- Introduction
- Advancements in Additive Manufacturing Technology
- Applications of Additive Manufacturing in Aerospace
- Benefits of Additive Manufacturing in Aerospace
- Challenges and Limitations
- Case Studies and Industry Examples
- Future Trends and Innovations
- Conclusion
- At Unionfab Experience Various 3D Printing Services
In this article, learn about the latest advances and significant uses of additive manufacturing (AM) in aerospace.
Introduction
Additive manufacturing (AM), or 3D printing, builds objects layer by layer from a digital design, enabling the creation of complex geometries previously impossible with traditional techniques.
Though a young technology with commercial use beginning in the 1980s, AM’s integration into aerospace has rapidly developed in recent decades.
Pioneering companies saw the potential of AM to optimize designs, reduce weight, and streamline production, making it a critical tool for the industry’s constant pursuit of lighter, stronger, and more efficient aircraft.
Advancements in Additive Manufacturing Technology
Types of Additive Manufacturing Technologies Used in Aerospace
Stereolithography (SLA)
This technique uses a laser to cure liquid resin layer-by-layer, ideal for creating high-precision, intricate parts for prototyping and wind tunnel models.
Selective Laser Sintering (SLS) & Direct Metal Laser Sintering (DMLS)
These processes use a laser to fuse powdered materials (plastics for SLS, metals for DMLS) into solid objects. They offer excellent strength and are suitable for functional aerospace components.
Fused Deposition Modeling (FDM)
FDM uses a heated extruder to deposit molten plastic filament, creating lightweight and cost-effective parts suitable for non-critical applications or initial prototypes.
Electron Beam Melting (EBM)
This technology utilizes an electron beam to melt metal powders, creating high-performance parts with exceptional strength and heat resistance, ideal for jet engine components.
Material Innovations
- Advanced metals and alloys: These offer superior strength-to-weight ratios, enabling lighter and more fuel-efficient aircraft. Think titanium alloys for airframes and Inconel for high-temperature engine components.
- Polymers and composites: Tailored polymers with improved heat resistance and flame retardancy are finding applications in aircraft interiors and non-structural components. Additionally, composites with embedded fibers offer unique mechanical properties.
- Ceramic Materials: Research in ceramic AM is ongoing, with potential applications for heat-resistant engine components and lightweight, high-temperature structures.
Improvements in Precision and Scalability
Advancements in printing resolution and laser control are leading to the creation of parts with tighter tolerances and finer features.
Larger build volumes and faster printing speeds are enabling the production of bigger and more complex aerospace components.
Automation and software improvements are streamlining the AM process, making it faster, more efficient, and more cost-effective for production.
Applications of Additive Manufacturing in Aerospace
Prototyping and Product Development
Rapid Prototyping
AM’s ability to quickly create functional prototypes from digital models allows for faster design iterations and testing cycles. This streamlines the development process and reduces time-to-market for new aerospace vehicles.
Design Optimization and Testing
Complex internal features and lightweight lattice structures can be easily incorporated into AM prototypes, enabling engineers to test and optimize designs for performance and weight efficiency.
Production of Aerospace Components
Engine Parts
Fuel nozzles, turbine blades, and other intricate engine components can be additively manufactured with complex cooling channels, leading to more efficient and powerful engines.
Structural Components
Brackets, supports, and other lightweight structural components can be AM-produced, optimizing weight and performance. Think complex lattice structures for increased strength-to-weight ratio.
Interior Parts
Customizable seating, lightweight cabin components, and even personalized passenger amenities can be 3D printed, enhancing passenger comfort and potentially reducing weight.
Maintenance, Repair, and Overhaul (MRO)
On-Demand Part Replacement
Obsolete or hard-to-find parts can be readily printed at repair facilities, reducing downtime and keeping aircraft operational.
Tooling and Fixture Production
Custom jigs, tools, and fixtures needed for aircraft assembly and maintenance can be 3D printed quickly and efficiently, streamlining the MRO process.
Benefits of Additive Manufacturing in Aerospace
Design Flexibility and Customization
AM allows for the creation of complex geometries and intricate internal structures that were unimaginable with traditional methods. This is beneficial to highly customized designs tailored for specific functions and performance needs.
Weight Reduction and Performance Enhancement
AM excels at creating lightweight components with superior strength-to-weight ratios. This translates to significant fuel savings, increased range, and improved overall aircraft performance.
The ability to create intricate internal structures allows for parts to be lighter and stronger simultaneously. This optimization leads to more efficient engines, improved aerodynamics, and ultimately, better performing aircraft.
Cost Savings and Efficiency Improvements
AM builds parts layer-by-layer, minimizing material waste compared to traditional subtractive manufacturing techniques.
Complex assemblies can be additively manufactured as single components, reducing part count, assembly time, and overall production costs.
Reduction in Lead Times and Supply Chain Optimization
AM allows for quick and efficient creation of functional prototypes, accelerating the design and development process. This leads to faster time-to-market for new aircraft models.
With AM, parts can be printed as needed, reducing reliance on extensive stockpiles and potentially leading to a more agile and responsive supply chain.
Sustainability and Environmental Impact
AM minimizes material waste compared to subtractive techniques.
Its ability to create lightweight components leads to reduced fuel consumption by aircraft, lowering carbon emissions.
Additionally, AM allows for the potential use of recycled materials in the printing process, further reducing the environmental footprint.
Challenges and Limitations
Technical and Engineering Challenges
- Material Properties and Performance: Some AM-produced materials may not yet fully match the established properties and performance of traditionally manufactured aerospace materials.
- Quality Control and Certification: The layer-by-layer nature of AM can introduce potential inconsistencies in part quality.
Economic and Logistical Barriers
- High Initial Investment Costs: AM equipment can be expensive, and setting up an AM production line requires significant investment.
- Scalability Issues: Current AM machines often have limitations on build size. Producing large-scale aerospace components can be challenging, and production times may be longer compared to traditional methods for certain parts.
Regulatory and Compliance Concerns
- Standardization and Certification Processes: Regulatory bodies are still developing standardized guidelines and certification processes for AM-produced aerospace parts. This lack of established procedures can create uncertainty and hinder wider adoption.
Case Studies and Industry Examples
Boeing, a leading aerospace giant, is at the forefront of utilizing additive manufacturing (AM), also known as 3D printing, to revolutionize aircraft design and production.
3D-Printed Satellite: WGS-11+
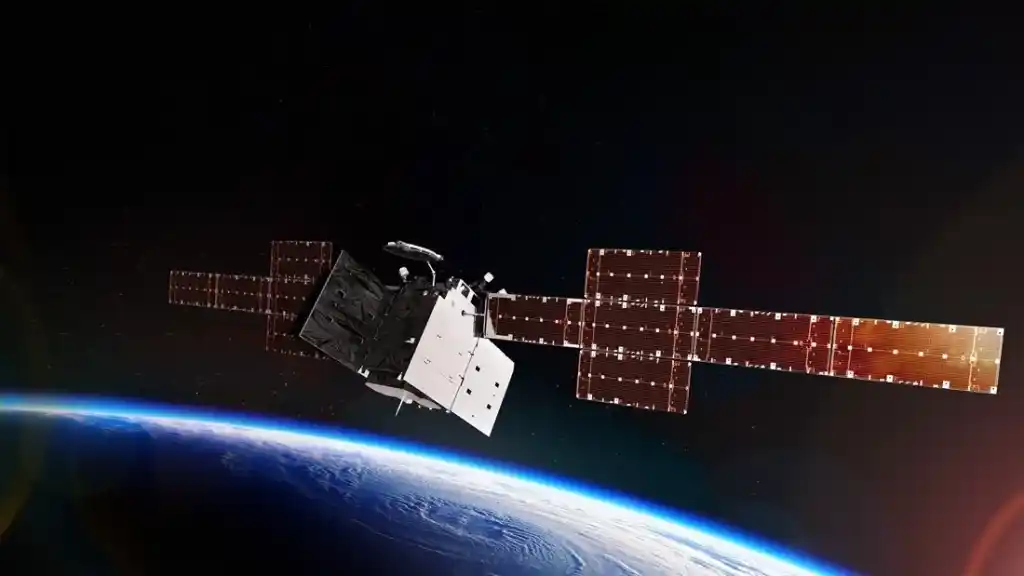
Source: boeing.mediaroom.com
Project
Boeing is collaborating with the U.S. Army to build the WGS-11+, the 11th satellite in the WGS constellation. This next-generation military communications satellite leverages AM for over 1,000 parts.
Benefits
- Speed: AM allows for faster production compared to traditional methods, potentially leading to quicker deployment of the satellite.
- Customization: The ability to 3D print parts enables the creation of components with specific functionalities and performance characteristics.
- Weight Reduction: AM-produced parts can be lighter than traditionally manufactured components, which is crucial for satellites due to launch weight limitations.
MQ-25 Stingray: The 3D-Printed Refueling Drone
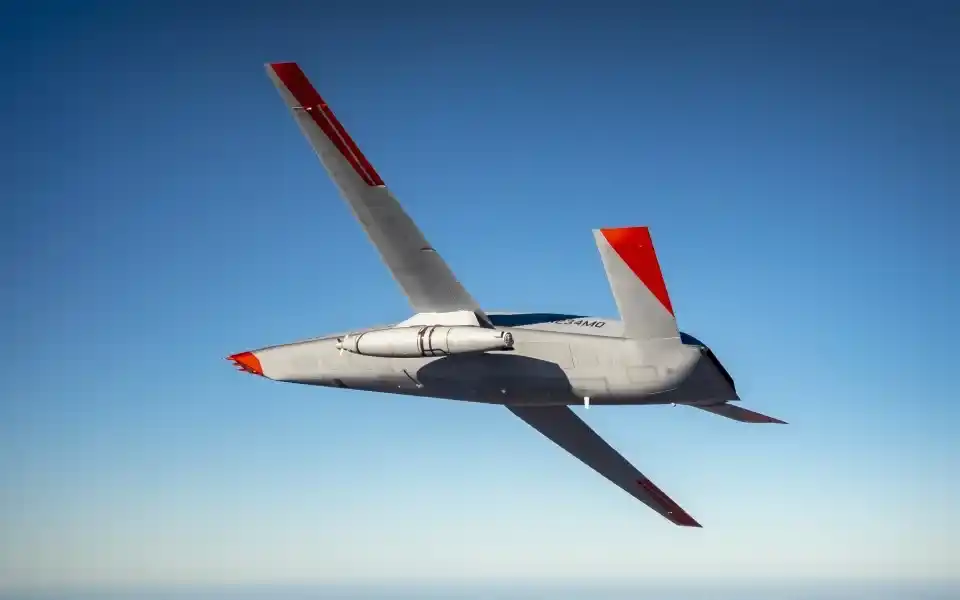
Source: boeing.com
Project
The MQ-25 Stingray is a next-generation unmanned aerial refueling drone being developed by Boeing for the U.S. Navy. While details on specific AM applications are limited, Boeing has acknowledged using 3D printing for certain components.
Possible Applications
AM could potentially be used for intricate internal parts, lightweight structures, or even complex antenna housings on the MQ-25.
Chinook Helicopter: First Flight-Critical AM Component
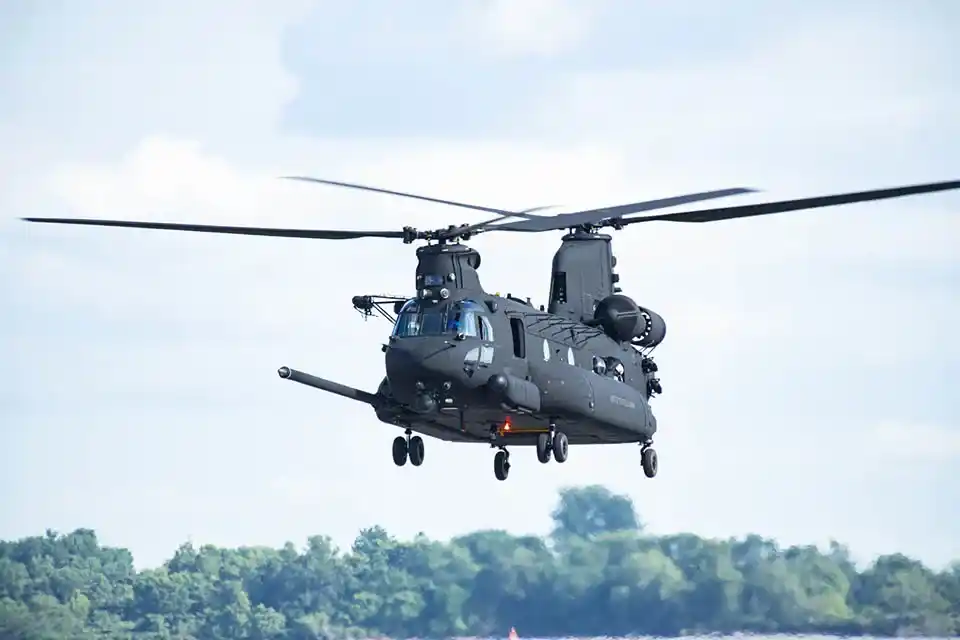
Source: boeing.com
Project
Boeing successfully test-flies a CH-47 Chinook helicopter with a 3D-printed aluminum gearbox housing. This marks the first instance of a rotorcraft using a flight-critical component produced via additive manufacturing.
Significance
This successful test paves the way for broader adoption of AM in critical helicopter components, potentially leading to lighter, more efficient designs, and faster production times.
Future Trends and Innovations
Emerging Technologies in AM
Multi-Material Printing
This technology allows for the creation of parts with graded properties, where material composition changes within the object. This could lead to, for example, a turbine blade with a strong, heat-resistant core and a wear-resistant outer layer.
Nano-Scale Printing
Nano-scale printing has the potential to create incredibly intricate structures for sensors, micro-electronics, and even micro-fluidic devices used in satellites and spacecraft.
Hybrid Manufacturing Approaches
Combining AM with traditional techniques like machining or casting allows for 3D-printing a complex core structure and then using traditional methods for high-precision finishing touches.
Predictions for the Next Decade
Expansion of AM in Space Exploration
- In-Situ Manufacturing: Building and repairing spacecraft components directly on the moon or Mars, reducing reliance on parts shipped from Earth.
- Habitat Construction: Creating shelters and structures on other celestial bodies using locally sourced materials and 3D printing technology.
Increased Integration with Digital Twin and AI
- Digital Twins: Creating virtual models of AM-produced parts that can be analyzed and optimized for performance before they are even printed, leading to more efficient designs and reduced waste.
- AI-Powered Design and Optimization: AI algorithms can analyze vast amounts of data to recommend optimal printing parameters and identify potential defects before they occur.
Conclusion
Additive manufacturing (AM), or 3D printing, is revolutionizing the aerospace industry. This technology’s ability to create complex, lightweight parts with superior strength-to-weight ratios makes it perfect for the demanding requirements of aircraft design and production.
The future holds promise for even greater advancements like multi-material printing, space-based AM, and AI-powered optimization. Through collaboration and continued innovation, AM has the potential to transform aircraft design, streamline production, and propel us further into the cosmos.
At Unionfab Experience Various 3D Printing Services
Unionfab offers a wide range of 3D Printing services, including SLA, FDM and SLS.
Our team of experts is here to help you optimize your designs and unlock the power of 3D printing for your project.
