What is anodizing steel? In this article we’ll uncover this process, weigh its pros and cons, and discover how it transforms steel across various sectors.
Introduction
Anodizing steel is an electrochemical process that converts the metal surface intoa decorative, durable, corrosion-resistant, anodic oxide finish. Anodizing canprotect steel from a variety of corrosive environments and make steel morewear-resistant.
Anodized steel is commonly used in various applications, including automotiveindustry, electronics and more.
Understanding Anodizing Steel
What is Anodizing?
Anodizing is an electrochemical process that converts the surface of a metal into a protective oxide layer. This layer, called anodic oxide, is harder, more durable, and more corrosion-resistant than the underlying metal.
Anodizing can be applied to various metals, including aluminum, titanium, magnesium, and steel.
Why is Steel Anodized?
Steel is anodized to protect itself from rust and enhance its overall performance. The resulting benefits include improved corrosion resistance, increased durability, potential aesthetic improvements, and some level of electrical insulation.
These advantages make anodized steel a valuable material choice for various applications across different industries.
How Anodizing Works on Steel?
Pre-Anodizing Preparations
- Surface Cleaning: Remove grease, dirt, and contaminants to ensure a good oxide layer forms..
- Surface Roughening (optional) : Sandblasting or grit blasting can increase surface area for better oxide adhesion (if needed).
- Surface Etching (optional) : A chemical dip removes a thin layer of steel for improved oxide adhesion (if necessary).
Process Overview
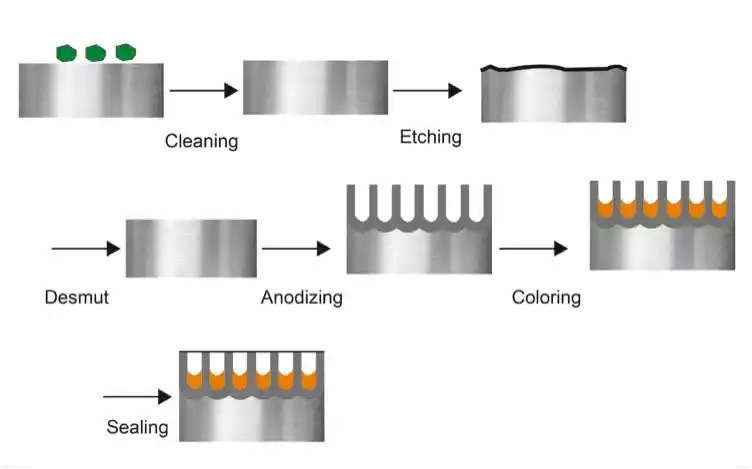
- Cleaning and Pretreatment: The steel surface is thoroughly cleaned and pretreated to remove any contaminants and ensure a uniform oxide layer.
- Electrolytic Bath: The steel is submerged in an electrolytic bath containing an acidic solution, typically sulfuric acid.
- Direct Current: A direct current is passed through the bath, making the steel the anode (positive electrode).
- Oxide Formation: Oxygen ions in the electrolyte migrate towards the anode and react with the steel surface, forming the anodic oxide layer.
- Sealing: After anodizing, the oxide layer is often sealed in hot water or a chemical solution to improve its durability and corrosion resistance.
Chemical Reactions
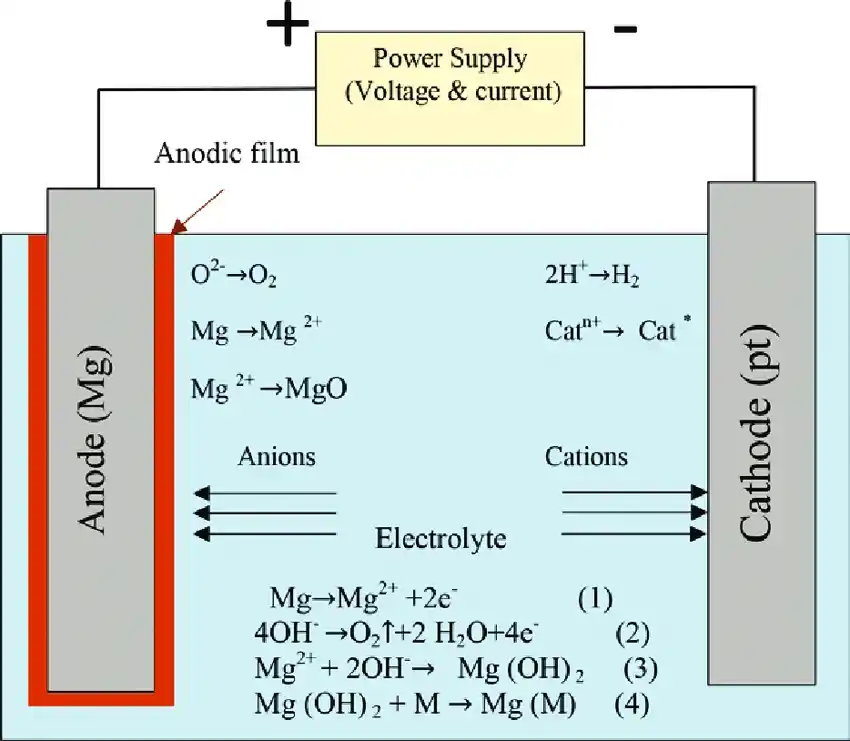
- Anode (Steel): Iron atoms lose electrons, becoming ferrous ions (Fe²⁺) that enter the electrolyte.
- Cathode: Hydrogen ions (H⁺) gain electrons and form hydrogen gas (H₂) bubbles.
Overall, iron ions react with water to form a protective iron oxide layer (like magnetite, Fe₃O₄) on the steel surface. This layer fights rust and enhances durability.
Techniques of Anodizing Steel
Methods of Anodizing
Method | Oxide Layer Thickness | Applications |
---|---|---|
Sulfuric Acid Anodizing | 0.5-2 mm | General purpose, decorative, electrical components |
Hardcoat Anodizing | 25-50 mm | Wear parts, tooling, machinery components |
Chromic Acid Anodizing | 0.5-2 mm | Similar to SAA, but with better color options |
Oxalic Acid Anodizing | 0.5-2 mm | Similar to SAA, but more environmentally friendly |
Phosphoric Acid Anodizing | 0.5-2 mm | Similar to SAA, but with a more matte finish |
Pros and Cons of Anodizing Steel
Pros
- Enhanced Corrosion Resistance: The primary benefit. Anodizing creates a stable oxide layer that acts as a barrier against rust and other forms of corrosion. This extends the lifespan of steel exposed to moisture or harsh environments.
- Improved Durability: The anodizing process hardens the steel surface, making it more resistant to scratches, abrasions, and wear and tear.
- Aesthetic Options: Compared with bare steel, anodizing can create a black oxide layer or even other colors, potentially eliminating the need for additional painting or coating.
- Electrical Insulation Properties: The oxide layer formed during anodizing provides some electrical insulation,which can be beneficial in specific applications.
Cons
- Potential for Hydrogen Embrittlement: If not properly controlled, the anodizing process can introduce hydrogen into the steel, which can make it brittle and susceptible to cracking.
- Dimensional Changes: The anodizing process can cause slight changes in the dimensions of the steel parts.
- Color Limitations: The natural color of anodized steel is typically a dull gray or black. Color options are limited compared to other finishes.
- Increased Cost: Anodizing adds an additional cost to the manufacturing process.
- Environmental Concerns: Some anodizing processes use hazardous chemicals, which can pose environmental risks.
Applications of Anodized Steel
Anodized steel finds uses in various industries due to its properties:
- Architecture: Corrosion resistance and aesthetics make it ideal for building facades, railings, and cladding.
- Automotive: Wheels, trim, and some engine components benefit from wear resistance and corrosion protection.
- Aerospace: Lightweight and durable, it’s used in some aerospace components.
- Consumer Goods: Tools, hardware, and cutlery can be anodized for better wear and appearance.
- Medical Equipment: Corrosion resistance and biocompatibility make it suitable for certain medical instruments.
- Electronics (limited): Some components might utilize its slight electrical insulation properties.
Conclusion
Anodizing steel offers a unique set of advantages. The resulting oxide layer significantly improves corrosion resistance and durability, while also offering some aesthetic options and electrical insulation properties. When strategically applied, anodizing steel can be a valuable tool .
Find Perfection in Finishing at Unionfab
In addition to anodizing, there’s a wide range of finishing techniques available. Unlock the full potential of your creation with expert finishing services at Unionfab:
Bead blasting: Creates a matte or textured finish for improved grip or a decorative effect.
Polishing: Creates a smooth and reflective surface, ideal for aesthetic applications.
Powder coating: Applies a durable and colorful coating for both aesthetics and protection.
Tumbling: Smoothes and cleans parts using abrasive media in a rotating container.
Explore new possibilities, unleash your design’s full potential, and create something truly remarkable!
