This article discover the intricacies of 3d printing stainless steel, from its fundamental principles to its diverse applications across industries.
Introduction
Stainless steel is a popular choice for 3D printing thanks to its desirable qualities. This process, often using SLM 3D printing technique, also known as Direct Metal Laser Sintering (DMLS), fuses layers of metal powder together with a laser to create a strong, corrosion-resistant part.
Understanding 3D Printing Stainless Steel
Basics of Additive Manufacturing
Additive Manufacturing (AM), also known as 3D printing, builds objects layer by layer from a digital design. For stainless steel, this typically involves a metal powder and a high-powered laser. Here’s a breakdown of the process:
- Powder Preparation: Fine stainless steel powder is spread onto a platform.
- Laser Melting: A high-powered laser selectively melts the powder particles according to the design blueprint.
- Layer by Layer: The platform lowers, and a new layer of powder is deposited. The laser then melts the fresh powder, fusing it to the previous layer.
- Support Removal: Once complete, the part is removed from the machine, and any support structures used during printing are removed.
Advantages of 3D Printing Stainless Steel
Design Freedom
3D printing eliminates many limitations of traditional methods. Complex geometries, internal channels, and intricate lattice structures become achievable.
Customization
The ability to directly produce a part from a digital file allows for easy customization and rapid prototyping of various designs.
Complex Geometries
Unlike subtractive techniques, 3D printing can create intricate and lightweight structures that would be challenging or impossible to machine.
Comparison with Other Metals
While stainless steel is a popular choice, other metals are also suitable for 3D printing:
- Aluminum: Offers a good balance of strength, weight, and affordability. Ideal for applications requiring lightweight components.
- Titanium: Exceptionally strong and lightweight but more expensive than stainless steel. Used in aerospace and medical implants due to its biocompatibility.
- Inconel: Known for its high-temperature resistance, making it valuable for applications like jet engine components.
Metal | Advantages | Disadvantages |
---|---|---|
Stainless Steel | Excellent corrosion resistance High strength and density Good balance of cost and properties | Requires post-processing Limited to specific alloys |
Aluminum | Lightweight Affordable Good machinability | Lower strength compared to stainless steel Not ideal for high-temperature applications |
Titanium | High strength-to-weight ratio Excellent biocompatibility | Expensive Difficult to machine traditionally |
Inconel | Exceptional high-temperature resistance Good strength | Very expensive Difficult to print due to high melting point |
Material Properties of 3D Printing Stainless Steel
Mechanical Properties
Strength
3D printed stainless steel parts can achieve high tensile and yield strength, comparable to their wrought counterparts. This makes them suitable for parts that need to withstand significant loads.
Density
The 3D printing process typically results in parts with a density exceeding 99% of solid stainless steel. This translates to strong and reliable components.
Surface Finish
The surface finish of 3D printed stainless steel can vary depending on the printing process and parameters. However, post-processing techniques like polishing can improve the surface quality for specific applications.
Corrosion Resistance
One of the most significant advantages of stainless steel is its excellent resistance to corrosion. This property is retained in 3D printed parts, making them ideal for applications exposed to harsh environments or corrosive elements.
Temperature Resistance
3D printed stainless steel can withstand a wide range of temperatures, depending on the specific alloy used. Generally, these parts can function effectively in moderately high-temperature environments.
Techniques of Stainless Steel 3D Printing
Selective Laser Melting (SLM) 3D Printing
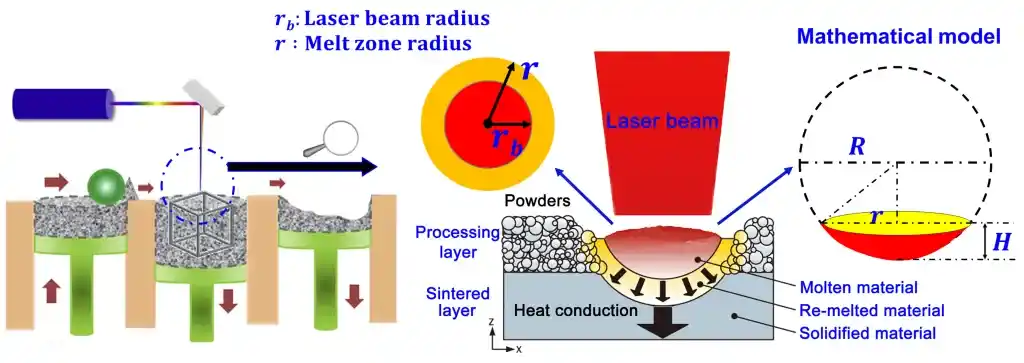
Source: wikipedia.org
SLM, also known as Direct Metal Laser Sintering (DMLS), is the most widely used technique for 3D printing stainless steel.
- Process: A high-powered laser beam selectively melts thin layers of metal powder, fusing them together to create the desired part layer by layer.
- Advantages: Offers high accuracy, excellent surface finish, and the ability to produce complex geometries. Parts boast near-net density and good mechanical properties.
- Disadvantages: Relatively expensive compared to other techniques. Limited build volume due to the laser’s power limitations. Requires support structures for overhanging features, which can add complexity and post-processing time.
Binder Jetting
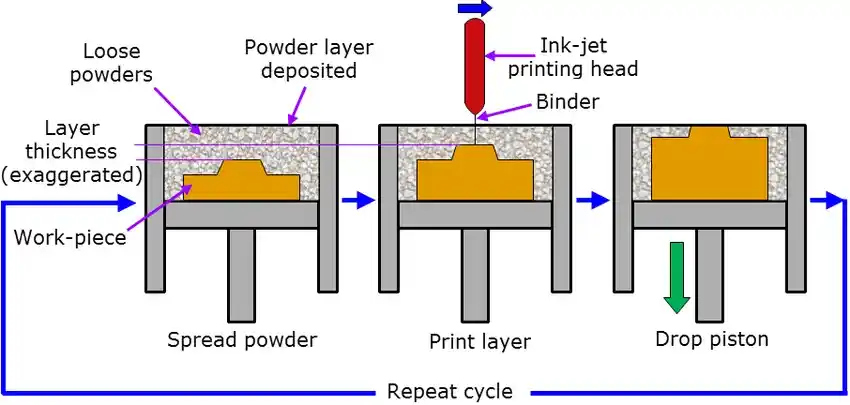
Source: oceanproperty.co.th
This method uses a binder jetting system to selectively deposit a liquid binding agent onto a bed of metal powder. The layers are then infiltrated with a bonding agent to create a solid part.
- Process: A print head jets a binder solution onto specific areas of the powder bed, adhering the powder particles together. Once a layer is complete, a new layer of powder is deposited, and the process repeats. Finally, the entire part is infiltrated with a bonding agent to create a solid structure.
- Advantages: Faster printing speeds and lower cost compared to SLM. Can handle larger build volumes.
- Disadvantages: Parts typically have lower density and mechanical strength compared to SLM. Limited surface finish and potential for part brittleness. May require additional post-processing for improved strength.
Powder Bed Fusion (PBF)
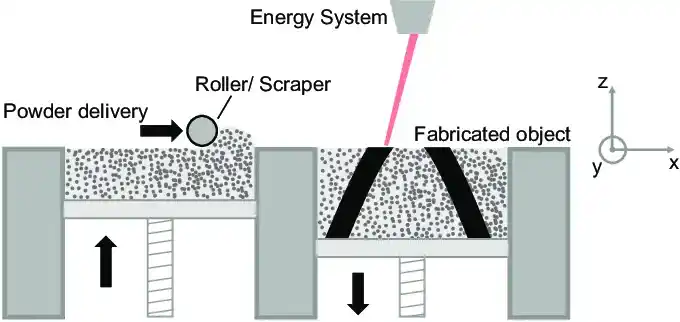
Source: researchgate.net
PBF is a broader category involving two main techniques:
- Laser-Based PBF: This refers to SLM, which utilizes a laser beam for melting the powder.
- Electron Beam Melting (EBM): A high-powered electron beam melts the metal powder, offering advantages for processing materials like titanium but generally less common for stainless steel compared to SLM.
Direct Energy Deposition (DED)
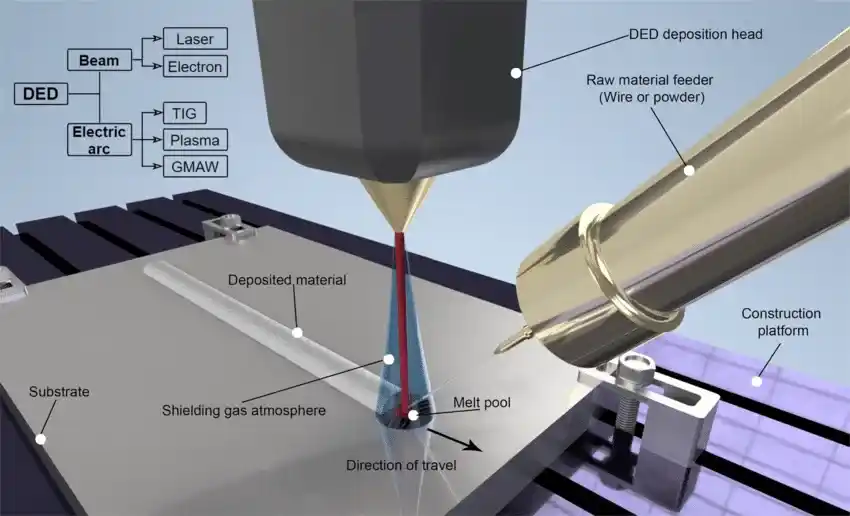
Source: additec3d.com
DED utilizes a concentrated energy source, typically a laser or electron beam, to melt metal feedstock (wire or powder) and deposit it layer by layer onto a substrate or base plate.
- Advantages: DED excels at creating large-scale metal parts and can be used for repairing existing components.
- Disadvantages: DED offers lower resolution and dimensional accuracy compared to PBF techniques. Surface finish can also be rougher, requiring more post-processing.
Comparison of Various Techniques
Feature | SLM | Binder Jetting | PBF (EBM) | DED |
---|---|---|---|---|
Process | Laser melts powder | Binder jets powder | Thermal energy melts powder (electron beam) | Melts wire/powder & deposits |
Speed | Slow | Fast | Moderate | Moderate to Fast |
Accuracy | High | Moderate | High | Moderate |
Surface Finish | Good | Rough | Good | Rough |
Cost | High | Moderate | High | Moderate |
Support Structures | May be required | Not required | Not required | Not typically required |
Applications | Complex parts, aerospace, medical | Simpler parts, prototypes | Thick parts, reactive metals | Large-scale parts, repairs |
Post-Processing of 3D Printing Stainless Steel
3D printed stainless steel parts often require some post-processing steps to achieve their final form and desired properties.
Heat Treatment
Heat treatment involves controlled heating and cooling cycles to modify the internal microstructure of the metal. This process helps to:
- Relieve residual stresses: The 3D printing process can introduce internal stresses within the part. Heat treatment helps to alleviate these stresses, improving the part’s dimensional stability and reducing the risk of cracking.
- Enhance mechanical properties: Heat treatment can optimize the strength, hardness, and ductility of the 3D printed stainless steel, tailoring it for specific applications.
Machining and Polishing
Machining techniques like CNC milling can be used to achieve tighter tolerances and improve the dimensional accuracy of the part.
Additionally, polishing methods can be employed to create a smooth and aesthetically pleasing surface finish, especially for parts requiring a high-quality appearance.
Surface Finishing Techniques
Several surface finishing techniques can be applied to 3D printed stainless steel depending on the desired outcome:
- Sandblasting: Creates a matte or textured finish, improving grip or enhancing the part’s cosmetic appeal.
- Vibratory finishing: Utilizes a tumbling media to smooth out the surface and remove any sharp edges.
- Chemical finishing: Certain chemicals can be used to passivate the surface, further enhancing the corrosion resistance of the stainless steel.
- Electroplating: A thin layer of another metal can be deposited on the surface for improved conductivity, wear resistance, or decorative purposes.
Applications 3D Printing Stainless Steel
Aerospace
Lightweight and Strong Components
The high strength-to-weight ratio of 3D printed stainless steel makes it ideal for aerospace components like lightweight brackets, structural elements in unmanned aerial vehicles (UAVs), and even rocket engine parts.
Complex Fuel System Components
3D printing allows for the creation of intricate fuel system components with internal channels and complex geometries, reducing weight and improving efficiency.
Automotive
Customizable and High-Performance Parts
3D printed stainless steel finds its way into custom intake manifolds, lightweight brake calipers, and even prototypes for new car parts. The ability to create complex geometries allows for optimized designs and improved performance.
Motorsports Components
Due to the need for strong and lightweight parts, 3D printed stainless steel is used in motorsports for suspension components, gear housings, and even custom heat exchangers.
Medical
Surgical Instruments and Implants
3D printed stainless steel can be used to create custom surgical instruments with improved ergonomics and functionality.
Additionally, it is biocompatible and can be used for certain types of medical implants, such as custom bone plates and prosthetics.
Medical Devices
The ability to create complex internal channels and intricate geometries makes 3D printing suitable for various medical devices, such as microfluidic components for diagnostics or heat sinks for medical lasers.
Consumer Goods
Jewelry and Design
The ability to create intricate and unique designs makes 3D printing stainless steel a valuable tool for jewelry designers and artists.
Durable Consumer Products
Components requiring strength and corrosion resistance, such as watch parts, high-end cutlery, and sporting goods, can be 3D printed in stainless steel.
Conclusion
3D printing stainless steel offers a versatile and powerful approach to metal manufacturing. With its ability to produce complex geometries and high-strength parts, this technology opens doors for innovative applications across various industries.
Make Your Design a Reality with Unionfab
Unionfab offers a vast array of 3D printing and post-processing services, allowing you to bring even the most intricate designs to life.
Whether you require high-precision prototypes, small-batch production runs, or functional parts, our team of experts can guide you through the process and ensure exceptional results.
Contact Unionfab today and experience the difference!