- Introduction
- What are Jigs and Fixtures
- Drawbacks of Traditional Rapid Prototyping Methods
- 3D Printing Methods for Jigs and Fixtures
- Advantages of 3D Printed Jigs and Fixtures
- Real World Applications of 3D Printed Jigs
- Future Potential and Industry Adoption
- Conclusion
- Unionfab Services: Custom Jig and Fixture Solutions
This article will explore how 3D printing technologies like FDM, SLS, and SLA are streamlining the creation of jigs and fixtures.
Introduction
What are Jigs and Fixtures?
Jigs and fixtures are custom tooling used to accurately position and hold workpieces during manufacturing processes. They help guide machines and tools for drilling, cutting, welding, and assembling components with precision.
Jigs and fixtures are crucial for automating production and maintaining quality and consistency across large quantities.
Challenges of Traditional Rapid Prototyping
Traditionally, jigs and fixtures were rapidly prototyped using methods like woodworking or metal fabrication, which could be time-consuming and expensive. Modifying designs often required entirely new tooling to be made from scratch. For low-volume production or frequent design changes, the costs associated with traditional rapid prototyping could be significant.
The Revolution of 3D Printing
3D printing is revolutionizing custom tooling by making it faster, easier and more affordable to produce jigs and fixtures.
The rise of 3D printing is radically transforming how jigs and fixtures are created. Technologies like FDM, SLS, and SLA allow manufacturers to “print” plastic and composite tooling directly from CAD files. This streamlines the design-to-production process for jigs and fixtures, saving substantial time and money.
What are Jigs and Fixtures
Differentiating Jigs and Fixtures

Jigs are specialized tools primarily used to guide, support, and control the movement of cutting or machining tools during the manufacturing process. They are designed to ensure that a specific operation, such as drilling holes or shaping components, is carried out with utmost accuracy and repeatability. Jigs often feature templates, guides, and clamps to securely hold and position workpieces, enabling workers to perform tasks with minimal error.
Fixtures, on the other hand, are fixtures are designed to hold and secure workpieces in a predetermined position for various manufacturing operations like welding, assembly, or inspection. Unlike jigs, fixtures do not guide or control cutting tools but focus on stabilizing workpieces to maintain consistent positioning throughout a process. Fixtures play a crucial role in ensuring uniformity and precision in tasks that involve multiple components or intricate assemblies.
Common Applications of Jigs and Fixtures
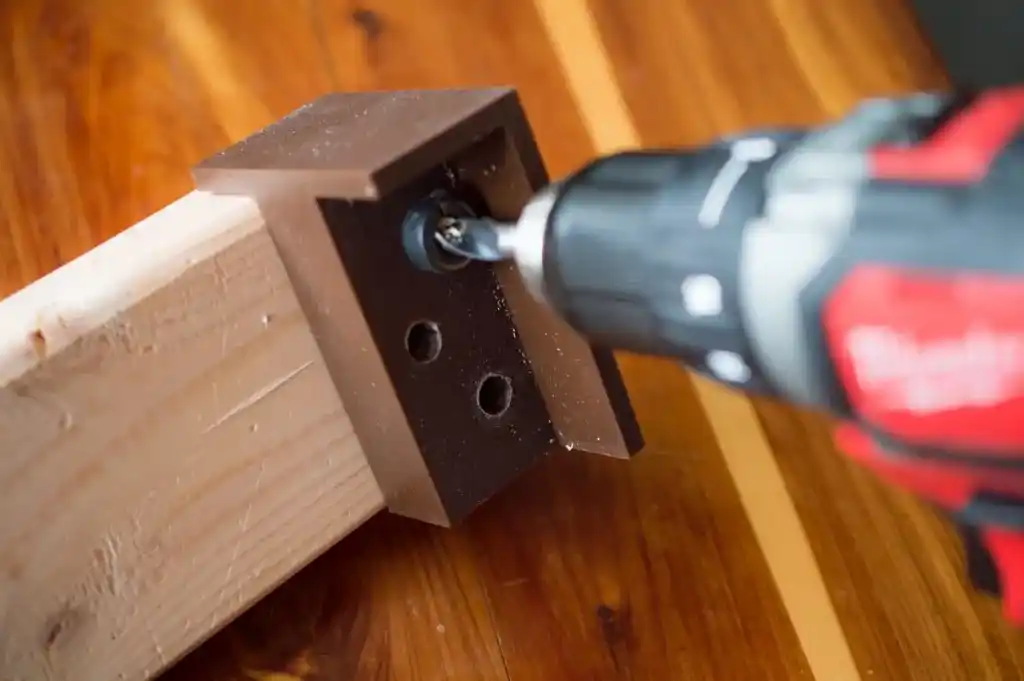
- Drilling jigs are used to accurately drill holes or perform other machining operations like countersinking, deburring, reaming, etc. on multiple parts. They ensure holes are placed in the exact locations needed with precise alignment between parts.
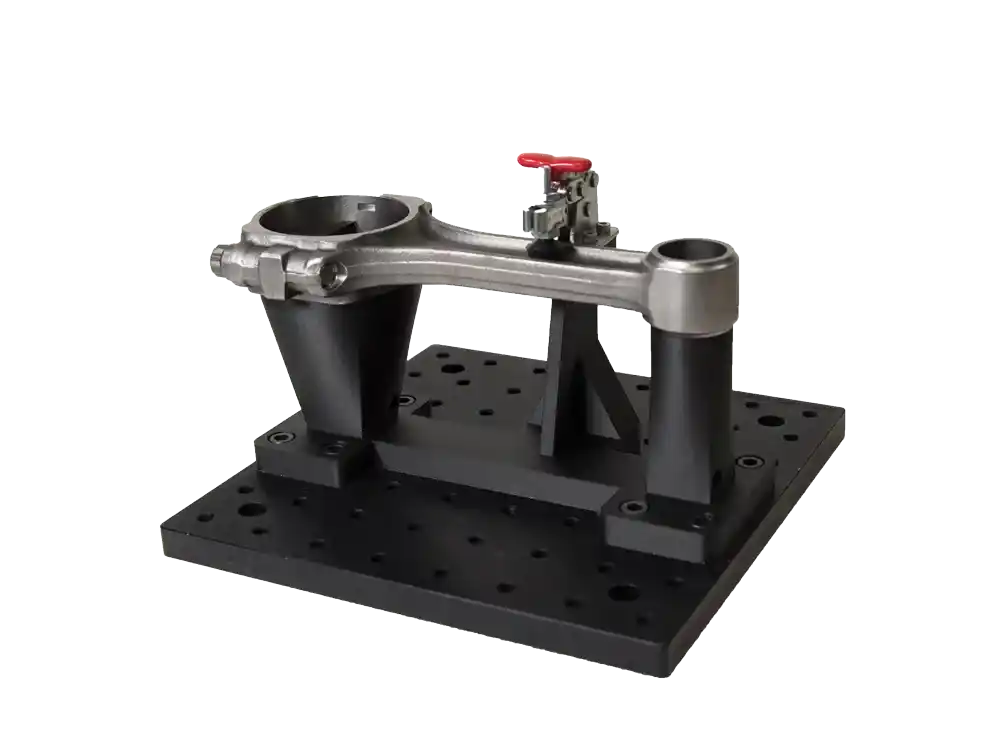
- Inspection fixtures precisely position components in a fixed relationship to measuring/inspection devices like calipers, micrometers or vision systems. This allows consistent and repetitive evaluation of dimensions and features to tight quality control standards.
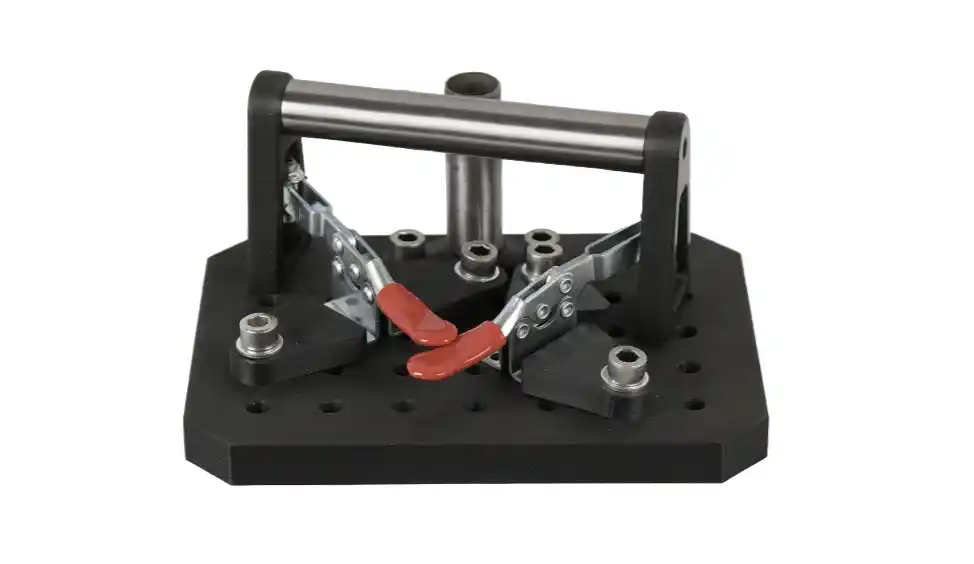
- Welding fixtures securely clamp materials together during welding processes. For example, spot welding fixtures help locate vehicle body panels in the proper spacing and alignment for automated spot welding guns. This ensures welds meet strength and aesthetics requirements.
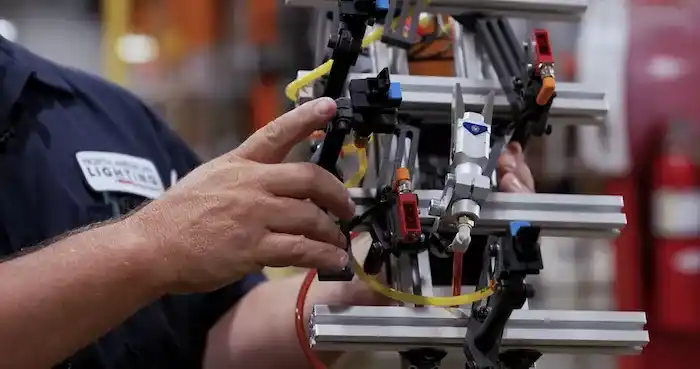
- Assembly jigs locate individual parts and subassemblies in specific arrangements to efficiently guide assembly line workers or robots. They help speed assembly by standardizing part positioning and orientation from one product to the next.
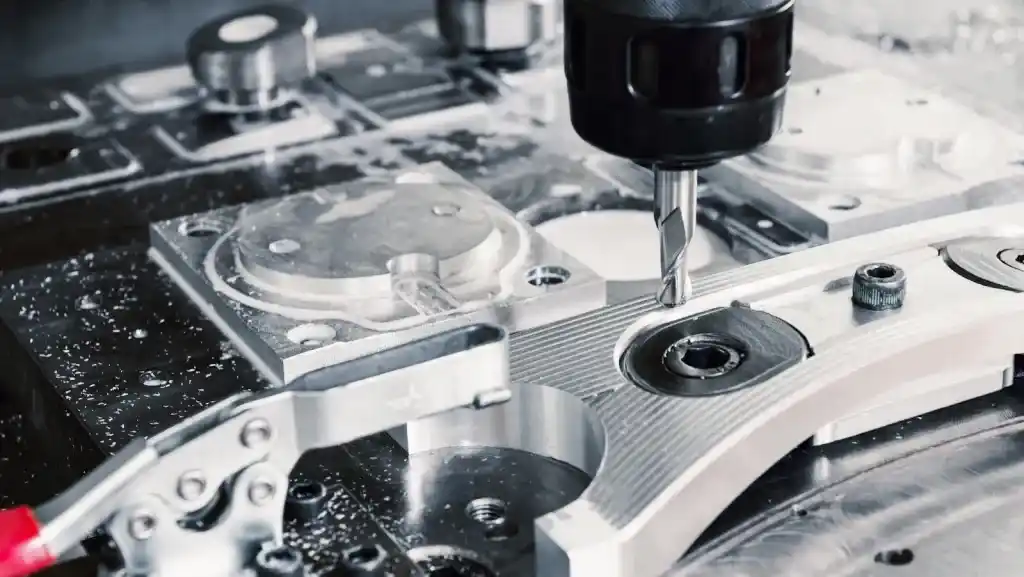
- CNC jigs guide CNC (Computer numerical control) cutting tools, such as end mills or routers, to shape components accurately. They are vital for creating intricate shapes and profiles.
Drawbacks of Traditional Rapid Prototyping Methods
Traditionally, jigs and fixtures were rapidly prototyped using woodworking, welding, metal fabrication or CNC machining from raw materials like wood, steel or aluminum.
- Time and Labor Intensiveness: Conventional techniques of jig manufacturing were inherently time and labor-intensive, extending production timelines significantly.
- Higher Costs: Conventional methods often incurred higher costs, especially for smaller production runs or prototypes. Expenses associated with skilled labor, specialized machinery, and raw materials contributed to the overall cost of creating jigs and fixtures.
- Limited Design Flexibility: Complex and intricate designs were challenging to achieve through traditional methods.
- Inefficient Iteration and Prototyping: Traditional jigs and fixtures were tailored for high-volume manufacturing, intended to maximize efficiency and throughput over long production runs. Altering their design often meant extensive physical tooling modifications, which may disrupt production schedules.
These drawbacks highlighted the need for a more efficient, cost-effective, and flexible approach to jig and fixture creation. Luckily, the advent of 3D printing technology has addressed many of these challenges, offering a revolutionary alternative that provides unprecedented design freedom and iteration capabilities.
3D Printing Methods for Jigs and Fixtures
Fused Deposition Modeling (FDM)
FDM 3D printing involves the extrusion of thermoplastic materials, like ABS or PLA, layer by layer to create objects.
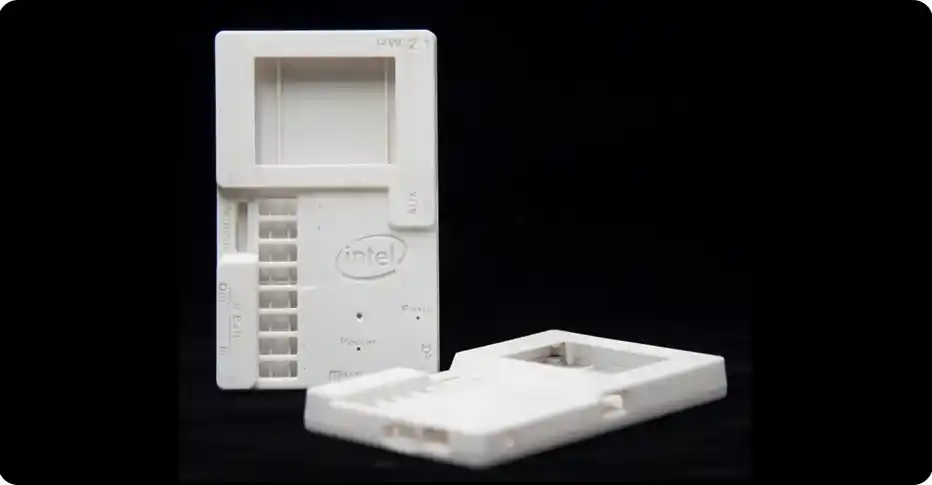
FDM is widely used for jigs and fixtures due to its accessibility, cost-effectiveness, and suitability for rapid prototyping.
It allows manufacturers to produce robust, lightweight, and customizable tools that can withstand the demands of various manufacturing processes.
Selective Laser Sintering (SLS)
SLS employs a high-powered laser to selectively fuse powdered materials, often nylon or other polymers, into a 3D object.

SLS offers advantages like excellent material strength and heat resistance, making it suitable for jigs and fixtures subjected to harsh conditions.
Its ability to produce intricate and complex geometries without the need for support structures is particularly beneficial.
Stereolithography (SLA)
SLA utilizes a liquid photopolymer resin that solidifies when exposed to an ultraviolet (UV) laser.
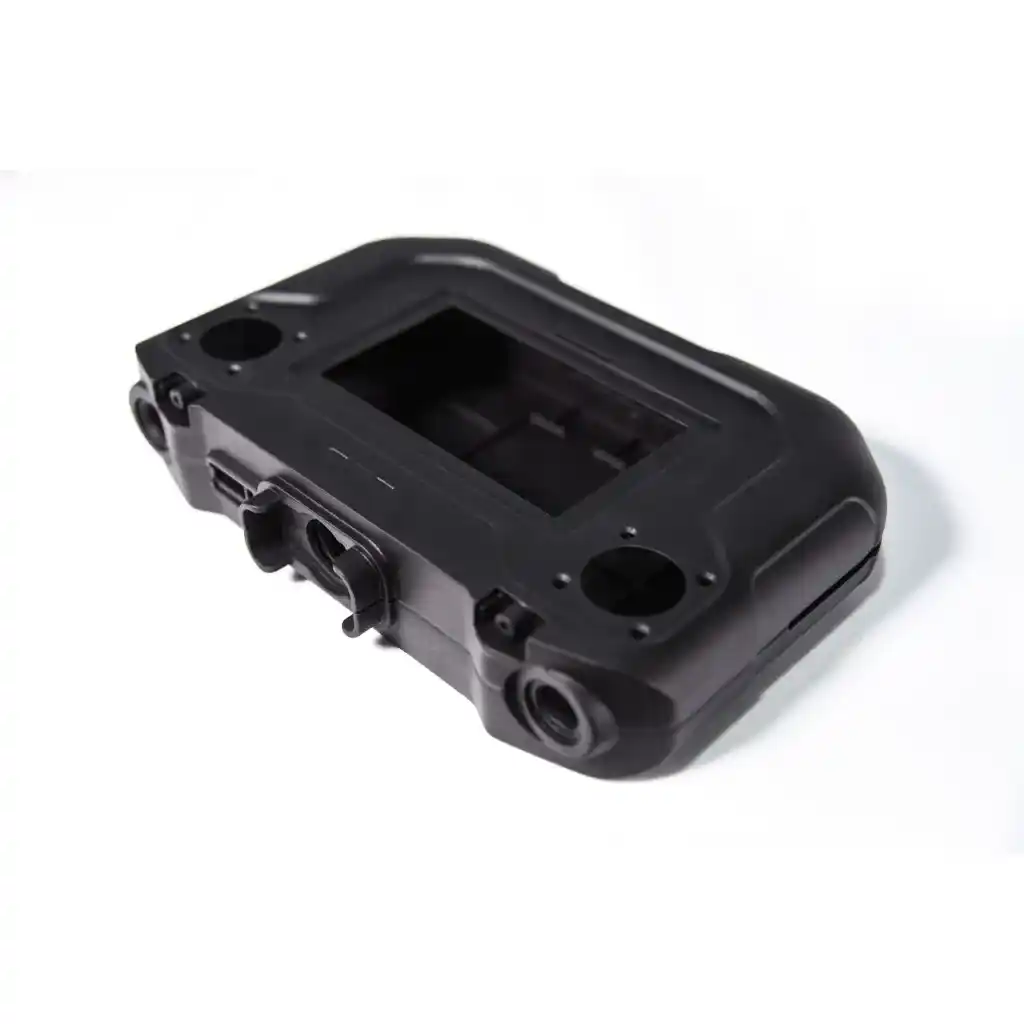
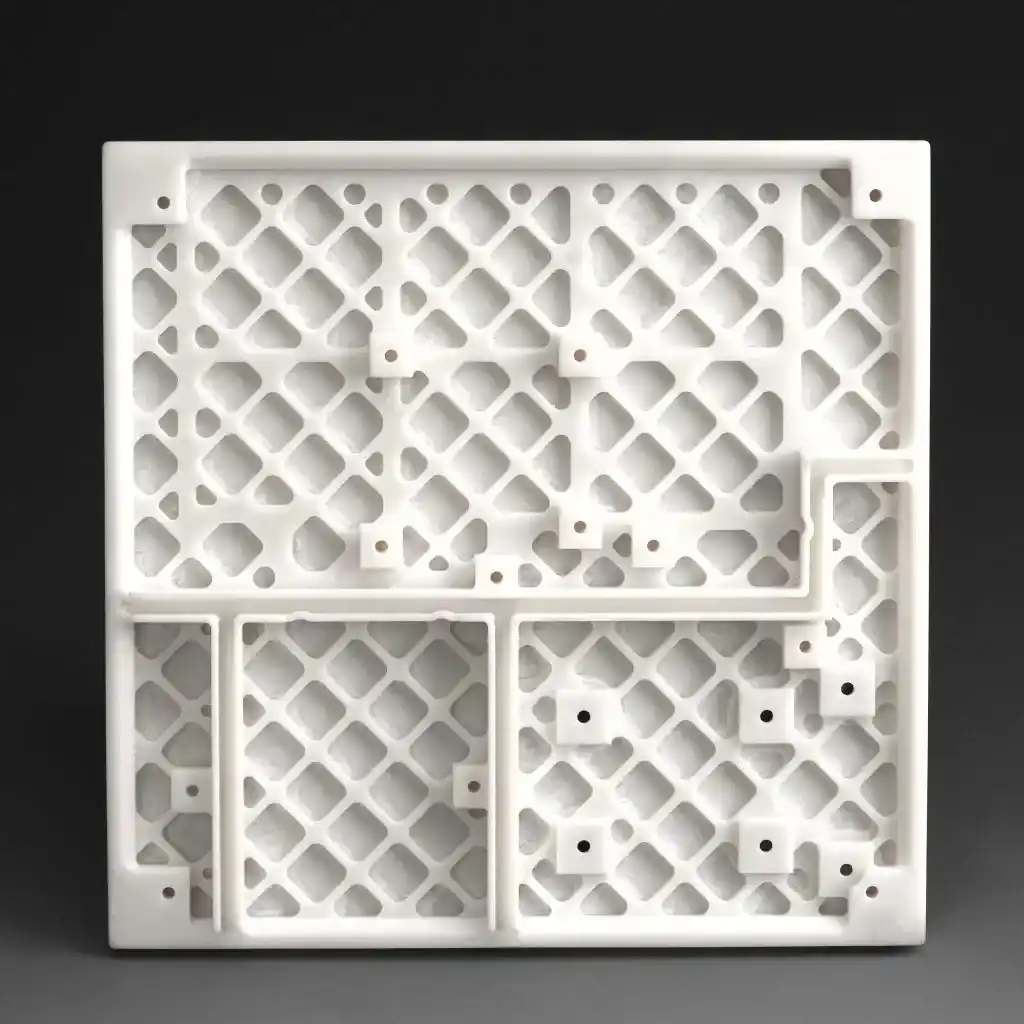
SLA technology excels in creating highly detailed, smooth-surfaced jigs and fixtures with exceptional precision.
It is a preferred choice for applications requiring intricate designs and a superior surface finish.
Advantages of 3D Printed Jigs and Fixtures
Reduced Lead Times
- 3D printing cuts weeks/months off traditional tooling. Parts can go from CAD file to finished tool in hours/days instead of weeks.
Lower Costs
- No Minimum order quantities, expensive tooling, storage, or machining costs. Even single piece prototypes are affordable.
- On-demand printing eliminates inventory costs.
Quick Prototyping and Iteration
- Design changes are file edits and reprints, avoiding rework. Easy prototyping and iterations drive more design ideas in less time.
Customization
- Tools can now be tailored for unique components or processes with design-for-manufacturing in mind from the start.
- Intricate interior geometries or moving parts possible for optimal part alignment or accelerated integration.
- Ability to produce jigs for rare, obsolete or one-of-a-kind parts traditional machining can’t handle.
Real World Applications of 3D Printed Jigs
Automotive
Opel, an automaker, has been utilizing 3D printing to create plastic assembly tools that are cheaper, quicker to produce, and versatile. These tools are used for assembly operations in Opel manufacturing plants across Europe.
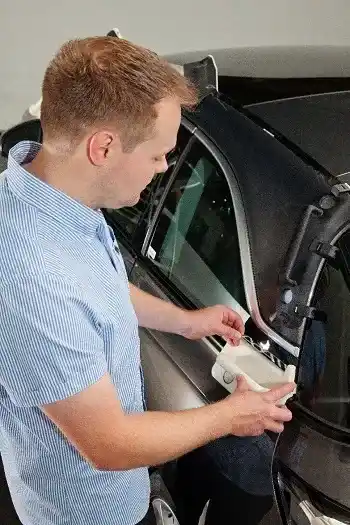
The advantages of using 3D printed jigs include reduced production costs (up to 90% cheaper), faster production (ready to use in about eight hours), and significant weight reduction (up to 70% lighter). Additionally, 3D-printed tools offer adaptability, ease of modification, and compatibility with various assembly situations.
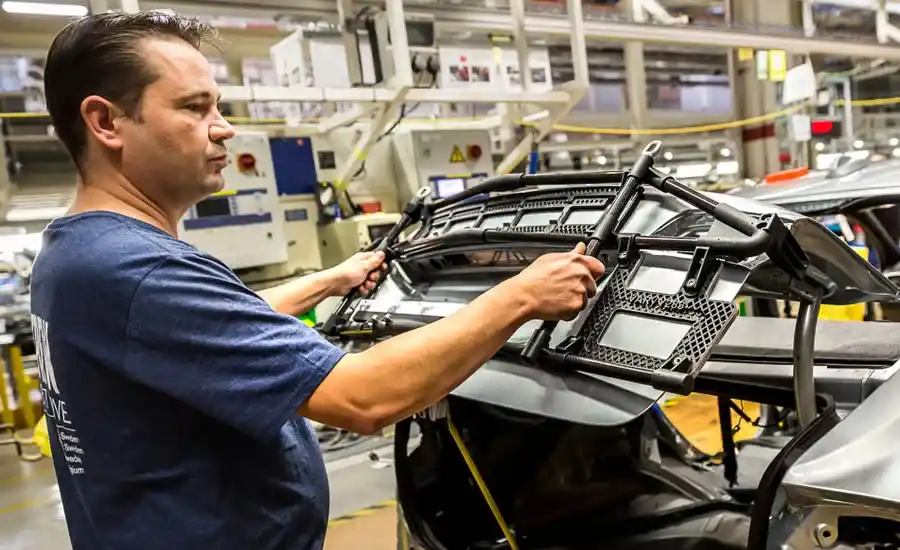
Another example would be Volvo Trucks North America, who has integrated 3D printing technology into its manufacturing processes, producing over 500 3D-printed tools and fixtures for their assembly plant. This enables quicker production, significant cost savings, and continuous quality improvement.
Electronics
The use of 3D printed jigs in electronics manufacturing offers significant advantages.
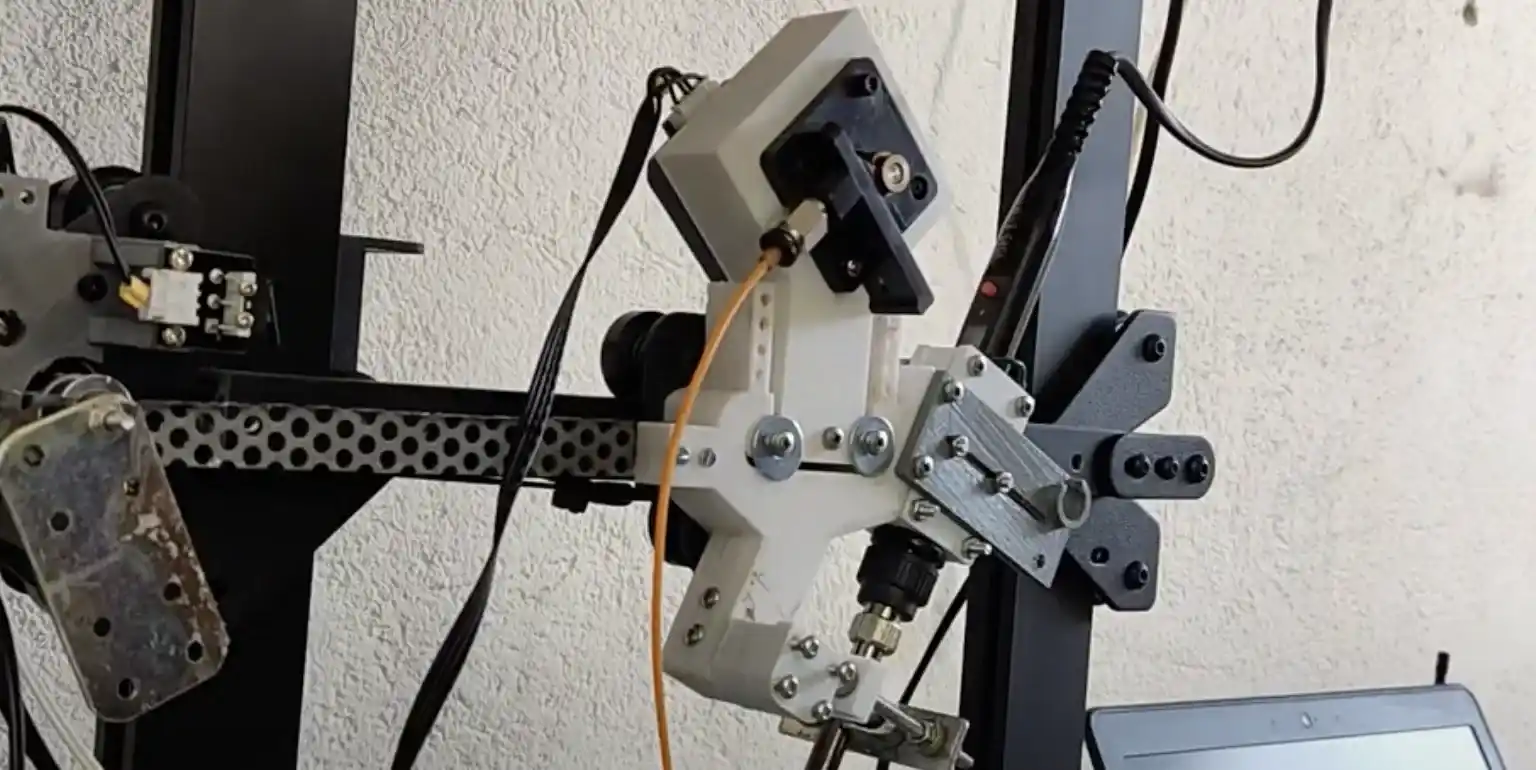
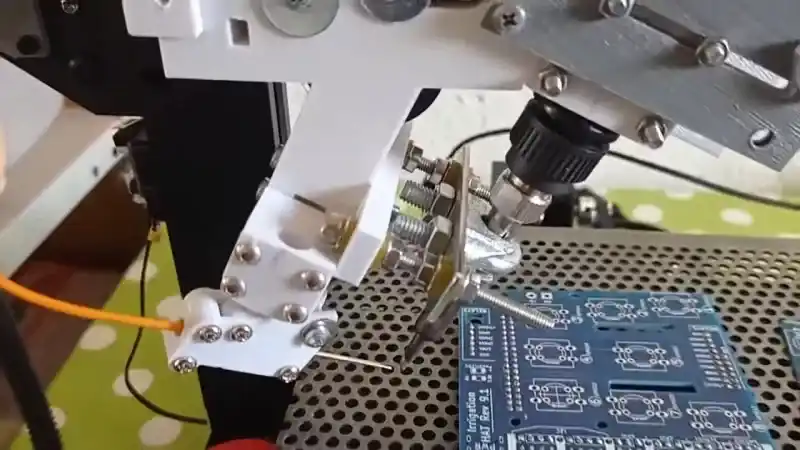
In one application, these jigs facilitate automated through-hole component soldering, providing precise and consistent soldering results. They excel in precision and reliability, making them particularly beneficial for small-scale PCB manufacturing runs. This innovative approach simplifies the soldering process and enhances overall efficiency in electronics production.
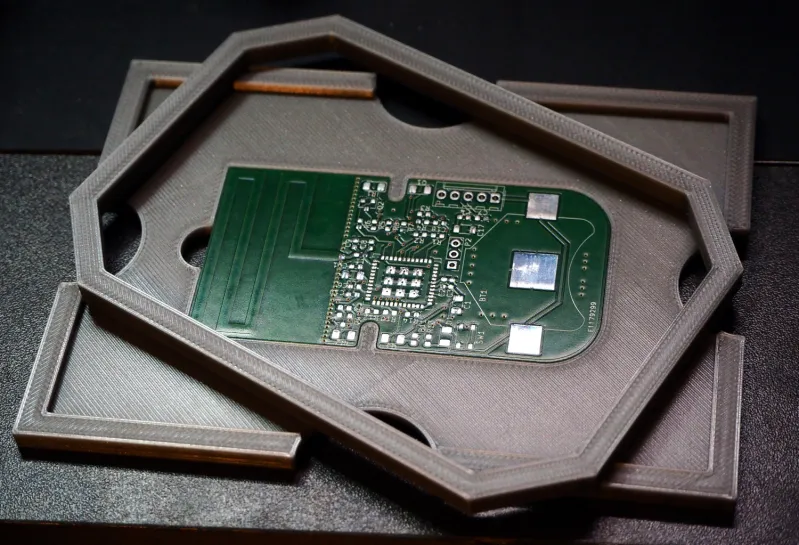
3D printed jigs can also ensure perfectly-aligned stencils, eliminating the frustration of manual alignment. This tool streamlines the PCB assembly process and seamlessly integrates with open-source assembly workflows, making it a valuable addition to the electronics manufacturing toolkit.
Construction
In construction, formwork jigs can consume a substantial portion of the budget, especially for intricate shapes. 3D printing with specialized filaments offers a more efficient and cost-effective solution, revolutionizing the production of formwork for concrete casting in various applications such as building restoration, facade panels, and public sculptures.
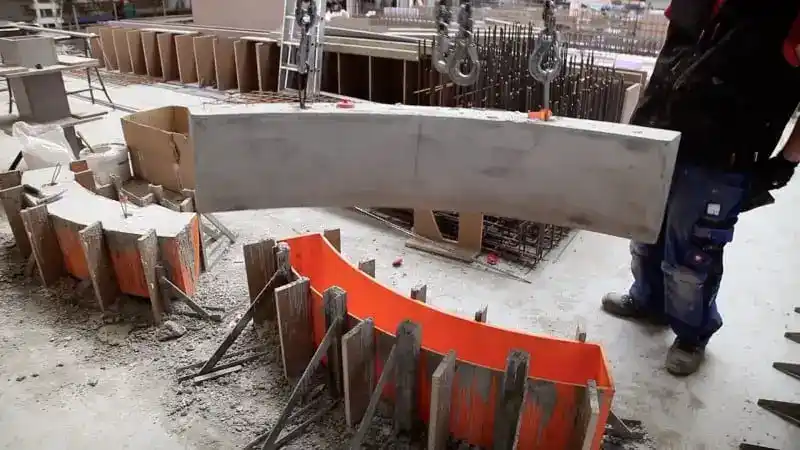
The ability to reuse the 3D printed formwork making it an environmentally friendly and economically sound choice in the construction industry.
Future Potential and Industry Adoption
- Conventional tooling methods will become obsolete for lower volume operations
- Reinforced materials and advanced printers will further distance 3D printing from prototyping to an integral mainstream manufacturing process.
- Advanced digital simulations may eventually replace physical trials.
Conclusion
The advent of additive manufacturing allowed direct digital production from CAD files, eliminating delays from conventional tooling methods. Technologies like FDM, SLS, and SLA each enable unique benefits for producing intricate and durable tools.
Industries now leverage 3D printed jigs and fixtures to reduce costs, speed production, ensure quality and rapidly iterate designs for assembly, inspection and drilling. Customized, digital tooling via 3D printing presents significant opportunities for future manufacturing efficiency and flexibility.
Unionfab Services: Custom Jig and Fixture Solutions
While 3D printing has revolutionized tool manufacturing, not all companies have the equipment, budget or expertise to produce tools in-house. This is where a service like Unionfab can help.
We offer:
- Affordable Pricing – tailored to be accessible for any budget
- Rapid turnaround – receive your 3D printed parts within weeks
- No minimum order sizes – orders of any size are accepted from a single prototype part to tens of thousands pieces
- Experienced technicians – on staff for design consultation, printing and post-processing
- Transparent Platform – Track order status in real-time from initial submission to shipment
By leveraging Unionfab’s capabilities, companies of any size can take advantage of the latest in 3D printing technologies for prototyping and manufacturing tooling solutions.