What is passivation and why is it important? This article explores the process of passivation, the techniques used, and applications in industries.
Introduction
Passivation produces oxide films that safeguard metals from corrosion. It works by controlling how metal oxides form on the surface. This creates an invisible shield that blocks oxygen and moisture from reaching the metal underneath.
Passivation ensures product longevity, maintains cleanliness in sectors like food processing, and enhances electronic device reliability by safeguarding against environmental factors. It helps products last longer by preventing rust.
What is Passivation?
Define Passivation
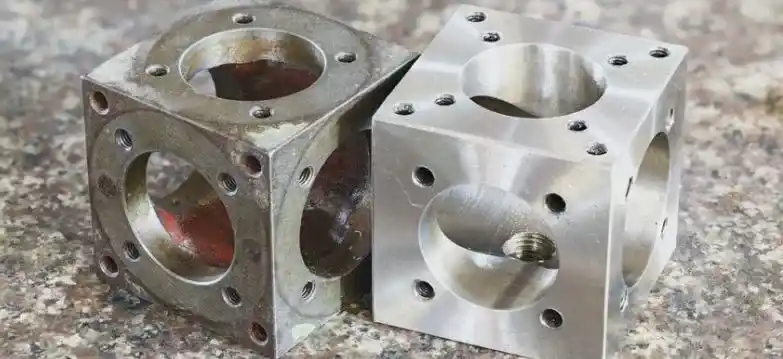
Passivation is a post-manufacturing process that is performed after welding, grinding, cutting and other machining operations.
This technique puts a protective layer on metals to stop rusting. It works by using chemical or electric reactions to change how metal atoms bond on the surface.
How Passivation Differs from Others
Passivation stands out from other corrosion protection methods in a key way: it modifies the metal itself.
Method | Protection Mechanism | Material Dependence | Advantages | Disadvantages |
---|---|---|---|---|
Passivation | Strengthens natural oxide layer | Stainless steel only | Simple, good corrosion resistance | Limited use |
Painting/Coating | Acts as a physical barrier, isolating the metal from the environment | Many materials | Customizable, good protection | Maintenance, chipping |
Galvanization | Sacrificial protection – the zinc coating corrodes first, protecting the underlying steel | Iron and steel | Excellent outdoor protection | Not ideal for all environments, bulky |
Electroless Plating | Creates a new, thin layer of a different metal on the surface through a chemical reaction | Many materials | Hard, durable | Complex process |
Mechanisms of Passivation
Passivation shields metals from corrosion by forming a protective oxide layer.
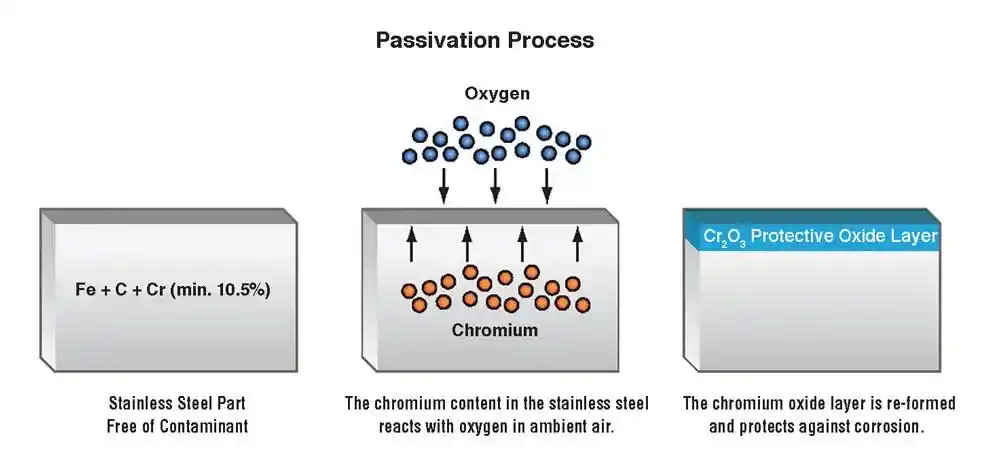
Step 1. Metal Dissolves
The metal surface breaks apart a little, letting metal pieces (ions) mix into the liquid. This activates the metal for the next step.
Step 2. Hydrous Oxide Film Forms
As the metal comes apart, it reacts with water to make a very thin, watery rust layer. This is like a first coating on the metal.
Step 3. Special Metal Ions Join in
Under the right conditions, ions like chromium that really like oxygen get added to the rust layer. This makes the rust layer stronger.
Step 4. Rust Hardens and Protects
The rust layer loses water molecules and gets very dense, changing into a stable, tight “passive layer.” This layer stops more metal from dissolving and blocks harmful stuff from touching the metal surface. The metal is now protected from rusting.
Factors Influencing Passivation
Metal Composition
The ability of a metal to form a stable and effective passive layer heavily depends on its composition.
Element | Role in Passivation |
---|---|
Chromium (Cr) | Forms a protective chromium oxide layer, key for passivation |
Molybdenum (Mo) | Improves chromium oxide layer stability (especially with chlorides) |
Nickel (Ni) | Enhances overall stability and mechanical properties of the passive layer |
Nitrogen (N) | May improve localized corrosion resistance in specific cases |
Surface Condition
The condition of the metal surface strongly affects how well it can be protected.
- Contaminants: Contaminants like oil, grease, dust or existing rust prevent the protection solution from reacting right with the metal below. This stops an even protective layer from forming properly.
- Surface roughness: Surface roughness also affects protection. Valleys may not get treated enough while peaks get too much, giving inconsistent coverage. A smooth, even surface allows for uniform protection.
- Scars and Weak Spots: Scratches, dents or other flaws act as weak spots that corrosion can start from. Embedded debris has the same effect. If these imperfections are not removed, corrosion will occur more quickly at the vulnerable spots. This will then spread and reduce how well the rest of the protected surface is shielded from damage.
Passivation Treatment
The passivation treatment itself plays a big role in how well it works.
- Temperature: Generally, higher temperatures during passivation promote a more robust and complete passive layer. Think of it like cooking – higher heat allows a reaction to proceed more thoroughly.
- Treatment Uniformity: Consistent application of the passivation solution is crucial. Uneven application due to factors like poor agitation or inadequate time can lead to a patchy and ineffective passive layer. Imagine painting a wall – you need even strokes for good coverage.
- Solution type: The specific type of passivation solution used can also influence effectiveness. Different solutions are formulated for different metals and can have varying strengths and effects on the passive layer formation.
Common Methods of Passivation
There are many methods of passivation. Each method has its own characteristics.
Method | Operation | Pros | Cons |
---|---|---|---|
Immersion | Submerging metal in a solution to form a protective oxide layer | Simple, versatile | Not ideal for complex shapes/acid-sensitive materials |
Nitric Acid | Nitric acid bath removes contaminants and promotes a chromium oxide layer | Effective for stainless steel | Requires special handling |
Nitric Acid + Dichromate | Enhanced immersion with added chemical for superior protection | Highest resistance | Environmentally hazardous |
Anodizing (Electrolytic) | Electric current creates a thick oxide layer | Hard, decorative | Requires equipment, limited materials |
Conversion Coatings | Dipping metal in a conversion solution for a corrosion-resistant layer | Good resistance, various materials | Less durable layer |
Importance of Passivation
Corrosion Protection
Passivation acts as a suit of armor for metals. It forms a protective oxide layer that shields the underlying metal from rust, wear, and environmental attacks, significantly extending its lifespan.
Enhanced Durability
The oxide coating fortifies metal, making it more resilient to scratches, dents and physical abuse. Components see improved performance and extended use.
Cost-effectiveness
While initial passivation costs money, it saves overall through extended component life. Preventing corrosion cuts replacement and repair expenses. Less maintenance further reduces costs long-term.
Aesthetic Preservation
The process leaves a lustrous, blemish-free shine that enhances visual appeal. Important where exposed metal impacts design, like appliances and architectural features.
Chemical Resistance
The oxide acts as a chemical barricade, stopping specific solutions from reacting with the substrate. Crucial for withstanding bleach, acids and factory environments.
Biocompatibility
In some cases, passivation creates a more inert interface, potentiallyreducing rejection risk for certain implants. But effects depend on metal and treatment used.
Applications of Passivation
Aerospace
- Aircraft components: Passivation safeguards critical aircraft parts like engine components, landing gear, and fuselage panels from corrosion caused by high humidity, extreme temperatures, and de-icing fluids.
- Fuel systems: Passivated components in fuel systems enhance their resistance to corrosion from jet fuel and ensure the integrity of the fuel delivery system.
Medical Devices
- Implants: Passivation creates a biocompatible surface on certain implants, like stents or surgical instruments, reducing the risk of rejection and ensuring their long-term functionality within the body.
- Dental instruments: Passivated dental tools resist corrosion from disinfectants and bodily fluids, maintaining their sharpness and functionality during procedures.
Automotive
- Engine components: Passivation protects engine parts like exhaust manifolds and coolant passages from corrosion caused by high temperatures, exhaust fumes, and coolants.
- Fuel system components: Passivation safeguards fuel injectors, pumps, and lines from corrosion by gasoline and ethanol blends, ensuring reliable fuel delivery.
Electronics
- Semiconductor components: Passivation creates a thin, protective oxide layer on electrical leads and bond pads of electronic chips, preventing corrosion and ensuring reliable electrical connections.
- Encapsulants: Passivated encapsulants offer additional protection for electronic components from moisture and environmental contaminants.
Food Processing
- Food processing equipment: Passivation safeguards equipment surfaces that come into contact with food products from corrosion caused by acidic or salty foods. This helps maintain hygiene and prevents contamination.
- Storage tanks: Passivated storage tanks for food liquids like juices or syrups improve corrosion resistance, ensuring product quality and storage integrity.
Passivation Standards
For passivation to work properly, the process needs to be controlled carefully. That’s where passivation standards come in.
Standards are guidelines that specify things like the correct types of chemicals to use, temperatures, timing, and testing methods. Following the standards helps ensure consistent and high-quality results.
Standard | Organization | Application | Focus |
---|---|---|---|
ISO 16048 | International Organization for Standardization (ISO) | General – Corrosion-resistant alloys (iron-chromium, nickel-copper) | Bath chemistry, temperature/duration, agitation |
ASTM A967 | ASTM International | Metal finishing – Stainless steel | Nitric/citric acid solutions, testing methods |
AMS 2700 | Society of Automotive Engineers (SAE) Aerospace Material Specification (AMS) Committee | Aerospace – Steel & nickel alloys | Methods, materials, verification |
QQ-P-35C | US Department of Defense (DoD) | Government applications – Stainless steel | Surface preparation, acid treatment, rinses & seals |
Conclusion
Passivation protects metals through a protective oxide barrier. By promoting the formation of a thin, invisible oxide layer, passivation significantly extends the lifespan and maintains the functionality of metal components across various industries.
Beyond resisting corrosion, passivation boosts durability, lowers costs and maintains appearance. Offering multifaceted benefits through a straightforward process, passivation proves its worth as a vital anticorrosion technique.
Achieve Perfection in Finishing at Unionfab
Elevate your creation with comprehensive finishing solutions at Unionfab:
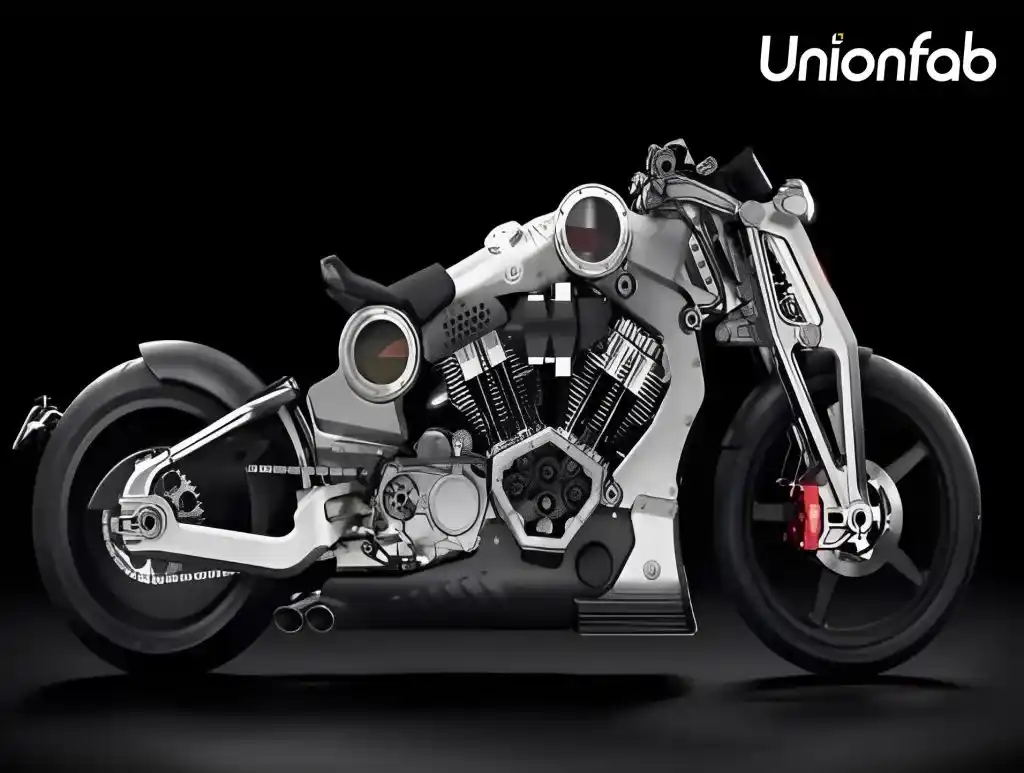

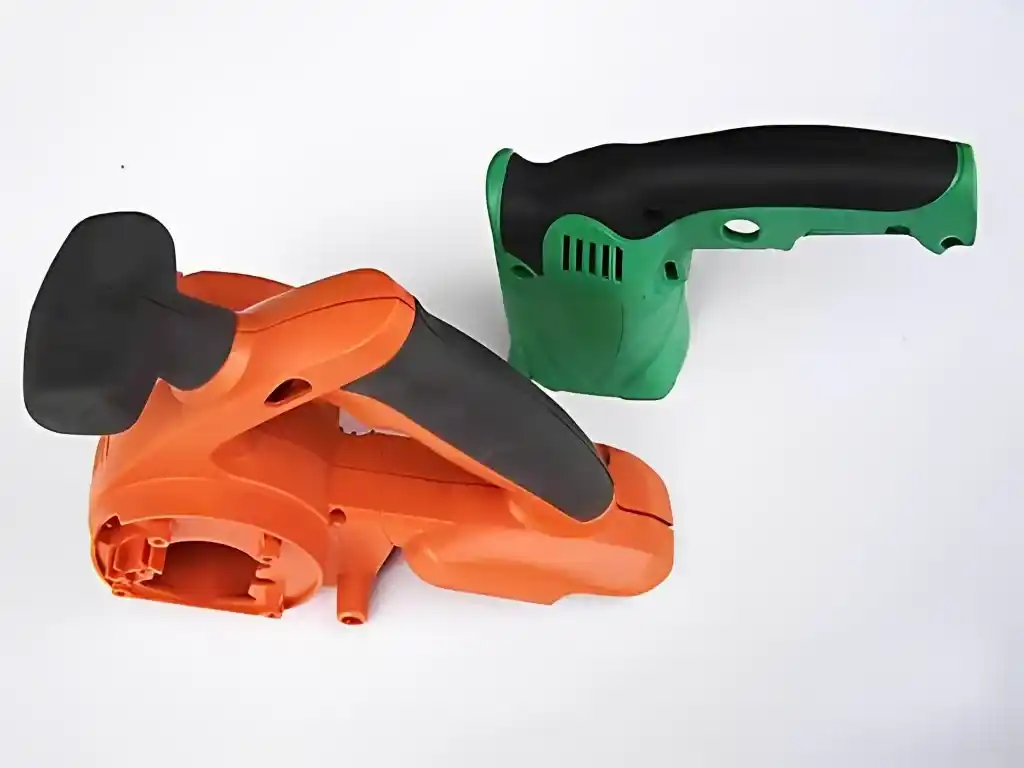
Painting and Dyeing: We ensure a uniform, professional look through meticulous painting and natural dyeing techniques that yield parts with consistent, vibrant color throughout.
Metal Plating: Choose from electroplating options to add sophistication and luxury, upgrade materials, or boost functionality with hardening or anti-corrosion qualities
Silk Screening: Unionfab offers a full-service silk-screen printing solution. We can customize the process for your specific products and designs.
Laser Marking: Unionfab provides laser marking services using advanced laser technology. The laser neatly etches these directly onto the surface of the material without damaging the surrounding area.
Discover alternatives, maximize your design’s potential, and produce something truly remarkable!