- Introduction
- SLS vs. MJF: Understanding the Core Differences
- SLS vs. MJF: Printing Process Comparison
- SLS vs. MJF: Material Options
- SLS vs. MJF: Part Quality
- SLS vs. MJF: Post-Processing Requirements
- SLS vs. MJF: Cost Comparison
- SLS vs. MJF: Applications
- Conclusion
- Experience Advanced 3D Printing Technology
Discover the differences between SLS and MJF alloys to learn their unique properties, applications, and performance in 3D printing.
Introduction
While both SLS and MJF utilize powder beds to create functional prototypes and end-use parts, their underlying techniques differ significantly.
This guide explores the core distinctions between these two 3D printing powerhouses, empowering you to make informed decisions for your next project.
SLS vs. MJF: Understanding the Core Differences
Both SLS (Selective Laser Sintering) and MJF (Multi Jet Fusion) are 3D printing techniques that use powder beds to create functional prototypes and end-use parts. However, they differ in how they fuse the powder material together, leading to distinct advantages and considerations for each method.
SLS vs. MJF: Printing Process Comparison
While both SLS and MJF utilize powder beds for 3D printing, the way they handle the powder and achieve fusion differs significantly.
SLS Printing Process
- Powder Preparation: A thin layer of thermoplastic powder (nylon, polyamide etc.) is evenly distributed across the build platform.
- Laser Scanning: A high-powered CO2 laser selectively scans the powder bed according to the digital blueprint. The laser melts the powder particles in designated areas, fusing them together to form the first layer of the 3D object.
- Lowering the Platform: The build platform lowers slightly, and a fresh layer of powder is deposited on top of the sintered layer.
- Repeating the Process: Steps 2 and 3 are repeated layer-by-layer until the entire 3D object is complete.
- Post-Processing: Once printing is finished, the build chamber cools down. The completed part is then removed from the surrounding unsintered powder. Support structures, if used, are removed manually or with a waterjet.
MJF Printing Process
- Powder Preparation: Similar to SLS, a thin layer of thermoplastic powder (primarily nylon) is spread across the build platform.
- Fusing Agent Deposition: Inkjet-like printheads jet a fusing agent onto specific areas of the powder bed, corresponding to the required geometry of the 3D object.
- Infrared Heating: An infrared energy source sweeps across the powder bed, selectively melting the powder particles where the fusing agent is present. This bonding creates the first layer of the object.
- Lowering the Platform: The platform lowers, and a new layer of powder is deposited.
- Repeating the Process: Steps 2 and 4 are repeated layer-by-layer until the entire object is built.
- Post-Processing: The build chamber cools down, and the completed part is extracted from the surrounding unsintered powder. Support structures, if needed, are removed.
SLS vs. MJF: Comparision of Printing Process
Feature | SLS | MJF |
---|---|---|
Fusing Mechanism | Laser melting | Fusing agent and infrared heat |
Material Options | Wider range (nylon, polyamide, some metals) | Primarily nylon powders |
Layer Fusion | Complete melting of powder particles | Bonding through fusing agent and heat |
Surface Finish | Generally rougher | Generally smoother |
Printing Speed | Slower | Potentially faster |
SLS vs. MJF: Material Options
While both SLS and MJF utilize powdered materials for 3D printing, a key difference lies in their material options.
Similarities:
- Primary Material: Both processes primarily use nylon, specifically nylon 12 (PA 12). This versatile material offers good strength, flexibility, and heat resistance.
- Nylon Variations: Both SLS and MJF offer variations of nylon, including glass-filled nylon (PA 12 GF) for enhanced strength and stiffness.
Differences:
SLS has a wider range of material options compared to MJF. Here’s what SLS offers that MJF typically doesn’t:
- Metal-filled Nylons: These include carbon-filled PA for improved conductivity or aluminum-filled PA (alumide) for a lighter weight with a metallic look.
- Flexible Materials: SLS can handle some flexible materials like TPU, which is beneficial for applications requiring some give.
SLS vs. MJF: Part Quality
The quality of a 3D printed part includes various aspects: dimensional accuracy, surface finish, mechanical properties, and overall consistency.
Part Quality Achieved by SLS
- Dimensional Accuracy: SLS offers high dimensional accuracy due to the precise laser control. Parts closely match the digital design with minimal deviations.
- Surface Finish: SLS parts typically have a rougher surface texture directly related to the size and shape of the powder particles used. This might require additional finishing techniques for a smoother aesthetic.
- Mechanical Properties: SLS parts are known for their strength, durability, and heat resistance. The complete melting of powder particles creates strong inter-particle bonds, making them suitable for functional applications.
- Consistency: SLS offers good overall consistency in part quality due to the controlled laser melting process. Material properties tend to be consistent throughout the part.
Part Quality Achieved by MJF
- Dimensional Accuracy: MJF also delivers good dimensional accuracy. However, due to the use of a fusing agent and heat, there might be a slightly higher chance of dimensional deviations compared to SLS.
- Surface Finish: MJF parts generally boast a smoother surface finish right out of the printer. The fusing agent can fill in gaps between particles, reducing the grainy texture associated with SLS parts.
- Mechanical Properties: While still good for many applications, MJF parts might have slightly lower overall strength compared to SLS. The bonding process using a fusing agent might not be as strong as complete material melting in SLS.
- Consistency: MJF parts generally exhibit good consistency. However, there’s a possibility of slight variations in material properties depending on the distribution of the fusing agent within the powder bed.
SLS vs. MJF: Comparision of Part Quality
Feature | SLS | MJF |
---|---|---|
Dimensional Accuracy | High | Good (might have slight variations) |
Mechanical Strength | Strong and durable | Strong, but potentially less than SLS |
Surface Finish | Rougher texture (requires post-processing) | Smoother texture |
SLS vs. MJF: Post-Processing Requirements
While both SLS and MJF produce 3D printed parts directly from a powder bed, they might require some post-processing steps to achieve the desired final quality.
Post-Processing Steps Required for SLS Parts
- Cooling: The build chamber needs to cool down slowly to prevent warping or cracking of the parts due to thermal stress.
- Part Removal: The completed part is excavated from the surrounding unsintered powder. Depending on the complexity, this might involve manual removal or using compressed air.
- Support Structure Removal: SLS parts often require support structures for overhanging features. These supports are typically removed manually with tools or with a waterjet cutting system. Waterjetting requires additional equipment and expertise.
- Bead Blasting: This optional step involves blasting the part with tiny glass or ceramic beads to achieve a smoother surface texture.
- Dyeing: SLS parts are typically white or off-white. Dyeing can be used to achieve a desired color for aesthetic purposes.
- Machining or Finishing: Additional machining or finishing techniques like sanding or polishing might be necessary to achieve precise dimensions or a desired surface finish.
Post-Processing Steps Required for MJF Parts
- Cooling: Similar to SLS, the build chamber needs to cool down gradually to minimize the risk of warping.
- Part Removal: The completed part is removed from the surrounding unsintered powder. Due to the potentially weaker bonds between particles in MJF, this might be easier compared to SLS.
- Support Structure Removal: Support structures, if used, can often be removed manually with less force compared to SLS parts because of the potentially weaker bonds.
- Bead Blasting (Optional): Bead blasting can be used for MJF parts as well, but due to the potentially smoother surface finish achieved with the fusing agent, it might not always be necessary.
- Dyeing: Similar to SLS, dyeing can be used to add color to MJF parts.
SLS vs. MJF: Comparision of Post-Processing
Feature | SLS | MJF |
---|---|---|
Cooling | Required | Required |
Part Removal | Can be challenging, might require compressed air | Potentially easier due to weaker particle bonds |
Support Structure Removal | Requires tools or waterjetting | Often easier to remove manually |
Bead Blasting | Optional, but common for smoother finish | Optional, might not be necessary for some parts |
Dyeing | Possible | Possible |
Machining/Finishing | Might be necessary for precise dimensions | Might be necessary for precise dimensions |
SLS vs. MJF: Cost Comparison
The cost of 3D printing a part using SLS or MJF depends on several factors, including part complexity,part volume,material selection and post-processing needs.
Cost Considerations for SLS Technology
- Machine and Material Costs: SLS machines tend to be more expensive. Nylon is a common SLS material, but specialty materials like metals can significantly increase the cost.
- Printing Speed: SLS printing is generally slower, leading to potentially higher costs per unit time.
- Post-Processing: Removing support structures with waterjetting can be expensive and require additional expertise. Bead blasting or other finishing techniques add to the cost.
Cost Considerations for MJF Technology
- Machine Cost: MJF machines might have a lower initial investment compared to SLS.
- Printing Speed: MJF printing can be potentially faster, leading to lower costs per hour of printing time for single parts.
- Material Usage: Similar to SLS, unsintered powder can be potentially recovered and reused to some extent.
- Post-Processing: Support removal for MJF parts can often be done manually, reducing costs associated with waterjetting.
SLS vs. MJF: Comparision of Cost
Feature | SLS | MJF |
---|---|---|
Machine Cost | Higher | Lower |
Material Cost | Can vary depending on material selection | Primarily uses nylon, might be lower |
Printing Speed | Slower | Potentially faster |
Material Usage | Can be partially recovered and reused | Can be partially recovered and reused |
Post-Processing Cost | Potentially higher due to waterjetting | Potentially lower due to simpler removal methods |
SLS vs. MJF: Applications
The choice between SLS and MJF depends on the desired outcome of your project.
Applications Suitable for SLS
- Functional Prototypes: Due to their high strength and durability, SLS parts are ideal for prototypes undergoing rigorous testing or requiring functional performance under stress.
- End-Use Parts: SLS excels in creating robust end-use parts for various industries like aerospace, automotive, and medical. Examples include gears, brackets, and housings.
- Applications Requiring High Heat Resistance: SLS parts can withstand high temperatures, making them suitable for applications like jigs and fixtures used in manufacturing processes.
- Wide Material Selection: SLS offers a wider range of materials beyond nylon, including some metals. This allows for creating parts with specific properties like biocompatibility or electrical conductivity.
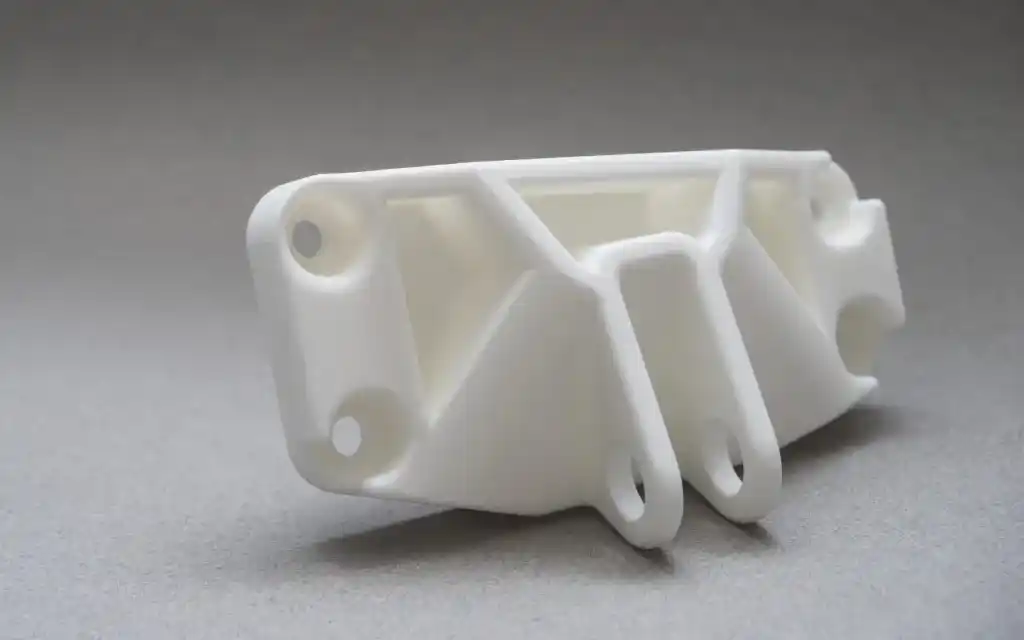
Source: protolabs.com
Applications Suitable for MJF
- Visual Prototypes: MJF parts generally have a smoother surface finish, making them ideal for creating visually appealing prototypes for design validation or presentations.
- Low-Volume Production Runs: MJF can be cost-effective for producing small batches of end-use parts, especially for simpler geometries.
- Applications Prioritizing Aesthetics: The smoother finish and potential for dyeing make MJF suitable for applications where appearance matters, like consumer goods or wearables.
- Rapid Prototyping: Due to potentially faster printing speeds, MJF can be a good choice for quickly iterating on prototypes during the design process.
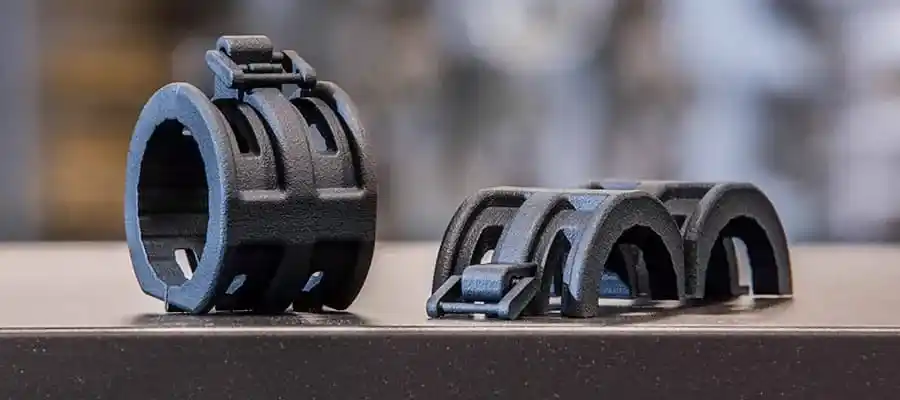
Source: hubs.com
Conclusion
Both SLS and MJF are powerful 3D printing technologies with distinct advantages. SLS excels in functionality with its durable parts and wider material range, ideal for prototypes and end-use parts.
MJF offers a smoother finish, potentially faster printing, and simpler post-processing, making it a good fit for visual prototypes and low-volume production runs.
Experience Advanced 3D Printing Technology
In addition to SLS and MJF, Unionfab offers other 3D Printing Services, including SLA, FDM, SLM, PolyJet and Large Scale Printing. With advanced technology and quality services, Unionfab help make your project perfect!
