This article offers a comprehensive exploration of Nylon PA 12, covering its composition, properties, applications and considerations for use.
Introduction
Nylon PA 12, also known simply as Nylon 12, is a powerful and versatile plastic material with a wide range of uses.
Compared to other nylons, Nylon PA 12 has impressive mechanical properties like strength and flexibility, and suitability for various applications, from 3D printing to food packaging.
What is Nylon PA 12
Definition of Nylon PA 12
Nylon PA 12 is a synthetic thermoplastic polymer, meaning it can be melted, shaped, and then solidify again. This allows for easy processing and manufacturing.
It’s derived from monomers called ω-aminolauric acid or laurolactam, which have 12 carbon atoms each, giving PA 12 its specific designation.
Propeties of Nylon PA 12
PA 12 has a range of properties that make it valuable across various applications.
Mechanical Strength
PA 12 is known for its excellent toughness, tensile strength, and impact resistance. It can withstand significant force and pressure without breaking or deforming.
Chemical Resistance
PA 12 demonstrates impressive resistance to a variety of chemicals, including oils, fuels, and many solvents. This makes it ideal for applications where exposure to harsh substances is a concern.
Thermal Properties
PA 12 offers good thermal stability, retaining its mechanical properties even at elevated temperatures. It has a relatively low melting point compared to other nylons (around 178°C), making it easier to process.
Electrical Properties
PA 12 is a good insulator, meaning it conducts electricity poorly. This is useful for applications requiring electrical neutrality.
Dimensional Stability
PA 12 exhibits good dimensional stability, meaning it resists warping or shrinking significantly under varying conditions.
Nylon PA 12 Variants: Advanced Materials
Ongoing research and development leads to the creation of advanced Nylon PA 12 variants. These variants offer enhanced characteristics or functionalities to cater to specific applications.
- Description: This variation incorporates glass fibers into the PA 12 matrix. The glass fibers act as a reinforcing agent, significantly increasing the tensile strength, stiffness, and dimensional stability of the material.
- Applications: Glass fiber reinforced PA 12 finds applications in parts requiring high mechanical strength, such as gears, machine components, and structural parts exposed to demanding loads.
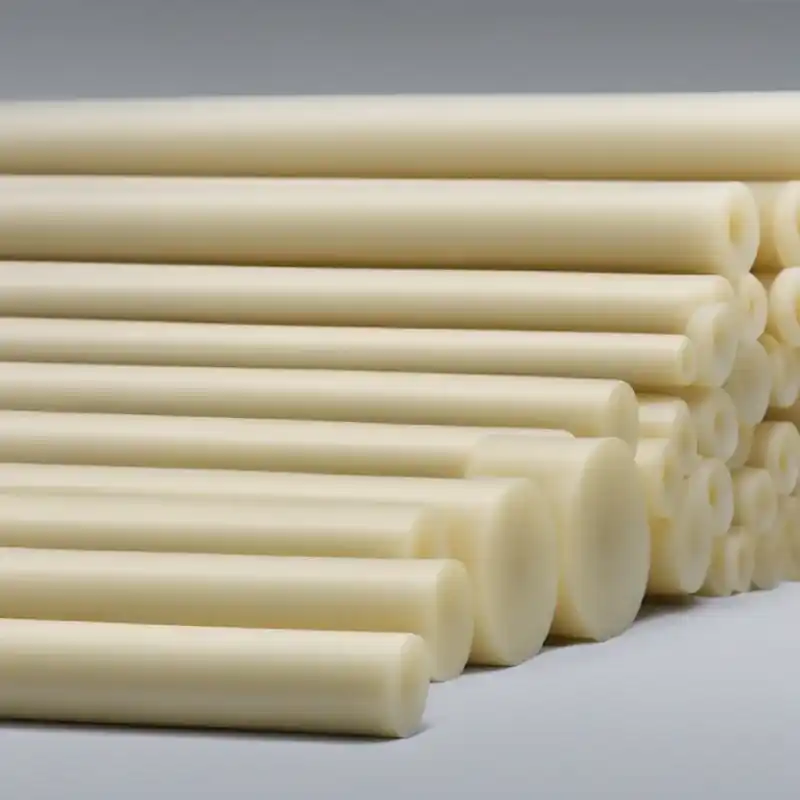
Source: procure-net.com
- Description: Similar to glass fiber reinforcement, carbon fibers are incorporated into the PA 12 matrix. Carbon fiber offers an even higher level of reinforcement, resulting in exceptional strength-to-weight ratio, stiffness, and dimensional stability.
- Applications: Carbon fiber reinforced PA 12 is ideal for lightweight yet high-strength components in various industries, including aerospace (aircraft parts), automotive (racing components), and sporting goods (high-performance equipment).
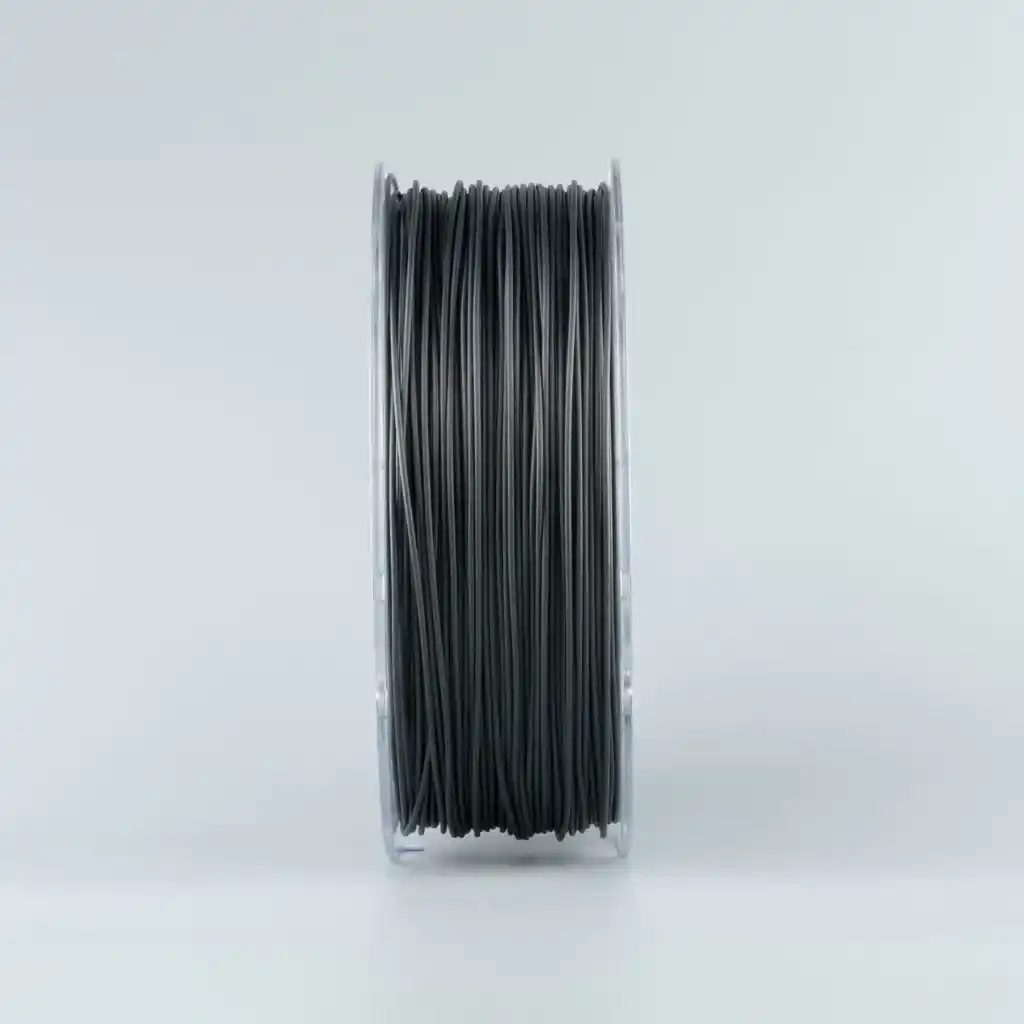
Source: michobby.com
Flame Retardant PA 12
- Description: Special additives are incorporated into the PA 12 to achieve flame retardant properties. This makes the material self-extinguishing or slows down its burning rate, enhancing fire safety.
- Applications: Flame retardant PA 12 is crucial for applications with strict fire safety regulations, such as electrical components in electronics, parts in mass transportation (trains, airplanes), and building materials in specific environments.
Comparison of PA 12 with Other Polyamides
While PA 12 offers a lot of impressive properties, it’s important to understand how it compares to other commonly used polyamides, like PA 6 (Nylon 6) and PA 66 (Nylon 66).
Chemical Structure: PA 12 vs. PA 6 vs. PA 66
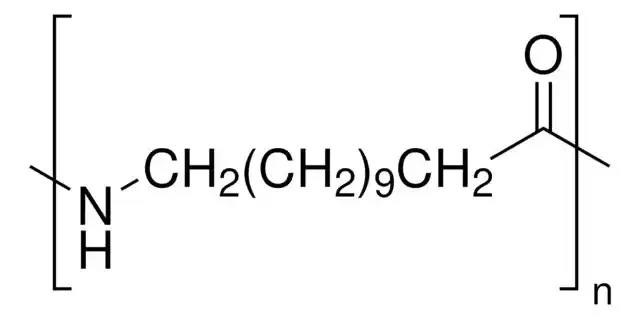
Source: sigmaaldrich.cn
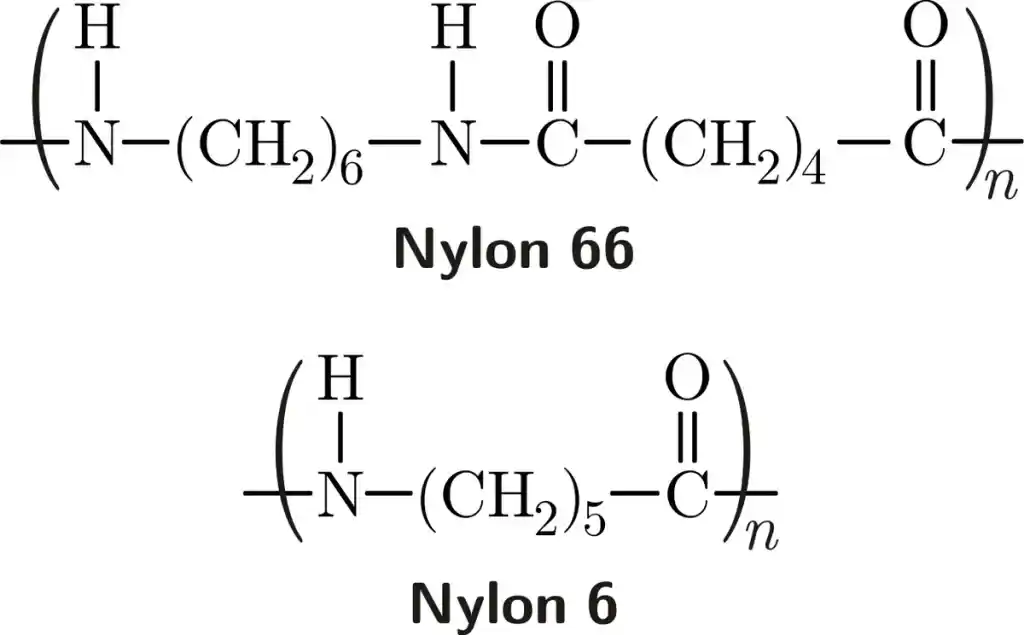
Source: wikimedia.org
Property Comparision: PA 12 vs. PA 6 vs. PA 66
Property | PA 12 | PA 6 | PA 66 |
---|---|---|---|
Moisture Absorption | Lowest | Higher | Higher |
Chemical Resistance | Excellent against hydrocarbons, fuels, and oils | Good | Good |
Mechanical Strength | Good overall, superior impact resistance | Good | Highest tensile strength |
Thermal Properties | Lower melting point, easier to process | Higher continuous use temperatures | Higher |
Dimensional Stability | Good | More susceptible to moisture changes | More susceptible to moisture changes |
Cost | More expensive | Less expensive | Less expensive |
3D Printing Process of Nylon PA 12
SLS 3D Printing of PA 12
- Preparation
- 3D Model: The first step involves creating a precise 3D model of the desired PA 12 part using CAD software. This model dictates the layer-by-layer instructions for the SLS printer.
- Powder Material: A fine Nylon PA 12 powder is loaded into the build chamber of the SLS machine. Particle size and quality significantly impact the final print properties.
- Printing Process
- Laser Scanning: A high-powered laser beam scans each layer of the sliced 3D model on the powder bed. The laser precisely melts or sinters the PA 12 powder particles together according to the design.
- Layer by Layer: The platform lowers slightly, and a fresh layer of PA 12 powder is deposited across the build chamber. The laser then scans and sinters this new layer, bonding it to the previous layer. This process continues layer by layer until the entire part is complete.
- Natural Support Structures: The unfused PA 12 powder surrounding the sintered areas acts as a natural support structure for the part. This eliminates the need for additional support materials often required in other 3D printing methods, saving time and minimizing potential damage to delicate features.
- Post-Processing
- Cooling: Once printing is complete, the entire build chamber cools down to solidify the sintered PA 12 particles and lock in the final part shape.
- Excavation: The completed build platform is transferred to a separate station where the PA 12 part is carefully excavated from the loose powder.
- Finishing (Optional): Depending on the application, the part might undergo additional finishing processes like bead blasting for a smoother surface or dyeing for a specific color.
FDM 3D Printing of PA 12
- Preparation
- 3D Model: Similar to SLS, a precise 3D model of the PA 12 part is created in CAD software. This model is then sliced into thin layers for FDM printing.
- Filament Selection: A spool of PA 12 filament with the desired diameter (typically 1.75mm or 2.85mm) is loaded into the filament feeder of the FDM printer. Filament quality and diameter can impact printing results.
- Printing Process
- Preheating: The FDM printer nozzle preheats to a temperature appropriate for melting the PA 12 filament.
- Material Extrusion: The feeder pushes the PA 12 filament through the heated nozzle, melting it into a molten state.
- Layer Deposition: The printer’s computer-controlled motion system precisely moves the nozzle, depositing the molten PA 12 filament layer by layer according to the sliced 3D model data. The filament cools and solidifies as it’s deposited, forming the desired shape.
- Support Structures (Optional): For parts with overhangs or complex geometries, additional support structures might be printed from a separate support filament material. These will be removed after printing.
- Post-Processing
- Cooling: Once printing is complete, the printed part remains on the build platform to cool down gradually and solidify completely.
- Part Removal: The PA 12 part is carefully removed from the build platform.
- Support Removal (if used): Support structures, if necessary, are removed using tools or by snapping them off designated breaking points. This might require some care to avoid damaging the PA 12 part.
- Finishing (Optional): Similar to SLS, the PA 12 part might undergo additional finishing processes like sanding or vapor smoothing for a smoother surface or dyeing for specific color needs.
Advantages of Nylon PA 12
Nylon PA 12 offers many advantages that make it a popular choice across various industries.
Lightweight Design
PA 12 boasts a relatively low density compared to metals. This allows for significant weight reduction in components, making it ideal for applications where weight is a critical factor, such as in aerospace, automotive, and consumer electronics.
High Impact Resistance
PA 12 excels in its ability to absorb impact without breaking or cracking. This makes it suitable for parts that experience shock or stress, such as gears, bearings, and machine components.
Chemical Compatibility
PA 12 demonstrates impressive resistance to a wide range of chemicals, including oils, fuels, and many solvents. This allows it to function reliably in harsh environments where exposure to such substances is a concern.
Design Flexibility
PA 12 exhibits good processibility, meaning it can be shaped into various forms using different techniques like extrusion, injection molding, and even 3D printing. This allows for a high degree of design freedom when creating parts with complex geometries.
Cost-Effectiveness
While PA 12 offers excellent performance, it’s generally a more expensive material compared to some other nylons like PA 6.
However, the long-term benefits like durability, potential weight reduction, and potentially less replacement needs can sometimes offset the initial cost.
The cost-effectiveness ultimately depends on the specific application and its requirements.
Applications of Nylon PA 12
Automotive Industry
- Fuel Lines and Brake Lines: PA 12’s excellent chemical resistance and good mechanical strength make it ideal for fuel and brake lines, where it can withstand exposure to harsh fluids and pressure.
- Engine Components: PA 12’s ability to handle heat and impact makes it suitable for various under-the-hood components like engine covers, intake manifolds, and wear parts.
- Interior Parts: PA 12 can be found in various interior components like gearshift knobs, instrument panels, and even some car seat parts due to its good strength and potential weight reduction benefits.
Aerospace Industry
- Lightweight and High-Strength Parts: PA 12’s ability to maintain strength at a low weight makes it suitable for aircraft components where weight reduction is crucial. Applications include interior panels, ducts, and even some structural parts.
- Fuel Systems: PA 12’s compatibility with fuels and resistance to harsh environments make it a valuable material for fuel system components like pipes and fittings.
- Wire and Cable Insulation: PA 12’s electrical insulation properties make it suitable for electrical wiring and cable insulation in aircraft.
Healthcare Sector
- Biocompatibility: Certain grades of PA 12 are biocompatible, meaning they can be used in applications that come into contact with human tissue without causing harm. This is useful for potential applications in prosthetics, orthotics, and some medical devices.
- Sterilization: PA 12 can withstand sterilization processes, making it suitable for medical instruments that require cleaning and disinfection.
- Drug Delivery Devices: The good chemical resistance and processibility of PA 12 make it a potential material for drug delivery devices like inhalers or nebulizers.
Considerations for Using Nylon PA 12
While Nylon PA 12 has numerous advantages, it’s important to consider certain factors to ensure it’s the most suitable material for specific application.
Environmental Factors
- Temperature: PA 12 has good thermal stability but can experience some deformation at very high temperatures (above 180°C).
- UV Resistance: PA 12 offers moderate UV resistance. For applications with prolonged exposure to sunlight, adding UV stabilizers or using a different material with superior UV resistance might be necessary.
Compatibility with Other Materials
- Chemical Compatibility: While PA 12 offers good chemical resistance, it’s not universally resistant to all chemicals. Ensure compatibility with any chemicals the PA 12 part will come into contact with during use.
- Adhesion: Bonding PA 12 to other materials can sometimes be challenging. Surface preparation and appropriate adhesives or welding techniques are crucial for achieving a strong bond.
Longevity and Durability
- Wear and Tear: While PA 12 has good wear resistance, applications involving constant high friction might require additional wear-resistant additives or coatings.
- Hydrolysis: Long-term exposure to moisture can degrade PA 12 in extreme cases. If your application involves a very humid environment, consider using a different material or employing protective measures.
Conlusion
Nylon PA 12 stands out as a versatile and powerful plastic material with a combination of impressive strength, chemical resistance, and good processibility.
PA 12’s advantages make it a good choice for applications in diverse industries like automotive, aerospace, and healthcare, offering the potential for weight reduction, improved performance, and long-lasting functionality.
Unionfab: Versatile Materials for Manufacturing
Unionfab caters to the growing need for high-performance materials and compatibility within modern manufacturing processes. Here are varieties of materials, including Nylon 12 Carbon-filled and Nylon 12 Glass-filled.
If you’re looking for a reliable source for advanced materials for your next project, especially those involving 3D Printing (e.g. SLS, FDM) or CNC Machining, Unionfab could be a strong contender to consider.
