Learn how the properties and costs of 6061 vs 7075 aluminum influence appropriate applications and help engineers select the best alloy.
Introduction
Overview of 6061 and 7075 Aluminum Alloys
6061 and 7075 alloys are two of the most widely used types of aluminum. Both contain magnesium as a primary alloying element, but their compositions give them different characteristics well-suited to distinct applications.
While both offer advantages over other metals, their varying properties can impact durability and performance if the wrong alloy is selected. 6061 aluminum has good formability and machinability due to about 1% magnesium and silicon. It is commonly extruded, rolled, and drawn for general structural components. 7075 aluminum contains higher amounts of zinc, magnesium and copper providing high strength and fatigue resistance ideal for aircraft structures.
This article provides a side-by-side comparison of 6061 and 7075 aluminum, examining key metrics like mechanical properties, corrosion resistance, cost and typical uses to help engineers determine the best alloy for their needs.
Here is an expanded section on 6061 aluminum:
What is 6061 Aluminum?
Chemical Composition
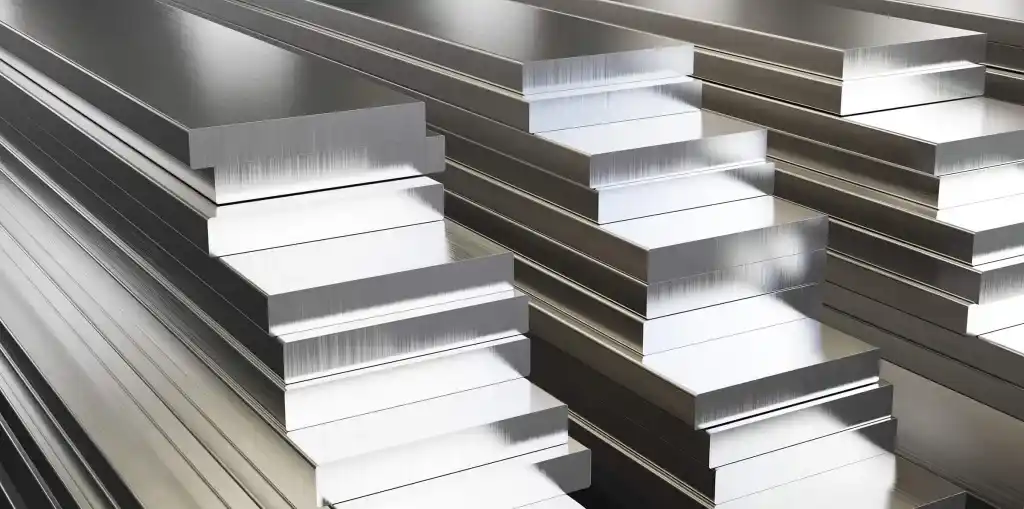
6061 aluminum is a precipitation-hardened alloy containing a maximum of 1.0% magnesium and 0.6% silicon as its primary alloying elements. Other allowable elements in lesser amounts include chromium, copper, iron and zinc.
Physical Properties
- Medium-high strength: Tensile yield strength of about 276 MPa (40 ksi) giving good structural capability.
- Good ductility and formability: It can be readily extruded, rolled, drawn or machined into complex shapes.
- Fatigue and corrosion resistance: Moderate strength retention over time and ability to withstand corrosion exposure.
- Machinability: The silicon content improves machining characteristics, allowing efficient cutting, drilling, etc.
- Surface finish: Leaves surfaces with a brighter, smoother texture than 7000 series alloys.
Common Uses
- General structural components: Load-bearing beams, panels, fittings in industrial or construction equipment.
- Transportation: Auto or truck chassis, suspension parts, bicycles frames benefiting from light weight.
- Marine/boating: Hulls, decks where corrosion resistance is important.
- Aerospace applications: Secondary aircraft structures, window frames where high strength isn’t critical.
- Consumer goods: Lawn equipment, appliances, sporting goods utilizing formability and moderate strength.
What is 7075 Aluminum?
Chemical Composition
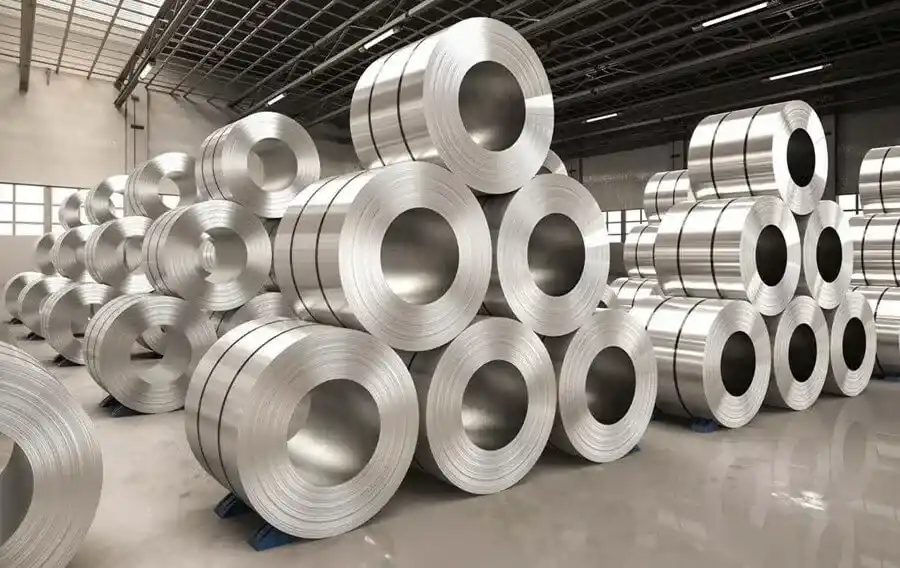
7075 aluminum contains 5.6-6.1% zinc as its main alloying element. It also contains 2.1-2.9% magnesium and 1.2-2.0% copper. This composition contributes to its excellent mechanical properties.
Physical Properties
- High strength: Yield strength of around 455 MPa (66 ksi), over 60% stronger than 6061.
- Fatigue and impact resistance: Good resistance to stress fluctuations and impacts over long periods.
- Stiffness: Modulus of elasticity of about 73 GPa provides durability against deflection.
- Hardness: Higher hardness of 112 BHN versus 95 BHN for 6061 aids wear resistance.
- Corrosion resistance: Moderately resistant but less than 6061 due to its zinc content.
Common Uses
- Aircraft structures: Skins, spars, frames where exceptional strength is required.
- Military applications: Armored vehicles, protective equipment leveraging the weight savings.
- Construction equipment: Buckets, gears, under-hood components facing fatigue stresses.
- Tooling: Jigs, fixtures for heavy manufacturing thanks to its rigidity.
- Industrial parts: Valves, pistons benefiting from premium strength in harsh conditions.
6061 vs 7075: Mechanical properties comparison
Tensile strength, yield strength, hardness, fatigue resistance, impact resistance – how do 6061 and 7075 compare?
Property | 6061-T6 | 7075-T6 | Notes |
---|---|---|---|
Tensile Strength (MPa) | 310 | 570 | 7075 is nearly 84% stronger |
Yield Strength (MPa) | 270 | 490 | 7075 is 81% stronger |
Hardness (Brinell Hardness Number) | 95 | 150 | 7075 is 58% harder |
Fatigue Resistance | Moderate | Good | 7075 offers better resistance to repeated stress |
Impact Resistance | Moderate | Good | 7075 generally has better impact absorption |
- Tensile & Yield Strength: 7075 clearly dominates in both tensile and yield strength, meaning it can withstand significantly higher pulling and bending forces before breaking or deforming permanently.
- Hardness: Similar to strength, 7075 exhibits greater hardness, making it more resistant to scratching and indentation.
- Fatigue Resistance: While both offer decent fatigue resistance, 7075 performs slightly better due to its superior strength and resistance to microscopic cracks under repeated stress.
- Impact Resistance: 7075 generally shows better resistance to sudden impacts due to its slightly higher ductility (ability to deform without breaking).
6061 vs 7075: Corrosion resistance comparison
The corrosion resistance of aluminum alloys, like 6061 and 7075, is influenced by their composition.
6061 Aluminum:
- Generally considered more corrosion-resistant than 7075.
- Higher aluminum content allows it to form a more consistent and robust oxide layer. This layer acts as a barrier against external elements, protecting the underlying metal.
7075 Aluminum:
- Has lower corrosion resistance compared to 6061.
- Higher copper content (around 1.8-2%) compared to 6061 (around 0.6%) makes it more susceptible to corrosion. Copper is more reactive than aluminum and readily interacts with the environment, leading to faster breakdown of the protective oxide layer.
Generally, 6061 aluminum exhibits better corrosion resistance than 7075.
6061 vs 7075: Machinability
Machinability refers to the ease with which a material can be shaped through processes like cutting, drilling, and milling.
When it comes to these two aluminum alloys, 6061 is significantly easier to machine compared to 7075. This difference arises primarily from their contrasting alloy compositions:
6061 Aluminum:
- Contains lower amounts of harder elements like magnesium and copper: These elements contribute to the alloy’s strength but also make it more challenging to machine.
- Softer and more ductile: Due to its lower content of hardening elements, 6061 is softer and more pliable, allowing machining tools to cut through it more readily with less wear on the tools themselves.
- Produces shorter and less abrasive chips: These chips are easier to manage and pose less risk of damaging the tools or the machined surface.
⠀7075 Aluminum:
- Contains higher percentages of magnesium and copper: These elements enhance its strength but make it harder and more abrasive to machine.
- Produces longer and stringy chips: These chips can clog tools, require frequent cleaning, and potentially cause surface imperfections on the machined part.
- Requires sharper and more wear-resistant tools: Due to its increased hardness and abrasiveness, 7075 necessitates the use of specialized cutting tools that can withstand the wear and tear of machining.
6061 vs 7075: Cost comparison
There is a significant cost difference between 6061 and 7075 aluminum, with 7075 generally being more expensive across various product forms like sheet, bar, and others.
Relative Cost of 6061 and 7075
- 6061: Considered a commercially pure aluminum and readily available, making it more cost-effective. Its lower production complexity and wider availability translate to lower prices for various forms.
- 7075: Due to its higher strength and the inclusion of additional alloying elements like copper and zinc, 7075 comes at a premium. The additional processing and higher demand for specific applications contribute to its increased cost.
6061 vs 7075: Cost Examples
While specific prices can vary depending on factors like market fluctuations, location, and supplier, here’s a general comparison:
- Sheet Metal: 6061 sheet metal can be roughly 20-30% cheaper than 7075 of the same thickness and size.
- Bar Stock: Similar to sheet metal, 6061 bar stock can be 25-35% less expensive than 7075 of the same size.
6061 vs 7057: Applications
Here’s a recap of the typical applications of 6061 and 7075 aluminum based on their respective properties:
6061 Aluminum (Versatile, Cost-Effective, Moderate Strength):
- Building and construction: Cladding, roofing, door frames, window frames, and non-structural components.
- Electrical applications: Bus bars, enclosures, conductor rails, and heat sinks.
- General fabrication: Furniture, brackets, pipes, tubing, and non-critical automotive parts (e.g., wheel covers).
- Marine applications: Due to its decent corrosion resistance, it’s used in some non-critical marine components like railings and hatches.
- Consumer goods: Appliance parts, bicycle frames (mid-range), and sporting goods (e.g., baseball bats).
⠀7075 Aluminum (High Strength, Lower Corrosion Resistance):
- Aerospace: Aircraft wings, fuselage components, and landing gear due to its exceptional strength-to-weight ratio.
- Military and defense applications: Armor components, weapons parts, and other high-stress applications.
- Sporting goods: High-end bicycle frames, baseball bats, and other equipment requiring high strength and minimal weight.
- Automotive: Parts requiring high strength, such as pistons, connecting rods, and suspension components in high-performance vehicles.
- Molds and tooling: Due to its good machinability and strength after heat treatment, it’s used in some molds and tooling applications.
Conclusion: Choosing the Right Aluminum Alloy
The choice between 6061 and 7075 depends on your specific application’s needs. Consider the following factors:
- Required strength: If high strength is paramount, 7075 might be ideal. For moderate strength, 6061 is sufficient.
- Corrosion resistance: If your application experiences harsh environments, 6061 might be a better choice due to its superior corrosion resistance.
- Machinability: If ease of machining is important, 6061 is the clear winner.
- Cost: If cost is a major concern, 6061 is considerably cheaper than 7075.
By carefully considering these factors, you can select the most appropriate aluminum alloy for your project, ensuring optimal performance and cost-effectiveness.
1 comment
An impressive share! I’ve just forwarded this onto a coworker who has been conducting a little
research on this. And he actually bought me breakfast due to the fact that I stumbled upon it for
him… lol. So allow me to reword this…. Thanks for the meal!!
But yeah, thanx for spending time to talk about this subject here on your internet site.