Discover how 3D printed injection molds offer unmatched design flexibility, fast development, and low costs.
Introduction
Traditionally, injection molding relies on expensive metal molds. However, 3D printing offers a new approach for creating injection molds. This technology allows for quicker production and lower costs, particularly for situations requiring low volume production runs.
Understanding Injection Mold
Functionality and Importance in Manufacturing
An injection mold is a vital tool in manufacturing, specifically designed to create plastic parts in high volume. It functions like a mold for casting, but instead of liquid metal, it uses molten plastic.
- Mass Production: Injection molding excels at producing large quantities of identical plastic parts efficiently and consistently.
- Design Flexibility: Molds can be crafted to create parts with complex geometries and intricate details.
- Material Versatility: A wide range of plastic materials can be used in injection molding, allowing for parts with specific properties like strength, flexibility, or heat resistance.
- High Precision: Injection molding produces parts with high dimensional accuracy and repeatability.
- Cost-Effectiveness: For high-volume production, injection molding becomes very cost-effective due to the efficiency and minimal material waste.
Traditional Injection Mold Production Methods
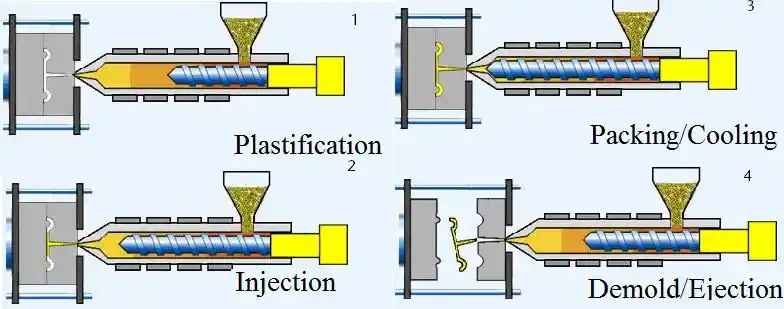
Source: rapiddirect.com
Traditionally, injection molds are crafted from high-grade steel or aluminum using subtractive manufacturing techniques like CNC machining. This process involves:
- Creating a digital computer-aided design (CAD) file of the mold.
- Utilizing CNC machines to precisely remove material from a solid block of steel or aluminum to match the mold cavity design.
Challenges of Traditional Methods:
- This process can be time-consuming and labor-intensive, requiring skilled machinists to operate the CNC machines.
- The cost of steel or aluminum, especially for larger or complex molds, can be significant.
- Lead times for mold production can be lengthy, impacting product development timelines.
Undersanding 3D Printed Injection Mold
Introduction to 3D Printed Injection Molds
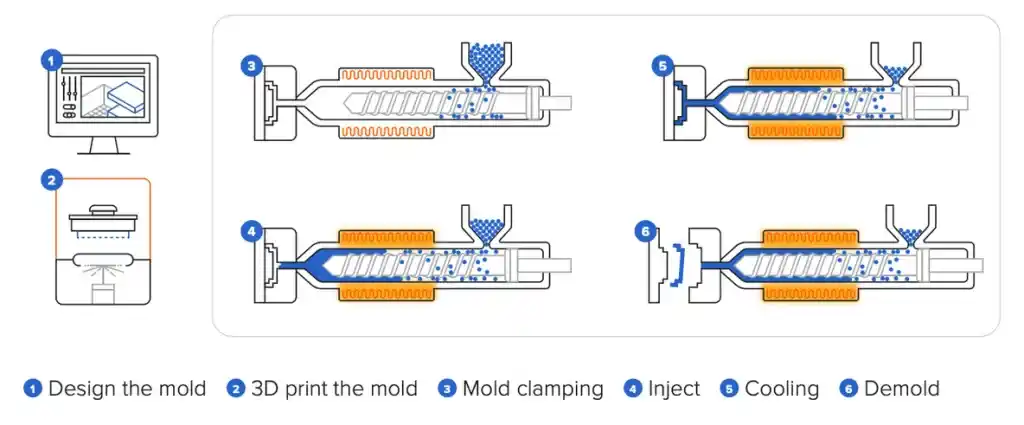
Source: formlabs.com
3D printed injection molds represent a new approach to mold production, utilizing additive manufacturing technology.
Instead of removing material from a solid block, a 3D printer builds the mold layer-by-layer based on a digital design file.
Materials used for 3D Printed Molds
- High-performance resins: These offer good heat resistance and can withstand the injection process for a limited number of cycles.
- Engineering-grade filaments: Some advanced filaments provide improved heat deflection and durability compared to standard filaments.
Advantages over Traditional Molds
3D printed injection molds offer several advantages, particularly for low-volume production scenarios.
Design Freedom and Customization
3D printing allows for complex geometries and intricate features that might be difficult or expensive to achieve with CNC machining.
Rapid Prototyping and Iterative Development
The faster turnaround time for 3D printed molds enables quicker creation of prototypes for testing and design iteration. This reduces the time it takes to bring a product to market.
Cost Efficiency and Time Savings
Compared to traditional methods, 3D printing molds can be significantly cheaper, especially for low-volume production runs.
The reduced need for complex machining and skilled labor contributes to cost savings.
Additionally, the faster printing process brings down lead times for mold production.
Benefits of 3D Printed Injection Molds
Enhanced Design Flexibility
Unlike traditional CNC machining with its limitations on material removal, 3D printing allows for the creation of molds with highly complex geometries and intricate details.
Undercuts, internal channels, and other intricate features can be incorporated directly into the mold design, offering greater freedom in product design.
Accelerated Time-to-Market
The speed of 3D printing significantly reduces mold production lead times compared to traditional methods. This allows for faster prototyping, design iterations, and quicker product development cycles.
Companies can bring innovative products to market faster, gaining a competitive edge.
Cost Savings and Economic Viability
3D printed molds can be significantly cheaper than traditional steel or aluminum molds, especially for low-volume production runs.
The elimination of expensive materials and the reduced need for skilled labor contribute to cost savings. This makes it more economically viable to produce small batches of parts or prototypes.
Complex Geometries and Intricate Details
3D printing excels at creating complex geometries that would be challenging or cost-prohibitive with traditional machining.
This allows for the production of parts with intricate details, internal channels, undercuts, and other features that enhance functionality or aesthetics.
Applications of 3D Printed Injection Molds
Automotive Industry
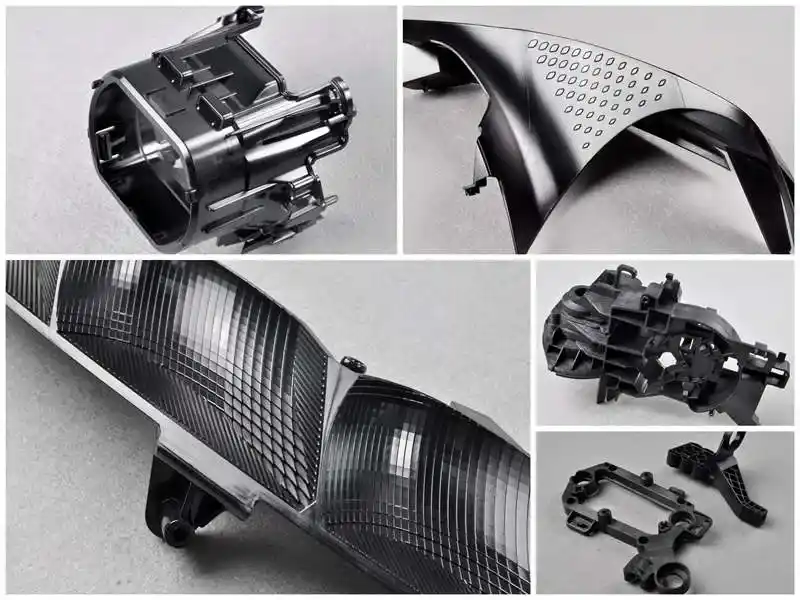
Source: autoprotoway.com
- Low-volume production of car parts: 3D printed molds can be used to create custom parts, prototypes for new vehicle models, or limited-edition components in a cost-effective way.
- Functional testing and prototyping: Rapidly produced molds enable the creation of parts for wind tunnel testing, aerodynamic optimization, and functional testing of new designs.
- Jigs and fixtures: 3D printed molds can be used to create custom jigs and fixtures for assembly line applications, often at a lower cost and faster turnaround time compared to traditional methods.
Aerospace Sector
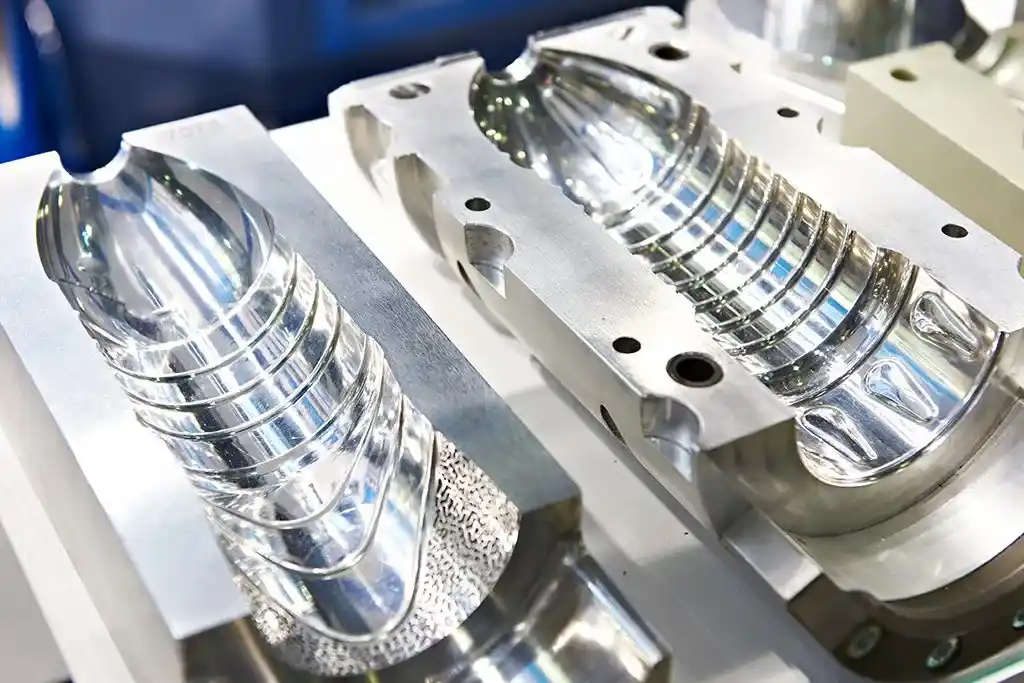
Source: pmcplastics.com
- Manufacturing lightweight components: The ability to create complex geometries with 3D printed molds allows for the design of lightweight yet strong plastic parts for aircraft interiors or unmanned aerial vehicles (UAVs).
- Rapid prototyping of aerospace parts: The quick turnaround time of 3D printed molds is ideal for creating prototypes for wind tunnel testing and design iteration in the aerospace industry.
- Low-volume production of custom parts: Aerospace applications often require custom components for specific purposes. 3D printed molds allow for cost-effective production of these parts in small quantities.
Medical Device Manufacturing
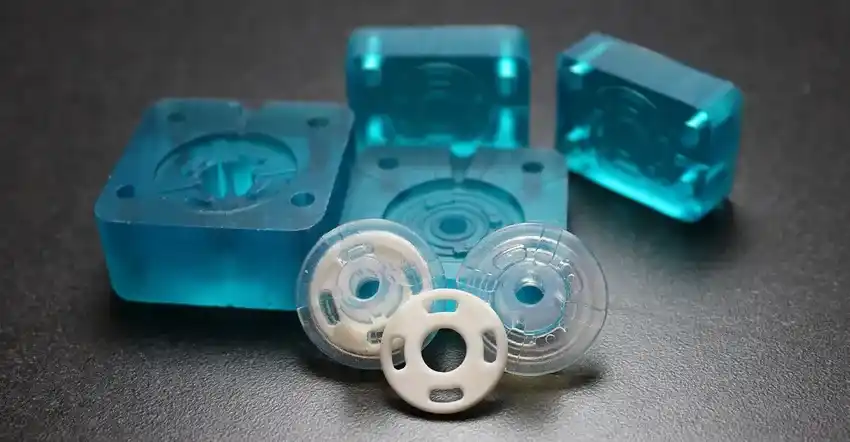
Source: plasticstoday.com
- Prototyping of medical devices: 3D printed molds are valuable for creating functional prototypes of medical devices for testing and design validation before mass production.
- Low-volume surgical tools: Certain surgical tools may only be needed for specific procedures or in limited quantities. 3D printed molds can be a cost-effective option for producing these specialized tools.
- Customization of medical devices: For patients requiring personalized medical devices, 3D printed molds can be used to create custom implants or prosthetics with precise geometries.
Consumer Goods Production
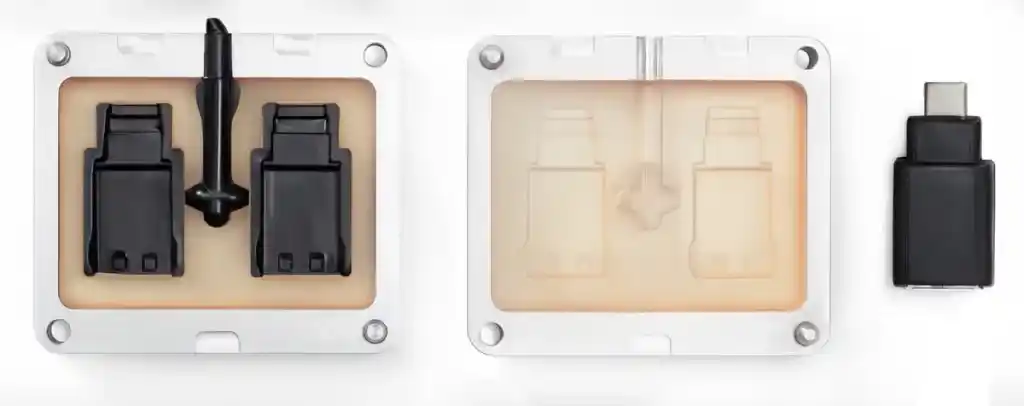
Source: formlabs.com
- Limited edition products: 3D printed molds can be used to create molds for limited edition consumer goods, allowing for quick production and design variations.
- Functional prototypes for consumer products: The ability to rapidly iterate on designs makes 3D printed molds ideal for creating functional prototypes of new consumer products before mass production.
- Short-run production of seasonal items: For seasonal products with limited production runs, 3D printed molds offer a cost-effective and fast turnaround option.
Considerations for Producing 3D Printed Injection Mold
Material Selection and Compatibility
Material properties
Choose a 3D printing material with high heat deflection temperature to withstand the molten plastic during injection.
Common options include high-performance resins and engineering-grade filaments with good thermal resistance.
Compatibility with injected plastic
Ensure the 3D printed mold material is compatible with the type of plastic being injected. Some materials might react chemically with certain plastics, leading to part defects or mold degradation.
Example
When producing a mold for Polypropylene (PP) parts, a high-temperature resistant Nylon filament might be a suitable choice due to its compatibility and thermal properties.
Surface Finish and Tolerance Requirements
Surface finish
The surface finish of the 3D printed mold directly impacts the final finish of the produced plastic parts.
For parts requiring a smooth surface finish, a finer layer height and potentially post-processing techniques might be necessary.
Dimensional tolerances
3D printing has inherent limitations in dimensional accuracy compared to CNC machining.
Consider the required tolerances for the final parts and adjust the printing parameters or employ post-processing methods to achieve the desired precision.
Post-Processing and Finishing Techniques
Surface smoothing
Techniques like polishing, sanding, or vapor smoothing can improve the surface finish of the 3D printed mold, leading to better quality parts.
Sealing and reinforcement
For improved durability, the mold might be coated with heat-resistant resins or undergo infiltration processes to enhance its resistance to high temperatures and pressures.
Regulatory Compliance and Quality Assurance
Medical Devices
For medical applications, the 3D printing process and materials used must comply with stringent regulations like ISO 13485 to ensure patient safety and device functionality.
Food Contact Applications
If the molded parts will come into contact with food, the 3D printing materials and any post-processing techniques must comply with food safety regulations to prevent contamination.
Conclusion
3D printed injection molds offer a compelling alternative to traditional methods for low-volume production, rapid prototyping, and applications requiring design flexibility.
While considerations like material selection, post-processing, and limitations in durability exist, the faster turnaround times and cost-effectiveness make them a valuable tool for various industries.
Produce Flawless Products at Unionfab
Unleash your design potential with Unionfab’s comprehensive 3D printing and injection molding support.
Our expert team empowers your creativity by providing all the resources you need, from material selection to exceptional finishing services. Together, we can transform your innovative ideas into flawless reality.
