).
This versatility makes them ideal for intricate aerospace parts like engine components and landing gear housings.
Turning Machines
Turning machines are well-suited for creating cylindrical parts. The workpiece rotates on a spindle, while a cutting tool shapes the outer diameter and inner features.
Aerospace applications include manufacturing shafts, bushings, and engine parts with rotational symmetry.
Multi-Axis Machines
For even greater complexity, multi-axis CNC machines offer more than three axes of movement. This allows for intricate machining of parts from all angles.
The aerospace industry utilizes these machines to create highly complex parts like turbine blades and airframe components.
Aerospace Applications of CNC Machining
Component Manufacturing
- Engine Parts: CNC machining tackles intricate components like turbine blades, combustors, and housings. The high precision and ability to handle heat-resistant materials are crucial for engine performance.
- Structural Components: CNC machines create critical structural elements like wing spars, longerons (longitudinal beams), and bulkheads. These parts require exceptional strength and dimensional accuracy to withstand flight loads.
- Landing Gear: Landing gear components, including struts, brakes, and wheels, are meticulously machined for strength and smooth operation during landing and taxiing.
Precision Tooling
CNC machining is instrumental in crafting the jigs, fixtures, and molds used in aircraft and spacecraft manufacturing. These tools require tight tolerances to ensure consistent and precise assembly of other components.
Prototyping and R&D
The rapid prototyping capabilities of CNC machining allow engineers to quickly create and test new designs for parts and components before committing to large-scale production.
This iterative process accelerates innovation and helps optimize designs for performance and weight reduction.
Materials Used in Aerospace CNC Machining
The success of aerospace components hinges on the materials used in their creation. CNC machining thrives in this industry due to its compatibility with a diverse range of high-performance materials, each with distinct advantages.
Aluminum Alloys
These lightweight metals, particularly Aluminum 7075 with its high strength-to-weight ratio, are popular choices for fuselage components, wings, and non-critical structural elements.
Their machinability makes them ideal for complex shapes using CNC processes.
Titanium Alloys
For applications demanding exceptional strength and resistance to high temperatures, titanium alloys are the go-to choice.
Landing gear components, engine parts like compressor blades, and airframe structures often utilize titanium due to its ability to withstand demanding flight conditions.
Composite Materials
Modern aircraft heavily utilize composite materials like carbon fiber reinforced plastic (CFRP).
These materials offer an unbeatable combination of high strength and low weight, making them ideal for wings, fuselage panels, and other structures requiring a balance of both.
While not directly CNC machined, CNC creates the molds and tools needed for composite part fabrication.
Superalloys
For parts exposed to extreme heat and pressure, such as turbine blades and combustor liners in jet engines, superalloys are best.
These nickel-based alloys possess exceptional high-temperature strength and creep resistance, allowing them to function reliably in the harsh environment of a jet engine.
CNC Machining Technologies in Aerospace
5-Axis Machining
Traditional 3-axis CNC machines move along X, Y, and Z axes. However, 5-axis machines introduce two additional rotary axes (often A and B), enabling machining from virtually any angle.
This capability is crucial for creating highly complex, contoured aerospace parts like turbine blades and contoured wing components.
High-Speed Machining (HSM)
HSM utilizes significantly faster spindle speeds and feed rates compared to conventional machining.
This translates to quicker machining times and improved surface finishes, particularly beneficial for aluminum components like fuselage skins and wing ribs.
Additive Manufacturing Integration
While CNC machining is a subtractive process, additive manufacturing (3D printing) builds parts layer-by-layer. The combination of these technologies is powerful in aerospace.
CNC machining can create the complex molds and jigs needed for additive manufacturing, while 3D printing can be used for lightweight, intricate structures or lattice designs.
Automated Quality Control Systems
Automated quality control systems, often using laser scanning or coordinate measuring machines (CMMs), are integrated with CNC machining processes.
These systems perform in-line inspections, ensuring parts meet the stringent dimensional tolerances and surface finish requirements of the aerospace industry.
Advantages of CNC Machining in Aerospace
Precision and Accuracy
Aerospace components require exceptional dimensional accuracy and tight tolerances to ensure proper functionality and safety. CNC machining excels in this area.
Cost Efficiency
While the initial setup costs for CNC machines can be significant, the long-term benefits outweigh them.
CNC machining offers high production efficiency, minimizing waste and labor costs.
Additionally, its ability to precisely machine complex shapes reduces the need for expensive assembly processes involving multiple parts.
Flexibility in Design
CNC machining readily adapts to various designs, allowing for the creation of intricate, non-standard components.
Speed and Efficiency
Automated processes and efficient tool pathing of CNC machining enable faster production times, crucial for meeting tight deadlines in the aerospace industry.
Additionally, the ability to create multiple identical parts consistently eliminates the need for manual rework, further streamlining production.
Reduction in Material Waste
CNC machining software can optimize cutting paths to minimize material waste during the machining process.
Challenges & Solutions of CNC Machining in Aerospace
Challenge | Solution |
---|---|
Material Hardness and Tool Wear | Specialized cutting tools (carbide, diamond) |
High-Speed Machining (HSM) to minimize tool-workpiece contact | |
Thermal Stress Management | Flood cooling with coolants and lubricants |
Specialized machining strategies to reduce cutting forces | |
Maintaining Tolerances | Advanced CNC machines with high-resolution encoders |
Automated in-process quality control with laser scanning or CMMs | |
Integration with Other Manufacturing Processes | Computer-Aided Manufacturing (CAM) software for process planning |
Quality Assurance and Certification
The aerospace industry prioritizes safety and reliability above all else. To achieve this, stringent quality assurance (QA) measures are implemented throughout the entire CNC machining process.
Standards and Regulations
ISO 9001
This international standard outlines the fundamental requirements for a robust quality management system. It emphasizes continuous improvement, customer focus, and documented processes.
While not aerospace-specific, ISO 9001 certification serves as a strong foundation for building an AS9100 compliant quality system.
Unionfab excels in CNC machining and 3D printing services in strict accordance with ISO 9001.
AS9100
This international standard specifically addresses quality management systems for the aerospace industry.
It builds upon the foundation of ISO 9001 and incorporates additional requirements focused on risk management, traceability, and counterfeit parts prevention.
AS9100 certification demonstrates a manufacturer’s commitment to the highest quality standards in aerospace production.
Inspection Techniques
Coordinate Measuring Machines (CMM)
These automated machines utilize a probe to precisely measure the dimensions and geometry of a part. They offer high accuracy and repeatability, making them ideal for verifying that parts meet the required tolerances.
Non-Destructive Testing (NDT)
This involves various techniques that allow for the evaluation of a part’s internal structure and material properties without causing damage. Common NDT methods used in aerospace CNC machining include:
- Ultrasonic Testing (UT): High-frequency sound waves are used to detect cracks, voids, and other internal defects within the material.
- X-Ray Inspection: X-rays penetrate the material and create an image that reveals internal flaws or inconsistencies.
- Eddy Current Testing (ECT): This method utilizes electromagnetic fields to detect surface and sub-surface defects, particularly relevant for conductive materials like aluminum alloys.
Case Studies of Quality Control in Aerospace CNC Machining
Engine Turbine Blades
These intricate components require tight tolerances and flawless surfaces to ensure efficient and safe engine operation.
CMMs and NDT techniques like UT are used extensively to verify dimensional accuracy and detect any internal cracks or imperfections.
Landing Gear Components
The immense forces exerted on landing gear necessitate rigorous quality control.
High-precision CMM inspection ensures proper dimensions, while NDT like ET verifies structural integrity and identifies potential fatigue cracks.
Flight Control System Parts
The smooth and precise operation of flight controls depends on the quality of their components.
CNC machining combined with CMM inspection and NDT guarantees these parts meet the stringent requirements for functionality and safety.
Future Trends in Aerospace CNC Machining
Advancements in Machine Learning and AI
Predictive Maintenance
ML algorithms can analyze sensor data from CNC machines to predict potential equipment failures before they occur. This allows for proactive maintenance, minimizing downtime and maximizing production efficiency.
Process Optimization
Machine Learning and AI can analyze historical machining data and real-time sensor readings to optimize cutting parameters for each part. This can lead to faster machining times, improved surface finishes, and reduced tool wear.
Increased Use of Robotics and Automation
Robotic arms and automated systems excel at repetitive, high-precision jobs, minimizing human error and boosting production throughput.
In the aerospace industry, where consistent quality is crucial, automation ensures flawless parts across large batches, ultimately leading to a more efficient and reliable manufacturing process.
Hybrid Manufacturing Techniques
Additive Manufacturing (AM) Integration
Combining CNC machining with 3D printing allows for the creation of complex parts with internal lattice structures for weight reduction, something not achievable with traditional methods.
Laser Additive Manufacturing (LAM)
This emerging technology utilizes lasers to melt metal powder layer-by-layer, potentially enabling the creation of complex, high-strength parts directly within a CNC machine.
Case Studies and Industry Examples
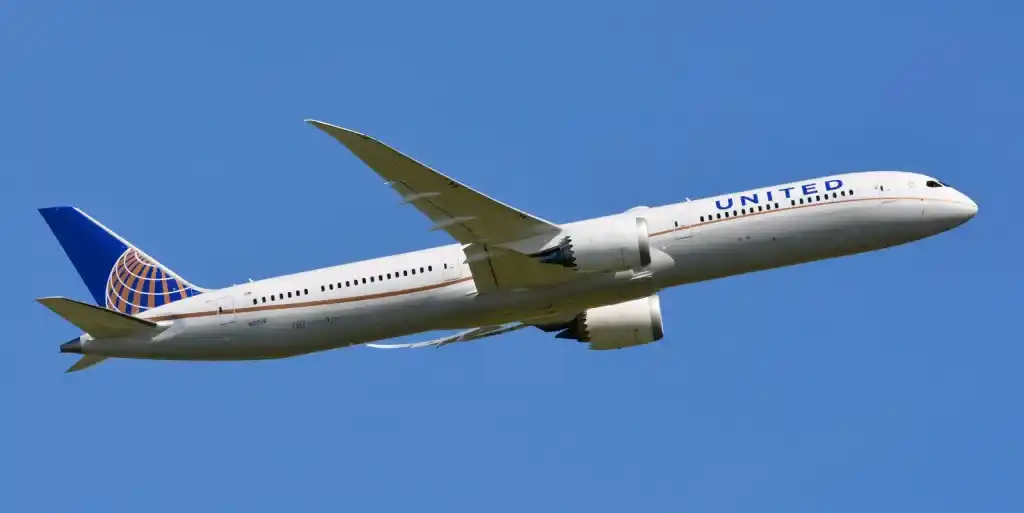
Source: wikimedia.org
The Boeing 787 Dreamliner stands as a testament to the transformative power of CNC machining in the aerospace industry.
This revolutionary aircraft boasts several innovations achieved in part through the extensive use of CNC technology.
- Lightweight Composite Fuselage: The 787 Dreamliner is the first commercial aircraft with a composite fuselage, significantly lighter than traditional aluminum designs. This weight reduction, enabled by CNC-machined molds and tools used in composite layup, translates to improved fuel efficiency and longer range.
- Complex Curved Wing Design: The 787’s distinctive curved wing design optimizes airflow for improved aerodynamic performance. CNC machining played a crucial role in creating the high-precision molds and tools needed to manufacture these complex wing components.
- Intricate Engine Nacelles: The nacelles (housings) for the 787’s Rolls-Royce Trent 1000 engines are intricately shaped for optimal engine performance. CNC machining allowed for the creation of these complex components with precise tolerances and smooth surfaces, minimizing drag.
Conclusion
CNC machining is transforming aerospace. It’s empowered the creation of intricate, lightweight parts, ensured exceptional precision and repeatability for safety, boosted production efficiency to meet deadlines, and minimized material waste of expensive materials.
In the future advanced technologies like machine learning and AI will optimize processes, while increased automation and robotics will improve production precision. Hybrid techniques with 3D printing and laser-based manufacturing promise even more complex parts.
All of this positions CNC machining to remain a vital tool in shaping the future of flight and pushing the boundaries of aerospace design and performance.
Unionfab: Powering Aerospace with Precision CNC
Unionfab’s expertise goes beyond renowned 3D printing. We offer high-precision CNC machining, ideal for the demanding world of aerospace.
From CNC turning and milling to advanced techniques like EDM and wire EDM, our diverse capabilities ensure precision and efficiency in your aerospace projects.
With a focus on quality and timely delivery, we handle complex parts and tight tolerances, meeting the rigorous standards of the aerospace industry.
