Learn how to use tapped holes effectively to enhance structural integrity and durability with our expert tips.
Introduction
Tapped holes, achieved through the creation of internal threads via a cutting tool (tap), represent a crucial modification to a material’s geometry for achieving robust mechanical joints.
Understanding Tapped Hole
What is Tapped Hole?
A tapped hole is a specifically designed cylindrical cavity within a workpiece that has internal threads machined onto its surface. These threads are created using a specialized cutting tool called a tap.
The primary function of a tapped hole is to provide a secure and standardized location for a threaded fastener, such as a screw or bolt, to engage and create a strong mechanical joint.
Features of Tapped Holes
Thread Specifications
- Thread Type: There are various thread types, each with its own profile and application. Common types include Unified Thread Standard (UTS) for general purpose, Metric threads for international standardization, and specialty threads like Acme threads for high-friction applications.
- Thread Size: This refers to the diameter and pitch of the thread. Diameter defines the overall width of the threaded section, while pitch determines the distance between each thread.
Depth and Diameter Considerations
Beyond the thread specifications, two crucial dimensions define a tapped hole: depth and diameter.
- Depth: The depth and diameter of a tapped hole are critical factors for its functionality and structural integrity. The depth should be sufficient to allow for the full engagement of the fastener’s threads
- Diameter: The diameter of a tapped hole is slightly smaller than the core diameter of the corresponding screw or bolt. This difference allows for the creation of the threads and ensures a secure fit without excessive play.
Techniques for Creating Tapped Hole
Beyond the basic steps of planning, drilling, and tapping, here are some additional techniques for creating high-quality tapped holes.
Tapping Blind Holes
Taper Taps
For blind holes (holes that don’t go all the way through), a taper tap is generally recommended, which allows for smoother thread initiation and better swarf (metal shaving) clearance.
Chip Management
Blind holes require extra attention to chip management. Regularly back out the tap slightly to clear accumulating chips. Consider using a tap with a spiral flute design, which helps evacuate chips during tapping.
Tapping Hard Materials
Tapping Speeds
Harder materials require slower tapping speeds to prevent tap breakage and thread stripping.
Pilot Hole Adjustments
For very hard materials, the pilot hole diameter might need to be slightly smaller than what a standard tapping chart suggests. This creates a tighter fit for the tap and reduces the amount of material the tap needs to remove, minimizing stress on the tool.
Advanced Techniques
Tapping Inserts
For high-volume production or when dealing with particularly challenging materials, consider using tapping inserts.
These are replaceable cutting tips that can be mounted on a dedicated shank. They offer superior wear resistance and chip control compared to traditional solid taps.
Thread Milling
This technique utilizes a CNC machine with a specifically designed rotary cutting tool to create the threads. It offers greater precision and control over thread geometry, especially for larger or non-standard thread sizes.
Tapped Holes vs. Threaded Holes
Tapped Holes vs. Threaded Holes: Definition
Tapped Hole
A tapped hole is a specifically designed cylindrical cavity within a workpiece that has internal threads machined onto its surface. These threads are created using a specialized cutting tool called a tap.
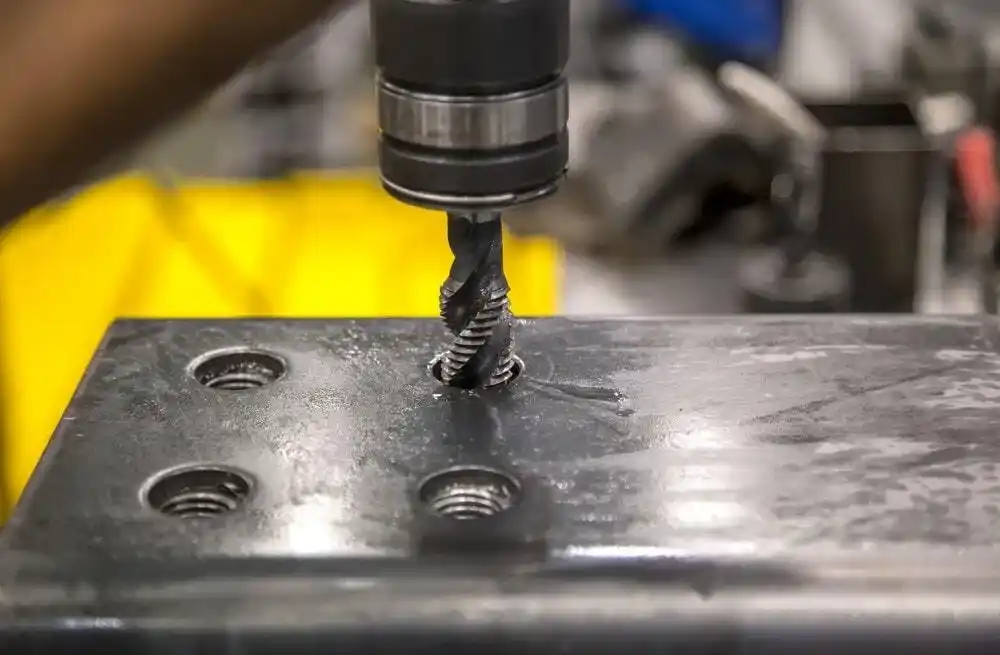
Source: xometry.com
Threaded Hole
A general term for any hole with helical threads on its inner surface, regardless of how it was created. It can be formed through various methods, including tapping, thread milling, or even come pre-threaded (e.g., in pipes).
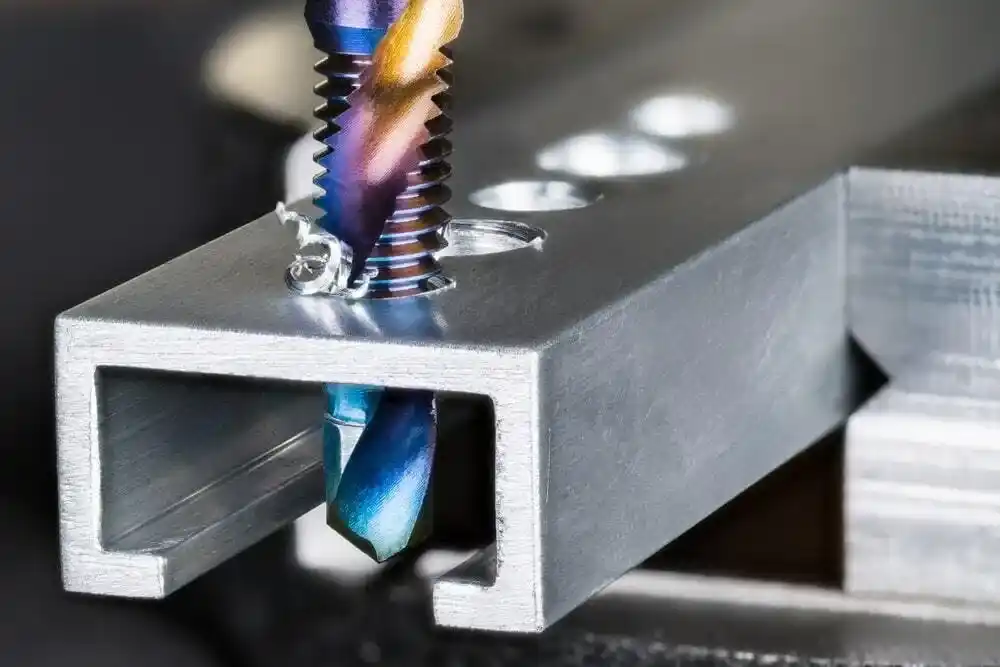
Source: xometry.com
Tapped Holes vs. Threaded Holes: Characteristics
The terms “tapped hole” and “threaded hole” are often used interchangeably, leading to some confusion. While they both involve threads, there’s a key distinction in how they are created and their intended purpose.
Feature | Tapped Hole | Threaded Hole |
---|---|---|
Thread Location | Internal | Internal or External |
Purpose | Creates a joint for screws/bolts | Various purposes (joints, fittings, fluid paths) |
Creation Method | Formed by tapping a pre-drilled hole | Created during manufacturing or by threading tools |
Typical Size Range | Smaller (limited by tap size) | Wider range of sizes |
Tapped Holes vs. Threaded Holes: Key Differences
Formation Process
- Tapped Holes: Involve a subtractive process. A pilot hole is drilled first, then a tap (cutting tool) is used to remove material and create internal threads within the hole.
- Threaded Holes (External): Utilize a forming process. A threading die (forming tool) reshapes the material around the shank of a screw or bolt to create external threads.
- Threaded Holes (Formed): Involve a cold forming process like rolling or coining. These techniques use pressure to deform the material and create internal threads without removing any material.
Strength and Durability
- Tapped Holes: Generally considered less strong than the original material due to the removal of material during tapping. Strength can be further impacted by factors like material properties and tap size.
- Threaded Holes (External): Can be as strong, or even stronger, than the original material because the forming process can strain harden the metal around the threads.
- Threaded Holes (Formed): Strength depends on the material and the forming process used. Generally not as strong as externally threaded holes due to the limitations of cold forming techniques.
Installation Methods
- Tapped Holes: Require a separate threaded fastener (screw, bolt) to be screwed into the hole to create a joint. This two-part assembly process offers some flexibility in terms of choosing fastener size and type.
- Threaded Holes (External): The threaded feature is already part of the fastener itself. These fasteners are simply screwed into a pre-drilled hole (not tapped) to create a joint. Installation is faster but offers less customization compared to tapped holes.
- Threaded Holes (Formed): The internal threads are part of the workpiece itself. A non-threaded fastener or a component with a complementary external shape can be inserted to create a joint or seal. This method is often used in high-volume applications where speed and efficiency are priorities.
Tapped Holes vs. Threaded Holes: Pros and Cons
Feature | Tapped Holes | Threaded Holes (External) | Threaded Holes (Formed) |
---|---|---|---|
Pros | Versatile (works with many materials) Customizable fastener selection Reusable Strong joints | Fast installation Strong threads Simple process | Fast production Sealing capability |
Cons | Time-consuming process Weaker material due to removal Requires tapping skill Limited hole size | Less versatile (fixed thread type) Precise pre-drilled hole size required | Material limitations (soft/ductile materials) Weaker threads compared to external Less customization for fasteners |
Maintenance and Repair of Tapped Holes
Common Issues with Tapped Holes
Tapped holes, while durable, can encounter various issues over time that compromise their functionality.
- Thread Wear: Normal use and repeated assembly/disassembly cycles can cause the threads in a tapped hole to wear down. This can lead to a loose or sloppy fit for the fastener.
- Stripped Threads: Applying excessive torque or using the wrong size fastener can strip the threads in the tapped hole. This makes the hole unusable for the original fastener size.
- Corrosion: Exposure to moisture or improper storage can lead to corrosion on the threads. This can make it difficult to screw in the fastener and potentially weaken the joint.
- Seized Threads: Corrosion, debris buildup, or over-tightening can cause the threads in the hole and the fastener to seize together. This can make it challenging or even impossible to remove the fastener without damaging the tapped hole.
- Broken Taps: Improper tapping technique, using a dull tap, or incorrect tap size for the material can lead to a broken tap shank lodged within the hole. This can be a difficult and time-consuming issue to address.
Repair Techniques of Tapped Holes
When a tapped hole suffers damage, several repair techniques can restore its functionality.
- Thread Repair Kits: All-in-one kits for various repairs. Includes drill bits, taps, inserts & installation tools. Good value for multiple repairs.
- Helicoil Inserts: Helicoil is a brand name for a specific type of threaded insert made from a high-strength, pre-coiled wire. These inserts are designed to create a new internal thread within a damaged tapped hole.
- Oversized Tapping: Drill out the hole and use a larger tap for a bigger fastener. Simpler and faster, but weakens the joint and requires a new, larger screw.
Preventive Measures of Tapped Holes
Taking proactive steps can significantly extend the life and functionality of tapped holes.
- Thread Lubricants: Use cutting oil or tapping compound to reduce friction, create cleaner threads, and prevent tap wear.
- Protective Coatings: Apply zinc plating, nickel plating, or dry lubricants to fight corrosion, reduce friction, and improve appearance (optional).
- Scheduled Inspections: Regularly check tapped holes for wear, corrosion, or damage to catch problems early and prevent thread failure.
Applications of Tapped Holes
Tapped holes are a fundamental building block in various industries, playing a crucial role in creating strong and reliable connections.
Manufacturing Sector
Machinery Assembly
Tapped holes enable secure attachment of motors, gears, bearings, and other parts using bolts, screws, and threaded inserts. This ensures proper alignment, functionality, and the ability to disassemble for maintenance.
Automotive Manufacturing
From engines and transmissions to body panels and electrical systems, tapped holes are essential for assembling various automotive components.
They provide secure attachment points for critical parts like engine blocks, suspension components, and interior fittings.
Construction Industry
Structural Integrity Enhancement
Tapped holes can be used to reinforce existing structures or connect different structural elements. For example, they might be used to fasten steel plates to concrete walls for added strength.
Installation of Fixtures and Fittings
From electrical outlets and plumbing fixtures to cabinets and shelves, tapped holes ensure these elements are firmly anchored to walls, floors, or ceilings.
Aerospace and Defense
Importance in Aircraft Assembly
Tapped holes are used to join fuselage sections, attach wings, secure engine mounts, and fasten various control surfaces. The high strength and reliability of tapped holes are crucial for ensuring the safety and performance of aircraft.
Military Equipment Fabrication
Tapped holes play a vital role in assembling and securing components in military equipment like tanks, armored vehicles, and weaponry.
Their ability to withstand demanding conditions and vibrations makes them essential for creating reliable and functional military hardware.
Conclusion
Tapped holes, while seemingly simple, offer a powerful and versatile solution for creating strong and reliable connections.
From their role in assembling critical machinery and aircraft components to their use in everyday applications like furniture and electronics, tapped holes are fundamental building blocks across various industries.
Unionfab: Provide Professional Machining Services
Unionfab offers a comprehensive suite of CNC machining services, including CNC turning and milling.
Turn your concepts into reality with speed and precision at Unionfab. Our cutting-edge technology and skilled machinists provide adaptable solutions for both prototyping and full-scale production.
