This article offers a comprehensive overview of milling, from its definition to the intricacies of milling machines.
Introduction
Milling is a key machining process that uses a rotating cutter to remove material from a workpiece, creating various shapes and features. It’s essential in manufacturing because it’s versatile, works with many materials, and achieves precise results.
Milling machines hold the workpiece and use a cutting tool and feed mechanism to control material removal. They can be manual or CNC-controlled.
What is Milling
Definition of Milling
In manufacturing milling is a subtractive machining process. It utilizes a rotary cutting tool with multiple sharp edges to progressively remove material from a solid workpiece.
This process allows you to achieve specific shapes, features, and dimensions on the final component.
Types of Materials Suitable for Milling Processes
Milling’s versatility extends to a wide range of materials, making it a valuable tool for various manufacturing applications.
- Metals: Milling is extensively used with various metals like steel, aluminum, brass, and titanium.
- Plastics: Many plastics can be milled, including acrylic, nylon, and polyethylene. However, some softer plastics require specific cutting tools to prevent melting.
- Wood: Wood is a natural material traditionally shaped with milling techniques. Modern milling machines can achieve intricate designs and precise cuts in wood for furniture making and other applications.
Factors Influencing Milling Operations
Several factors influence how a milling operation is conducted. Here are some key considerations:
- Material Properties: Harder materials require slower cutting speeds and sturdier cutting tools compared to softer materials.
- Desired Shape and Features: The complexity of the final shape you want to achieve will influence the choice of milling technique and the number of machining passes required.
- Cutting Tool Selection: Different milling operations utilize various cutting tool designs with specific numbers and geometries of cutting edges.
- Cutting Speed and Feed Rate: These parameters determine how quickly the material is removed.
What is Milling Machine
Definition of Milling Machine
A milling machine is a power-driven machine that utilizes rotary cutting tools to progressively remove material from a workpiece. It holds and positions the workpiece while the cutting tool performs the shaping.
What is a Milling Machine Used for
Milling machines are incredibly versatile and can be used for a wide range of applications.
- Creating flat surfaces: Milling can create smooth, precise flat surfaces on workpieces.
- Machining pockets and slots: Various shapes and sizes of pockets, grooves, and channels can be milled into workpieces.
- Forming gears and sprockets: Milling machines can create the intricate teeth profiles required for gears and sprockets.
- Cutting threads: Threading attachments can be used on milling machines to create external and internal threads on fasteners and other parts.
- Contouring and profiling: Complex curved shapes and edges can be achieved through multi-axis milling operations.
Types of Milling Machines
- Vertical Milling Machine (VMC): The most widely used type. The cutting tool rotates on a vertical spindle, allowing for operations from above.
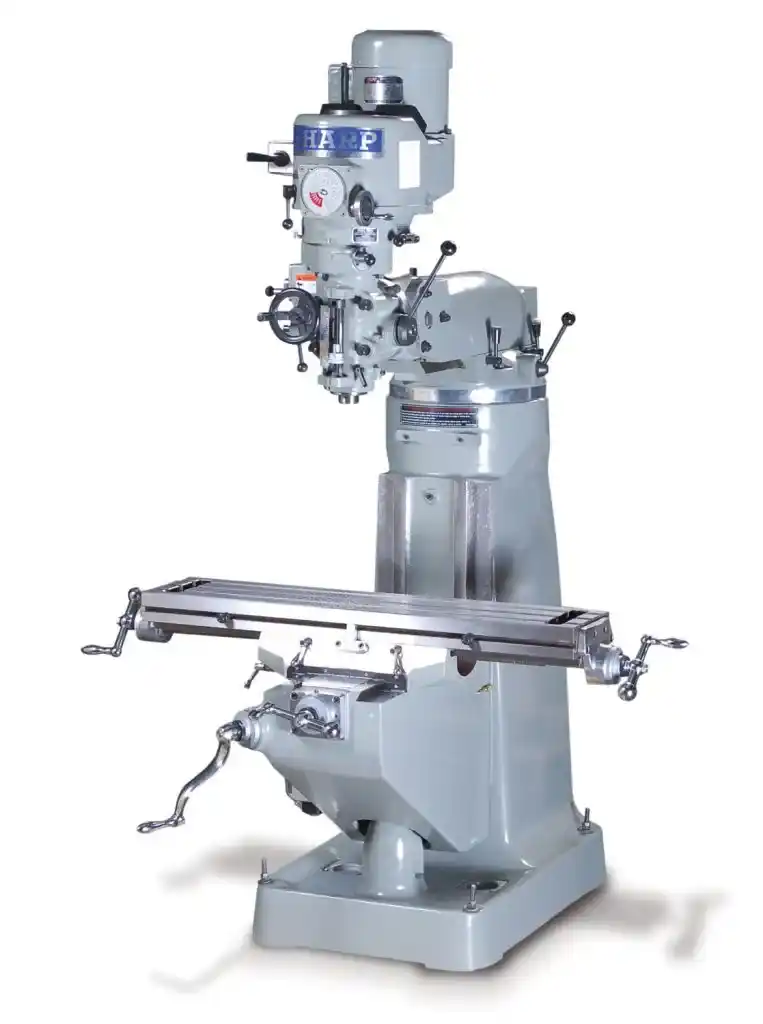
Source: normanmachinetool.com
- Horizontal Milling Machine (HMC): The cutting tool spins on a horizontal spindle. HMZs excel at machining large workpieces and those requiring long cuts along their length.
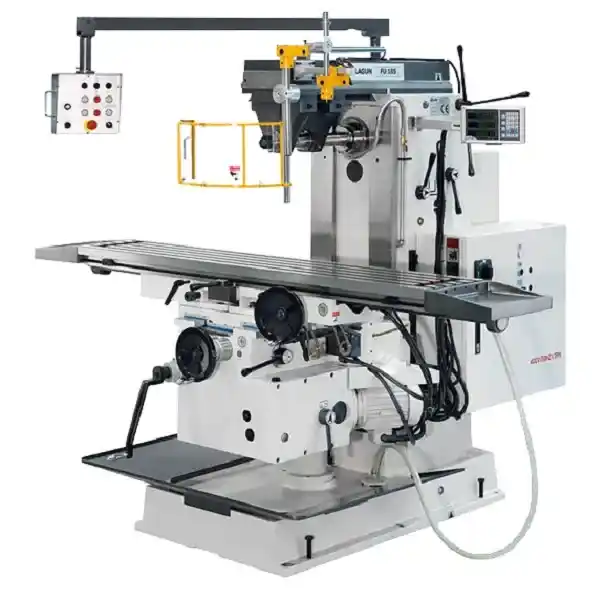
Source: normanmachinetool.com
- Bed Mills: These large, powerful machines are designed for heavy-duty milling operations on massive workpieces.
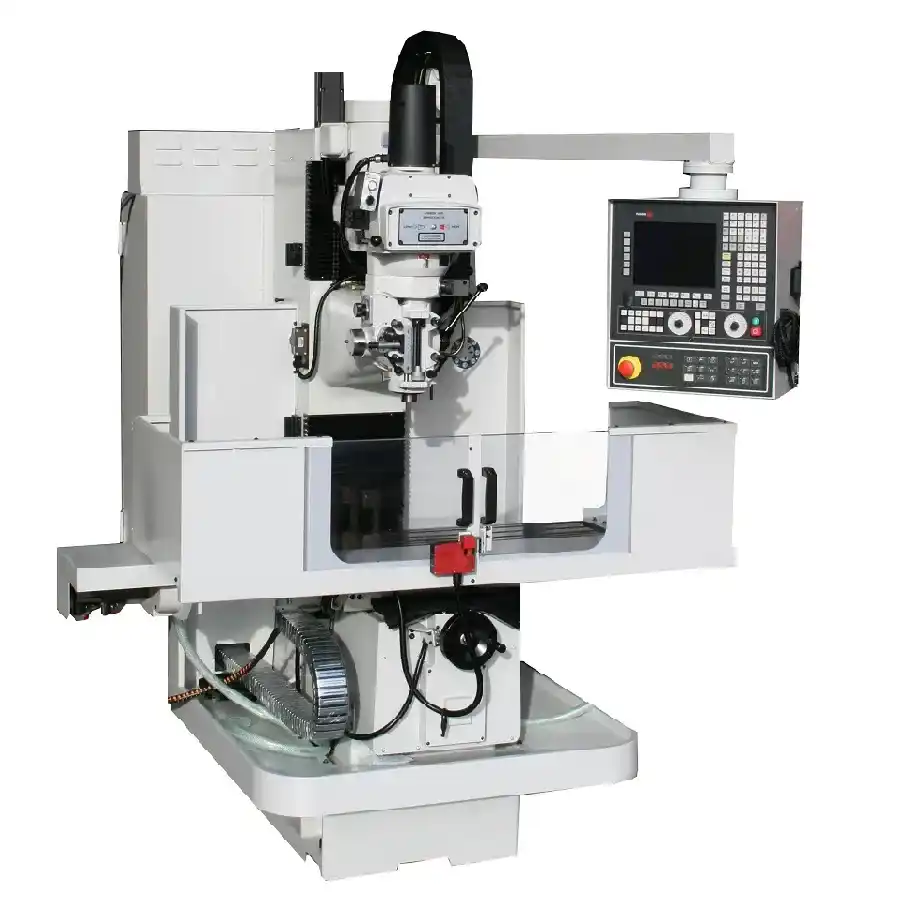
Source: semco.uk
- CNC Milling Machines: These machines are computer numerically controlled, allowing for precise and automated machining based on digital instructions.
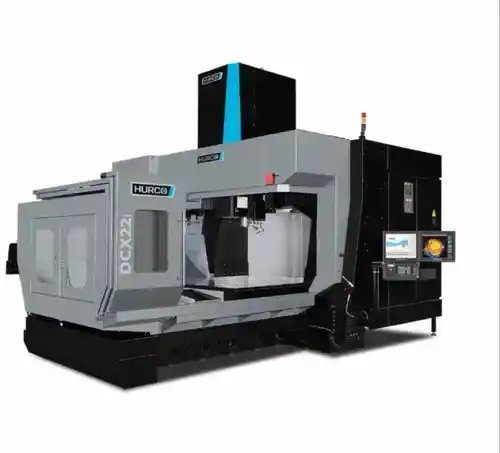
Source: 5.imimg.com
Type | Characteristics | Applications |
---|---|---|
VMC | 1. Vertical spindle for cutting from above 2. Versatile for various milling tasks 3. Offers good visibility of the cutting area | 1. General-purpose machining 2. Complex 3D shapes 3. Prototype creation 4. Machine shops, tool and die shops |
HMC | 1. Horizontal spindle for machining along the workpiece length 2. Ideal for large workpieces | 1. Heavy-duty applications on large components 2. Long cuts 3. Aerospace, automotive, construction equipment manufacturing |
Bed Mills | Large and powerful machines designed for heavy-duty milling | 1. Shaping massive workpieces 2. Engine blocks, turbine parts 3. Power generation, oil and gas industries |
CNC Milling Machines | Computer numerically controlled for precise and automated machining | 1. High-volume production of complex parts 2. Consistent and repeatable machining across batches 3. Nearly every manufacturing sector |
Different Milling Processes
Milling includes various techniques for shaping workpieces using rotary cutting tools. Here, we’ll explore two fundamental processes: Face Milling and Peripheral Milling, highlighting their distinct characteristics and applications.
- Face Milling: In Face Milling,a disc-shaped cutting tool with teeth on its flat face rotates on a vertical axis, and the entire face of the tool engages the workpiece with each revolution.
- Peripheral Milling: Peripheral Milling utilizes a rotating cylindrical cutting tool with cutting edges along its circumference. Unlike Face Milling, only the periphery of the tool engages the workpiece during each revolution.
Comparison between Face Milling and Peripheral Milling
Feature | Face Milling | Peripheral Milling |
---|---|---|
Cutting Tool Engagement | Entire face of the tool | Periphery of the tool |
Primary Function | Creating flat surfaces | Machining pockets, slots, grooves, and profiles |
Material Removal Rate | High | Moderate |
Surface Finish | Excellent for flat surfaces | Varies depending on tool diameter and feed rate |
Application Focus | Establishing reference planes | Creating features and details |
Advantages of Milling
Beyond a standard machining process, milling can improve efficiency and deliver a lot of benefits that make it the ideal solution for diverse production needs.
- Product Versatility : Milling can create a wide variety of shapes and features on workpieces. From simple flat surfaces to intricate pockets, slots, and complex contours, milling can achieve them all.
- Precision and Accuracy: Modern milling machines, particularly those with CNC technology, deliver exceptional precision and accuracy.
- Material Compatibility: Milling can effectively work with varieties of materials, including metals,plastics and wood.
- Automation: The integration of CNC technology into milling machines has revolutionized the process. CNC allows for automated operation based on digital instructions.
- Cost-Effective for Batch Production: Milling’s efficiency and automation make it cost-effective for batch production.
Applications of Milling
Milling isn’t confined to machine shops.Its ability to create precise shapes on various materials makes it a crucial tool across numerous industries.
- Automotive: Engine parts, transmissions, body panels (via molds) and lightweight components are milled for performance and efficiency.
- Aerospace: Milling shapes lightweight fuselage panels, landing gear parts, and critical engine components for flight worthiness.
- Electronics: Milling creates heat sinks, housings, PCB molds, and connectors for various devices.
- Medical: Prosthetic limbs, surgical instruments, dental implants, and various medical devices benefit from milling’s precision.
Conclusion
Milling is a fundamental machining process that utilizes rotating cutting tools to progressively remove material from a solid workpiece.
This process allows manufacturers to create a vast array of shapes, features, and precise dimensions on a wide range of materials.From car parts to medical devices, milling plays a crucial role in manufacturing.
Unionfab: Custom Professional CNC Machining Services
Unionfab has varieties of CNC Machining services,such as CNC Turning and CNC Milling.
Bring your ideas to life quickly and accurately with Unionfab. Our advanced machinery and experienced professionals will offer a flexible solution for your prototyping and production needs.
