- Introduction to Powder Metal 3D Printing
- Are All Metal 3D Printing Methods Powder-Based?
- The Technology Behind Powder Metal 3D Printing
- Powder Metal 3D Printing: Advantages and Benefits
- Applications Across Industries
- Metal Powders for 3D Printing
- Challenges and Limitations
- Conclusion and Outlook
- Realize Innovations with Unionfab Metal 3D Printing
This article provides an overview of the powder metal 3D printing process, the types of metals used, key benefits compared to traditional manufacturing, and current and potential applications across industries.
Introduction to Powder Metal 3D Printing
Definition and Brief History
Powder metal 3D printing is an additive manufacturing technique that uses powdered metal as the raw material.
Instead of machining metal blocks or using molds like traditional manufacturing, powder metal 3D printing builds up parts layer-by-layer using powders and binding agents.
The technology first emerged in the 1980s, but has seen significant advances in recent years that have greatly expanded its capabilities and applications.
Overview of the Process
In powder metal 3D printing, fine metallic powders are spread across the build platform and selectively fused together by a high-energy source, such as a laser or electron beam, to create a 3D object.
This iterative process continues, layer upon layer, until the complete object emerges, ready for post-processing and use.
The main processes used today are:
- binder jetting (BJT)
- selective laser melting (SLM)
- electron beam melting (EBM)
Powder metal 3D printing can utilize various metal powders including stainless steel, titanium, nickel alloys, aluminum, and cobalt-chrome. Each metal powder brings distinct properties to the table, be it titanium’s lightweight strength or stainless steel’s corrosion resistance.
Key Benefits
- Efficient production of dense, durable metal parts with excellent mechanical properties.
- Ability to create complex geometries impossible with conventional manufacturing methods.
- Reduced waste compared to subtractive techniques like machining.
Are All Metal 3D Printing Methods Powder-Based?
“Metal powder 3D printing” and “metal 3D printing” are terms often used interchangeably, but they can refer to slightly different aspects within the broader field of additive manufacturing. Here’s how they differ:
Metal 3D Printing
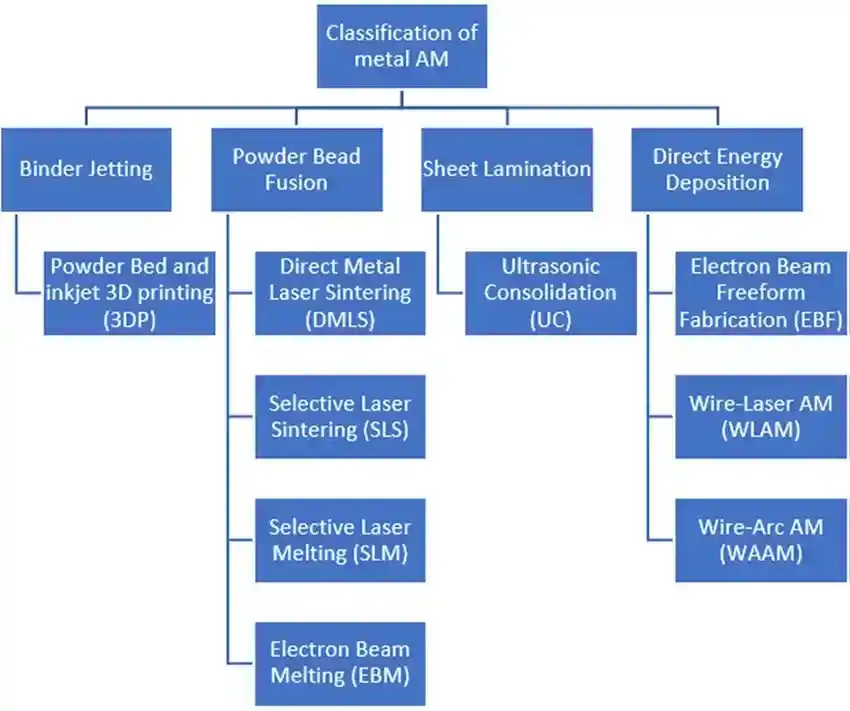
Source: https://www.researchgate.net/figure/Classification-of-metal-additive-manufacturing-technologies_fig1_332886203
“Metal 3D printing” is a general term that encompasses all types of 3D printing processes that involve metal materials. This includes both powder-based, wire-based and foil-based methods.
In a broader sense, “metal 3D printing” refers to any technique that uses metal as the primary material in additive manufacturing, regardless of the specific process or technology used. Read this article to gain more information about Metal 3D Printing.
Metal Powder 3D Printing
“Metal powder 3D printing” specifically refers to the subset of metal 3D printing techniques that utilize metal powders as the starting material.
This category includes methods like Direct Metal Laser Sintering (DMLS), Electron Beam Melting (EBM), Selective Laser Melting (SLM), and Binder Jetting, among others. In these processes, metal powders are selectively melted and fused together layer by layer to create complex and precise metal parts.
So, to summarize:
- Metal 3D Printing: The overarching term that covers all 3D printing processes involving metal as the primary material.
- Metal Powder 3D Printing: A subset of metal 3D printing that specifically focuses on techniques using metal powders to build up layers and create metal parts.
The Technology Behind Powder Metal 3D Printing
There are several techniques used in powder metal 3D printing, but they all rely on spreading thin layers of metal powder that are selectively fused together. The main methods include binder jetting, selective laser melting, and electron beam melting.
Preparing the Metal Powder
- Powder Selection: Different metals and alloys are selected based on the final part’s requirements, including mechanical properties, heat resistance, and material compatibility.
- Powder Size and Distribution: Metal powders are carefully sized to ensure uniform layer deposition. A narrow particle size distribution improves the flowability and packing density of the powder bed.
- Surface Treatment: Some metal powders undergo surface treatments to remove oxides and contaminants that might adversely affect the printing process.
- Flowability Enhancement: Metal powders may be treated to improve their flow characteristics, ensuring uniform spreading during layer deposition.
The Printing Process Step-by-Step
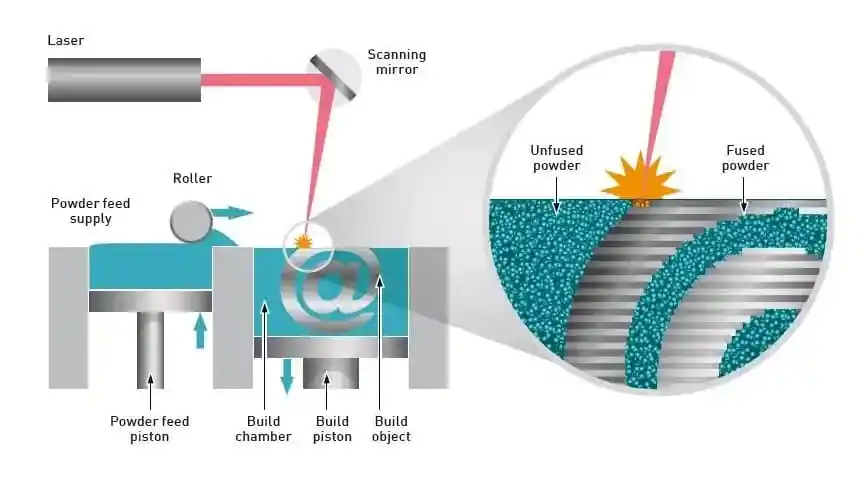
- Layer Preparation: The powder bed is spread evenly across the build platform. A controlled environment is maintained to prevent oxidation and ensure consistent printing conditions.
- Layer Fusion: In techniques like Selective Laser Melting (SLM) and Electron Beam Melting (EBM), a high-energy source (laser or electron beam) is directed onto the powder bed. This energy source selectively melts and fuses the metal particles together, according to the digital design’s specifications for that layer.
- Layer Solidification: After the energy source has passed, the molten metal rapidly solidifies, bonding with the surrounding material and forming a solid layer.
- Platform Lowering: The build platform descends, making space for the next layer of powder. The process repeats, layer upon layer, until the entire object is formed.
Post-Processing Requirements
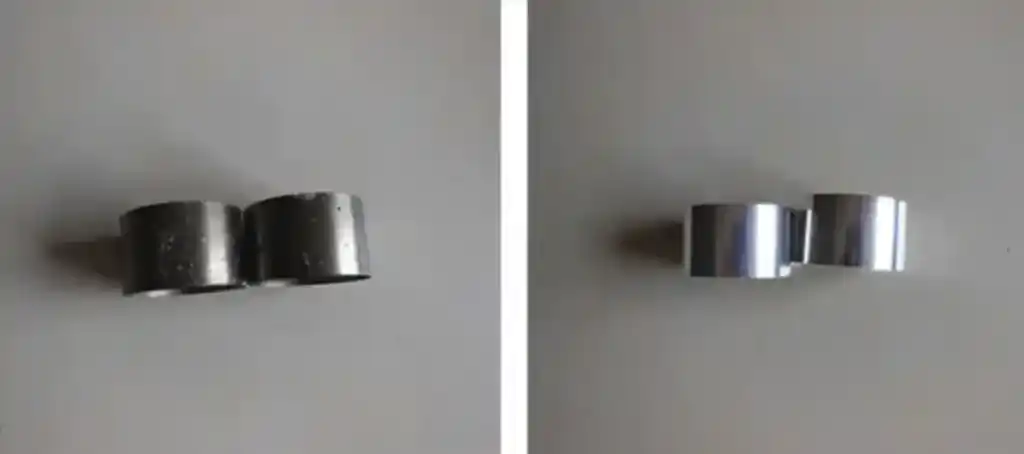
- Support Removal: For complex geometries, support structures are often printed alongside the part to prevent deformation during printing. These supports are removed after printing, typically through mechanical or chemical methods.
- Heat Treatment: Many printed parts undergo heat treatment (annealing) to relieve stresses, enhance mechanical properties, and eliminate defects.
- Machining and Finishing: Some parts might require additional machining to achieve precise dimensions and surface finishes. This can include milling, grinding, and polishing.
- Quality Inspection: Finished parts undergo rigorous quality checks, including dimensional accuracy, material integrity, and structural soundness.
For more information about the post-processing of metal parts, please refer to this article.
Powder Metal 3D Printing: Advantages and Benefits
Powder metal 3D printing offers several key advantages compared to traditional manufacturing processes:
- Complex geometries and intricate designs: The layer-by-layer printing process enables fabrication of complex structures with internal features, undercuts, lattices, and more that cannot be produced through machining or other methods. Parts can be highly optimized through generative design.
- Reduced material waste and energy consumption: Printing near net-shape parts consumes metal powder only where needed in the final part geometry, greatly reducing material waste compared to subtractive techniques that machine away excess material. Energy use is also lower.
- Customization and rapid prototyping: Parts can be easily customized and altered in CAD models. There is no need for new tooling, molds or dies, enabling rapid design iterations and prototypes. Short production runs become more economical.
- Enhanced material properties and performance: Parts exhibit excellent isotropic strength and microstructure. Parameter optimization allows tuning properties like hardness, wear/corrosion resistance, etc.
- Consolidation of multi-part assemblies: Multiple components can be printed as a single part, improving reliability by reducing joints and fasteners. This enables lighter, more integrated designs.
Applications Across Industries
Powder metal 3D printing is being adopted across a wide range of industries due to its capabilities and advantages over conventional manufacturing:
Automotive
Lightweight chassis, body, and engine components are printed for increased strength and fuel efficiency. Custom parts for low volume production are also viable.
Aerospace
Intricate and optimized aircraft and rocket engine parts are printed as single components, reducing assembly requirements. Lightweighting also improves fuel economy.
Medical
Custom implants and prosthetics are 3D printed to match patient anatomy and surgical requirements. Porous structures in implants promote bone in-growth.
Manufacturing
Printed metal tooling, jigs, fixtures, and molds enable rapid design iterations and workflow improvements for production.
Powder metal 3D printing is transforming manufacturing processes like injection molding by enabling innovative approaches for cooling management.
Energy
Turbine blades, heat exchangers and other oil/gas components leverage complex geometries and consolidated parts only possible through 3D printing.
Additive manufacturing drives innovation across these industries by enabling complex, high performance metal parts that could not be made using conventional subtractive and forming processes. As the technology advances, powder metal 3D printing will transform manufacturing.
Metal Powders for 3D Printing
A range of metals can be used in powder bed fusion 3D printing. The most common include:
Stainless Steels
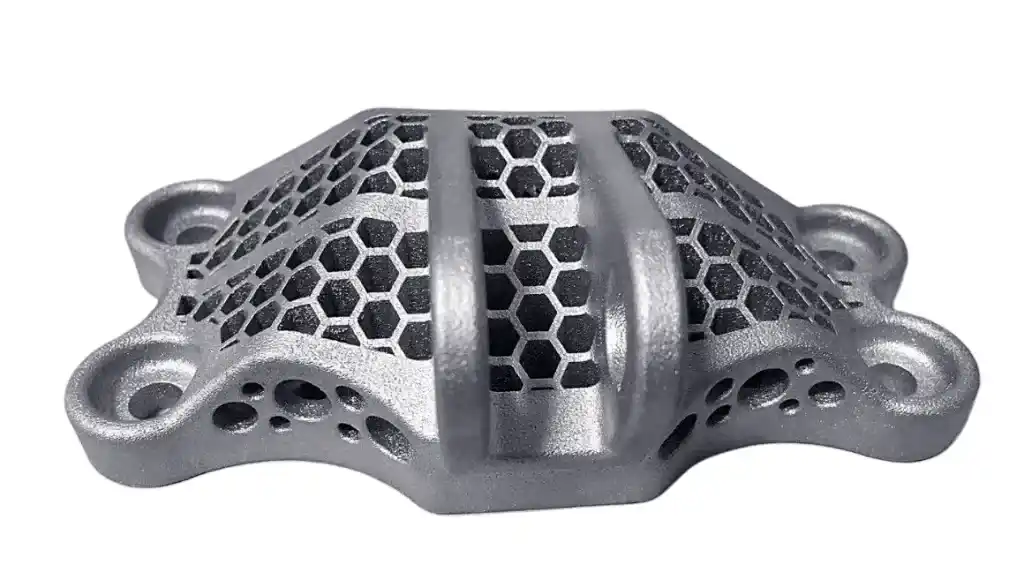
- Austenitic steels like 316L and 304L are popular options.
- Offer good corrosion resistance and weldability.
- Used for fixtures, tooling, medical, and chemical applications.
Aluminum Alloys

- AlSi10Mg is a common aluminum alloy powder.
- Provides high strength-to-weight ratio and thermal conductivity.
- Used for lightweight structural components.
Titanium Alloys
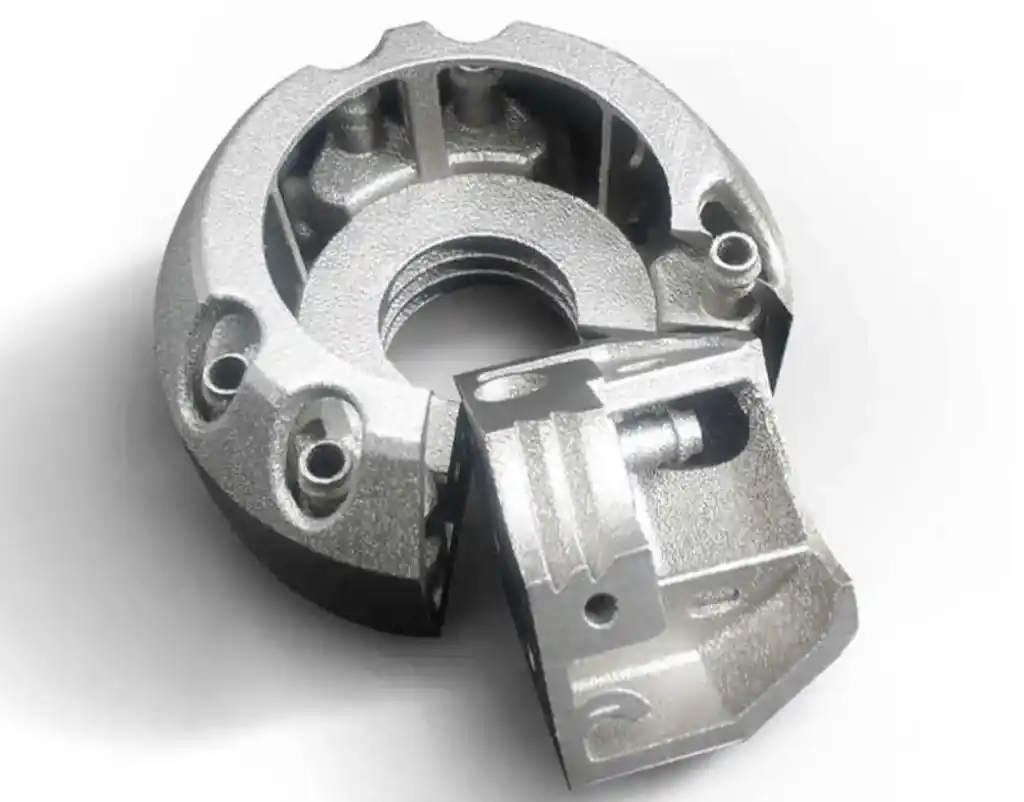
- Titanium 6Al-4V is the most common titanium alloy powder.
- Delivers excellent strength-to-weight ratio and biocompatibility.
- Used for aerospace components and medical implants.
Nickel Superalloys
- Alloys like Inconel 718 and 625 offer high strength and heat resistance.
- Enables lightweight aerospace engine parts to replace castings and forgings.
- Used for turbine blades, exhaust components, and combustion chambers.
Cobalt-Chrome Alloys
- Provides excellent corrosion resistance, wear resistance, and biocompatibility.
- Used for dental prosthetics and medical implants that require bone integration.
Challenges and Limitations
Residual Stresses
Powder metal 3D printing can introduce residual stresses within printed parts due to uneven cooling and solidification rates.
Porosity
Additionally, the layer-by-layer nature of the process can result in porosity within the material, affecting mechanical properties.
Surface Finish
Achieving a smooth surface finish on metal 3D-printed parts can be challenging, necessitating post-processing steps such as machining or polishing.
Cost Considerations
Powder metal 3D printing, especially with high-performance metals, can be cost-prohibitive. The expense of quality metal powders, post-processing equipment, and skilled labor can contribute to higher production costs compared to traditional manufacturing methods.
High-Performance Alloys
High-performance alloys, prized for their exceptional properties like heat resistance and mechanical strength, often come with challenges during powder metal 3D printing. The complex compositions and thermal behaviors of these alloys can result in porosity, cracking, or inconsistent mechanical properties.
Powder Quality
The success of powder metal 3D printing heavily relies on the quality and consistency of the metal powders used. Irregular particle size distribution, contamination, and varying particle morphology can lead to defects and inconsistencies in printed parts.
Material selection
Only certain alloy compositions have been optimized into printable powder feedstocks so far. This restricts the material options available compared to wrought metallurgy. For example, high strength aerospace alloys like titanium 6al-4v are widely available as powder, but more exotic nickel superalloys are not.
New alloy development
Qualifying and optimizing new alloys for 3D printing requires extensive metallurgical research and testing. Material suppliers tend to focus on proven aerospace grades rather than developing novel alloys. This slows expansion of material diversity.
Custom alloy compositions
Due to reliance on pre-alloyed powder, it is challenging to customize alloy chemistry and microstructures for specific applications. Elemental powder blends can be used but homogeneity and quality can suffer.
Powder production methods
Different powder production techniques, like gas atomization vs plasma atomization, result in powders with varying characteristics that influence printability and part performance.
Conclusion and Outlook
According to the report by financial news website Benzinga, the global 3D printing metal powder market is projected to reach a multimillion-dollar valuation by 2030, showcasing an unexpected compound annual growth rate (CAGR) during the forecast period of 2023-2030, in contrast to data from 2018 to 2022.
As the technology continues advancing, powder metal 3D printing will reshape manufacturing, aerospace, automotive, medical, and more. New printable alloys and larger build volumes will expand the applications further. Companies that leverage additive manufacturing will gain key competitive advantages.
While limitations remain, the future is bright for powder metal 3D printing.
Realize Innovations with Unionfab Metal 3D Printing
At Unionfab, we specialize in metal 3D printing to produce high-quality components. Our integrated one-stop platform enables customers to produce complex and high-performance metal parts optimized for their specific application needs.
With on-demand manufacturing and scalable production capacity, Unionfab offers rapid prototyping and production runs with exceptional lead times.
Contact us today to discuss how our metal 3D printing services can help realize your next project.