Pick the perfect 3D printing method for your project with comparisons between SLA, SLS and SLM based on output quality, material options, speed, cost and more.
Introduction
There are multiple 3D printing techniques with distinct pros and cons for different applications. Stereolithography apparatus (SLA), selective laser melting (SLM), and selective laser sintering (SLS) are three of the most known approaches. They differ in key aspects that determine their suitability for specific applications.
In this article, we will compare and contrast SLM, SLA, and SLS to help you pick the perfect method for your project based on material choice, resolution, part strength, Finishing choice, cost, speed, and industry application.
SLA, SLS and SLM: A Brief Summary
You can notice this by the first glance: the first two letters of the abbreviations SLA, SLS and SLM are identical. However, upon closer examination, more fundamental differences emerge. While in SLS and SLM, “SL” stands for “selective laser” and implies closer relationship between the two methods, this does not hold for SLA (Stereolithography).
Adding to the complexity, SLA and SLM technologies are also referred to by alternative names:
SLA:
- SL
- Vat photopolymerization
SLM:
- Direct Metal Laser Sintering (DMLS)
- Laser Powder Bed Fusion (LPBF)
- Direct Metal Printing (DMP)
However, the underlying principles remain the same.
All three represent 3D printing technologies, share things in common and also vary in significant ways. Organizing the comparisons into categories clarifies these distinctions. To begin, we will look into how they are sorted into categories by 3D printing process.
Categories of 3D printing process
3D printing, also known as its industrial production name additive manufacturing (AM), refers to a suite of revolutionary techniques that rapidly prototype and produce parts directly from digital 3D models. Instead of subtractive methods that remove material from the feedstock, 3D printing builds parts up layer by layer using materials like plastic or metal powder.
The ISO/ASTM 52900:2015 terminology standard defines seven categories of additive manufacturing (AM) processes based on differences in material and the process used to join the material. The seven categories of additive manufacturing processes, along with example technologies for each, are as follows:
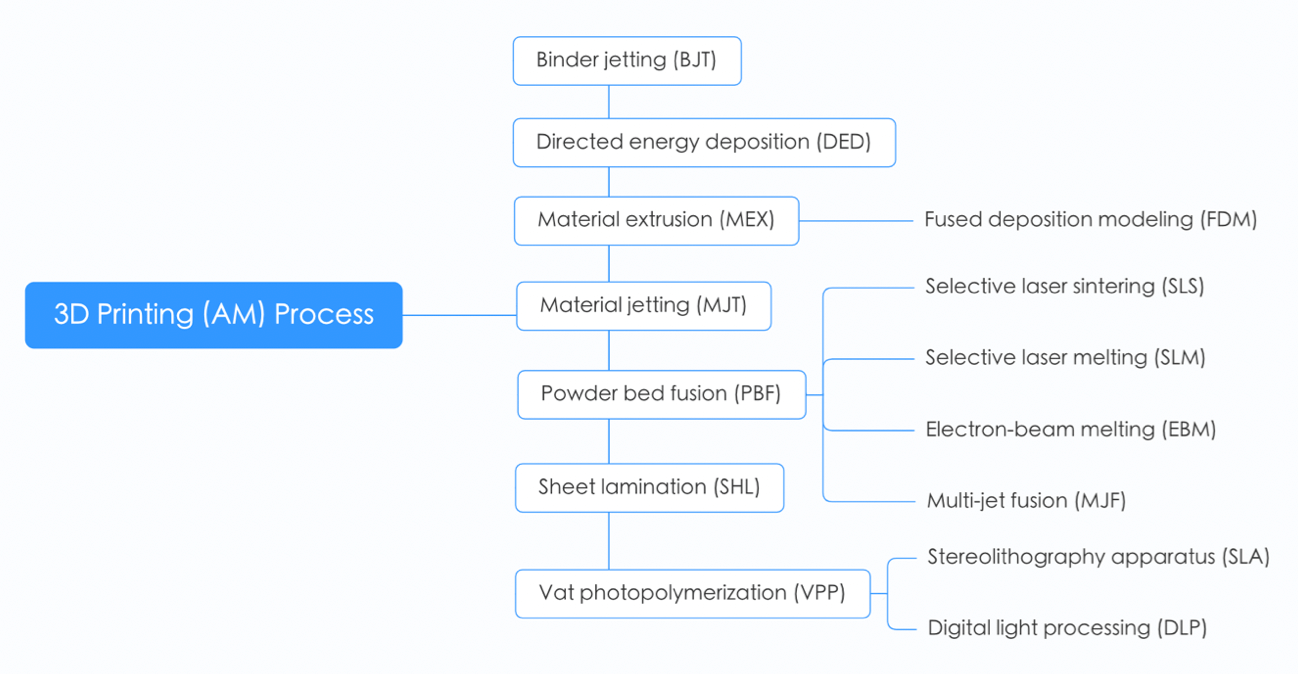
3D Printing (AM) Process
In this map, you can see SLS and SLM belong to the same powder bed fusion (PBF) process. SLA is under a different category — VPP — and shares the same process with another famous AM method: digital light processing (DLP).
SLA, SLS and SLM processes
In a VPP process, SLA uses photopolymer resin and UV laser to solidify each layer. Here are some key details:

SLA process
- SLA is an early and widely used 3D printing technology. SLA-1, which was introduced in 1987, is the world’s first commercial 3D printer.
- SLA uses a vat of liquid photopolymer resin as the build material.
- An ultraviolet (UV) laser traces and cures the first layer of the 3D model on the surface of the liquid resin. After curing a layer, the build platform lowers by one layer thickness into the resin vat. A wiper then coats a thin layer of liquid resin over the cured layer.
- The UV laser then traces and cures the next layer, fusing it to the layer below. This process repeats layer by layer until the entire 3D part is cured from the bottom up.
- Any excess uncured liquid resin is drained from the vat and washed away.
In a PBF process, SLS and SLM uses laser as the power to fuse powdered material into a solid 3D part, layer by layer. To be more specific:
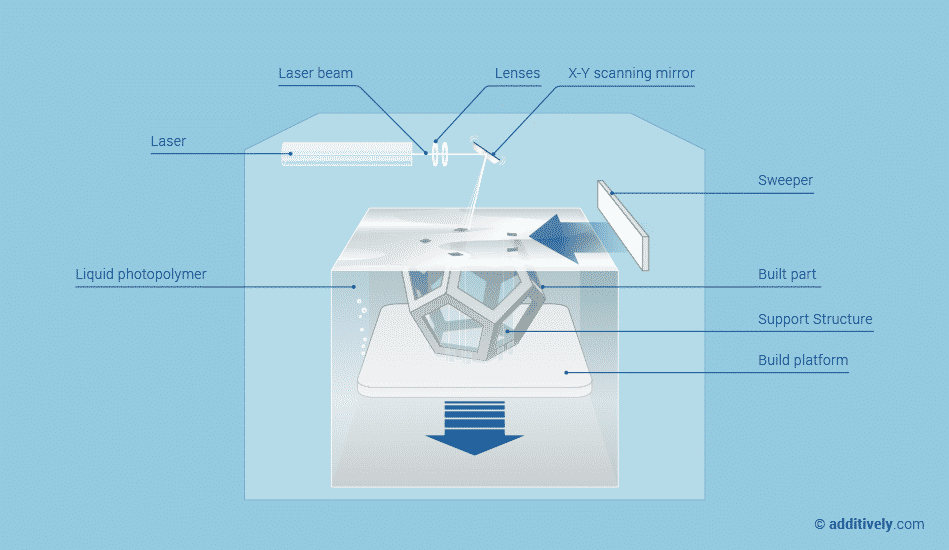
SLS and SLM process
- A thin layer of powder – ranging from nylon or polyamide (SLS) and metal (SLM) – is spread over a build platform using a roller.
- A high-power laser traces the cross section of the part for that layer based on a digital model. The energy source either partially melts the powder (SLS) or fully melts it (SLM) to fuse it together into a solid layer.
- The build platform moves down and a new layer of powder is spread, then selectively fused to the layers below to build the 3D part, layer by layer.
- Unfused exc ess powder acts as support material and can often be recycled.
SLA vs SLS vs SLM: Major differences
Material choice
SLA uses liquid photopolymers and resins as build material. There are many resins available for this 3D printing process, providing a wide range of options with different properties like heat resistance, high detail, durability, flexibility, and more.
SLS works with polymers, composites and several metal powders. Thermoplastics like thermoplastic polyurethane (TPU) and nylon are common with this method.
SLM is limited to metal powder. Some usual choices include stainless steel, titanium, aluminum, and maraging steel.

Browse through our wide selection of materials here, choosing properties to filter materials that meet your needs.
Resolution
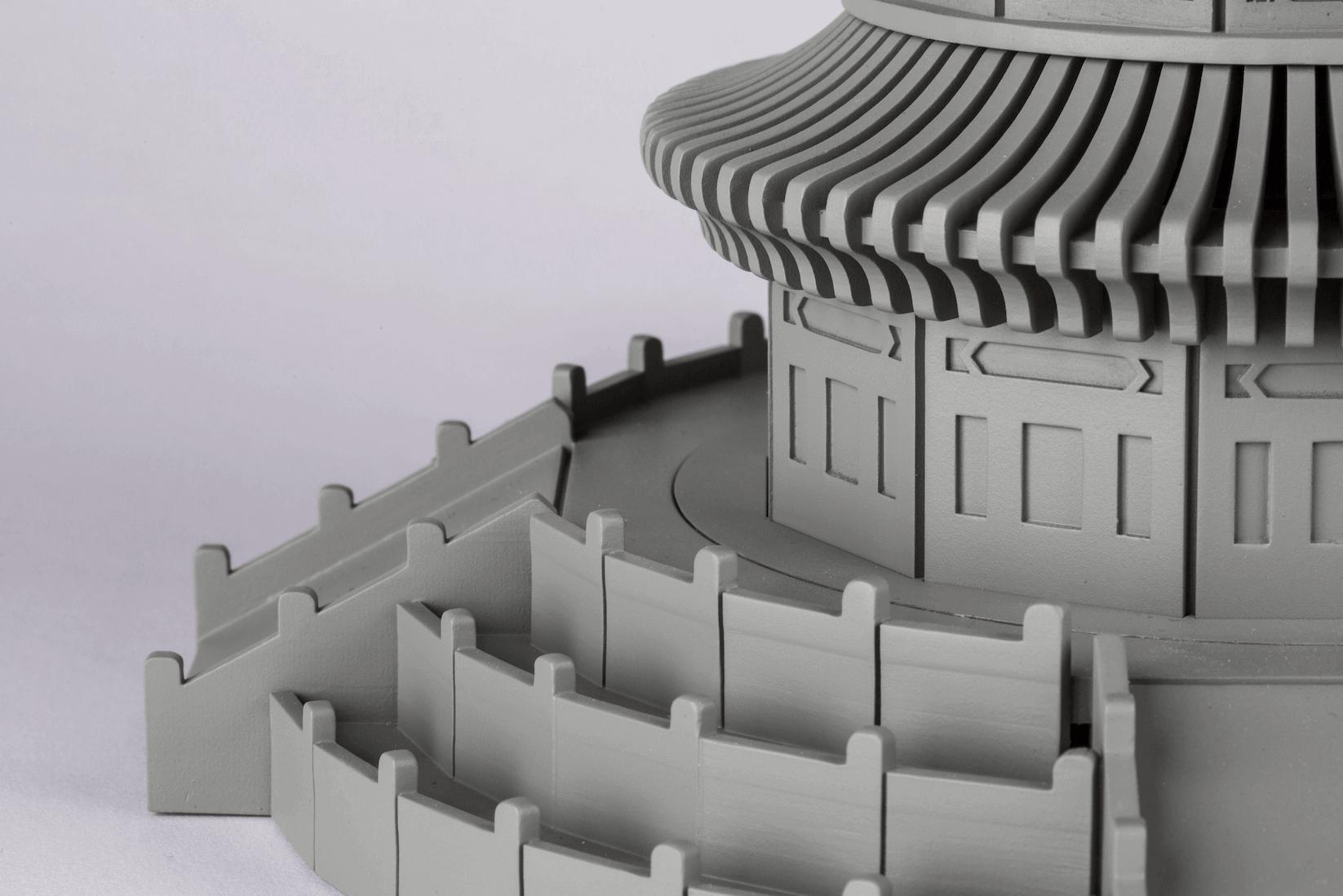
SLA print detail
In terms of precision and part accuracy, SLA and SLM are generally more precise than SLS. SLA and SLM can achieve resolutions down to 20-100 microns due to curing thin layers of resin or metal. SLS requires thicker layers, in the 100 to 150 mm range. This affects the precision and surface smoothness of the final parts. However, in Unionfab, we use the latest generation of SLS technologies to meet tolerances of +– 0.010” or +– 0.002” per inch, achieving high precision. Click to see the advantages we offer with SLS 3D printing service.
Part strength
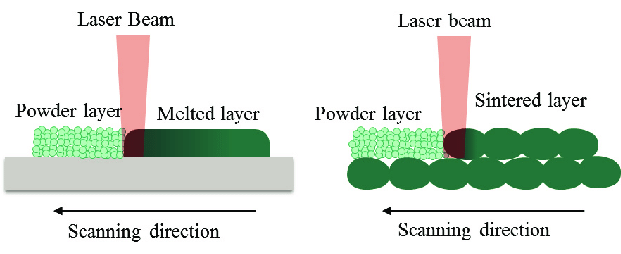
State-of-the-art Laser Additive Manufacturing for Hot-work Tool Steels – Scientific Figure on ResearchGate.
SLA parts have the lowest strength due to the nature of the resin material — resins do not achieve full densification and typically contain voids. Besides, many resins are not thermally or chemically stable over extended time periods, leading to material degradation and changes in mechanical properties. SLM produces the strongest 3D printed parts with strength close to conventional metal components due to fully melting metal powder, achieving nearly 100% density. SLS achieves partial densification since particles are sintered but not fully melted. It is suitable for functional prototypes and jigs that require durability but not high load-bearing strength.
Geometry
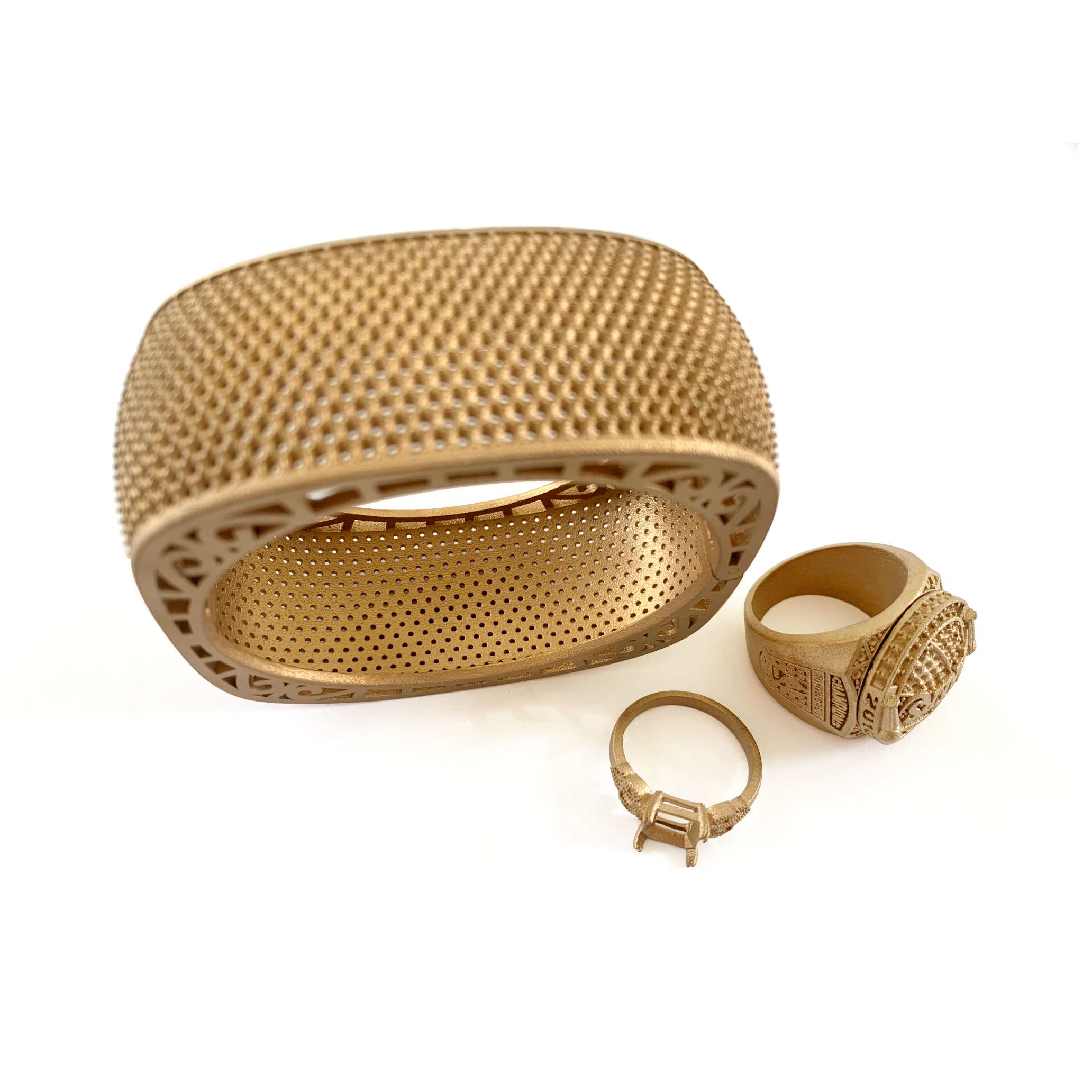
SLM metal geometry
SLM can print the most complex geometries of the 3 techniques, especially for metal parts. It can produce functional components with moving parts, intricate channels and hollow structures.
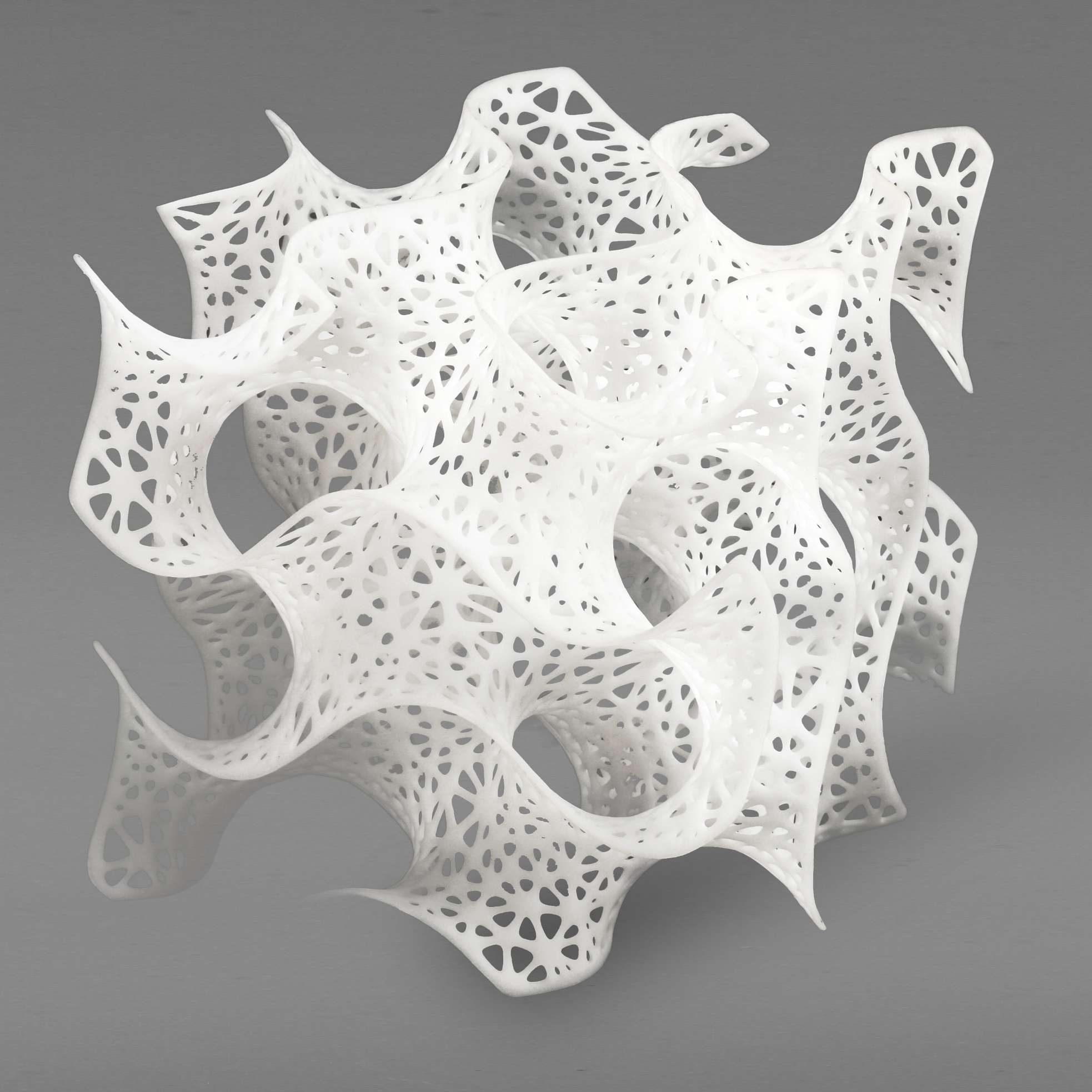
SLA geometry
SLA resins have lower temperatures and viscosities, so they can produce moderately complex geometries with some overhangs and hollow areas. However, multiple materials are available to achieve some functional parts with composite resins.

SLS nylon geometry
SLS nylon powders have the highest viscosity of the 3 techniques, so they struggle the most with complex internal channels, moving parts and overhangs that require support structures. However, flexible nylon materials allow for some functional parts with hinges and joints.
Finishing

The finish of 3D printed parts depends highly on the technology and post-processing used. SLA parts typically come off the build platform with a smooth surface finish due to the liquid resin. Some SLA resins can produce glossy or matte finishes. SLS and SLM parts often require post-processing like polishing, coating or vapor smoothing to achieve smooth functional finishes. After these procedures, dyeing and painting may be applied to printed parts to achieve beauty or corrosion-prevention purpose.
Speed
Generally, the length of time it takes to produce parts depends upon the complexity of the design and the size. Printing time can last anywhere from hours to weeks. SLA 3D printed parts do not require tooling, reducing the manufacturing lead time from weeks to 2-3 days. SLS is also quite fast. Parts can be shipped within a week, about 3-4 days. It usually takes longer to print SLM parts, but Unionfab’s productivity enables us to deliver high-quality metal parts to customers in just a handful of days – often between 5 and 7 days.
Cost
Costs vary significantly between the technologies based on material and production costs. SLA resins tend to be the most affordable material option. SLM metal powders still have high costs due to their premium properties. SLS plastic powders are more economical than SLM metals but generally cost more than resin. Production costs also differ based on factors like part size, part geometry, production volume, speed, post-processing, and throughput.
Estimating costs for 3D printed parts can be tricky due to many variables. However, our quote tool aims to provide a quick and precise cost estimate based on key part properties. If you already have a model file, click here to try our free quote service.
Environmental impact
SLA resins tend to have a lower environmental impact due to less material waste and potential for reuse. However, they contain toxic chemicals that require safe disposal. SLS and SLM powders have a higher impact due to material production but benefit from powder recycling. The recyclability of the metal parts themselves partly offsets this. Overall, none of the processes are inherently “green” and all benefit from material recycling, process optimization and transitions to sustainable feedstocks.
Industry application
SLA is suitable for prototyping in many industries due to its ability to produce high-resolution parts using multiple resin materials. It is used in product design, toys, consumer goods, dental and hearing aids.
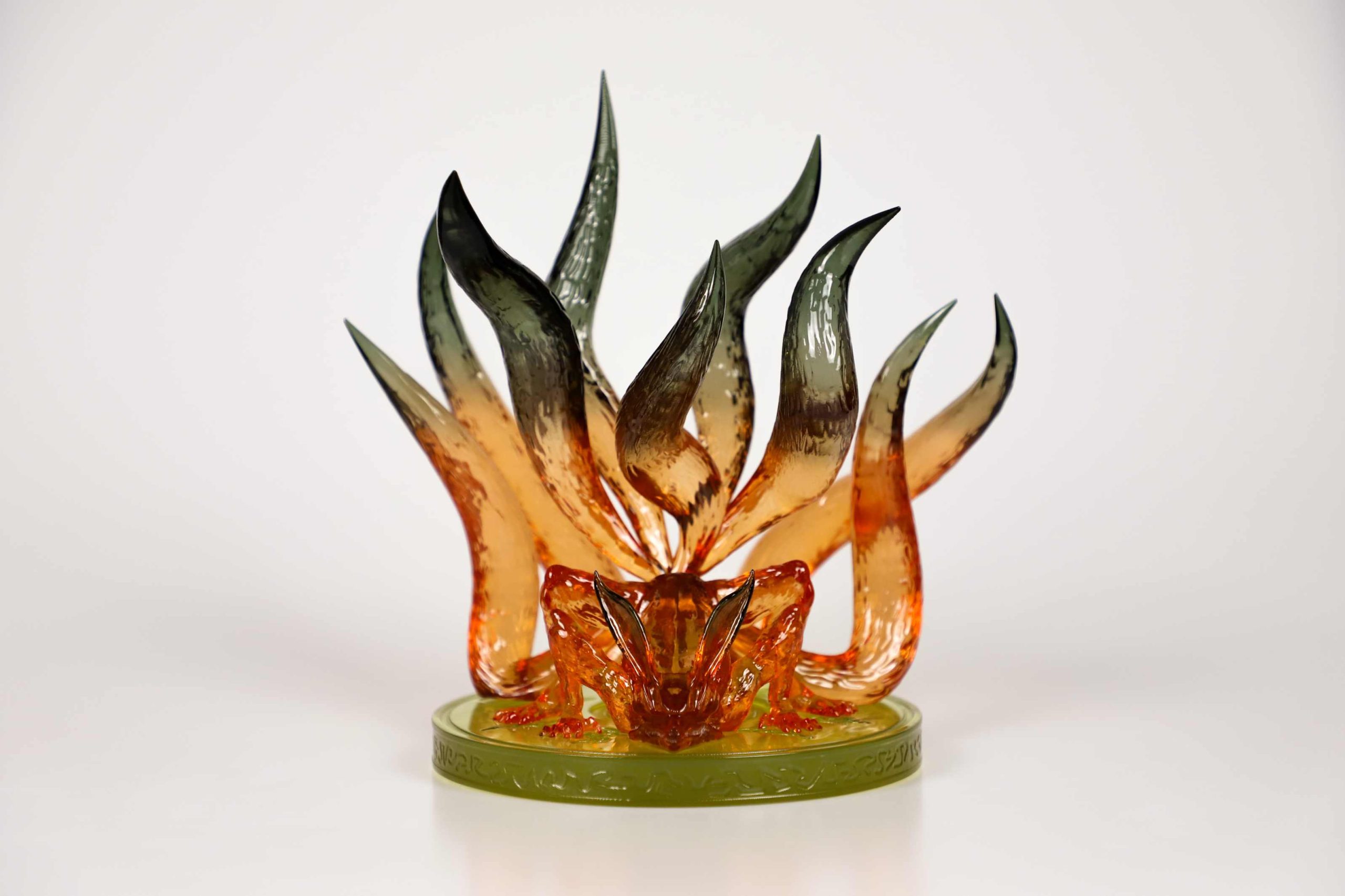
SLA art design
- Product Design – Design models, form studies and fit/function prototypes for consumer products. SLA is also widely used in car modification.
- Toys – Miniatures, collectibles and playsets produced with SLA resin are with fine details.
- Consumer Goods – Jewelry casting patterns, hearing aid shells and eyewear frames.
- Dental – Custom dental crowns, bridges and veneers created from digital impressions and CAD designs.
SLS nylon and TPU parts are utilized for functional prototypes and low-volume production runs in industries like consumer electronics, product design, and medical. The durable, tensile parts can be manufactured cost-effectively in flexible materials.

SLS footware prototype
- Electronics – Enclosures, mounts and housings for circuit boards, batteries and wiring.
- Footwear – SLS is well suited for footwear design due to its ability to print flexible TPU materials and enable rapid design iterations – all valuable capabilities for shoe prototyping and production.
- Medical – Surgical guides , drill jigs and models used for pre-operative planning and implant placement.
SLM is often used for high-strength metal parts in industries like aerospace, automotive and medical devices due to its ability to produce functional metal components. It can create complex geometries for drone frames, engine components and surgical tools.
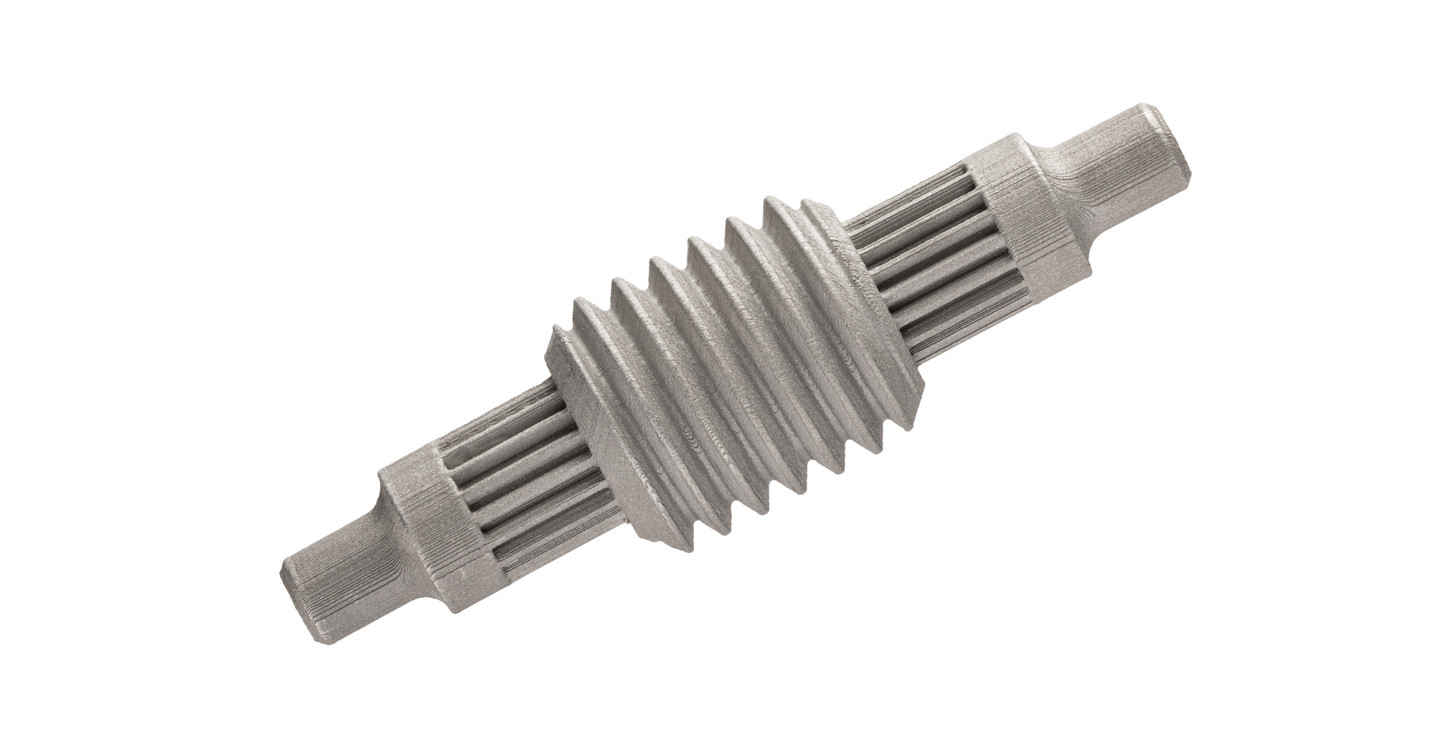
Functional metal part
- Aerospace – Complex metal lattice structures for 3D printed jet engine turbine blades like those made by GE Aviation. Titanium brackets for spacecraft.
- Automotive – High-strength metal parts like injection molds, connectors and hydraulics. Porsche has used 3D printed aluminum parts in their cars.
- Medical – Implants like knee replacements, hip stems and dental implants.
Conclusion
SLA uses UV light to cure liquid photopolymer resins, layer by layer. It produces parts with highest accuracy, precision and surface finish but lower durability. SLA’s features making it best for visual prototypes, models, products requiring good aesthetics but not high strength.
SLS uses laser to sinter polymer powder. It can offer durability and suitable for functional prototypes and low-volume production.
SLM uses high-powered laser to fully melt metal powder, layer by layer. It produces dense, functional metal parts suited for demanding applications like load-bearing metal components, tools and machinery.
For more detailed information, you may want to check our guide on SLA, SLS and SLM 3D printing technologies.
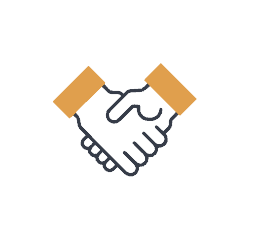
Join Unionfab Partner Program
FAQ
What are the merits and demerits of thin layer thickness?
Finer layer thickness provides several advantages for 3D printed parts:
- Higher resolution: Since the laser or light can focus on a smaller area, thinner layers enable smaller details and higher resolution parts.
- Improved surface finish: The stair-stepping effect between layers is reduced with thinner layers, providing a smoother surface.
- Greater precision and accuracy: Each layer introduces less deviation, enabling more precise dimensions when layers are stacked up.
However, thinner layers also have some drawbacks:
- Longer print times: Since more layers are needed to build the same part thickness, printing takes longer with thinner layers.
- Narrower process windows: Maintaining stable parameters like laser power and scan speed becomes more difficult with thinner layers.
Do note that thinner layer does not guarantee stronger or weaker printed parts. Different heights of layer introduce the tradeoff between material extrusions and cross-section.
The optimal layer thickness depends on balancing these benefits and flaws based on the requirements of the specific part and application.
What are the key considerations for choosing the optimal 3D printing method for your project?
Material requirements – What material properties do you need? Strength, flexibility, biocompatibility, etc. Each method has specialized materials.
Output quality – What resolution, surface finish and dimensional accuracy is required? SLA can produce the most precise parts while SLS has a rougher finish.
Production volume – How many parts do you need to produce? SLA is best for prototypes while SLM and SLS can produce mid-to-high volume runs.
Timescale – Do you need parts quickly or is a longer timeframe ok? SLA and SLM print faster than SLS generally.
Cost – Consider the cost of the printer, material and part production for your expected volume of parts. SLS tends to have lower material costs.
Post-processing – Some methods require more post curing, support removal and surface finishing of parts. Consider resource and time needs.
Design freedom – Some methods allow printing of more complex geometries with moving parts and thicker walls.
Repeatability – How consistent do you need print quality to be for functional parts? Some techniques offer better run-to-run repeatability