Although genuine 3D rubber printing is not yet available, rubber-like materials are transforming design and prototyping due to their flexibility.
Introduction
Rubber 3D printing aims to create objects with rubber-like qualities using additive manufacturing methods, mimicking the flexibility, elasticity, and resilience of natural rubber.
Its popularity is on the rise due to its ability to offer greater versatility to designers and engineers by enabling complex designs and functional prototypes.
Although this technology has not yet fully matured, with advancements in technology and a widening range of material choices, applications similar to rubber 3D printing are becoming increasingly prevalent across various industries.
Is 3D Print Rubber Possible?
Why 3D Printing with Rubber is Impossible?
Traditional rubber materials are challenging to 3D print directly due to their high viscosity and tendency to cure or vulcanize under specific conditions.
This makes it difficult to extrude or cure them layer by layer, which is the fundamental principle of most 3D printing processes.
Rubber-like 3D Printing Materials
Rubber-like Resin
- Custom ergonomic grips for tools: Using rubber-like resin in Stereolithography (SLA) 3D printing for comfortable and durable tool grips.
- Prototypes of flexible shoe components: Employing rubber-like resin to iterate quickly on shoe outsoles or midsoles for improved comfort and performance
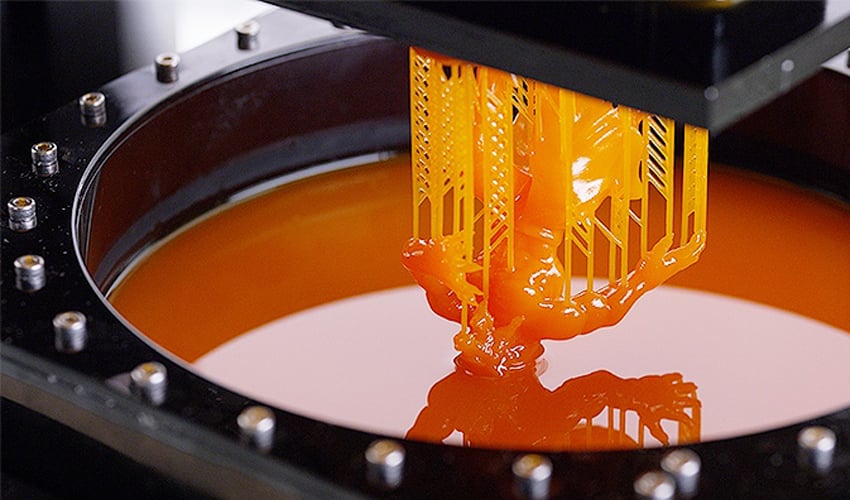
Source: 3dnatives.com
SLS TPU (Selective Laser Sintering Thermoplastic Polyurethane)
- Custom grommets and seals in automotive applications: Utilizing SLS TPU to create flexible and resilient grommets and seals for automotive systems.
- Prototypes of protective gear in sports: Producing impact-resistant prototypes of sports gear like knee pads or helmet liners using SLS TPU for athlete safety and comfort.
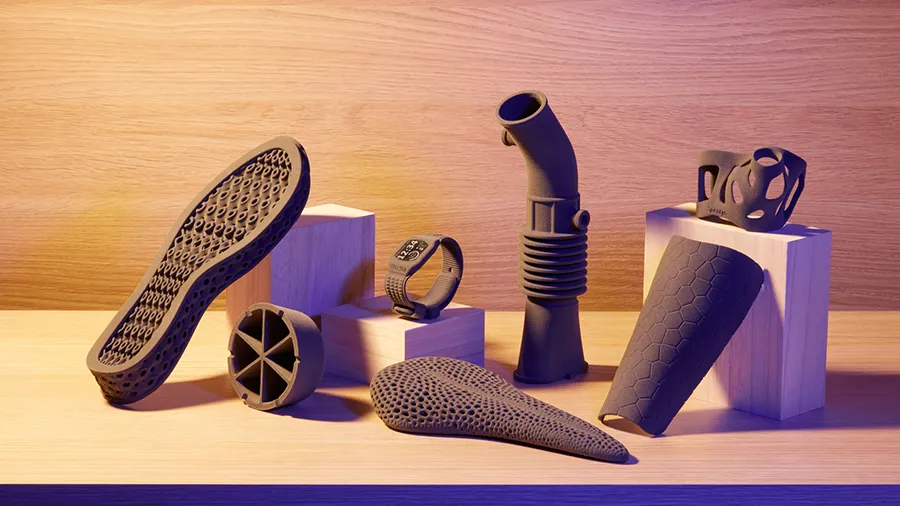
Source: engitype.com
Technologies of Rubber-like 3D Printing
Fused Deposition Modeling (FDM)
- Working Principle: FDM builds parts layer by layer by extruding thermoplastic materials through a heated nozzle.
- Rubber-like Properties: Specialized FDM printers and flexible filaments, like TPU, replicate rubber-like properties.
- Applications: FDM with rubber-like materials is used for prototypes and parts needing flexibility, such as gaskets and grips.
HP Multi Jet Fusion (MJF)
- Working Principle: MJF uses a powder-based process, applying a fusing agent and detailing agent selectively with an inkjet array.
- Rubber-like Characteristics: MJF achieves high-resolution prints with rubber-like qualities using specific material formulations.
- Applications: MJF with rubber-like materials is employed for end-use parts and prototypes requiring durability and flexibility.
Selective Laser Sintering (SLS)
- Working Principle: SLS sinters powdered materials, like TPU, using a laser to create solid objects layer by layer.
- Rubber-like Parts: SLS produces rubber-like parts with properties such as flexibility and impact resistance.
- Applications: SLS with rubber-like materials is utilized for prototypes and end-use parts needing resilience, like footwear components.
Stereolithography (SLA)
- Working Principle: SLA cures liquid photopolymer resin into solid layers using a UV laser.
- Rubber-like Resins: Some SLA resins mimic rubber-like properties when cured, offering flexibility and tear resistance.
- Applications: SLA with rubber-like resins is used for prototypes and parts requiring precise, flexible features, like molds and medical devices.
Advantages of Printing with Rubber-like Materials
Flexibility in Design and Functionality
Rubber-like materials allow for the production of parts with complex geometries and flexible features, enabling more innovative designs and functional prototypes.
For example, flexible and elastic parts such as seals or springs can be printed.
Rapid Prototyping
3D printing with rubber-like materials accelerates the prototyping process, enabling quick iteration and testing of designs, thus reducing time-to-market for new products.
For instance, multiple prototypes can be printed in a short period to validate different design concepts and rapidly optimize products.
Iterative Development
Designers can easily adjust prototypes and iterate on designs without the need for costly tooling changes, saving time and resources during product development.
For example, designs can be quickly modified based on testing and feedback, and updated prototypes can be printed immediately.
Cost-Effectiveness for Small-Scale Production
Compared to traditional manufacturing methods, 3D printing with rubber-like materials can be more cost-effective, especially for custom or low-volume parts.
For instance, there is no need for expensive molds or tooling changes, and material waste is reduced, making small-scale production economically viable.
Applications of 3D Printed Rubber-like Materials
Customized Phone Cases
The flexible nature of rubber-like materials makes them ideal for manufacturing custom phone cases that precisely fit individual models of smartphones. They can absorb shocks from drops, offering better protection than hard, brittle materials.
Moreover, they allow for personalization with a vast range of colors, patterns, and textures – from sleek, professional designs to vibrant, artistic creations.
Flexible Prototypes
In product development, being able to rapidly iterate on designs is crucial. Rubber-like materials serve well for prototyping parts that need to be flexible such as:
- Gaskets, which must provide tight seals in machines and devices.
- Seals, like O-rings, used in plumbing, engines, and various equipment to prevent leakage of fluids.
- Grips, for tools and equipment handles that require a non-slip, comfortable surface.
Healthcare
The healthcare sector benefits greatly from the application of rubber-like materials in 3D printing for several reasons:
- Prosthetics: Customized, flexible sockets for artificial limbs can be produced to enhance comfort.
- Orthotics: Insoles or corrective footwear can be tailor-made to assist with the patient’s specific foot structure or condition.
- Medical Devices: Items such as flexible tubing, bellows, or even components of wearable devices can be printed to cater to unique medical needs.
Automotive
Rubber-like materials are highly valuable in the automotive industry for prototyping and the production of end-use parts that require flexibility and durability such as:
- Grommets: To protect wiring and cables passing through metal parts.
- Bushings: Used in suspension systems for vibration isolation.
- Seals: Designed for various engine components, door seals, and window surrounds to prevent the ingress of fluids or air.
Conclusion
In conclusion, rubber 3D Printing is still in the process of development within current technology.
However, existing methods utilizing rubber-like materials and advanced technologies allow designers to effectively realize their creative concepts. This approach facilitates rapid prototyping and cost-effective production of flexible, resilient objects applicable across various industries.
Unionfab: Your Partner in Bringing Designs to Life
Unionfab focuses on the domain of 3D Printing and commits to delivering superior 3D printing solutions to our clientele.
In addition, we offer a diverse array of 3D Printing materials that may be required, including Rubber-like Resin and SLS TPU as referenced in this write-up.
For more information, kindly contact us through our Contact Us page.
