- Introduction
- 3D Printing: the Versatility of Additive Manufacturing
- CNC Machining: Unleashing Precision
- Vacuum Casting: Elevating Net-Shape Prototyping
- Cost and Efficiency Comparisons
- Materials comparisons
- Precision, Surface Finish, Strength and Toughness
- Product size limitations
- 3D printing vs CNC vs Vacuum Casting: the Conclusion
- Unionfab’s Manufacturing Expertise
This article will compare and contrast three common manufacturing techniques: 3D printing, CNC machining, and vacuum casting.
Introduction
3D printing, CNC machining, and vacuum casting have all emerged as viable production options, but each has distinct material capabilities and suitability for different volume needs.
For companies developing prototypes or producing goods, the choice of manufacturing technology is crucial. Selecting the right method can mean the difference between an on-time project and missed deadlines, or a costs that meets versus exceeds budgets. As manufacturing requirements become more advanced, it is imperative that professionals understand the strengths and limitations of these technologies.
This guide provides an in-depth comparison of 3D printing, CNC, and vacuum casting from an industrial perspective. We’ll discuss factors like production volumes, material options, workflows, tolerances, surface finishes, and of course costs. By reading this article, manufacturing and product development professionals will be equipped to evaluate which process best fulfills their specific technical and budgetary requirements.
3D Printing: the Versatility of Additive Manufacturing
3D Printing Process: How it Works
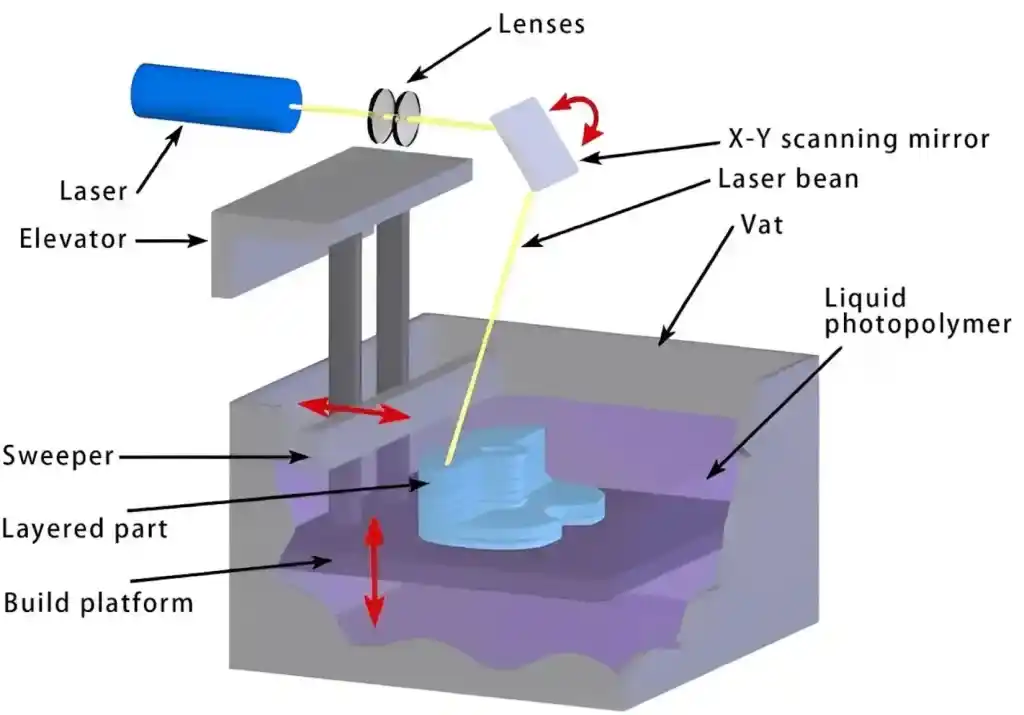
3D printing (also known as additive manufacturing or AM) involves building three-dimensional objects from a digital file through successive layers of material.
The general 3D printing process works by first designing a virtual 3D model using computer-aided design (CAD) software. This 3D model is then sliced into thin cross-sectional layers and sent to the 3D printer. During printing, materials such as plastic, metal, ceramic, or other materials are selectively deposited one layer at a time until the final object is completed.
Main 3D Printing Technologies: SLA, SLS and SLM
The main technologies used include Stereolithography (SLA), Selective Laser Sintering (SLS), and Selective Laser Melting (SLM). SLA provide high resolution while SLS and SLM can process industrial-grade materials suitable for end-use manufacturing applications.
If you want to learn more, this article provides a detailed comparison of SLA, SLS and SLM.
3D Printing Materials
Common materials used in 3D printing include plastics like ABS and PLA, metals including stainless steel and titanium. Powder-based systems like SLS and SLM can 3D print using nylon, plastic and polymer powders as well as metal and ceramic powders.
Typical Applications of 3D Printing
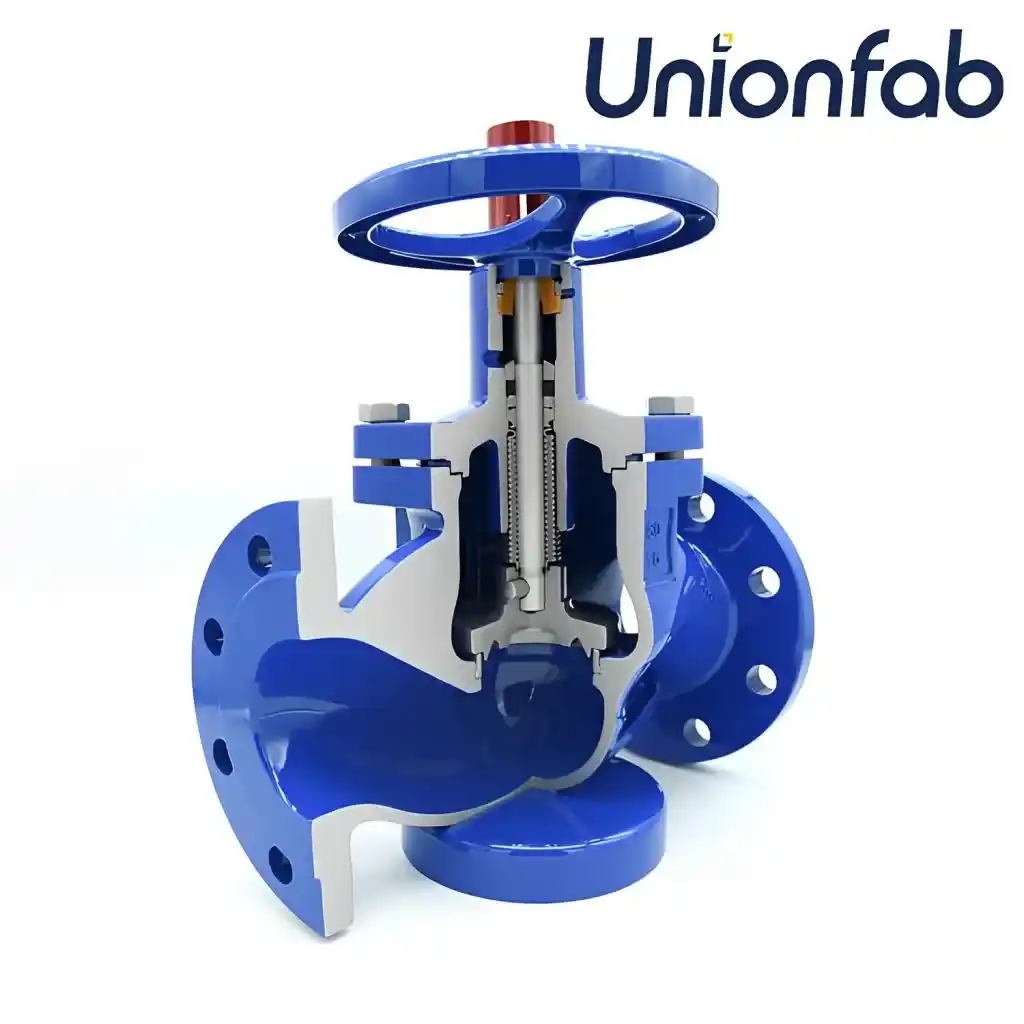
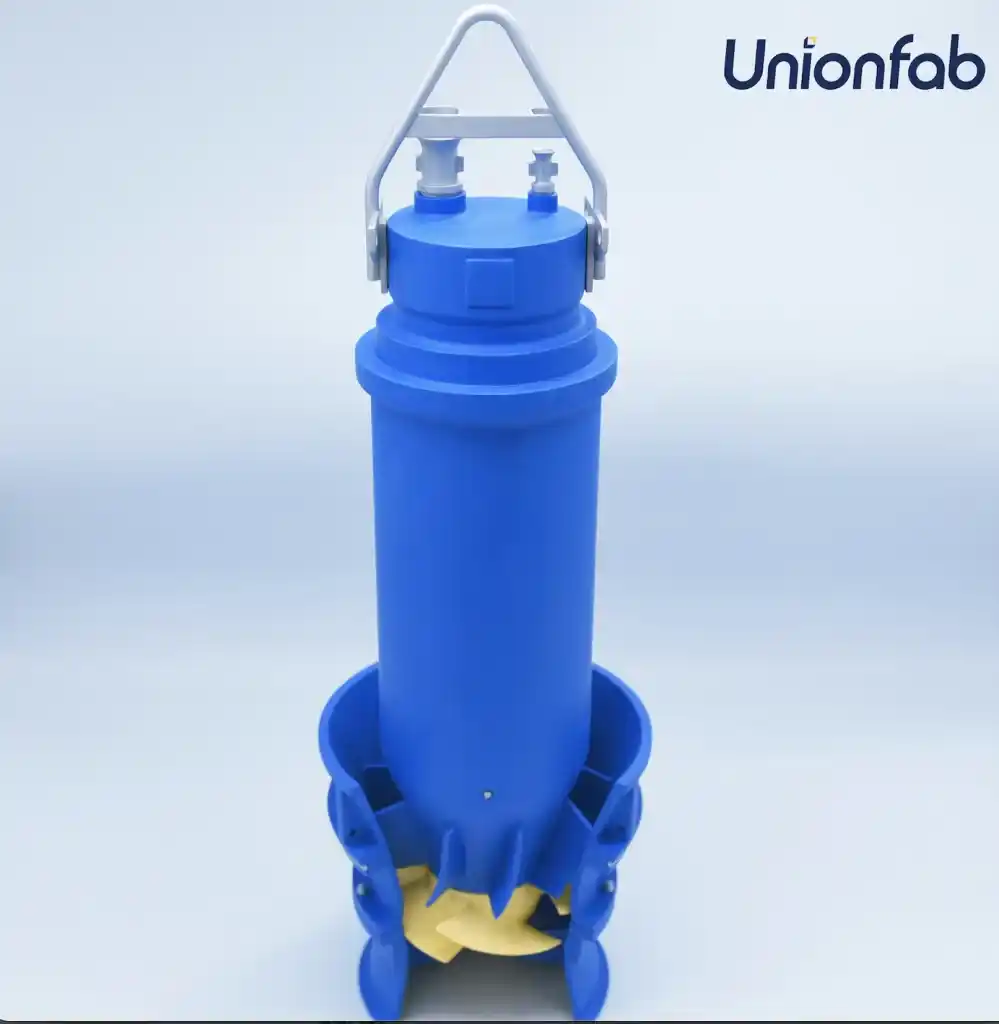
Areas where 3D printing truly excels include low-volume production of customized components, rapid prototyping to validate part functionality, creating intricate internal structures or geometries otherwise not possible, and producing specific parts for applications like medical implants or bespoke automotive components. Overall, 3D printing technology enables new frontiers in customized, on-demand manufacturing.
CNC Machining: Unleashing Precision
CNC Machining: A Brief Introduction
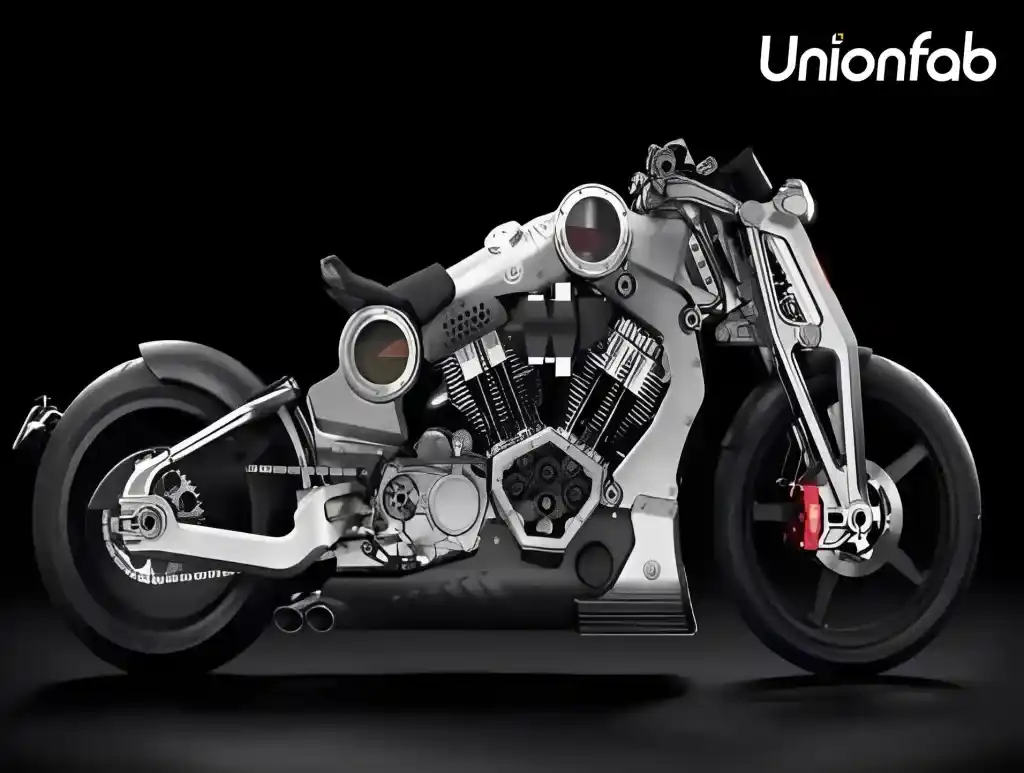
CNC (Computer Numerical Control) machining has its origins in the 1950s and has since transformed manufacturing through automation and precision. CNC involves programming and operating computer-controlled machine tools like mills, lathes and routers to produce parts by removing material.
In the CNC machining process, a programming software converts 3D CAD models into G-code instructions that precisely control axes and motions of cutting tools. CNC machines can carry out milling, turning, drilling and other subtractive operations on solid blocks or plates of material. Read this article to know the differences between CNC milling and turning.
Materials that are well-suited for CNC machining include metals such as aluminum, steel and titanium as well as plastics, wood and composites.
Advantages and Disadvantages of CNC Machining
Key advantages are high precision and surface finishes for demanding tolerances. Tight tolerances down to the micron level can be achieved through CNC. Mass production of intricate parts is feasible through automated CNC systems. However, setup times can be lengthy and material waste is inherent in subtractive processes.
Typical Applications of CNC Machining
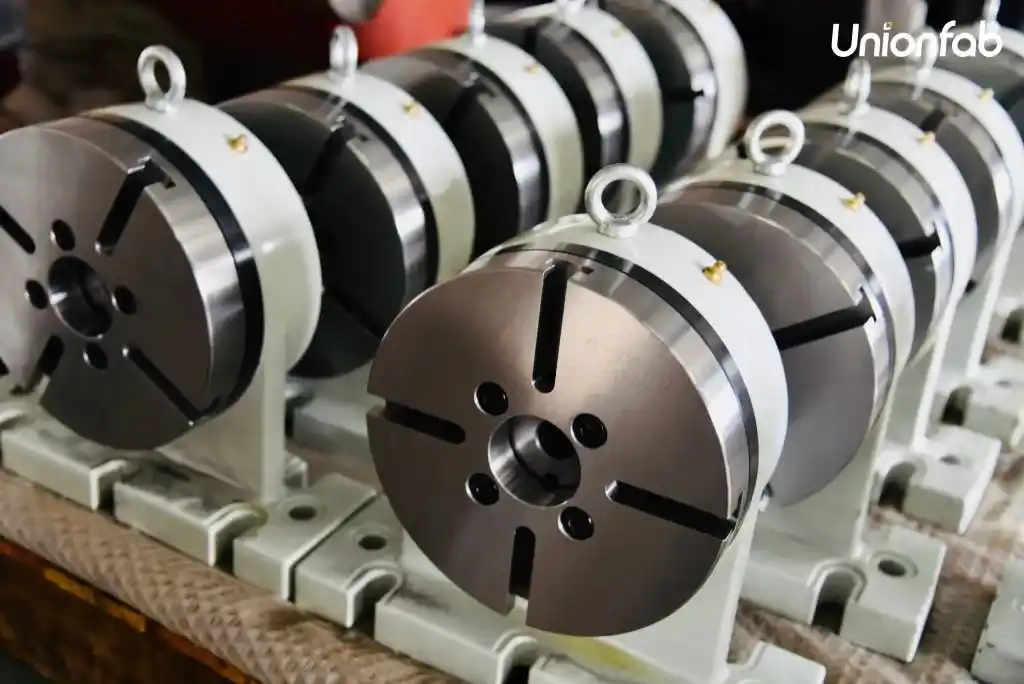
sectors that extensively use CNC machining are:
- Die/mold making – CNC milling machines and CNC wire EDM (electronical discharge machines) create molds and dies with tightly controlled features for plastic injection and other processes.
- Electronics – Tight-tolerance backplane/housing fixtures, test sockets, precision parts for small mechanical components, and enclosures are machined with CNC.
- Energy – Critical parts used in oil/gas drilling and wind/solar installations require the precise sealing surfaces and tight tolerances of CNC production. Also prototypes for structural testing before mass production.
- Automotive – CNC create low-volume body molds for specialty vehicles, prototypes. High-precision transmission/suspension parts in hardened alloys like chromium-molybdenum are also made with CNC machining, plus jigs, fixtures for component testing/validation.
Vacuum Casting: Elevating Net-Shape Prototyping
Vacuum Casting: a Brief Introduction
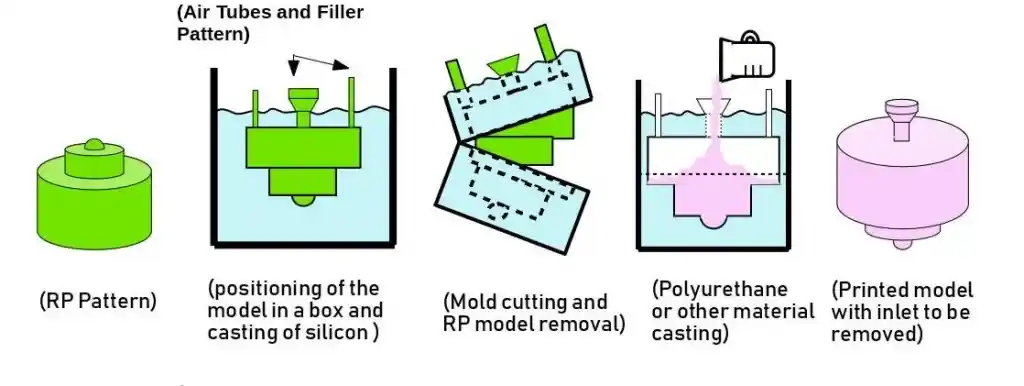
Vacuum casting involves injecting liquid materials into a precisely-crafted mold cavity under vacuum pressure assistance. This allows for complex geometries to be replicated in high resolution with minimal unwanted voids or pitting in the final parts. Read this article to learn more about this technique.
In the vacuum casting process, a master pattern or 3D printed prototype is used to create a multi-piece mold from materials like metals or silicone rubbers. Liquid polymers, resins or even metals are then injected and drawn deep into the mold thanks to the vacuum environment removing air pockets. Setting and curing ensues before demolding finished net-shaped castings.
Vacuum Casting Materials
Common materials amenable to vacuum casting include epoxy, polyurethane resins, and silicones.
Pros and Cons of Vacuum Casting
Advantages
- Vacuum casting can produce accurate and detailed casting replications of intricate master models/molds, capturing subtle surface textures and complex geometries well.
- Achieves smooth, void-free surfaces thanks to vacuum assistance drawing out air.
- Produces net or near-net shapes requiring little post-processing machining or finishing.
Disadvantages
- High setup costs for molds that are only offset by multiple castings. This makes it less economical for very low (<= 5 parts) production volumes.
- Material options are limited to those suitable for vacuum forming techniques like thermosets.
- Molds degrade with use and must be replaced (typically after 15 – 50 casts), adding recurring costs versus reuse of injection molds for example.
- Not as dimensionally precise as CNC milling or other high-tolerance techniques. The dimensional accuracy achievable through vacuum casting is dependent on the accuracy and surface finish of the master mold used. In general, the dimensional tolerance of vacuum cast parts will be within ±0.2mm of the original master mold dimensions.
typical applications of vacuum casting
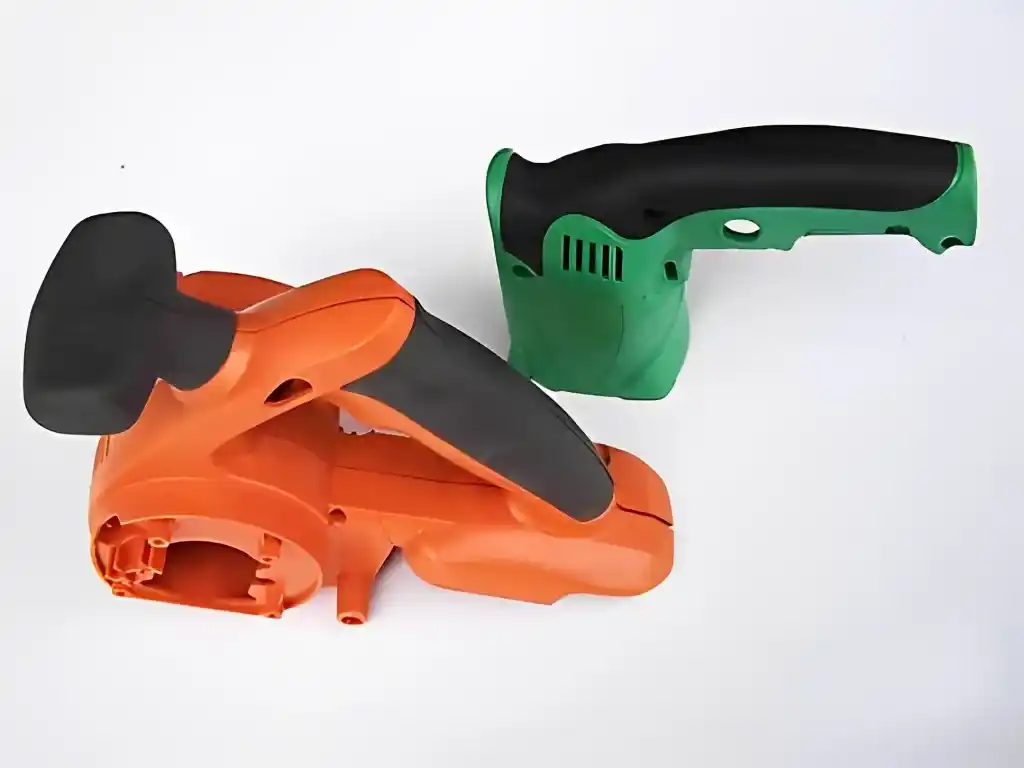
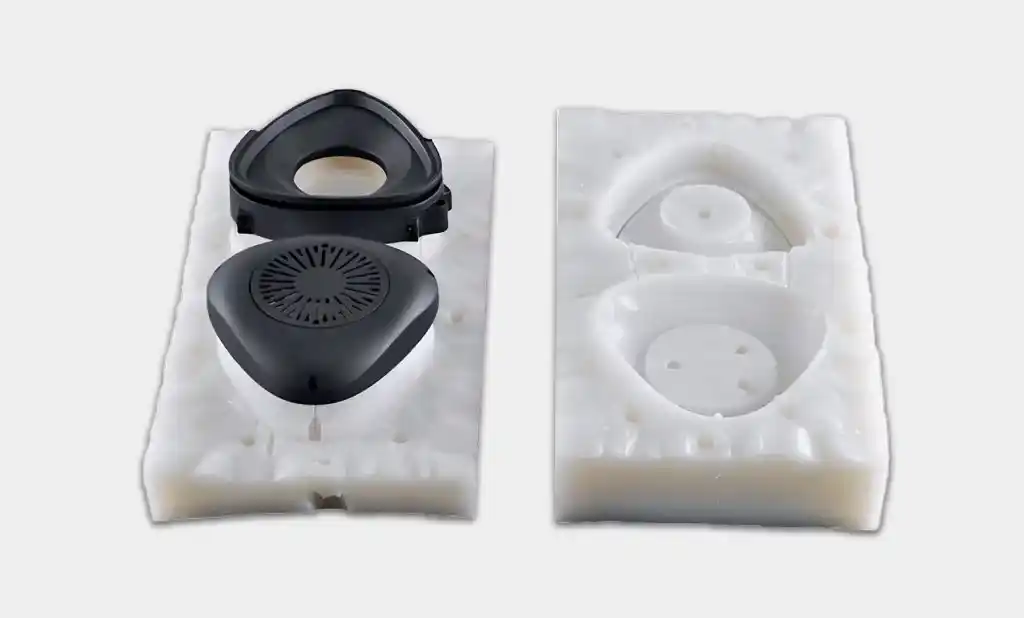
The combination of smooth finishes, low order quantity requirement, and material properties close to injection molding materials make vacuum casting a first choice in many creative and low-volume application areas:
- Prototyping and Product Development – Vacuum casting is commonly used for rapid prototyping to create functional prototypes that closely mimic the final product’s appearance and performance. This is especially valuable in product development and design validation.
- Consumer Electronics – Vacuum casting is employed to create casings, bezels, and custom electronic components, especially for low to medium volume production of niche electronic devices.
- Automotive – In the automotive sector, vacuum casting is used to produce concept car models, customized automotive parts, and interior components for design testing.
Factors Influencing Vacuum Casting
Several factors can influence the precision and quality consistency of vacuum cast parts:
- Mold/Pattern Quality: Imperfections get duplicated, degrading over time, affecting tolerances.
- Mold degradation – Over time and with repeated use (about 15~50 casts), molds may slowly deteriorate or warp, resulting in slightly less accurate replications.
- Vacuum Leaks: Incomplete evacuation leads to air pockets reducing fidelity and strength.
- Thermal Effects: Curing shrinkage/warping varies by materials and temperature control methods.
- Material Properties: Viscosity changes during pouring/curing can induce variances batch to batch.
- Curing Processes: Precise timing, environmental monitoring required to reliably replicate curing cycles.
Cost and Efficiency Comparisons
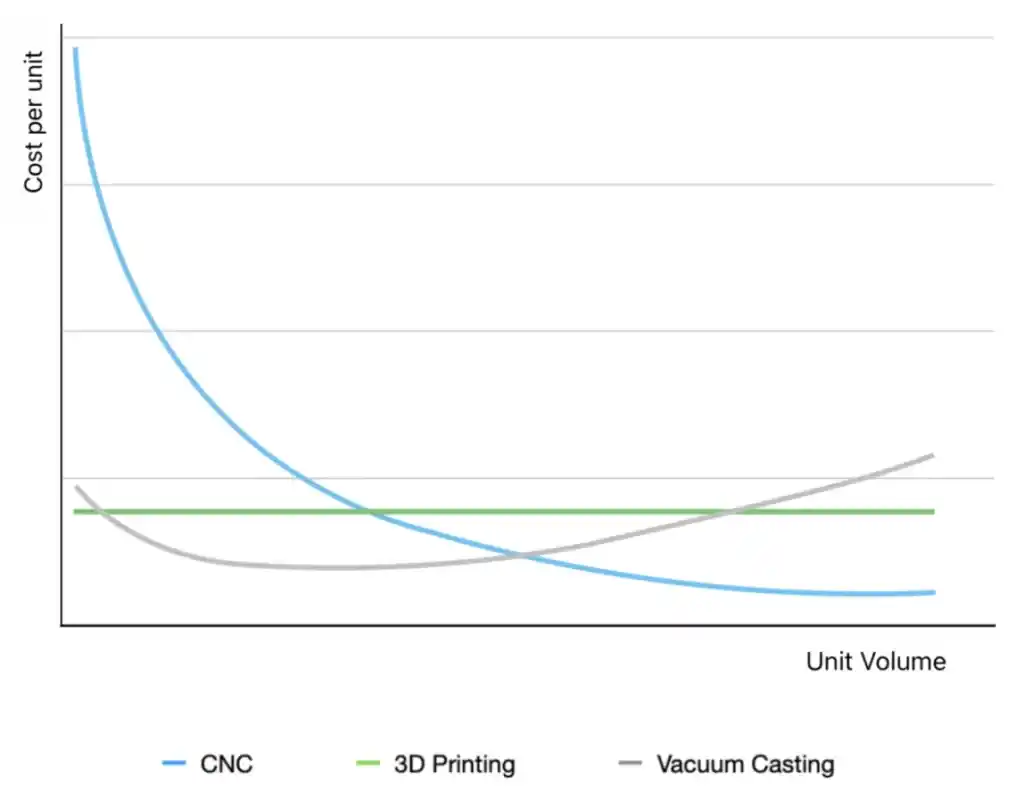
Very Low Volume Production: 5-100 parts
(Note: For quantities of fewer than 5 parts, 3D printing excels in both cost-effectiveness and efficiency.)
Most cost-effective choice: Vacuum Casting
Vacuum Casting
Once the master mold is created, vacuum casting can be cost-effective for very low volume production because it allows you to create multiple copies from a single mold. The setup cost for creating molds can make it less efficient for extremely low quantities.
3D Printing
3D printing is generally efficient for very low volume production as it doesn’t require tooling or molds. However, it can be relatively more expensive per part compared to other methods.
CNC Machining
CNC machining can be expensive and less efficient for very low volume production due to setup costs and machining time for each part.
Low Volume Production: 100-500 parts
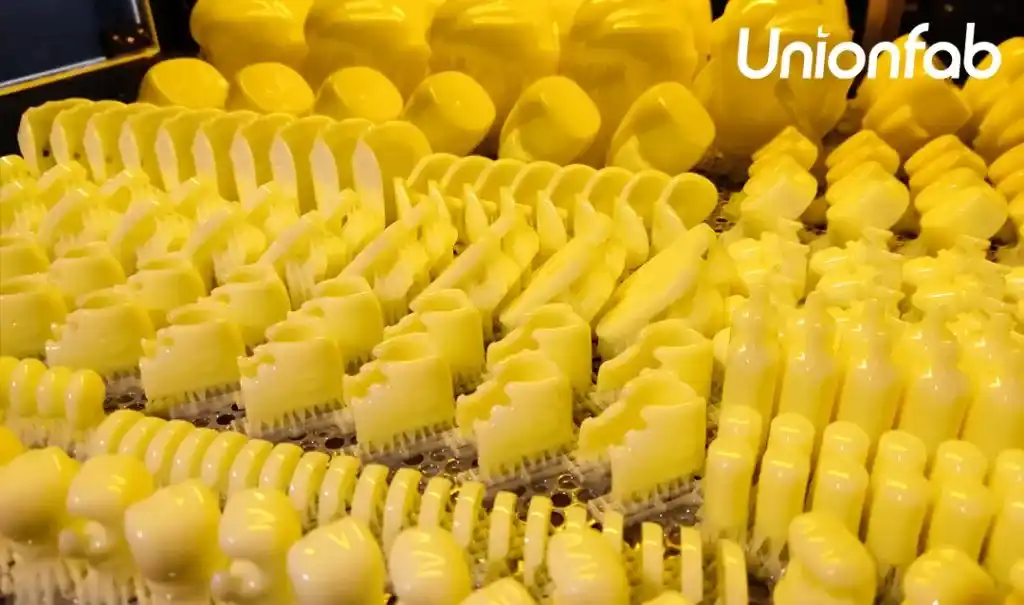
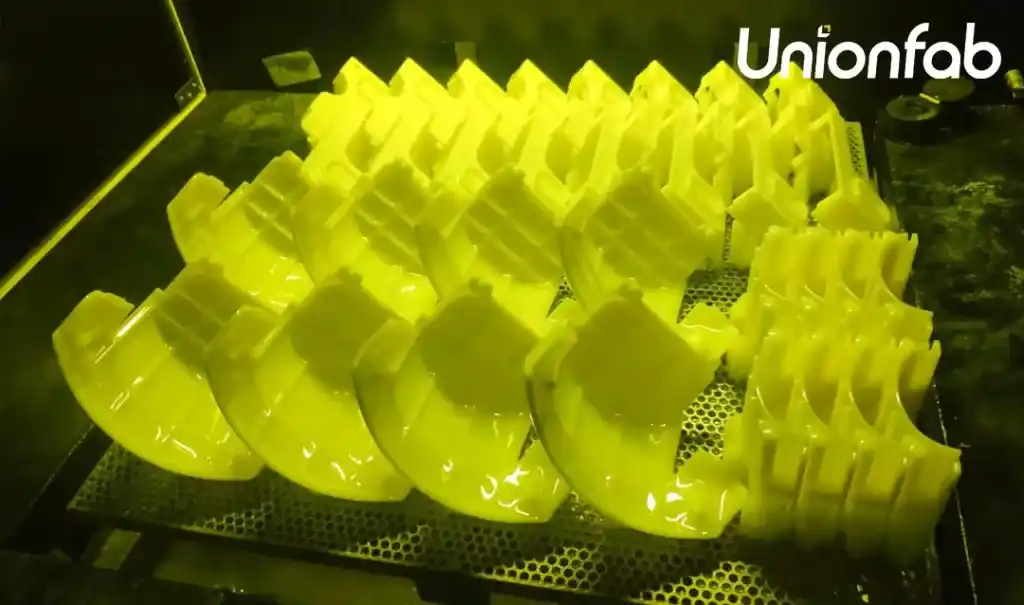
Most cost-effective choice: 3D Printing/CNC Machining
Vacuum Casting
Vacuum casting may become less cost-effective and less efficient for high volume production due to the time and cost involved in making multiple molds (each for 15~50 casts).
3D Printing
3D printing is still suitable for low volume production.
CNC Machining
CNC machining becomes more cost-effective on a per-unit basis as volume increases but may still have higher upfront costs.
Low to Medium Volume Production: 500 – 1,000 parts
Most cost-effective choice: Injection Molding/CNC Machining/3D Printing
Vacuum Casting
Volume beyond 500 is not suitable for vacuum casting.
Injection Molding
Injection molding is often the most cost-effective choice for producing parts in this volume range. The initial tooling or mold setup costs can be relatively high but are spread across the entire production run, making it economical for larger quantities.
CNC Machining
CNC machining becomes a valuable choice when the part’s design, complexity, or tight tolerances cannot be adequately met by injection molding.
3D Printing
In many cases, 3D printing can be cost-effective for low to medium volume production, especially when considering design flexibility, quick turnaround times, and minimal tooling costs. When the design geometries or materials needed for the part cannot be satisfied by CNC machining, 3D printing becomes a viable alternative.
Medium to High Volume Production: 1,000 – 10,000 + parts
Most cost-effective choice: Injection Molding/CNC Machining
Injection Molding
Injection molding remains the most cost-effective and widely used choice for medium to high volume production. It’s optimized for mass production because it can efficiently produce large quantities of identical parts from a single mold or tool.
CNC Machining
CNC machining can be highly cost-effective and efficient for high volume production, especially when producing a large quantity of identical parts requiring precision.
Materials comparisons
CNC Machining
- Metals (steel, aluminum, titanium alloys, etc.)
- Plastics/composites (fiberglass, carbon fiber, etc.)
- Wood, stone, foam for non-metallics
3D Printing
- Plastics like PLA (biodegradable), ABS (strong and durable), PETG (flexible), and nylon (high strength)
- Photopolymer resins for SLA/DLP
- Metals powders like stainless steel, aluminum, titanium, etc.
- Composites like carbon fiber with MJF (multi-jet fusion)
Vacuum Casting
- Thermoset & thermoplastic resins (epoxy, polyurethane, acrylic, etc.)
In conclusion, CNC machining offers a broad material selection, predominantly working with rigid, machinable materials like metals/composites but also soft materials. 3D printing is versatile with plastics, metal powders, ceramics, and composites, with ongoing material innovation. Vacuum casting primarily uses thermosets.
Precision, Surface Finish, Strength and Toughness
Precision Comparisons
CNC machining offers higher precision than vacuum casting and other formative/net-shape processes which rely more on the accuracy of molds/tooling and controlling material deformation. Dimensions can vary more with these techniques.
Additive methods like 3D printing have improved but many still lag CNC in obtainable tolerances and surface finish quality, especially for demanding applications.
Surface Finish Comparisons
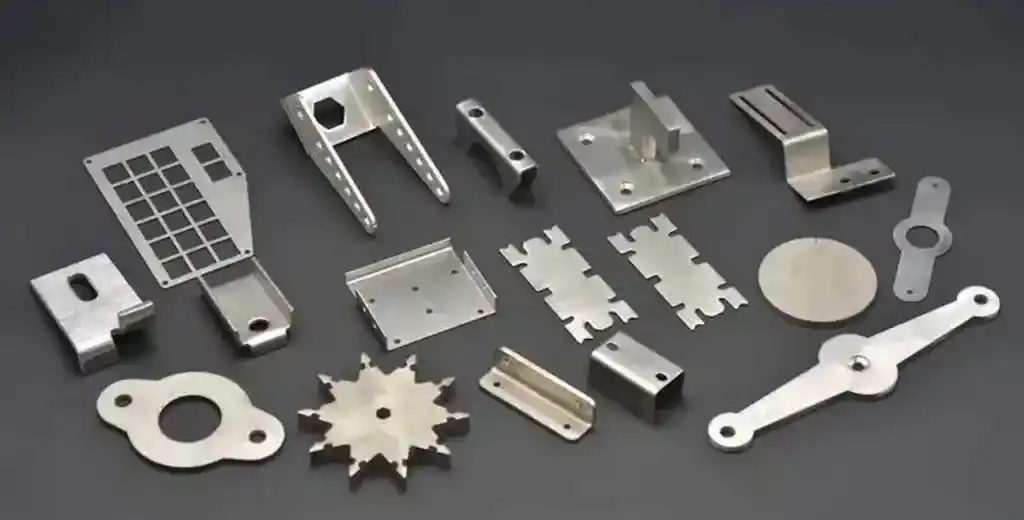
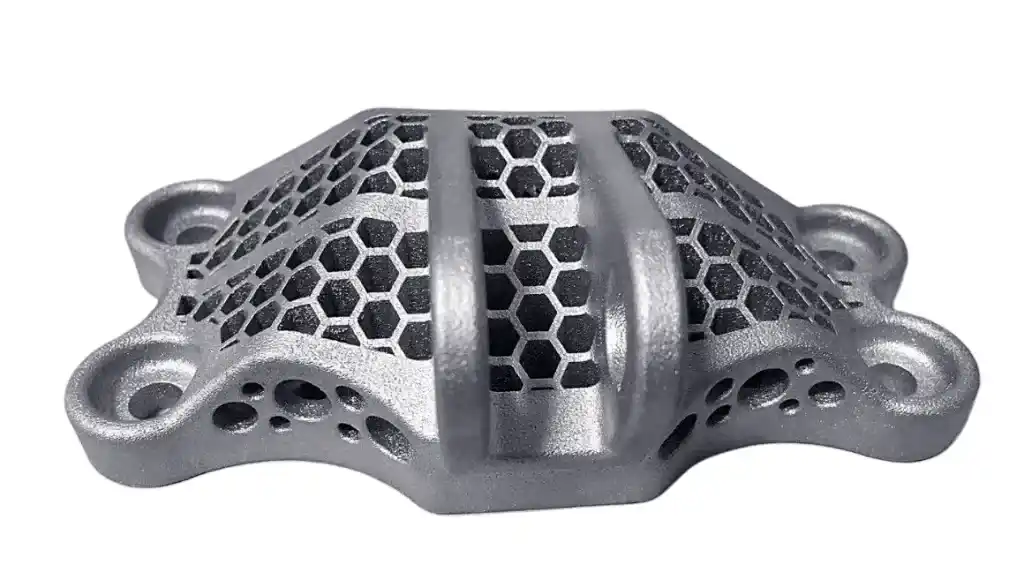
CNC machining produces a part with an “as-machined” or “as-milled” finish (surface roughness of 125 μin) as soon as the manufacturing process is completed.
In contrast, 3D printing techniques rely on discrete layers that leave visible step patterns even with SLA’s fine resolution.
Vacuum casting can match or come very close to CNC-level surfaces in many applications thanks to its tight mold tolerances and vacuum encapsulation process. It produce net-shaping parts with minimal or no additional machining or post-processing requirement.
However, porosity or mold imperfections in the vacuum casting process could potentially lead to rougher regions on some vacuum cast parts where CNC excels in maintaining consistent finishes.
Strength and Toughness Comparisons
CNC parts have higher density and are closer to the theoretical density of the substrate material.
Vacuum casting
- When casting metals like aluminum or zinc alloys, strengths can be on par with CNC materials if densities from the casting process are high without voids. However, porosity defects weaken parts more significantly than possible with CNC cutting a dense billet.
- Thermoset polymers like epoxies and polyurethanes cast in molds have heat deflection temperatures often below 150°C/300°F. Meanwhile, many engineering-grade CNC plastics like PEEK, nylon, and composites can withstand temperatures over 150°C during machining and post-machining heat treatments, increasing durability of CNC made plastic parts.
3D printing
- 3D printed parts can contain voids between deposited layers. Layered microstructures in 3D printed parts introduce areas of weakness between strata that do not exist in homogenous CNC machined structures.
- Metal 3D printing techniques like SLM can match densities and strengths of milled metals if parameters are optimized. But reproducibility between parts/machines is greater for CNC. Specialty composites 3D printed by SLS/SLM may see anisotropic reinforcement from grain/fiber orientations versus isotropic CNC structures.
- Thermoplastics 3D printed by FDM/FFF exhibit lower elongation, impact resistance and fatigue life compared to CNC machinable plastic stock.
Product size limitations
Vacuum Casting
Can produce parts ranging from a few centimeters up to a meter or more depending on mold/chamber size. Larger parts may require assembly.
3D Printing
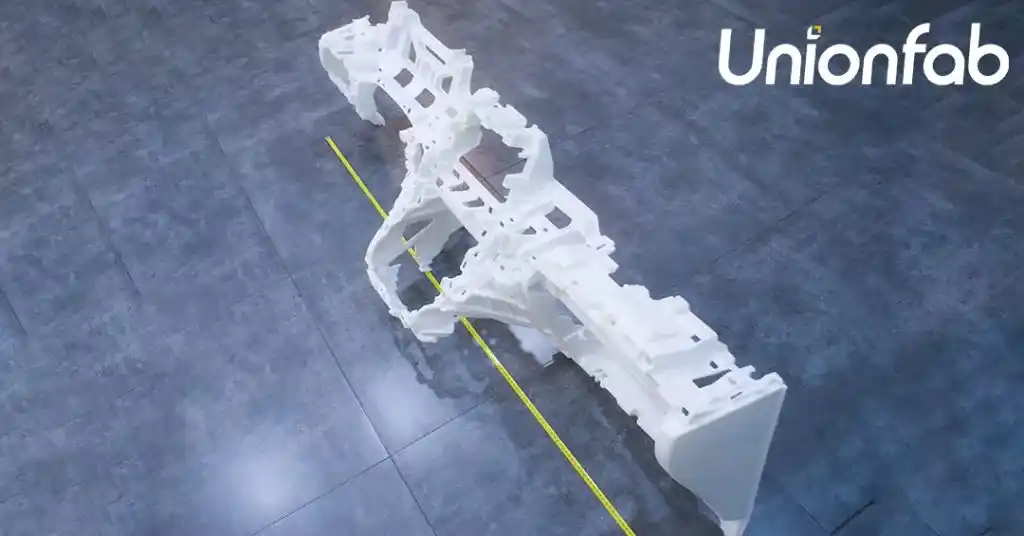
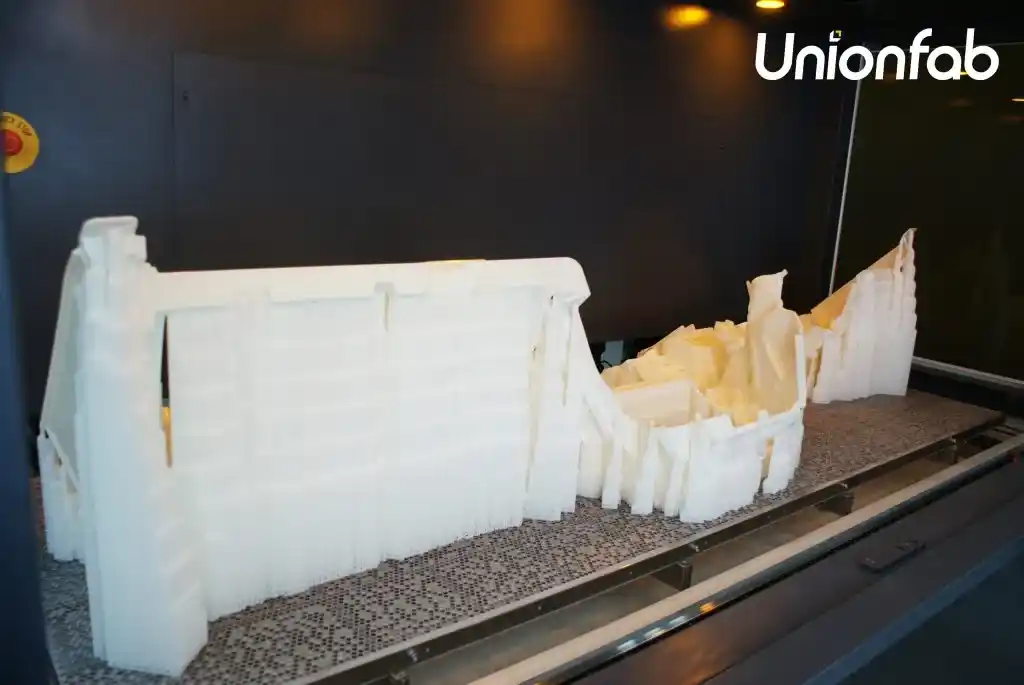
Large industrial 3D printers can achieve maximum individual build volumes approaching 1-2 cubic meters. However, due to their size and slower print speeds, they typically print these largest parts using divide-and-conquer techniques like multi-part builds or multi-chamber simultaneous printing of smaller sections.
Unionfab now support large size SLA printing up to 2100700800 mm.
CNC Machining
Limited mainly by travel of largest machine axis, with gantry mills covering areas of several square meters. Routers/lathes can produce very large or extremely long parts.
3D printing vs CNC vs Vacuum Casting: the Conclusion
Vacuum Casting
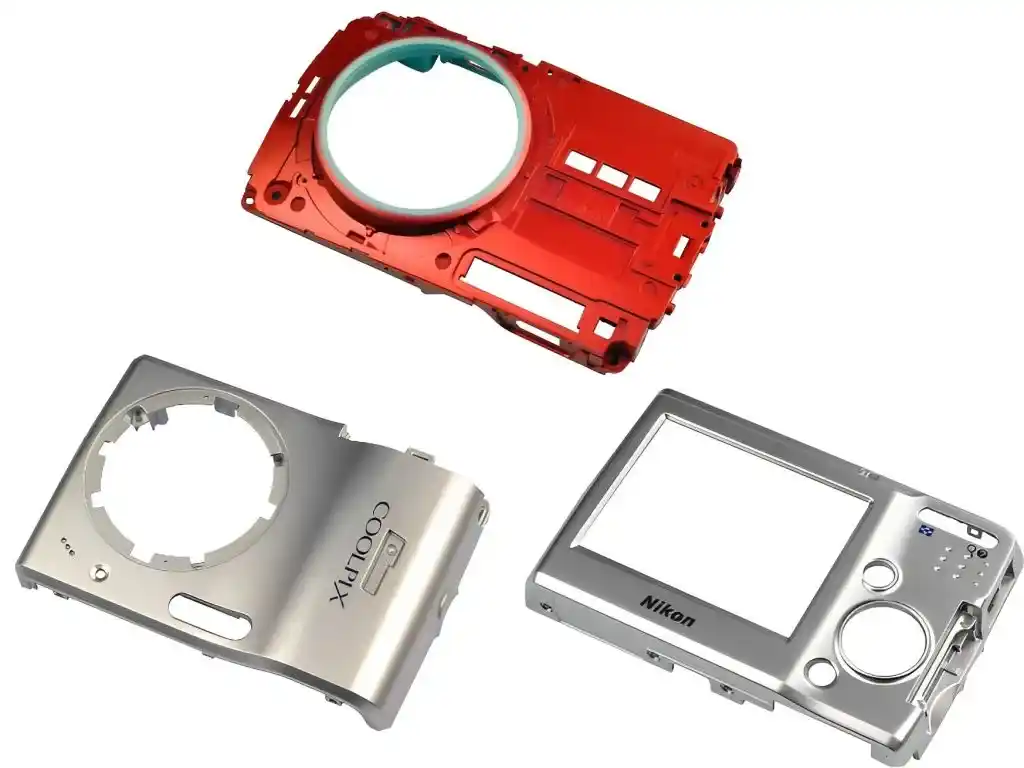
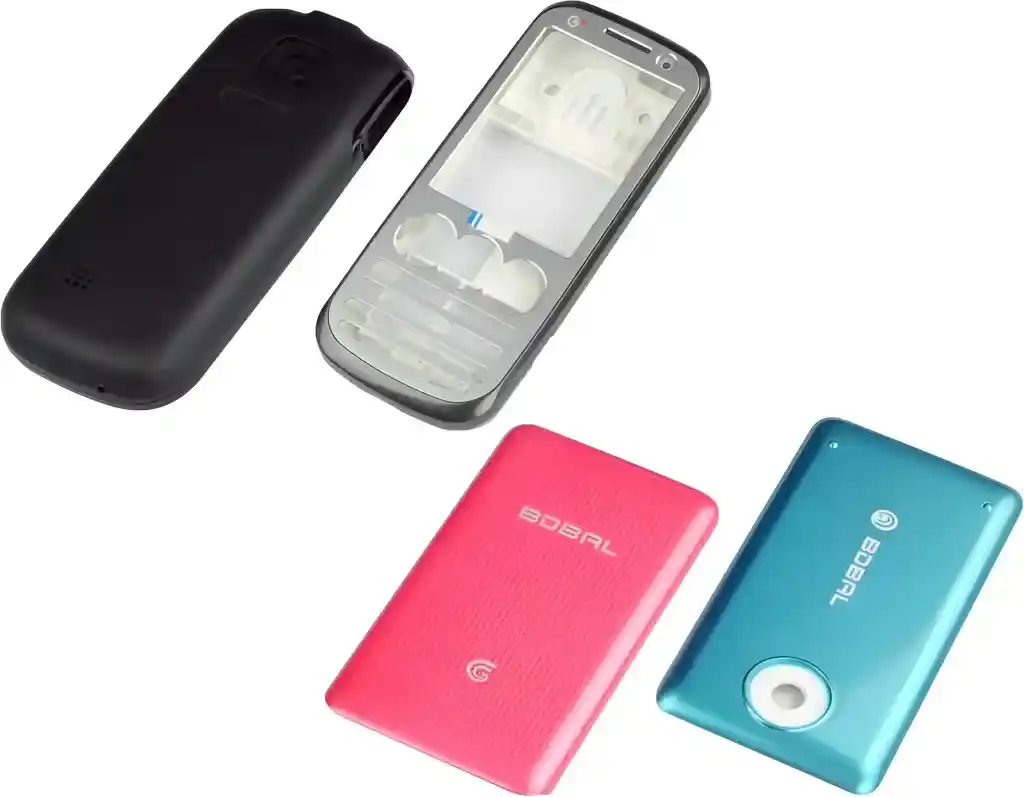
- Prototyping: Vacuum casting is excellent for creating prototypes with the look and feel of the final product. It’s ideal for design validation and user testing.
- Very Low Production: It’s cost-effective for producing small quantities (5-100) of parts with fine surface finishes.
- Smooth Surface and Net-Shape Excellence: Vacuum casting excels at creating parts with smooth surfaces and achieving net-shaped components that require no further machining or post-processing.
3D Printing
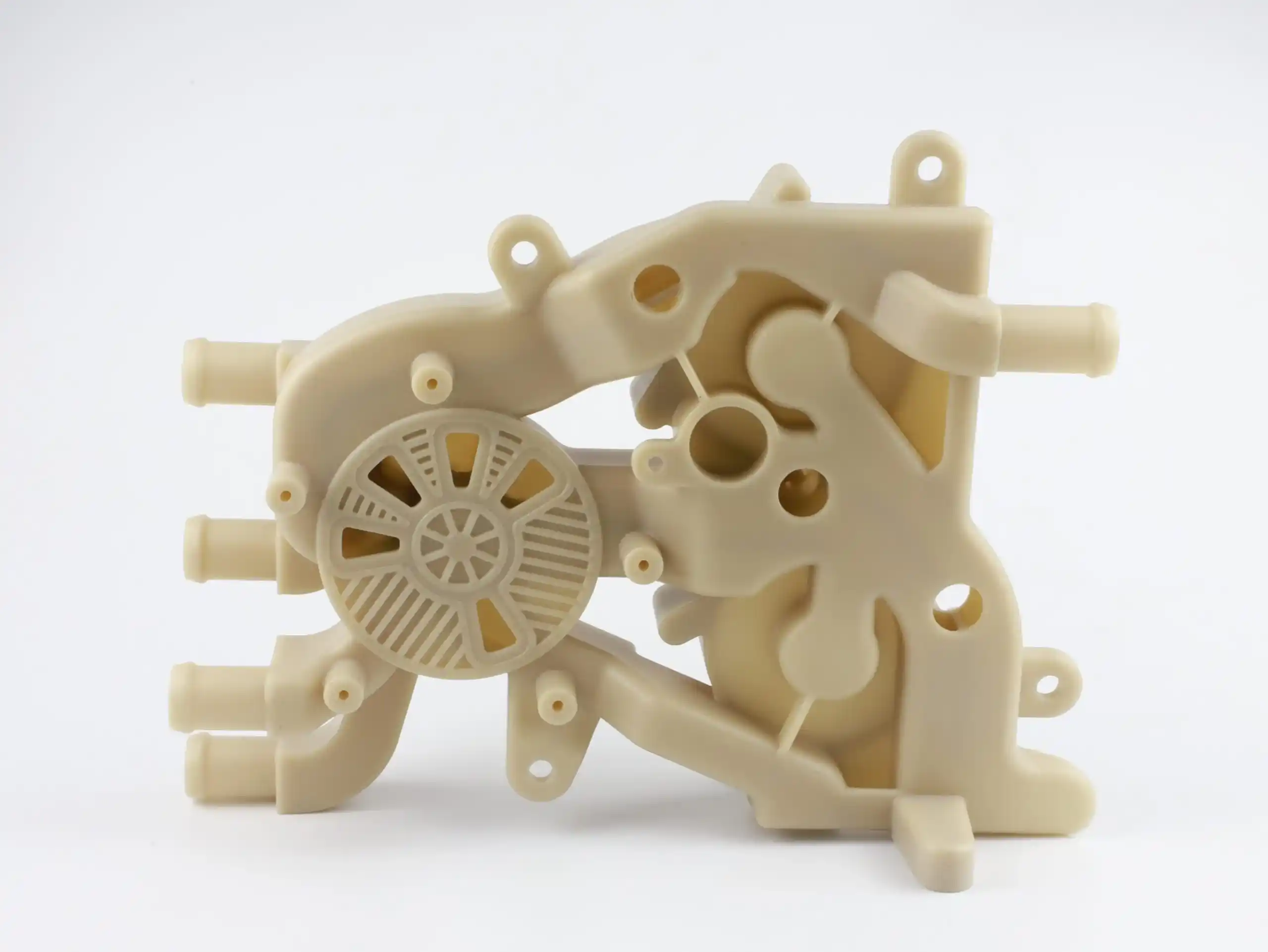
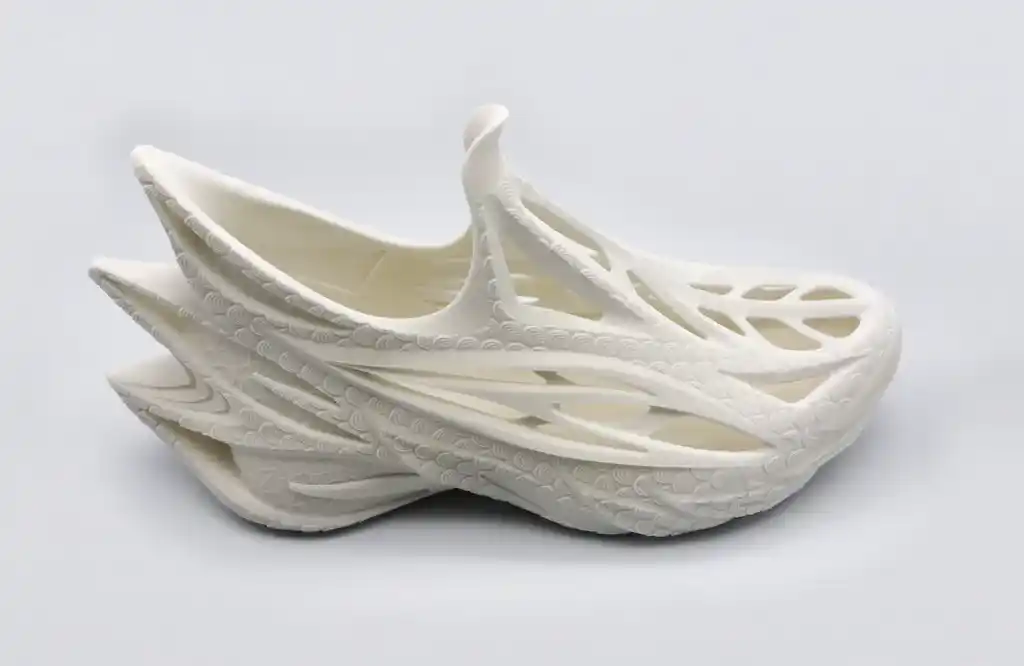
- Rapid Prototyping: 3D printing shines in the rapid prototyping stage, allowing quick iterations and design validation.
- Customization: Perfect for creating unique, one-off parts or personalized products.
- Complex Geometries: Suited for intricate and complex geometries that may be challenging for traditional manufacturing methods.
CNC Machining
- High Precision: CNC machining is known for its high precision and tight tolerances, making it ideal for critical parts.
- Medium to High Volume Production: Efficient for producing medium to high quantities of parts with consistent quality.
- Wide Material Selection: Works with a wide range of materials, including metals, plastics, and composites.
Conclusion
Choosing the right manufacturing process depends on your specific project requirements:
- For Affordable Prototyping and Very Low Volume (5-100) Production, consider vacuum casting for cost-effective replication of detailed parts and 3D printing for rapid iterations and customization.
- For High Precision and Medium to High Volume Production, CNC machining excels in producing accurate, high-quality parts efficiently.
- Complex Geometries and Customization are strengths of 3D printing, making it suitable for unique, intricate designs.
- Additionally, for High-Volume Production Runs, injection molding leverages economies of scale to achieve cost-effective manufacturing.
Unionfab’s Manufacturing Expertise
If you’re looking for a reliable and experienced partner to bring your designs to life, consider Unionfab’s comprehensive manufacturing services.
With a focus on precision and quality, Unionfab offers a wide range of production solutions, including CNC machining, 3D printing, vacuum casting and injection molding.
Explore Unionfab’s services today to achieve your project goals with confidence!