This article delves into what PET material is, its various applications in everyday products and its environmental benefits.
Introduction
Polyethylene terephthalate, commonly known as PET, is a widely used and versatile plastic material known for its strength, clarity, and lightweight properties.
PET is a polyester formed by combining ethylene glycol and terephthalic acid, and its applications range from the ubiquitous beverage bottle to clothing fibers and food containers.
What is PET Material?
Definition and Chemical Composition of PET
PET is a type of polyester, a polymer (a long chain of molecules) formed by linking repeating units. In PET’s case, these units come from two chemicals: ethylene glycol and terephthalic acid.
Physical and Chemical Properties of PET
- Strength and Lightweight: PET boasts impressive strength for its weight. This makes it ideal for applications where both durability and portability are important.
- Transparency: PET is naturally clear, allowing for easy product visibility in containers.
- Chemical Resistance: PET is a champion against many chemicals, including weak acids, bases, and alcohols. This makes it safe for food and beverage containers.
- Recyclability: PET is one of the most recycled plastics globally, thanks to its well-defined structure. This allows it to be broken down and reformed into new products.
Manufacturing Process of PET
- Purification: The starting materials, ethylene glycol and terephthalic acid, are meticulously purified to ensure a high-quality final product.
- Polymerization: These purified ingredients are heated and combined in a process called polymerization. This chemical reaction links the monomers into long chains, forming PET.
- Modification (Optional): Depending on the desired end product, additional ingredients or processes might be employed. For example, colorants can be added to create colored PET bottles.
- Shaping: Molten PET is then shaped into its final form through various techniques like injection molding (think bottles) or extrusion (think fibers for clothing).
- Solidification: The shaped PET is cooled and solidified to obtain the final product.
Common Applications of PET
Packaging
This is PET’s most recognizable domain.
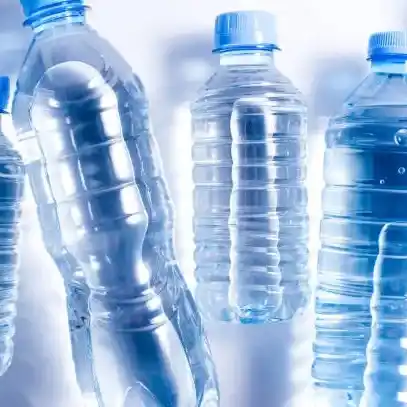
Source: omnexus.specialchem.com
- Bottles: From water and soda bottles to ketchup and salad dressing containers, PET’s clarity and lightweight nature make it ideal.
- Food Containers: Trays for pre-made salads, clamshell containers for fruits and vegetables, and even blister packs for medications often utilize PET for its durability and transparency.
- Films: PET films find use in food packaging to enhance shelf life, create blister packs for pharmaceuticals, and even as photographic film base.
Industrial Applications
PET’s strength and heat resistance make it suitable for industrial uses.
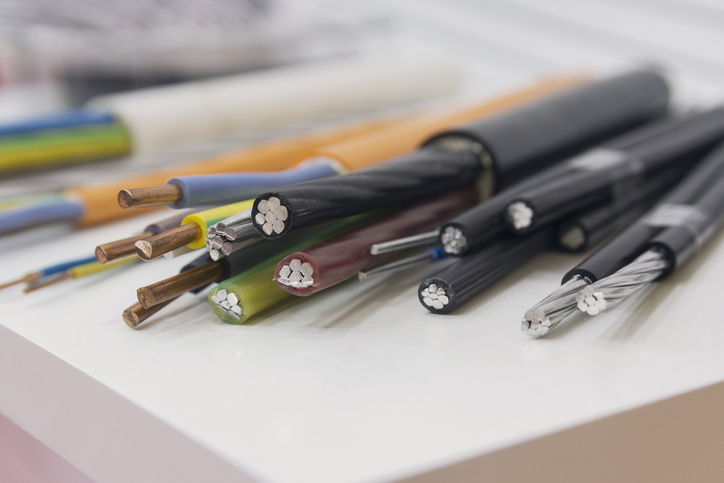
Source: electrolock.com
- Automotive Parts: Car manufacturers utilize PET for interior components like car seat covers, carpets, and sound insulation due to its lightweight and durable nature.
- Electronics: PET films can be found in electrical applications like capacitor films and printed circuit boards due to their insulating properties.
Medical Uses
PET’s sterility and clarity make it valuable in the medical field.
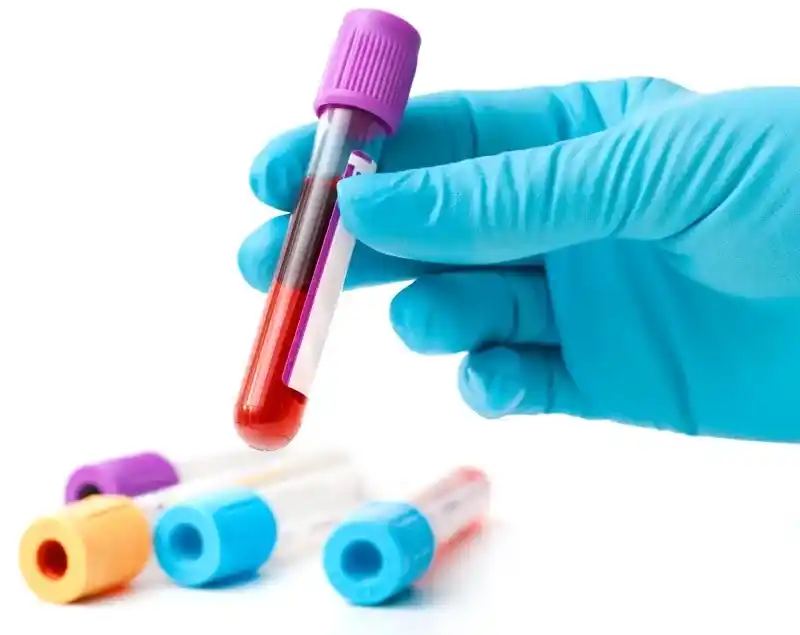
Source: xiangyiintl.com
- Sterilizable Instruments: Certain surgical instruments can be made from PET as they can withstand high-temperature sterilization processes.
- Medical Packaging: PET finds use in packaging for sterile medical supplies and pharmaceuticals due to its barrier properties that help prevent contamination.
PET 3D Printing
What is PET filament?
PET filament is a thin strand of recycled or virgin PET plastic used specifically for FDM 3D printing. The thin threads of PET plastic, typically wound onto spools, that are fed into a 3D printer. The printer’s extruder heats and melts the filament, meticulously depositing it layer-by-layer to create your desired 3D object.
Properties of PET Filament
Strength and Durability
PET filament inherits these qualities from PET plastic. It offers good dimensional stability and can withstand moderate wear and tear, making it suitable for functional prototypes and some end-use parts.
Clarity
Similar to PET plastic, PET filament can be clear or translucent, allowing some visibility within the printed object. Dyes can also be added to create a variety of colors.
Chemical Resistance
PET filament inherits PET plastic’s resistance to many chemicals, including weak acids, bases, and alcohols. This makes it suitable for applications requiring some chemical exposure.
Thermal Resistance
While not the most heat-resistant filament option, PET filament can withstand moderate temperatures, making it suitable for some functional applications.
Advantages and Disadvantages of PET filament
Advantages
- Cost-Effective: Compared to some other 3D printing filaments, PET is a relatively inexpensive option.
- Recycled Content: Choosing recycled PET filament offers a sustainable choice, reducing reliance on virgin plastic.
- Good Balance of Properties: PET filament offers a balance of strength, clarity, and chemical resistance, making it suitable for various applications.
- Ease of Printing: PET filament is generally considered user-friendly for beginners due to its forgiving printing characteristics.
Disadvantages
- Warping: PET filament can be prone to warping during printing if not handled carefully.
- Moisture Sensitivity: PET filament can absorb moisture from the air, affecting its printing quality.
- Limited Heat Resistance: For applications requiring high heat tolerance, PET filament might not be the best choice.
PET 3D Printing: Method and Process
FDM 3D Printing Using PET Filament
FDM, or Fused Deposition Modeling, is the most common 3D printing method that utilizes PET filament.
FDM 3D printing with PET filament brings digital designs to life layer-by-layer. After slicing 3D model into horizontal sections, the printer heats and extrudes the PET filament, building the object one layer at a time.
The key is to find the right temperature settings and manage warping to create successful prints from this affordable and versatile material.
PET 3D printing process
- Slicing the Model: 3D design software prepares the 3D model for printing by slicing it into thin horizontal layers.
- Filament Loading: The PET filament spool is loaded into the printer, and the filament is fed through a guide tube into the extruder.
- Extrusion and Deposition: The extruder heats the filament, melting it into a molten state. A nozzle precisely deposits the melted filament layer-by-layer onto the printing bed, following the sliced model instructions.
- Building the Object: The printing head moves horizontally along each layer, depositing filament and gradually building the 3D object. As each layer cools and solidifies, the next layer is deposited on top, creating the final form.
- Removal and Post-Processing: Once printing is complete, the finished object is removed from the printing bed and may require support structure removal and further finishing touches depending on the design.
Printing considerations for PET filament
- Printing Temperature: The ideal printing temperature for PET filament typically ranges between 220°C and 240°C (428°F – 464°F). Fine-tuning the temperature based on your specific filament brand and printer is recommended.
- Heated Bed: Using a heated bed (around 60°C – 80°C or 140°F – 176°F) helps prevent warping and ensures good layer adhesion.
- Printing Speed: A moderate printing speed is generally recommended for PET filament to allow for proper cooling and layer adhesion.
- Cooling Fan: Using a cooling fan helps the extruded filament solidify quickly, reducing the risk of warping and improving dimensional accuracy.
Benefits of PET Material
Durability and Strength
PET is surprisingly tough. It offers good impact resistance and can withstand moderate stress without breaking. This makes it ideal for packaging applications where protecting the contents is crucial.
Lightweight and Cost-effective
Compared to other materials like glass, PET is a featherweight. This reduces transportation costs and the overall weight of the final product. Additionally, PET is relatively inexpensive to produce, making it a cost-effective choice for manufacturers.
Barrier Properties
PET acts as a shield against unwanted elements. It has excellent resistance to moisture, gases, and even some chemicals. This property makes PET perfect for food and beverage packaging, as it helps preserve the product’s freshness and integrity.
Clarity and Aesthetic Appeal
PET is naturally transparent, allowing for clear visibility of the product within. This is crucial for marketing and consumer trust in the food and beverage industry. Additionally, PET can be dyed or molded into various shapes, offering some aesthetic flexibility for product design.
Environmental Impact and Sustainability
Recyclability of PET Material
PET is one of the most recycled plastics globally, designated by the recycling symbol #1. This is because its chemical structure allows it to be broken down and reformed into new products.
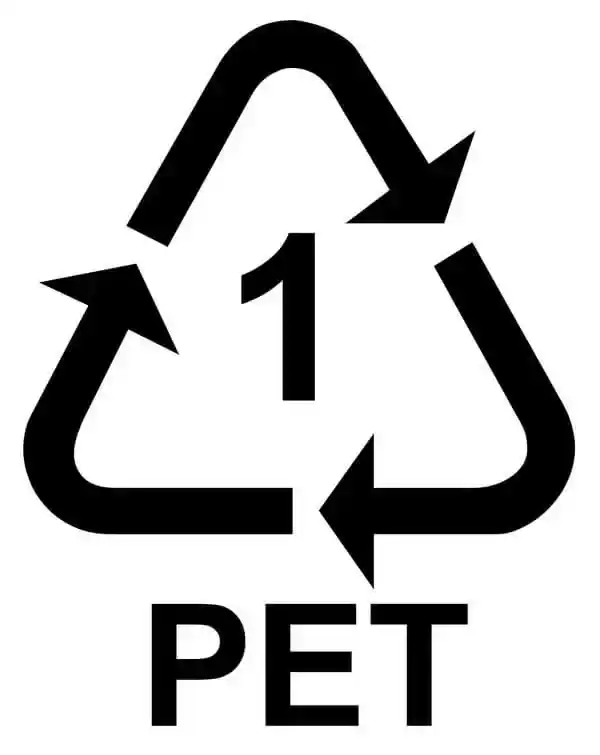
Source: ismwaste.co.uk
Lifecycle Analysis of PET Products
- Production: Manufacturing PET does have an environmental footprint. It requires fossil fuels and can generate emissions.
- Use: During its use phase, PET offers benefits like lightweight transportation and extended product shelf life.
- End-of-Life: Ideally, PET should be recycled. However, a significant portion ends up in landfills or leaks into the environment, contributing to plastic pollution.
PET Material Compared with Other plastics
Advantages
Compared to some plastics, PET offers a lighter weight, leading to lower transportation emissions. Its good barrier properties can extend the shelf life of food, reducing waste. Additionally, its well-defined structure makes it highly recyclable.
Disadvantages
PET’s reliance on fossil fuels for production is a concern. If not properly recycled, it contributes significantly to plastic pollution.
Innovations in Recycling Technologies
Mechanical Recycling
The traditional method involves sorting, cleaning, and grinding PET plastic into flakes. These flakes are then melted and reformed into new products.
Chemical Recycling
A newer approach breaks down PET plastic back into its chemical building blocks. These chemicals can then be used to create virgin-quality PET or other valuable materials.
Chemical recycling offers promise for dealing with lower-quality PET waste that might not be suitable for mechanical recycling.
Challenges and Future Prospects of PET Material
Addressing the Plastic Waste Crisis
- Improved Recycling Infrastructure: Investing in better collection and sorting systems is crucial to capture more PET waste and divert it from landfills and the environment.
- Consumer Education: Raising awareness about proper PET disposal habits and the importance of recycling is essential for behavioral change.
- Extended Producer Responsibility (EPR): This approach holds manufacturers responsible for the end-of-life management of their products, potentially incentivizing them to design for recyclability and invest in recycling infrastructure.
Developing Biodegradable Alternatives to PET
- Bio-based PET: Research is ongoing to develop PET derived from renewable resources like plant-based materials. This could offer a more sustainable alternative to traditional PET.
- Biodegradable PET: The holy grail! Scientists are exploring ways to create PET that can break down naturally under specific conditions, This would significantly reduce plastic pollution concerns.
Future Trends in PET Usage and Technology Advancements
- Chemical Recycling: This technology offers the potential to recycle lower-quality PET waste that might not be suitable for mechanical recycling, creating a more comprehensive recycling loop.
- Closed-Loop Systems: The concept of closed-loop recycling aims to keep PET within a continuous cycle, where used PET is recycled and reused to create new PET products, minimizing reliance on virgin materials.
- Lightweighting: Advancements in PET manufacturing are leading to thinner yet strong bottles, reducing material usage and transportation emissions.
- Bio-based PET: The development of PET partially derived from renewable resources can lessen dependence on fossil fuels.
Conclusion
PET’s versatility and functionality have made it a dominant plastic material. However, its environmental impact due to plastic waste and fossil fuel reliance demands solutions.
Moving forward, improved recycling infrastructure, advancements in chemical recycling and biodegradability, and a shift towards closed-loop systems are crucial for PET to remain a sustainable choice in the future.
Expertise in Materials at Unionfab
At Unionfab, we empower your creative process with both 3D printing and traditional techniques. Explore our extensive range of high-quality materials to find the perfect match for your design vision.
