- Introduction
- What is SLA Rapid Prototyping
- The Advantages of SLA Rapid Prototyping vs Traditional Prototyping Methods
- Key Principles of SLA Rapid Prototyping
- SLA Rapid Prototyping Applications
- SLA Rapid Prototyping in Various Industries
- SLA Rapid Prototyping: Challenges and Limitations
- The Future of SLA Rapid Prototyping
- Conclusion
- Embrace SLA Rapid Prototyping with Unionfab
An overview of how 3D printing enables SLA rapid prototype for fast, high-quality product design and development. Discusses key benefits, materials, processes, and applications.
Introduction
Rapid Prototyping, often abbreviated as RP, refers to a group of additive manufacturing technologies that can quickly produce physical prototypes.
Rapid prototyping enables fast iterative design, allowing multiple concepts and fits to be tested faster and more cost effectively than traditional techniques.
Key Principles of Rapid Prototyping
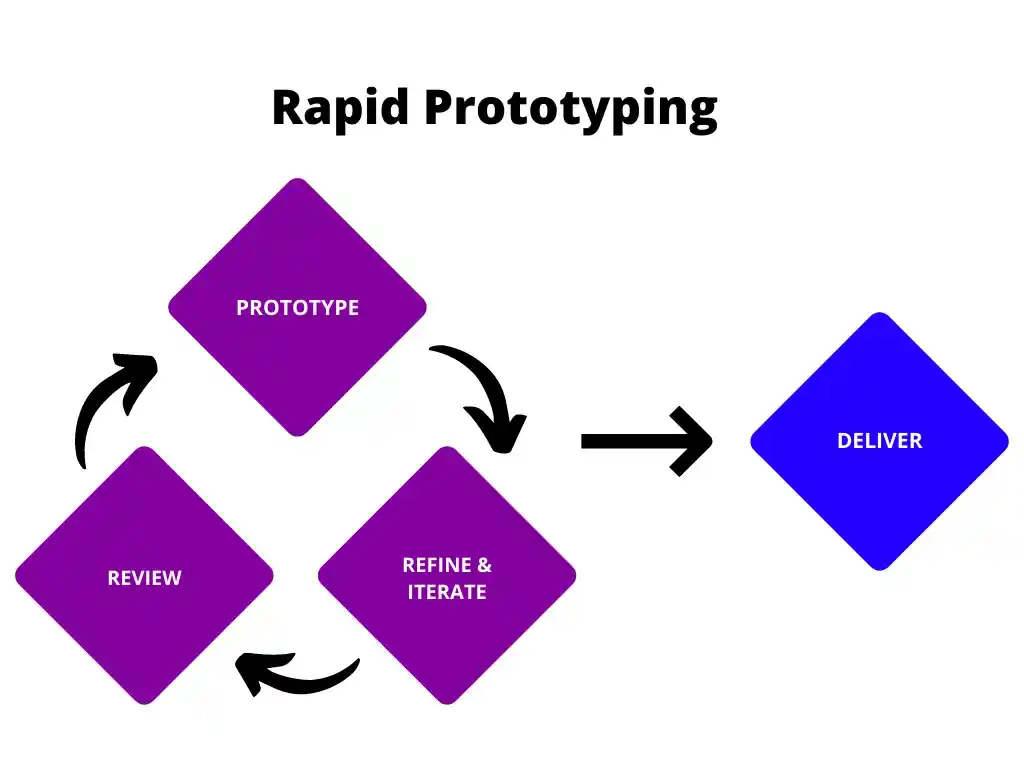
- User-Centered Design: Rapid prototyping enables designers to quickly create prototypes to gather user feedback for iterative improvement.
- Iterative Development: Rapid Prototyping thrives on iteration and refinement.
- Fail Fast, Learn Faster: Rapid Prototyping encourages a fearless attitude towards failure — a valuable source of learning.
Why Rapid Prototyping Matters
- Speeding Up Development: Quicker design feedback and iteration accelerates overall product development and time to market (TTM).
- Reducing Costs and Risks: Testing concepts early with prototypes minimizes costly late stage design changes.
- Enhancing Collaboration and Communication: Physical prototypes provide better understanding compared to concepts alone.
What is SLA Rapid Prototyping
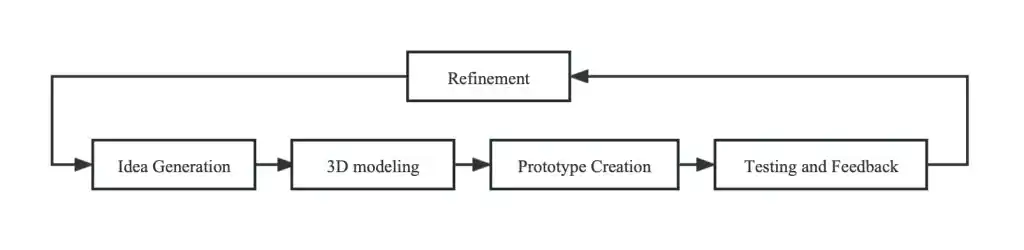
SLA Rapid Prototyping is a technique that utilizes Stereolithography, a 3D printing technology, to create highly detailed and precise prototypes. It involves curing layers of liquid photopolymer resin with ultraviolet (UV) light to build a three-dimensional object layer by layer.
Historical Evolution of SLA Technology
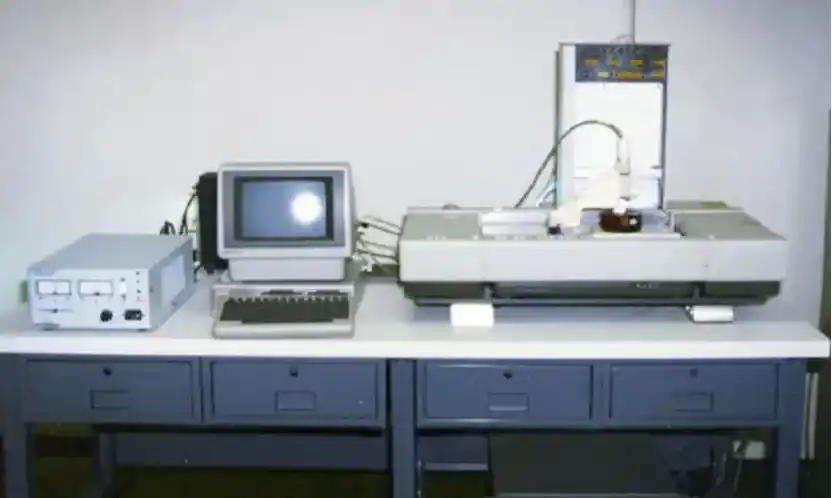
As one of the first 3D printing technologies invented in the 1980s, SLA was utilized with a primary focus on prototyping. During its early years, SLA machines were groundbreaking but prohibitively expensive. They were mostly used by large corporations and research institutions with substantial budgets for research and development.
Throughout the 1990s, SLA technology became more commercially viable. SLA technology expanded its reach to industries like aerospace, automotive, and healthcare. Prototyping remained a core application.
From 2000s on, SLA technology was used in various industries for rapid prototyping and even some limited production runs.
Today, SLA technology became almost ubiquitous. It still stands as a pinnacle of precision and efficiency in the realm of rapid prototyping.
SLA Technology’s Significance
The accuracy, speed, and surface finish of SLA has made it a leading choice for creating high-quality prototypes for concept modeling, fit testing, user research, and visualization.
It has become an indispensable tool in industries such as aerospace, healthcare, and automotive, where precision and performance are paramount.
The Advantages of SLA Rapid Prototyping vs Traditional Prototyping Methods
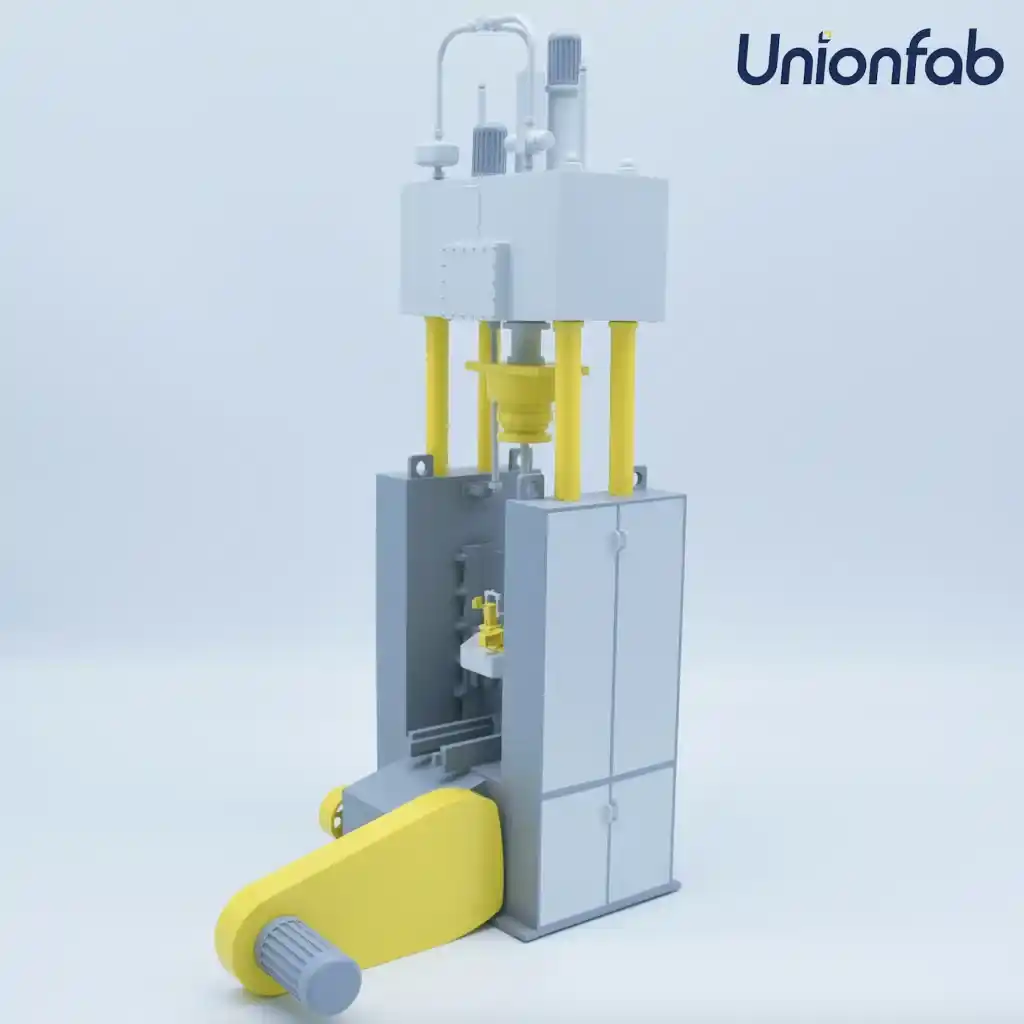
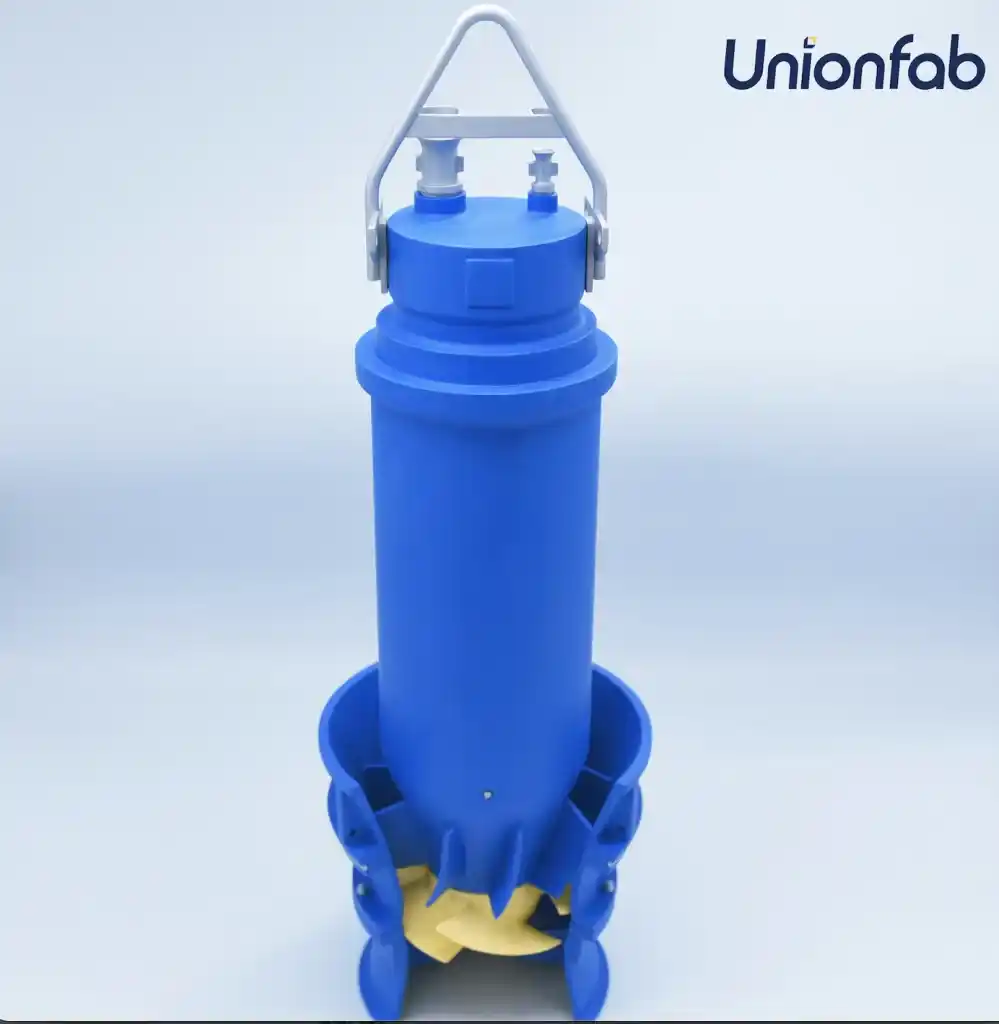
- Unparalleled Precision and Detail – SLA can produce details and tolerances down to 0.001 inches, capturing extremely fine features and complex geometries not possible with traditional methods. This enables high fidelity prototypes.
- Speed and Efficiency – SLA prototypes can be printed in hours or days rather than the weeks required for CNC machining or molding. Minimal setup and post-processing also improves speed.
- Material Variety and Quality – SLA resins range from rigid to flexible with properties engineered for different applications. The materials produce smooth, durable prototype parts.
- Complex Geometries Made Easy – Intricate internal structures, overhangs, and organic shapes are easily fabricated using SLA with no need for supports.
- Low Waste – SLA only uses the required resin, with no milling or leftover material. This makes it more sustainable and cost-effective than subtractive techniques.
- Surface Finishes – SLA parts require little to no post-processing, and have smooth, detailed exterior surfaces right out of the printer.
- Rapid Iteration – The speed of SLA allows designers to quickly print, evaluate, and refine multiple iterations of a prototype.
- Accuracy for Fit and Function – Exceptional tolerances and precision ensure SLA prototypes properly fit together and can be used for functional testing.
Key Principles of SLA Rapid Prototyping
Design Optimization for SLA
Orientation for Better Print Quality
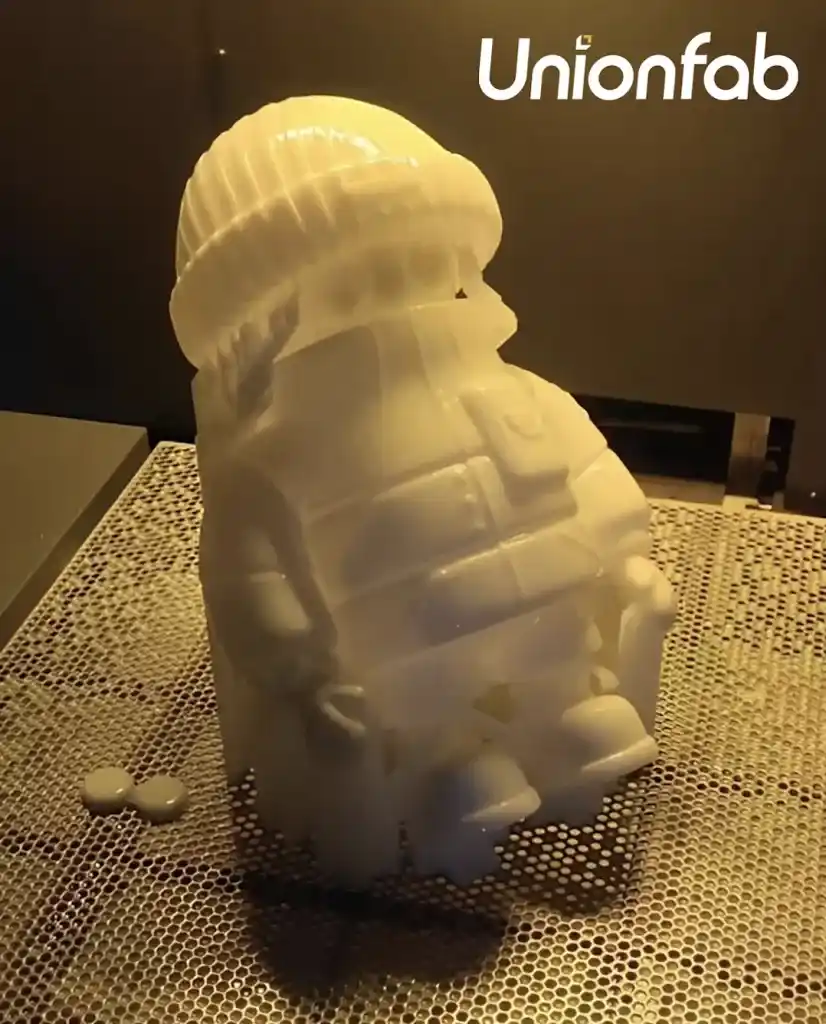
Proper part orientation can help minimize the need for support structures, reducing post-processing and material usage while ensuring successful prints.
Wall Thicknesses and Feature Sizes
There are minimum wall thicknesses based on resin viscosity and laser spot size. Designers must consider the minimum wall thicknesses to achieve the desired part strength and detail. Small features may not fabricate properly.
Accounting for Resin Properties and Post-Processing
Designs must account for resin shrinkage, thermal expansion, and requirements for post-curing, washing, etc. The choice of resin and its properties should align with the desired final characteristics of the prototype.
Troubleshooting Print Failures
Issues like cracking, warping, gaps, or poor detail can be caused by improper orientation, model errors, resin contamination, or machine factors.
Material Selection for SLA Rapid Prototyping

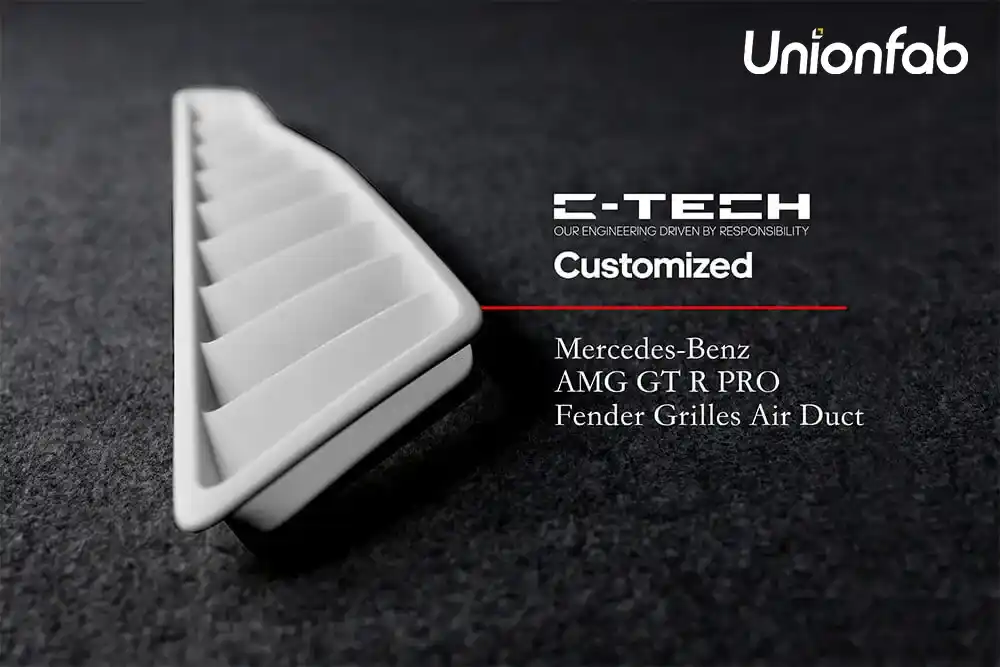
- Hardness: Resins come in a range of hardness from flexible to rigid, tailored to the required physical properties.
- Clear and colored resins provide a versatile range of options for achieving distinct visual aesthetics. Transparent resins, in particular, are ideal for creating see-through effects in mechanical and medical prototyping.
- Biocompatiblity: Bio-compatible resins allow prototyping of implants, medical and dental devices for testing fit and form.
- Strength: Resins with strength need to be considered if functional prototypes will endure stresses, heat or fluids over time.
- Composite resins: can prototype heat-resistant components for form/fit testing.
- Handling and storage for different resins – Different resins may have specific handling and storage requirements to maintain their quality and performance over time.
SLA Rapid Prototyping Applications
SLA (Stereolithography) Rapid Prototyping finds versatile applications across various industries, providing solutions for different needs and challenges. Here are some of the key applications of SLA technology:
Concept Models
Concept models are early stage physical representations of design ideas. They allow designers to visualize, test, and refine a concept before committing to a final design.
Functional Prototypes
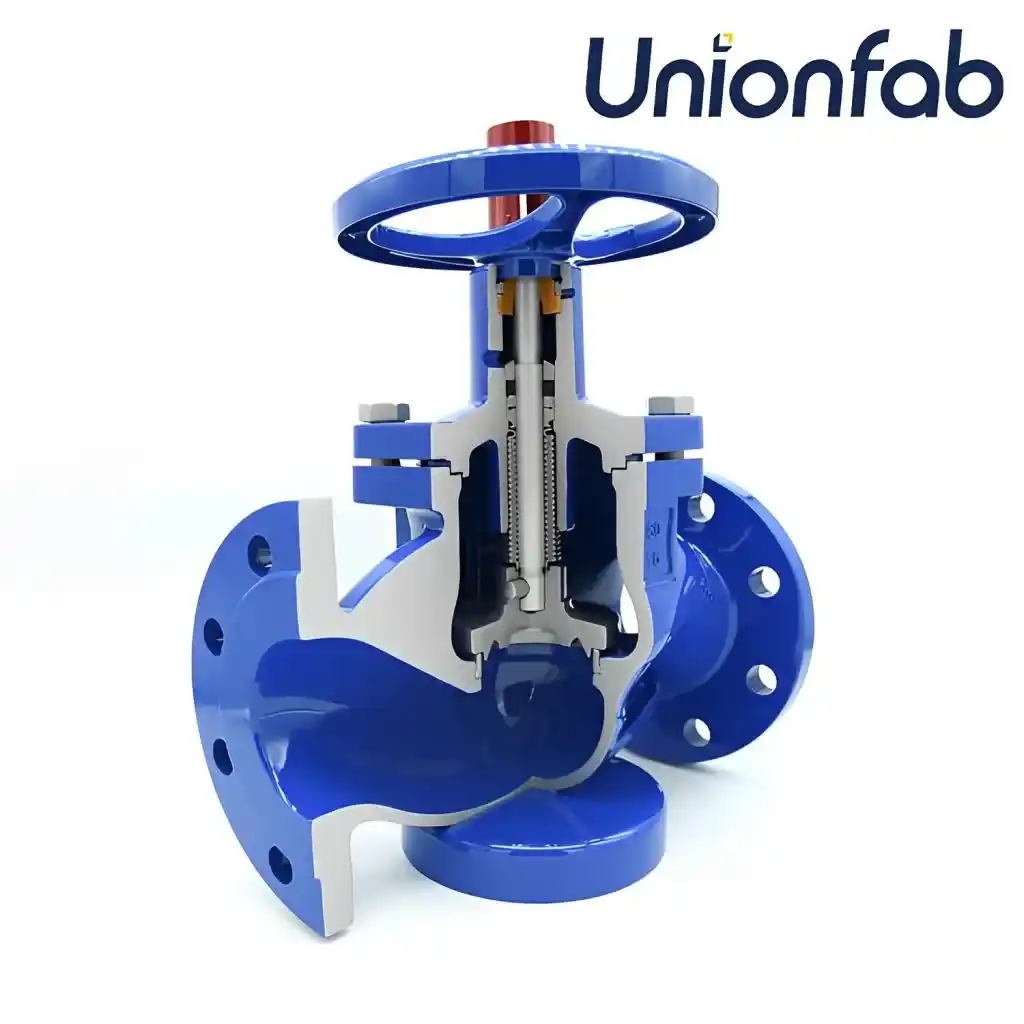
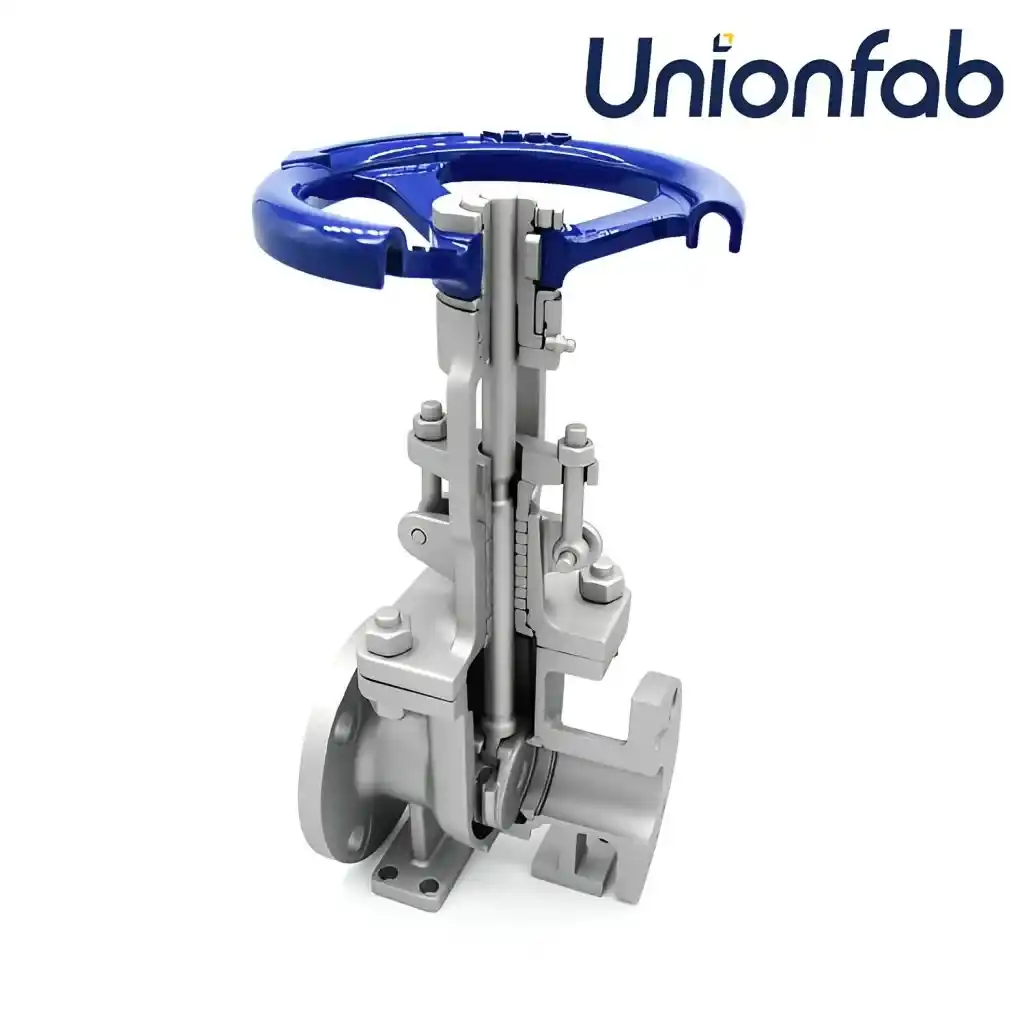
Functional prototypes are more fully developed versions of a design that demonstrate key functionality but may not be finalized in terms of appearance or production feasibility.
Small Batch Production
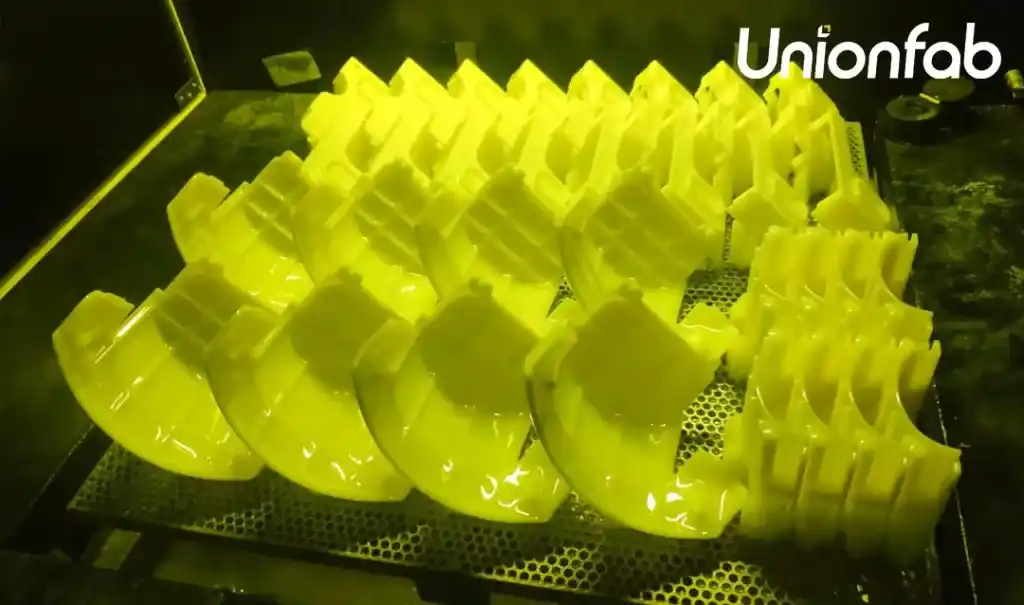
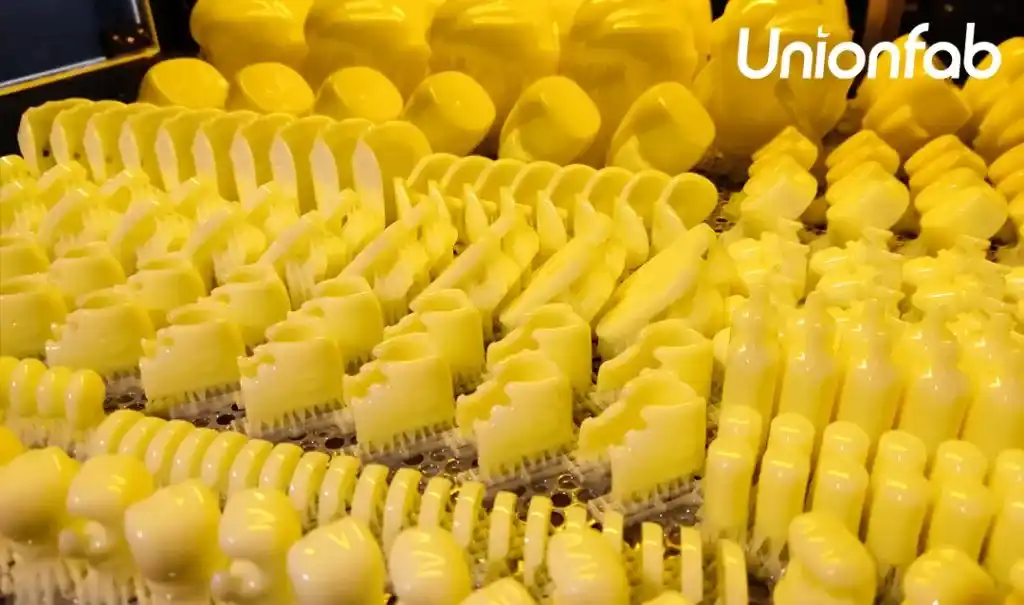
Production runs from a handful to a few hundred parts are well-suited to SLA. Larger volumes may be more cost effective on alternative production technologies.
Industry Applications
Industries like medical devices, automotive, consumer electronics commonly use SLA for design verification casts/tooling or initial low-rate production needs before high-volume manufacturing.
SLA Rapid Prototyping in Various Industries
Aerospace and Defense
- Producing functional prototypes and form, fit and function testing of parts for aircraft before switching to another production method like injection molding.
- Customized parts in limited quantities for UAVs.
- Creating assembly and installation jigs, fixtures and tools.
Healthcare and Medical Devices
- Prototyping and testing implants, prosthetics, surgical tools and devices.
- Producing models for pre-operative planning and surgical training/simulation.
- Manufacturing custom fitting models for dental aligners, orthotics and prosthetics, etc.
Automotive
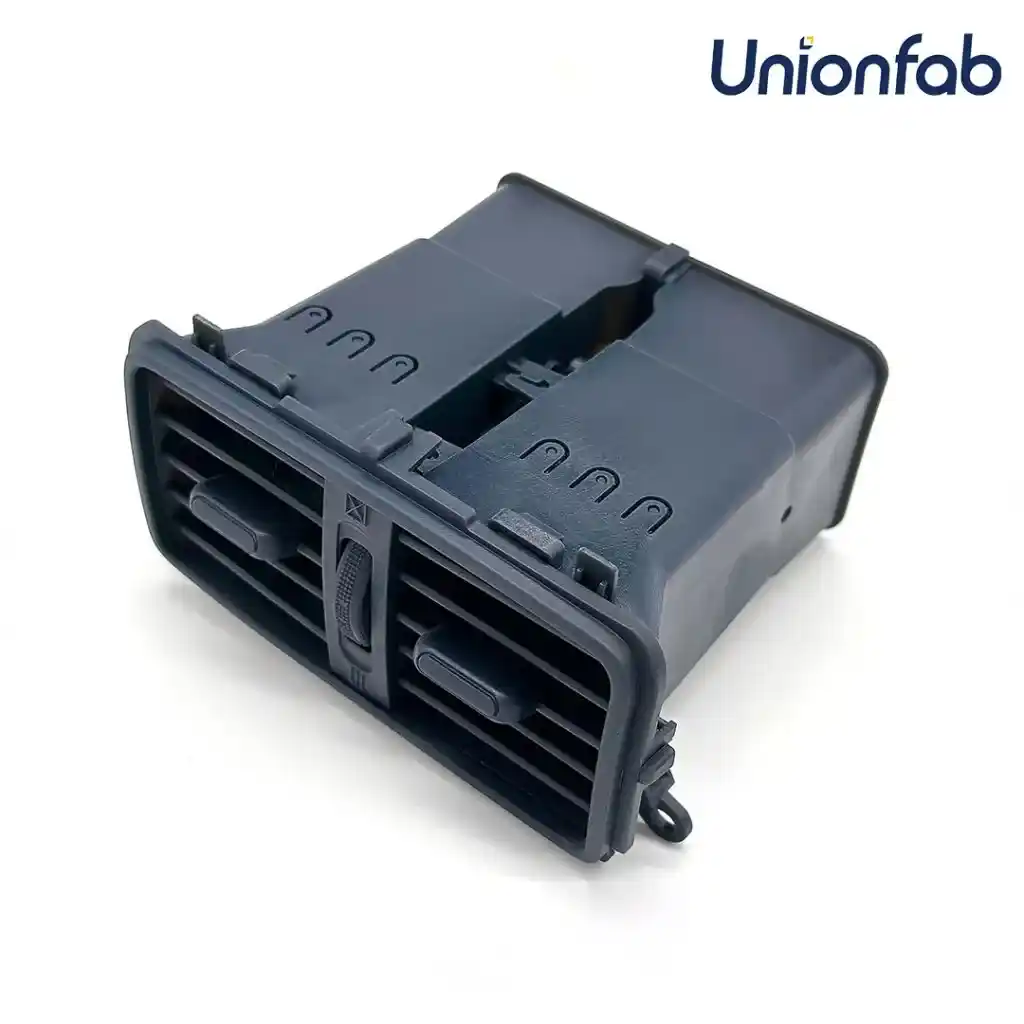
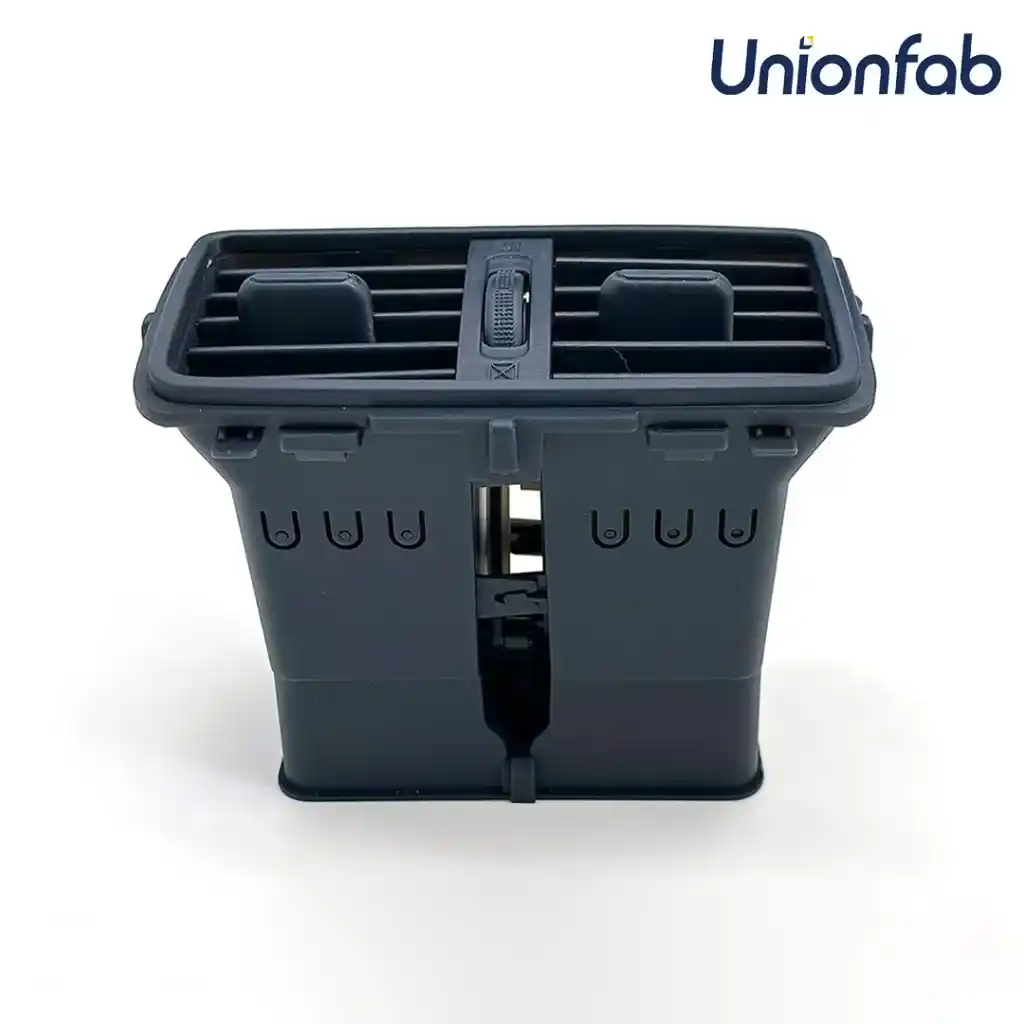
- 3D printed prototypes allow for rapid design iteration of parts, vents, consoles, trims etc.
- Producing low volume custom interior and exterior components.
- Jigs, fixtures and assembly tools improve quality control and efficiency.
Consumer Electronics
- Quickly prototyping devices, components, enclosures prior to manufacturing.
- Printing custom accessories, mounts and cases on-demand.
- Producing presentation models and samples for design validation.
Art and Design
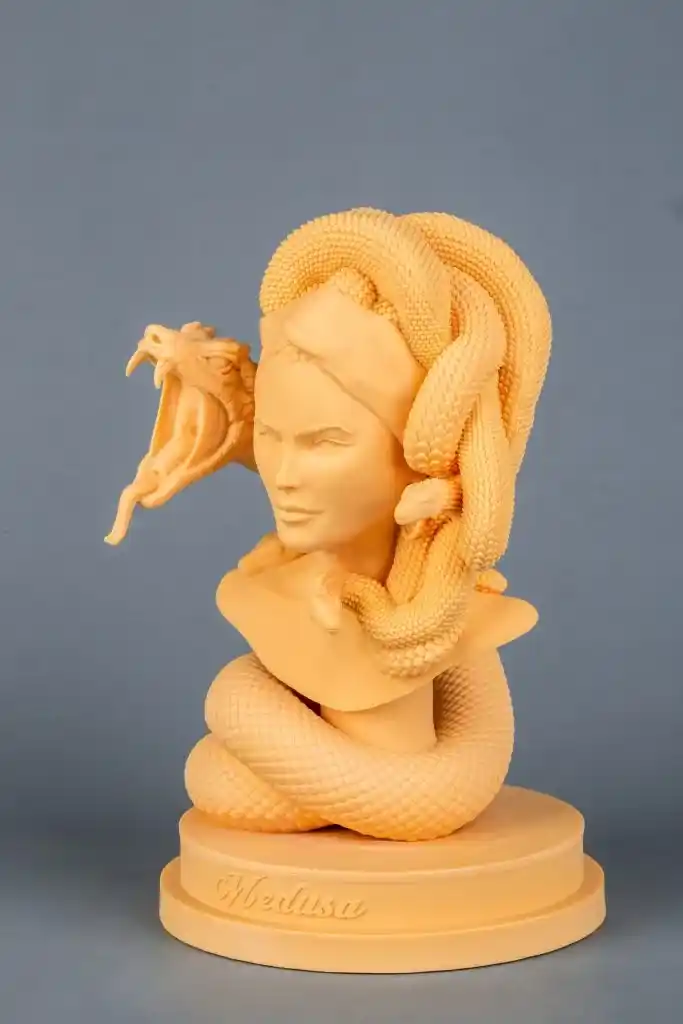
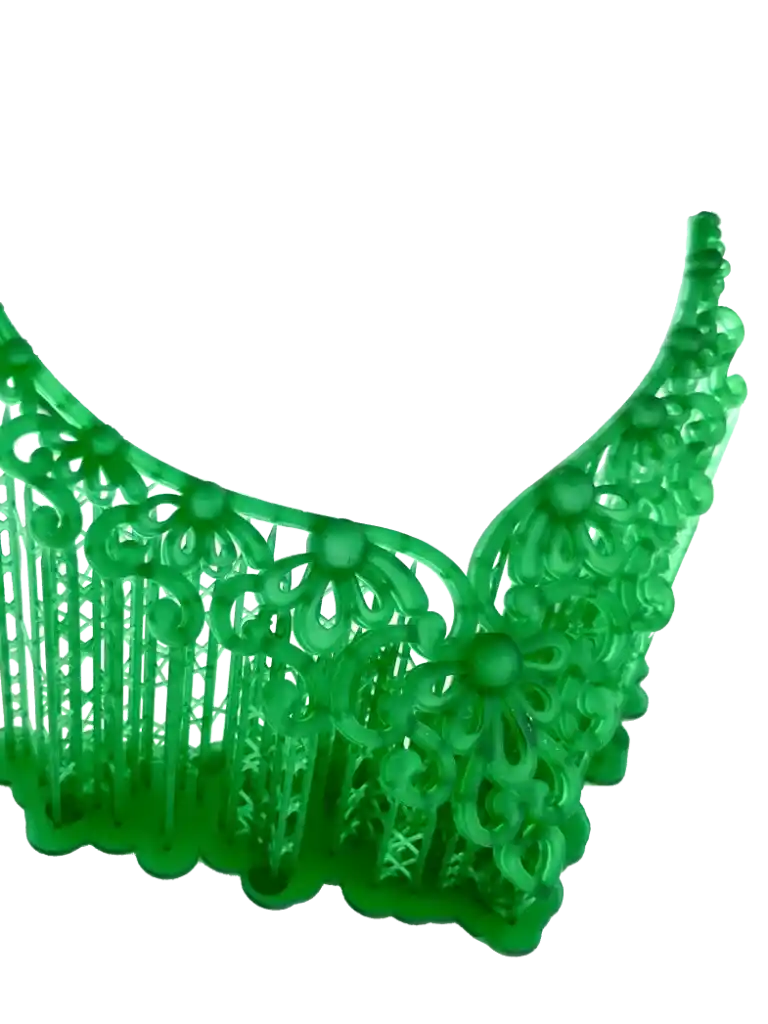
- Creating prototypes for fine art objects, jewelry, sculptural pieces, etc.
- Producing masters and production models for replication processes.
- Manufacturing limited runs of custom functional or decorative design objects.
SLA Rapid Prototyping: Challenges and Limitations
Material Costs
- Resins used in SLA can be more expensive on a per-volume basis than plastics for injection molding.
- Material costs need to be considered in the number and size of prototypes required.
Size Constraints
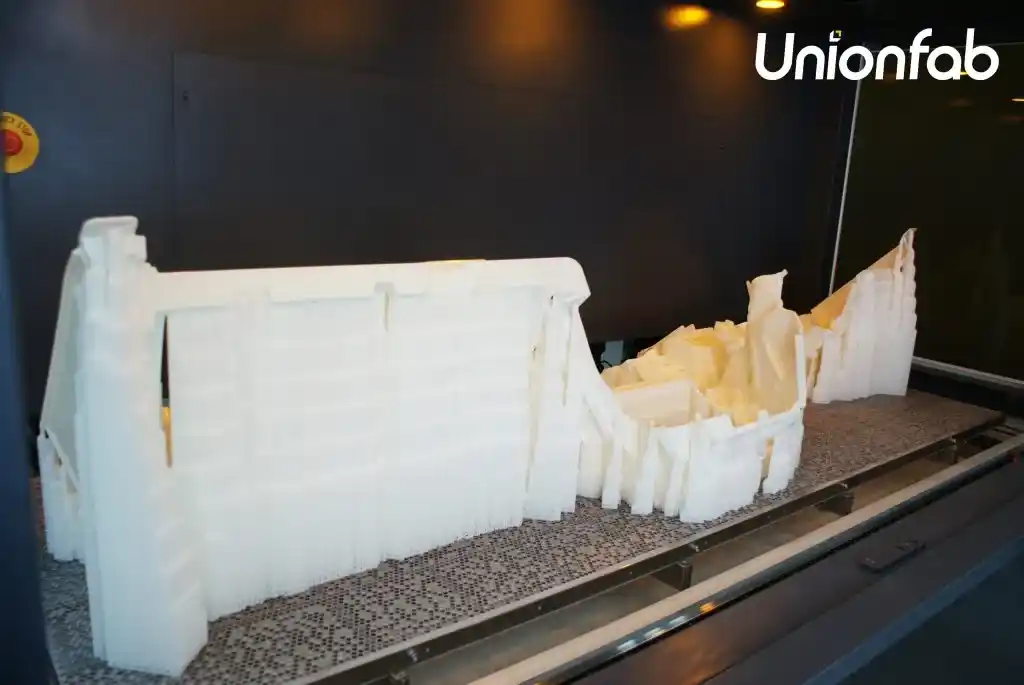
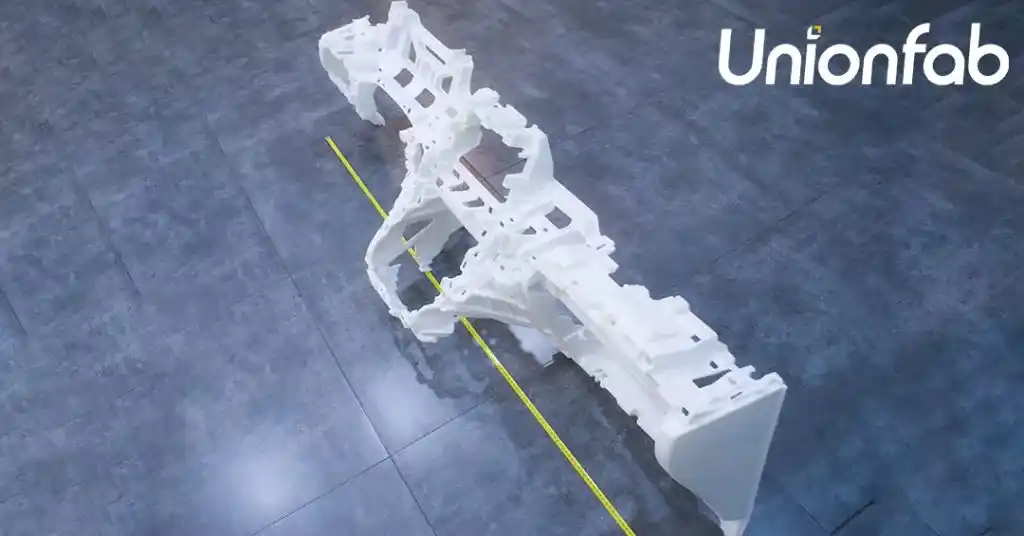
- Build volume is limited by the size of the SLA printer’s vat and build platform (now up to 2100 x 700 x 800mm at Unionfab).
- Large or unusually shaped parts may need to be split into multiple pieces and joined later.
Post-Processing Challenges
- Supports must be removed which can be difficult for complex geometries.
- Parts require washing/curing to complete polymerization which increases time and handling.
- Surface finishing may be needed through additional sanding or polishing.
Other Limitations
- SLA parts are typically made of resin materials that may not have the durability or temperature resistance for long-term use.
- Surface finish is usually rougher than molded plastic parts.
- Moving mechanical joints can degrade more rapidly than production materials.
- Curing and shrinkage result in less accurate dimensions vs production molds.
- Stress concentrations occur more easily than molded plastic.
The Future of SLA Rapid Prototyping
As SLA technology continues to advance, the future looks promising for further reducing its limitations and increasing its applications:
Improved Material Properties
- New resins will provide improved material properties – tougher, more temperature resistant plastics suitable for end-use prototyping.
- New initiatives like multi-material SLA will introduce elastomers, waxes and other materials for functional molding prototypes.
Advanced Printing Technology
- Higher laser intensities and resolutions will enhance detailing and surface finishes, rivaling injection molded parts.
- Bigger build volumes on SLA machines will accommodate larger prototype sizes without assembly.
Technology Integration
- Integrated hardware and software will optimize printer parameters to fabricate parts with exacting tolerances.
- Cloud-based and mobile solutions will make SLA prototyping even more accessible to designers everywhere.
Sustainability-Focused Innovations
- Bio-Based Resins: Resins made from plant oils or agricultural byproducts offer eco-friendly material options, reducing reliance on petroleum sources.
- Remanufacturing and Refill Stations: Stations for resin cartridges and parts are extending the lifecycle of SLA printers and consumables, minimizing single-use waste.
Conclusion
In this exploration of SLA Rapid Prototyping, we discussed the core principles, applications, and future advancements. Key takeaways include:
- SLA’s layer-by-layer photopolymerization process enables intricate prototypes.
- Design, orientation, material choices, and post-processing play key roles in achieving successful prototypes.
- Material selection considers properties, biocompatibility, handling, storage and compatibility.
- SLA serves industries like aerospace, healthcare for concepts, functions, and small production batches.
- Ongoing developments promise improved materials, detailing, size, multi-material use, technology advancement and sustainability innovations.
Embrace SLA Rapid Prototyping with Unionfab
Whether you’re a designer, engineer, artist, or entrepreneur, embracing SLA technology opens doors to faster, more efficient product development and design iteration.
Unionfab stands ready to support your prototyping needs. We offers cutting-edge solutions and expertise to help bring your ideas to life with precision and speed. Start you rapid prototyping with us and get a free quote!