Read this article to learn why smooth 3D prints is important, how to smooth 3D prints, and its benefits.
Introduction
In the world of 3D printing, achieving smooth prints is paramount for both aesthetic appeal and functional performance. Understanding the importance of smooth surfaces, how to attain them, and the benefits they bring is essential for every enthusiast and professional alike.
Why Smooth 3D Prints
Importance of Surface Finish
A smooth surface finish on 3D prints carries significant weight for several reasons:
- Visual Appeal: Smooth surfaces exhibit a professional, polished appearance, enhancing the overall quality and attractiveness of the printed object. This is especially crucial for objects intended for display or presentation.
- Functional Performance: Beyond aesthetics, surface smoothness directly impacts the functionality of 3D-printed objects. In applications where parts come into contact with one another or with external surfaces, a smooth finish minimizes friction and wear, contributing to optimal performance and longevity.
- Texture Consistency: Smooth surfaces ensure uniform texture across the print, avoiding rough patches or unevenness that could compromise the object’s integrity or aesthetics.
- Ease of Post-Processing: Smooth surfaces are easier to post-process, whether it involves painting, coating, or further finishing techniques. This simplifies the overall manufacturing process and reduces the time and effort required for post-production work.
Functional Benefits
The functional benefits of smooth 3D prints are multifaceted, offering tangible advantages in various scenarios:
- Strengthened Structural Integrity: A smooth surface is less prone to weak points, layer adhesion issues, and stress concentrations, resulting in 3D prints with improved structural integrity and durability. This is particularly critical for load-bearing or mechanically stressed components.
- Reduced Surface Imperfections: Smoothing techniques effectively minimize or eliminate common imperfections such as layer lines, visible seams, and rough surfaces. This results in a more aesthetically pleasing final product and reduces the need for additional finishing work.
- Heightened Performance: In functional prints, especially those used in mechanical or moving parts, smooth surfaces reduce friction and resistance, leading to smoother operation, less wear and tear, and improved overall performance. This is crucial in applications where precision and reliability are paramount, such as in robotics, automotive components, or prosthetics.
By prioritizing smoothness in 3D prints, creators can unlock a multitude of benefits, ranging from enhanced aesthetics to superior functionality, ultimately elevating the quality and performance of their printed objects.
How to Smooth 3D Prints: Preparation
Before embarking on the journey to smooth 3D prints, thorough preparation is key to achieving optimal results.
Here’s a closer look at the essential aspects of preparation:
Selection of Appropriate Print Materials
The choice of print material significantly impacts the smoothness achievable and the techniques required for smoothing.
Different materials, such as PLA, ABS, PETG, and resin, have unique characteristics that influence their printability and post-processing properties.
- Consider Material Properties: Evaluate factors like hardness, flexibility, and chemical resistance to determine which material best suits your project. PLA is hard and easy to print, ideal for decorative items. ABS is durable and heat-resistant, suitable for functional parts.
- Compatibility with Smoothing Techniques: Choose a material that aligns with your preferred smoothing method. PLA smooths well with sanding but not with solvents. ABS can be smoothed with acetone vapor for a glossy finish. PETG often requires sanding and chemical methods. Resin prints need UV curing, sanding, and sometimes polishing.
Choosing the Right Print Resolution
Print resolution plays a vital role in determining the level of detail and surface smoothness achievable in 3D prints.
Higher resolutions generally result in finer layer heights and smoother surfaces, but they may also increase printing time and material usage.
- High Resolution (Low Layer Height): Produces smoother surfaces with fine details but increases print time and material usage. This is ideal for intricate projects, such as sculptures, where capturing fine details is crucial.
- Medium Resolution (Standard Layer Height): Balances print quality and speed, making it suitable for most projects where extreme detail isn’t necessary. This is perfect for prototypes that require moderate detail but need faster production times.
- Low Resolution (High Layer Height): Results in faster prints with less detail, often used for large objects or rough prototypes. This is beneficial for projects like architectural models where speed is more important than fine detail.
Identifying Imperfections for Targeted Smoothing
Before applying smoothing techniques, identify imperfections and areas requiring attention on the printed object.
This proactive approach allows for targeted smoothing, ensuring that resources are efficiently allocated to areas that need improvement.
- Inspect Printed Object: Carefully examine the print for common flaws such as layer lines, stringing, blobs, or visible seams. Using tools like magnifying glasses can help spot fine imperfections that need attention.
- Prioritize Areas: Focus on the most visible or critical areas first, such as the face and hands on a figurine where details are most noticeable. This targeted approach ensures that the smoothing process enhances the most important aspects of the print.
- Document Imperfections: Make notes or take photos of the areas needing attention. Marking rough spots with a marker before starting the smoothing process on a complex part ensures all problem areas are addressed efficiently.
By meticulously preparing for the smoothing process through material selection, print resolution adjustment, and targeted imperfection identification, creators can set the stage for achieving smooth, high-quality 3D prints that meet their aesthetic and functional requirements.
Sanding: The Fundamental Smoothing Technique
Sanding is a fundamental and widely-used technique for smoothing 3D prints.
It involves the use of sandpaper to manually or mechanically remove layer lines and imperfections from the surface of the printed object.
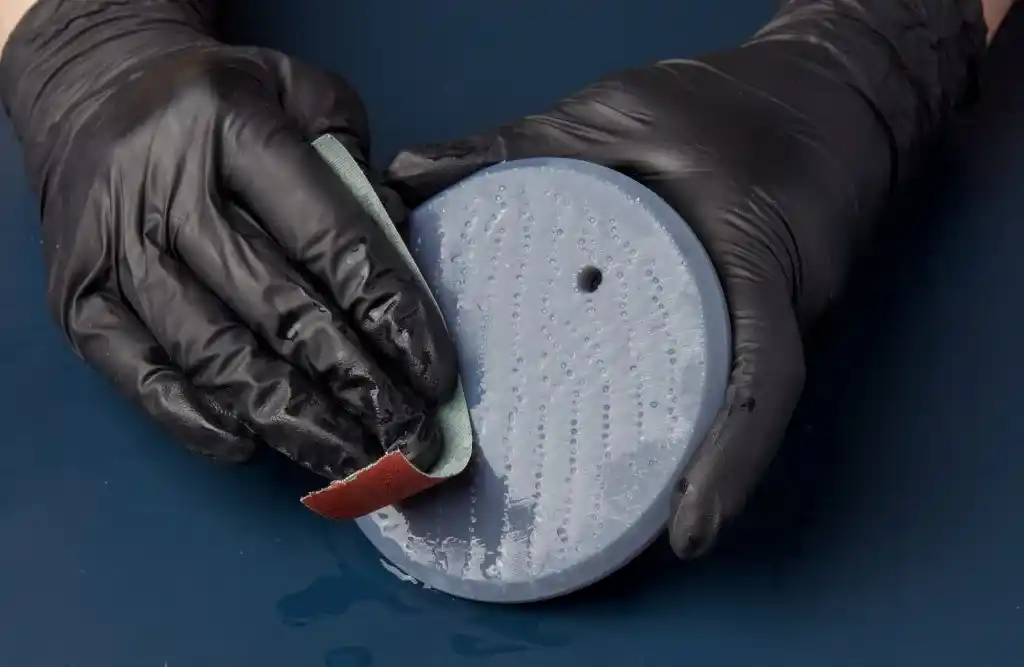
Source: support.formlabs.com
Sanding as a Smoothing Method
Sanding effectively reduces surface roughness and prepares the print for further finishing processes like painting or coating.
It’s a versatile method suitable for most 3D printing materials, particularly plastics like PLA, ABS, and PETG.
Types of Sandpaper and Their Applications
Different grits of sandpaper are used in the sanding process, each serving a specific purpose:
- Coarse Grit (60-100): Used for initial sanding to remove large imperfections and layer lines.
- Medium Grit (120-220): Smooths out the surface after coarse sanding and prepares it for finer sanding.
- Fine Grit (240-400): Provides a smooth finish and removes any remaining minor imperfections.
- Extra Fine Grit (600-1000): Achieves a highly polished surface, ideal for final finishing.
Step-by-Step Guide to Sanding 3D Prints
Initial Sanding with Coarse GritStart with a coarse grit sandpaper (60-100) to remove significant layer lines and surface imperfections.Sand in a circular motion or along the layer lines to ensure even material removal.
Progression to Finer Grits for Smoother Finish
Move to medium grit sandpaper (120-220) to smooth the surface further.
Continue with fine grit (240-400) to achieve a more refined finish.
For the best results, finish with extra fine grit (600-1000) to polish the surface.
Tips for Achieving Uniform Smoothness
- Keep the sandpaper and print surface clean to avoid scratches.
- Sand under running water or use wet/dry sandpaper to reduce dust and heat buildup.
- Apply even pressure and check progress regularly to avoid over-sanding.
By following these steps and selecting the appropriate sandpaper, you can achieve a smooth, high-quality finish on your 3D prints, making them ready for further processing or final use.
Chemical Smoothing:Advanced Technique
Chemical smoothing is an advanced technique that involves using solvents to dissolve and smooth the surface of 3D prints.
This method is particularly effective for achieving a high-gloss, professional finish.
Explanation of Chemical Smoothing Process
Preparation of the Smoothing Solution
Choose the appropriate solvent for your print material (e.g., acetone for ABS, isopropyl alcohol for PLA).
Ensure the work area is well-ventilated and equipped with necessary safety gear, such as gloves and goggles.
Application Methods for Different Print Materials
- ABS: Place the print in a sealed container with a small amount of acetone to create vapor smoothing. The vapor will gently smooth the surface.
- PLA: Brush or spray isopropyl alcohol onto the print. Alternatively, use a chemical smoothing solution specifically designed for PLA.
- Resin Prints: Use an appropriate solvent recommended by the resin manufacturer, often a mixture of isopropyl alcohol and other chemicals.
Post-Smoothing Rinsing and Drying Techniques
After smoothing, rinse the print with water or a neutralizing solution to remove any residual solvent.
Allow the print to dry completely in a well-ventilated area to prevent any solvent residue from causing damage or deformation.
Common Chemical Smoothing Methods
Acetone Vapor Smoothing (ABS): Effective for ABS prints, this method involves exposing the print to acetone vapor, which melts and smooths the outer layer.
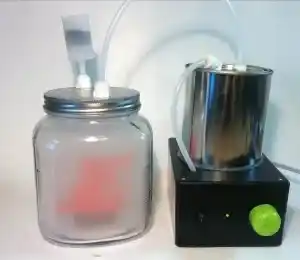
Source: engineerdog.com
Isopropyl Alcohol Smoothing (PLA): Brushing or spraying isopropyl alcohol helps smooth PLA prints, although the results may vary based on the specific PLA formulation.
Specialized Smoothing Solutions: Commercially available solutions designed for specific materials can provide consistent and effective smoothing results.
Safety Precautions
- Ventilation: Always perform chemical smoothing in a well-ventilated area to avoid inhaling harmful fumes.
- Protective Gear: Wear gloves, goggles, and, if necessary, a respirator to protect against chemical exposure.
- Fire Safety: Keep solvents away from open flames and high heat sources, as many are highly flammable.
- Proper Disposal: Dispose of used solvents and chemical residues according to local regulations to minimize environmental impact.
By following these guidelines and safety precautions, chemical smoothing can significantly enhance the surface quality of your 3D prints, offering a smooth, polished finish ideal for both aesthetic and functional applications.
Other Common Smoothing Techniques
Beyond sanding and chemical smoothing, several other techniques can help achieve smooth 3D prints. These methods are especially useful for different materials and specific applications, offering a range of approaches to enhance surface finish.
Heat Treatment Methods
Heat treatment involves using controlled heat to slightly melt the surface of the print, thereby smoothing it out. This method is particularly effective for certain plastics like PLA and ABS.
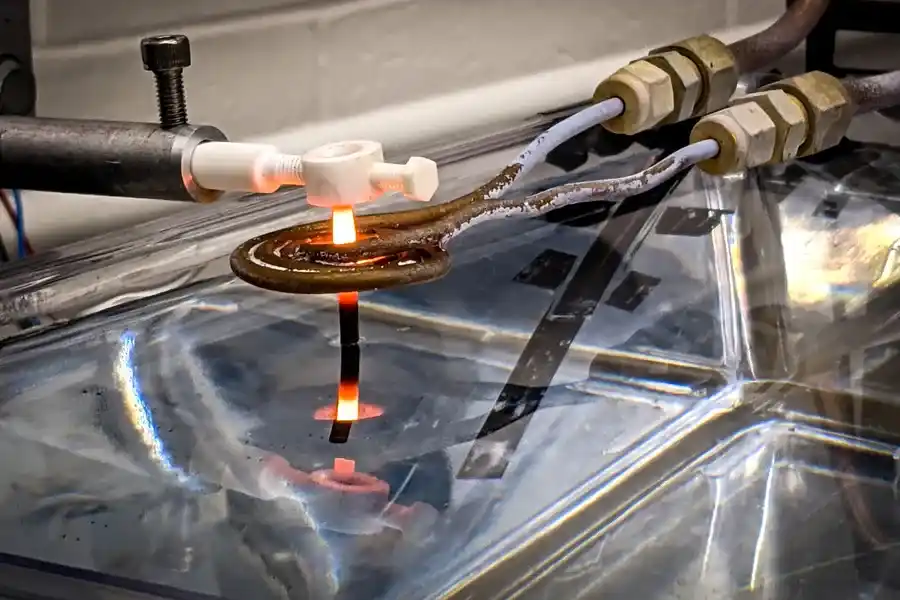
Source: news.mit.edu
- Heat Gun: Gently apply heat using a heat gun at a low setting, moving it evenly over the surface to avoid overheating any one spot. This method is quick and effective for small areas but carries a risk of warping if the heat is too intense.
- Oven Heating: Place the print in an oven at a low temperature (around 60-80°C or 140-176°F) for a short period, providing even heat distribution. Monitor closely to prevent melting or warping.
Resin Coating
Applying a thin layer of resin can smooth out the surface of 3D prints, filling in small gaps and layer lines.
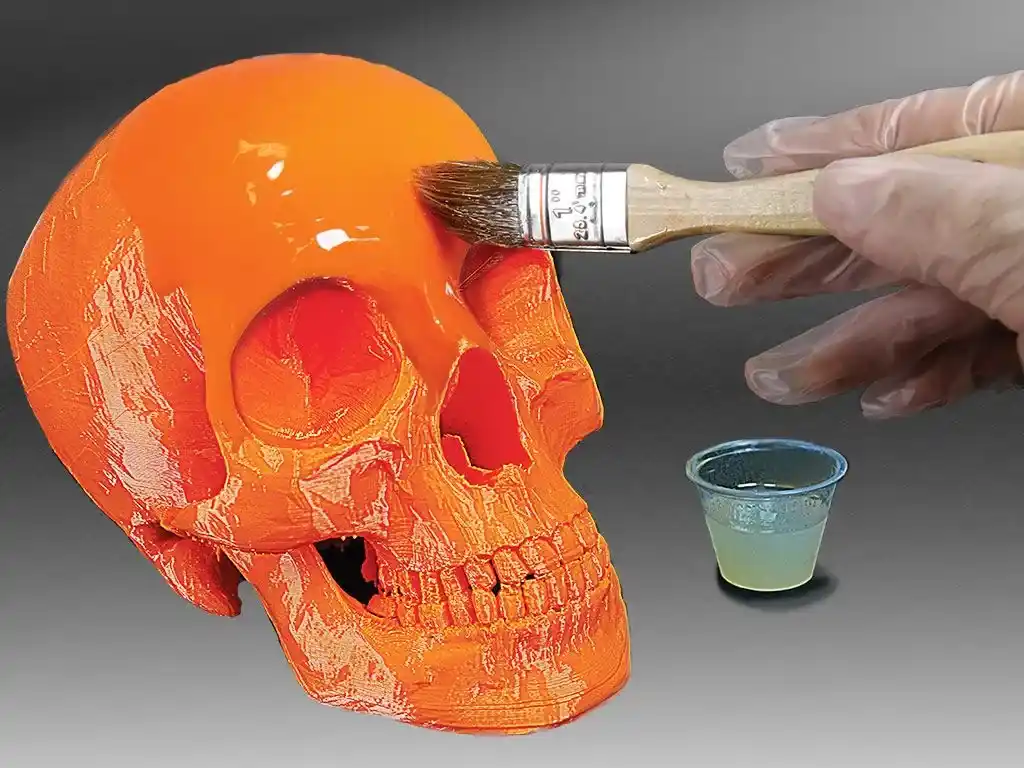
Source: pinterest.com
- UV Resin: Brush or dip the print in UV-curable resin, then expose it to UV light to harden the resin, creating a smooth, glossy finish. This method is particularly effective for SLA prints but requires careful application to avoid drips.
- Epoxy Coating: Mix and apply epoxy resin over the print, allowing it to cure according to the manufacturer’s instructions. This provides a durable, smooth surface, ideal for functional and aesthetic parts but can be messy and requires precise application.
Filler Primers
Filler primers, spray-on substances, fill in imperfections, creating a smooth base for finishing.
For instance, spray a coat, let it dry, then lightly sand for smoothness. Effective at filling gaps and lines, preparing for painting, it needs proper ventilation and protective gear.
These techniques enhance 3D print surfaces: heat treatment for minor flaws with careful temperature control, resin coating for glossy finishes, and filler primers to fill gaps. Choose based on material and project for smooth prints.
How to Smooth PLA 3D Prints
Smoothing PLA 3D prints can be challenging due to PLA’s properties. However, several techniques can help achieve a smooth finish.
Specific Challenges and Considerations with PLA
- Lower Heat Resistance: PLA softens at relatively low temperatures, making it susceptible to warping or deformation during heat treatments.
- Chemical Resistance: PLA is less responsive to common solvents, making chemical smoothing more complex compared to materials like ABS.
Techniques for Smoothing PLA Prints
Sanding PLA Prints:
Start with coarse grit sandpaper (e.g., 100-120) to remove major layer lines, then progress to finer grits (e.g., 220-400) for a smoother finish.
Sand under water or use wet/dry sandpaper to reduce dust and heat buildup, ensuring even pressure to avoid creating uneven surfaces.
Chemical Smoothing for PLA:
Use isopropyl alcohol or a PLA-specific smoothing solution. Apply with a brush or spray, allowing it to dissolve surface imperfections.
Ensure to apply in a well-ventilated area and use protective gear. Test on a small area first to gauge the effect and avoid over-application.
Heat Treatment Methods for PLA:
- Heat Gun: Apply low, controlled heat with a heat gun, moving it evenly across the surface to slightly melt and smooth the layers. Use the lowest effective heat setting and keep the heat gun moving to prevent warping.
- Oven Heating: Place the print in an oven at a low temperature (around 60°C or 140°F) for a brief period. Monitor closely to avoid melting and use an oven thermometer for precise temperature control.
By selecting the appropriate technique based on the specific needs of your PLA print, you can achieve a smooth and professional finish, enhancing both the aesthetic and functional quality of your 3D printed objects.
Benefits of Smoothing 3D Prints
Enhancing Visual Appeal
Smooth surfaces are crucial for showcasing product prototypes to clients or investors, providing a clear idea of the final product’s appearance.
In cosplay, smoothed 3D prints create realistic-looking props, enhancing the overall visual impact of the costume.
Improving Functional Performance
Smoothed surfaces reduce friction between gears and moving parts in mechanical assemblies, improving performance and extending the lifespan of the components.
For prosthetic devices, smoothed components ensure a comfortable fit and smoother movement for the wearer, enhancing functionality and usability.
Facilitating Post-Processing
Smooth prints provide a better surface for painting detailed miniatures and figurines, allowing for more intricate and vibrant color schemes.
In architectural models, smooth surfaces facilitate the application of realistic textures and finishes, enhancing the model’s overall appearance.
Strengthening Structural Integrity
Smoothed 3D prints of engineering prototypes are stronger and more durable, allowing for rigorous testing and validation of designs.
In functional tools and fixtures, smoothed surfaces improve their structural integrity, ensuring they can withstand repeated use in industrial or workshop settings.
Conclusion
In conclusion, smoothing 3D prints enhances their appearance, functionality, and durability. Techniques like sanding, chemical smoothing, and heat treatment ensure superior results for a variety of applications, from prototypes to cosplay props.
Prioritizing surface finish elevates the quality of prints, making them more visually appealing and structurally robust.
Achieve Perfect Finishing at Unionfab
Unionfab, as a company specializing in the field of 3D printing, is dedicated to providing finishing solutions for our customers.
Also, we can provide various types of 3D Printing materials you may need, such as PLA, PETG, and Stratasys ABS mentioned in this article.
For further details, please feel free to reach out to us via our Contact Us page.
