This article outlines 3D printing of automotive parts, examining the production process and advantages and exploring applications.
Introduction
3D printing allows for the creation of complex objects directly from a digital file, offering a whole new level of design flexibility and production speed. From concept cars to custom repairs, 3D printing is revolutionizing the automotive industry.
Understanding 3D Printing Automotive Parts
What is 3D Printed Automotive Parts
3D printed automotive parts are components created for cars and other vehicles using a 3D printing process. This process builds the part layer by layer from a digital 3D model, unlike traditional manufacturing methods that involve carving, molding, or casting.
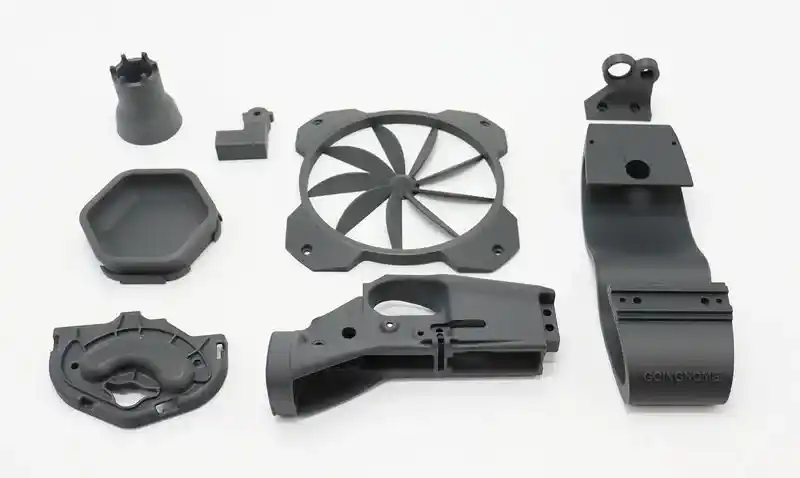
Source: top3dshop.com
Types of 3D Printing Technologies for Auto parts
Several 3D printing technologies are used for automotive parts, each with its own advantages and limitations.
- Fused Deposition Modeling (FDM): The most common method, uses spooled filament that’s melted and deposited layer by layer. It’s affordable but materials like ABS plastic might not be strong enough for all applications.
- Selective Laser Sintering (SLS): Uses a high-powered laser to fuse together powdered materials like nylon or metal. Offers better strength and heat resistance compared to FDM.
- Stereolithography (SLA): Employs a laser to cure liquid resin into solid layers, resulting in smooth and highly detailed parts. Often used for prototyping due to higher cost per part.
- Multi-jet Fusion (MJF): This industrial technology uses inkjet printing to deposit and fuse together layers of powdered plastic. MJF offers high production speed and good mechanical properties.
- Selective Laser Melting (SLM): Uses a laser to melt and fuse metal powder together, layer by layer. This creates strong, complex metal parts for the automotive industry, like pistons, brackets, and other functional prototypes for testing.
3D Printing Technologies for Automotive Parts
Technology | Process | Advantages | Limitations | Common Applications in Automotive |
---|---|---|---|---|
FDM | Melts and deposits spooled filament | Affordable, good for complex geometries | Lower strength, limited materials | Interior parts |
SLS | Laser fuses powdered materials | High strength, heat resistance | Expensive, limited part size | Brackets, engine components, functional prototypes |
SLA | Laser cures liquid resin | High precision, smooth finish | Limited strength, brittle materials | Concept car parts |
MJF | Inkjet printing fuses powdered plastic | High production speed, good mechanical properties | Requires specialized equipment | Functional prototypes |
SLM | Laser melts metal powder | Unmatched strength, complex geometries | High cost, surface finish limitations | High-performance engine components, functional prototypes |
Why 3D Print Automotive Parts
Rapid Prototyping and Iteration
3D printing allows for quick and iterative design exploration. Designers can create a digital model, print a prototype, test it, and make adjustments rapidly, significantly accelerating the development process.
Low-Volume Production
3D printing eliminates the need for complex tooling, making it cost-effective for producing limited-run parts, such as those for classic cars or specialty vehicles.
Design Flexibility and Customization
Traditional manufacturing requires significant adjustments to produce customized parts. 3D printing offers unmatched design freedom and allows for easy customization of parts for specific applications or even individual vehicles.
Common Materials of 3D printed Auto Parts
3D printing offers a diverse range of technologies, each with compatible materials best suited for specific applications in the automotive industry.
Fused Deposition Modeling (FDM)
- ABS (Acrylonitrile Butadiene Styrene): Affordable, good strength, various colors available. Common for prototypes and low-stress interior parts (trim pieces, knobs).
- Nylon 12 Carbon-filled: Offers better strength and heat resistance compared to ABS. Suitable for some functional parts with moderate stress (brackets, housings).
- Polycarbonate (PC): Strong, impact-resistant, and somewhat heat-resistant. Can be used for some functional parts requiring a balance of properties.
Selective Laser Sintering (SLS)
- Polyamide (PA) Powders: (e.g., Nylon PA12) Offer good strength, durability, and heat resistance compared to FDM materials. Used for functional parts (brackets, engine components) and high-quality prototypes.
- Aluminum Alloys: Enable creation of lightweight yet strong metal parts for applications requiring high-stress performance (e.g., brackets).
Stereolithography (SLA)
- High-Performing Resins: Resins like Somos® PerFORM and Somos® Taurus offer a compelling combination of strength, stiffness, and high-temperature resistance. These materials are lighter than metals, making them ideal for structural brackets, ducts, and heat-resistant components like headlamp housings.
Multi-Jet Fusion (MJF)
- Polyamide (PA) Powders: Similar to SLS, offering good strength, heat resistance, and detail compared to FDM parts. Suitable for functional parts with moderate stress (interior components, brackets).
Selective Laser Melting (SLM)
- Stainless Steel: A common choice for its overall strength, corrosion resistance, and suitability for various automotive applications (engine components, high-stress brackets).
- Aluminum Alloys: Offer a lightweight alternative to stainless steel, useful for applications requiring strength and weight reduction (brackets, some engine components).
- Titanium Alloys: High-strength, lightweight option used for high-performance parts requiring exceptional durability (e.g., racing components).
Advantages of 3D Printing in Automotive Parts
Design Flexibility and Complexity
3D printing allows for the creation of complex geometries with internal channels, lattices, and intricate shapes, which is beneficial to innovative designs that can improve performance.
Additionally, 3D printing enables the integration of multiple parts into a single, lighter, and more efficient component.
Rapid Prototyping and Iterative Development
Traditional prototyping can be slow and expensive, requiring specialized tooling and machining.
3D printing allows for rapid creation of functional prototypes directly from a digital model. Designers can quickly iterate on designs, test them, and make adjustments, significantly accelerating the development process.
This reduces the time and cost associated with bringing new car models to market and ensures optimal performance before mass production.
Customization and Personalization Options
3D printing allows for the creation of parts tailored to specific needs and can be used to create replacement parts for obsolete vehicles where traditional manufacturing may no longer be feasible.
Reduction in Material Waste and Weight Optimization
Traditional manufacturing often generates significant scrap material during machining or molding processes. 3D printing builds parts layer by layer, using only the necessary material. This reduces waste and allows for lightweighting of parts.
Applications of 3D Printing in Automotive Parts
Low-volume Parts
Traditional manufacturing often struggles with small production runs due to the high cost of tooling. 3D printing eliminates this barrier, making it cost-effective to produce limited-run parts.
- Classic car parts: Replacing or recreating parts for older vehicles where traditional manufacturing may no longer be viable.
- Specialty vehicles: Producing parts for limited-edition cars or vehicles with unique configurations.
- Prototyping and testing: Creating small batches of parts for testing and development before mass production.
Custom Parts
3D printing allows for the creation of parts tailored to specific needs.
- Racing: Teams can print custom components for improved performance, such as lightweight air intake manifolds or aerodynamic parts.
- Customization: Car enthusiasts can personalize their vehicles with unique interior trim pieces, spoilers, or other aesthetic elements.
- Disability modifications: Creating custom control knobs, steering wheel adaptations, or other parts to enhance accessibility for drivers with disabilities.
Assembly Line Tooling
3D printing can also be used to create tools and jigs used on the assembly line.
- Custom jigs and fixtures: These can be 3D printed to hold parts in place during assembly, welding, or quality control, ensuring precision and efficiency.
- Ergonomic tools: 3D printed tools can be customized to fit the worker’s hand size and grip, reducing fatigue and improving worker safety on the assembly line.
Customized & Replacement Parts
3D printing is increasingly used for customizing and replacing functional parts:
- Interior components: Lightweight and customizable dashboards, center consoles, or trim pieces can be produced using 3D printing.
- Functional parts: Brackets, engine components, and even air intake manifolds with intricate internal structures are becoming viable for 3D printing.
- Concept car parts: Functional parts can be 3D printed for concept cars, enabling real-world testing and validation.
Conclusion
3D printing is rapidly transforming the automotive industry, offering a faster, more flexible, and potentially more sustainable approach to car parts.
From rapid prototyping and low-volume production to custom parts and even functional components, 3D printing’s applications are diverse and constantly evolving.
Craft Your Dream Ride with Unionfab’s 3D Printing
Transform your car into a one-of-a-kind masterpiece. Unionfab’s cutting-edge 3D printing technology and unparalleled expertise unlock a world of customization possibilities.
We’ll partner with you to bring your vision to life, from concept to creation. Make your car truly yours and elevate your automotive journey – contact Unionfab today.
