- Introduction
- Understanding CNC Robots and CNC Robot Arms
- Benefits of CNC Robots and Robotic Arms
- Challenges and Considerations
- Applications of CNC Manufacturing Robotics
- Case Studies and Specific Applications
- Future Trends in CNC Manufacturing Robotics
- Conclusion
- Discover the Optimal Machining Process with Unionfab
This article explores how CNC robots and robot arms are transforming manufacturing by enhancing efficiency and driving innovation.
Introduction
In today’s manufacturing landscape, CNC robots and robotic arms merge CNC precision with robotic flexibility, revolutionizing production efficiency and quality. These advanced systems automate complex tasks once dependent on manual labor, offering industries like automotive and electronics unprecedented speed and accuracy.
This article delves into their integration, benefits, and transformative impact across diverse industrial sectors.
Understanding CNC Robots and CNC Robot Arms
What are CNC Robots?
CNC robots are robotic systems equipped with CNC capabilities, enabling them to perform machining, assembly, or handling tasks autonomously. They typically consist of robotic arms fitted with CNC tools and are guided by computerized controls for precise operation.
Differences between Traditional CNC Machines and CNC Robots
Aspect | CNC Machines | CNC Robots |
---|---|---|
Flexibility | Limited | High |
Movement Range | Limited axes | More axes, multi-directional |
Programming Complexity | Simple | Complex |
Applications | Repetitive tasks | Versatile tasks |
Setup Time | Longer | Shorter |
Cost | Higher | Lower |
Accuracy | High | High |
Traditional CNC machines are stationary and perform tasks within a defined workspace, whereas CNC robots are mobile and versatile, capable of operating in various orientations and performing multifunctional tasks beyond machining.
Types of CNC Robot Arms
Articulated Robots
Articulated robots are versatile robotic arms with multiple joints (typically 6-axis), allowing them to maneuver in complex ways. They are well-suited for tasks requiring dexterity and agility, such as welding, painting, and intricate assembly processes.
Cartesian Robots
Cartesian robots, also known as gantry robots, operate along three linear axes (X, Y, Z). They are ideal for applications that require precise, linear movements within a fixed workspace, such as pick-and-place operations in assembly lines.
SCARA Robots
SCARA (Selective Compliance Assembly Robot Arm) robots feature two parallel rotary joints to provide horizontal reach and vertical lift. They excel in tasks that demand speed and accuracy in a confined workspace, like electronic assembly and packaging.
Delta Robots
Delta robots utilize a parallel linkage mechanism with three arms connected to a common base, enabling fast and precise movements. They are commonly used in high-speed picking, sorting, and packaging applications in food processing and pharmaceutical industries.
Benefits of CNC Robots and Robotic Arms
Increased Efficiency and Productivity
- Reduction in Production Time: Robots automate tasks with precision, significantly cutting cycle times and boosting overall output.
- Minimization of Human Error: By following programmed instructions consistently, these systems ensure uniform product quality, reducing scrap and rework.
Cost-Effectiveness
- Long-Term Savings: Despite initial costs, CNC robots offer substantial long-term savings through increased productivity and reduced downtime.
- Reduction in Labor Costs: Automating repetitive tasks decreases reliance on human labor, lowering wage expenditures and allowing skilled workers to focus on higher-value activities.
Enhanced Safety and Ergonomics
- Reduction in Workplace Injuries: Robots operate in controlled environments, minimizing risks to human workers from hazardous tasks.
- Improved Working Conditions: By handling physically demanding tasks, CNC technology promotes better workplace ergonomics, enhancing employee well-being and productivity.
These advantages highlight how CNC robots and robot arms optimize manufacturing processes, making operations more efficient, cost-effective, and safer for both workers and businesses.
Challenges and Considerations
Initial Investment and Maintenance
- High Upfront Costs: Implementing CNC robots and robot arms involves significant initial investments in equipment, software, and infrastructure. Manufacturers must carefully assess budgetary constraints and ROI projections to justify these expenses.
- Ongoing Maintenance Requirements: Despite advancements in technology, robotic systems require regular maintenance to ensure optimal performance and longevity. This includes preventive maintenance, calibration, and occasional repairs, all of which add to operational costs over time.
Integration with Existing Systems
- Compatibility Issues: Integrating new CNC robots with existing manufacturing systems can pose compatibility challenges. Ensuring seamless communication and synchronization between different equipment and software platforms is crucial to avoid disruptions and maximize efficiency.
- Training and Skill Development for the Workforce: Adopting CNC robots necessitates upskilling or retraining the workforce to operate, program, and maintain these advanced systems effectively. Training programs are essential to equip employees with the necessary technical expertise and confidence in handling robotic technologies.
Security Concerns
- Cybersecurity Threats: As robots become interconnected through IoT (Internet of Things) and cloud-based systems, they are susceptible to cybersecurity vulnerabilities. Manufacturers must implement robust cybersecurity measures to protect against data breaches, unauthorized access, and potential sabotage.
- Ensuring Data Integrity: Maintaining data integrity is critical in CNC manufacturing, where precise instructions and operational data are essential for accurate production. Safeguarding data against corruption or manipulation ensures that CNC robots perform tasks correctly and consistently.
Businesses must plan, invest, and collaborate among manufacturers, technology providers, and cybersecurity experts to fully harness CNC robots and robot arms for competitive advantage in manufacturing.
Applications of CNC Manufacturing Robotics
CNC Robots in Various Industries
Automotive
In automotive manufacturing, CNC robots are widely used for welding, painting, and assembly tasks. They ensure precision and consistency in manufacturing processes, contributing to the production of high-quality vehicles with reduced cycle times.
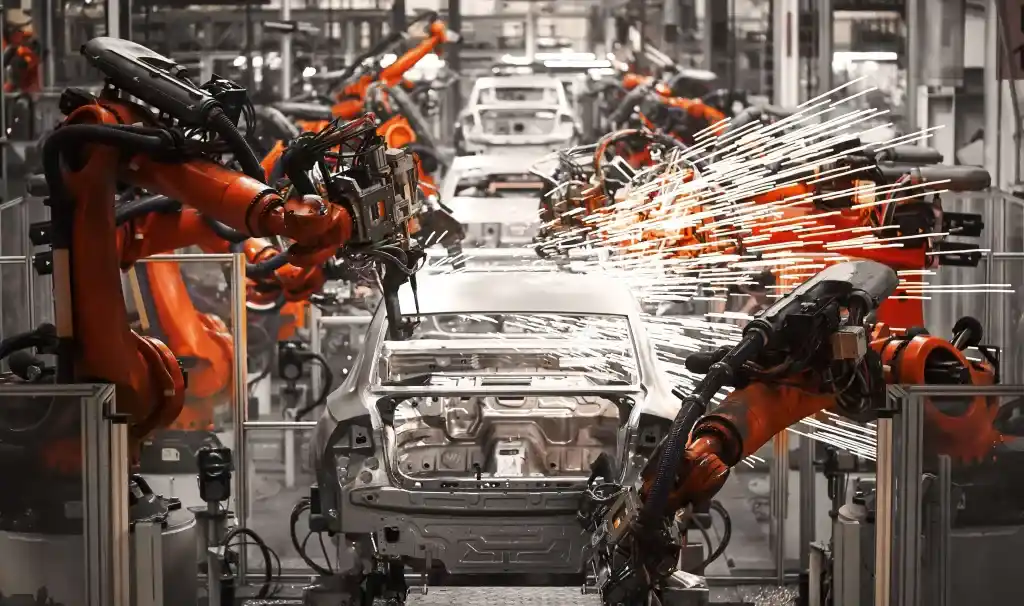
Source: 3ds.com
Aerospace
Robots play a crucial role in aerospace manufacturing for tasks such as machining complex components, drilling holes with exacting precision, and composite material layup. Their ability to handle intricate and critical processes helps meet stringent aerospace industry standards.
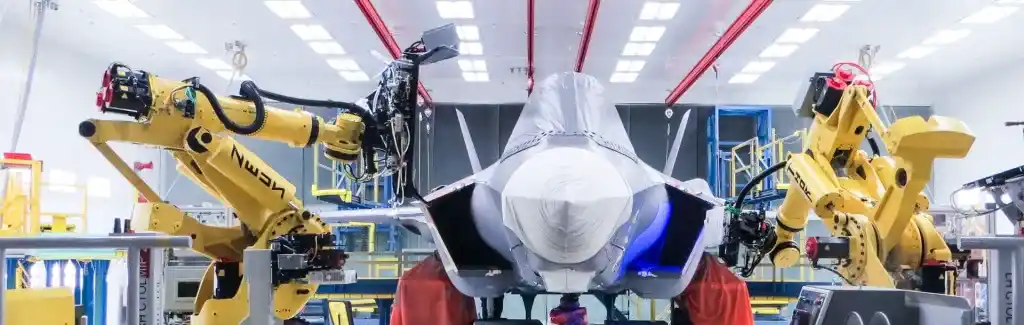
Source: fanucamerica.com
Electronics
In electronics manufacturing, CNC robots are employed for precise soldering, circuit board assembly, and handling delicate components. They enhance production speed and accuracy, crucial for meeting the demand for consumer electronics with ever-shrinking components.
Medical device manufacturing
CNC robots are integral to the production of medical devices, where precision and cleanliness are paramount. They perform tasks such as milling surgical instruments, assembling implants, and packaging sterile products, ensuring compliance with rigorous regulatory standards.
Case Studies and Specific Applications
Company: Tesla
Industry: Automotive
Application: Tesla utilizes CNC robots extensively in its Gigafactories for automating the production of electric vehicles. These robots are involved in precision cutting, welding, assembly, and painting processes. In the Model 3 production line, CNC robots are particularly important in the “Body-in-White” phase, where they assemble the vehicle’s frame. Their role includes performing numerous spot welds to ensure consistent quality and precision, ultimately contributing to the strength, durability, safety, and performance of the car bodies.
Impact:
- Efficiency: The use of robots has significantly increased the efficiency of Tesla’s production lines. Robots can operate 24/7 without fatigue, speeding up the manufacturing process and allowing for higher production volumes.
- Cost Reduction: Automation with robots reduces labor costs and minimizes material waste. The precision of CNC robots ensures that materials are used optimally, reducing the need for rework and scrap.
- Quality Improvement: The accuracy and consistency of CNC robots lead to higher quality products. This is especially important in the automotive industry, where safety and reliability are paramount.
- Scalability: The use of robots allows Tesla to easily scale up production to meet increasing demand for their electric vehicles. As new models are introduced, robots can be reprogrammed to handle new tasks, providing flexibility in the production process.
In conclusion, Tesla utilizes CNC robots extensively in their Gigafactories for precision tasks like cutting, welding, assembly, and painting. These robots, especially in the Model 3 line, enhance durability and safety, showcasing Tesla’s commitment to automated, high-quality electric vehicle production and industry innovation.
Future Trends in CNC Manufacturing Robotics
Advancements in AI and Machine Learning
Future robots will increasingly incorporate artificial intelligence (AI) and machine learning algorithms. These technologies enable robots to learn from data, adapt to changing environments, and optimize their performance autonomously. AI-driven robots can anticipate production variations, adjust parameters in real-time, and improve overall productivity and efficiency.
Collaborative Robots (Cobots)
Collaborative robots, or cobots, work safely alongside humans in shared workspaces. Future trends indicate increased cobot use in CNC manufacturing. These robots feature advanced sensors and user-friendly interfaces for easy deployment and task reconfiguration. They enhance factory floor flexibility, fostering seamless collaboration between human operators and robotic systems.
Innovations in CNC Robot Design
Future robotics will see lighter, stronger materials enhancing energy efficiency and maneuverability in confined spaces for agile manufacturing. Advanced sensor technologies like vision and tactile sensors will ensure CNC robots handle materials precisely, reduce machining errors, and improve quality control across manufacturing processes.
Conclusion
In summary, CNC robots and robotic arms revolutionize manufacturing by combining CNC precision with robotic flexibility. They offer advantages like increased efficiency, lower costs, and improved safety, making them essential for industries seeking to enhance productivity and quality.
As these technologies evolve with AI integration and collaborative capabilities, their role in modern manufacturing is set to expand further, driving innovation and competitiveness in global markets.
Discover the Optimal Machining Process with Unionfab
Unionfab specializes in customized solutions for your CNC Machining needs. Whether it’s CNC Robot or other techniques, you can rely on us for precision and efficiency in manufacturing.
Moreover, we offer a wide range of essential services, including finishing, to meet diverse requirements. For further details, feel free to reach out to us via our Contact Us page.