- Introduction
- How 3D Printing Enables Complex Automotive Geometries
- How 3D Printing Accelerates Automotive Manufacturing Processes
- Facilitating Automotive Customization with 3D Printing
- 3D Printing Methods and Applications for Automotive Manufacturing
- The Future of Automotive Industry with 3D printing
- Conclusion
- Unionfab: Fine-Tuned for the Future of Automotive Manufacturing
Discover how 3D printing is changing the automotive industry by enabling the production of complex geometries, reducing lead times, and allowing for greater customization.
Introduction
The automotive industry is rapidly adopting 3D printing, also known as additive manufacturing (AM), to transform design and manufacturing workflows. 3D printing builds up components layer-by-layer, offering new capabilities compared to traditional subtractive techniques like machining or injection molding.
Key Benefits of 3D Printing for Automotive
- Design freedom for complex geometries
- Faster iteration through rapid prototyping
- Reduction of lead times and tooling costs
- Facilitation of mass customization
As we’ll explore, these benefits are driving increased adoption across concept modeling and production applications.
How 3D Printing Enables Complex Automotive Geometries
One of the biggest advantages of 3D printing is the ability to fabricate complex geometries unattainable through conventional manufacturing methods.
Lightweighting Automotive Parts with Lattices
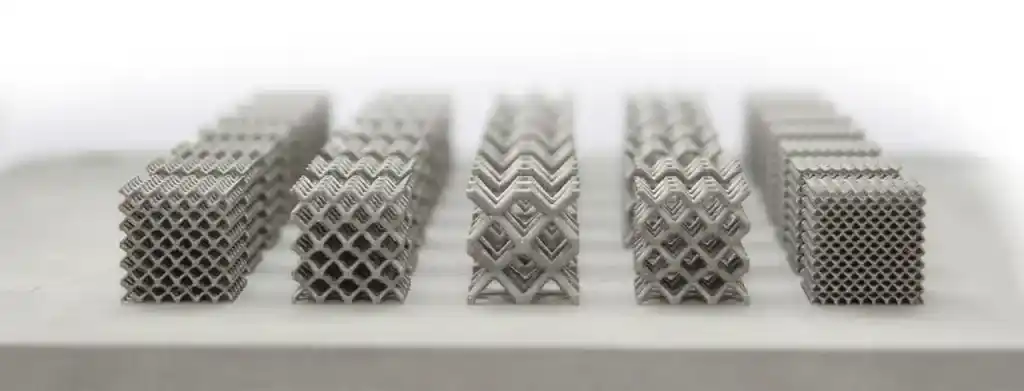
3D printed lattice structures. Source: 3dprinting.com
By creating hollow or lattice structures, 3D printing can reduce the weight of parts without compromising their strength or durability. This can improve fuel efficiency, acceleration, and handling of vehicles.
3D Printed Cooling systems
By creating internal channels within parts, 3D printing can improve the cooling and heat dissipation of engines, batteries, and electronics. This can enhance the performance and lifespan of these components.
Improved Aerodynamics with 3D Printing
3D printing can improve vehicle aerodynamics, reducing drag and noise by creating organic shapes and smooth surfaces. This can increase the speed and comfort of the driving experience. Not to mention that this is a very useful feature for racing cars.
Multi-Material Components
Mixing different materials within a single print allows tailored material properties and gradients.

3D Printed Multi-material car light cover. Source: Stratasys
For example, Audi has adopted Stratasys’ J750 full-color, multi-material 3D printer to prototype automotive parts like tail light covers. This printer mixes different materials and colors in one print. Audi uses it to print entire tail light covers as a single part with smooth color gradients, whereas previous methods required multi-part assemblies. For some parts, the J750 enables 50% faster prototyping compared to previous milling and molding methods.
How 3D Printing Accelerates Automotive Manufacturing Processes
3D printing is providing significant time and cost savings at multiple points in automotive manufacturing workflows.
Faster Design Iteration and Prototyping
Rather than waiting weeks for machine-tooled prototypes, automakers can leverage 3D printing to create design prototypes in days or even hours. This enables rapid iteration to evaluate and improve designs faster.
Prototypes can be printed on-demand to test new design concepts or variations without delays. This agility helps bring vehicle designs to market faster.
Reduced Need for Specialized Tooling
Conventional manufacturing relies on custom molds, dies, and other specialized tooling tailored to each component. This tooling is expensive and time-consuming to produce.
3D printing eliminates the need for custom tooling by printing parts directly from digital files. This removes the overhead time and cost associated with tooling, especially beneficial for prototyping and low-volume production scenarios.
Streamlined Small Batch Production
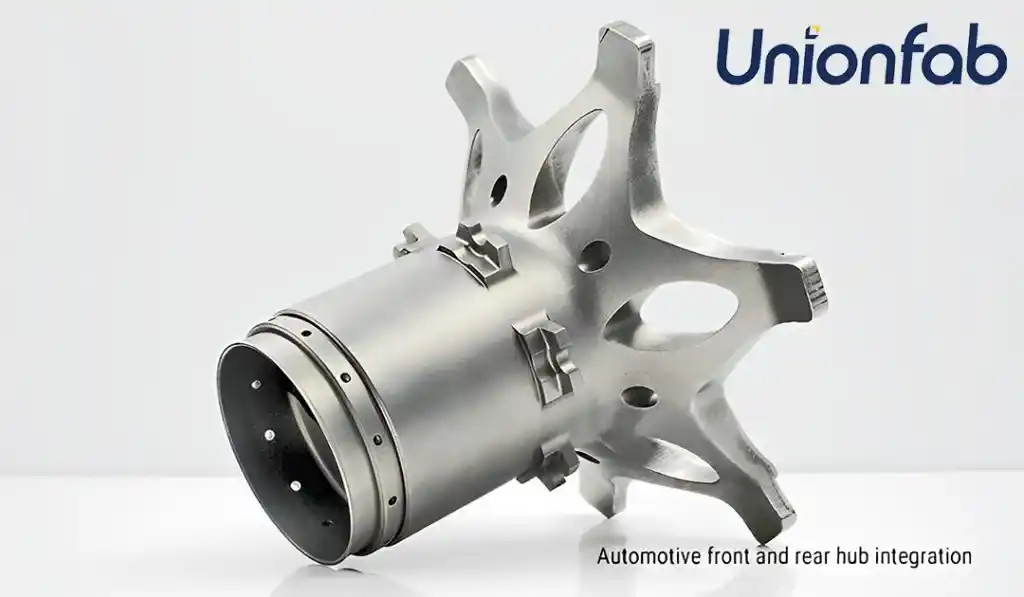
3D printed metal parts for automotive. Source: Unionfab
On-demand 3D printing enables cost-effective short run production, whether hundreds or thousands of units, without dedicating capital to tooling. This makes it economical to produce replacement and aftermarket components in smaller batches.
For limited edition and specialty vehicles produced in lower volumes, 3D printing can supply certain customized components just-in-time.
Facilitating Automotive Customization with 3D Printing
3D printing makes it simpler for automakers to offer customization options for vehicle interiors and exteriors. Unlike traditional methods that are limited by standard sizes, shapes, or colors, 3D printing can create parts that are tailored to the specific needs or preferences of customers or users.
Functional customization with 3D Printing
By using 3D printing, automotive manufacturers can create parts that are optimized for specific functions or performance criteria. For example, they can create parts that are more durable, flexible, resistant, or responsive to different environments or conditions.

Rolls Royce showcased a number of metal 3D printed components. Source: Rolls Royce
Rolls-Royce’s 3D printed parts and innovative materials led to engine test success, optimizing specific functions and performance. The use of 3D printing allowed for complex designs, enabling customized components that enhanced aerodynamics and engine efficiency. A carbon-titanium bracket was created using 3D printing, replacing traditional parts and reducing weight by 40%. Additionally, a redesigned nickel alloy turbine blade was manufactured, improving engine temperature resistance.
Aesthetic customization with 3D Printing
By using 3D printing, automotive manufacturers can create parts that are customized to the individual tastes or styles of customers.
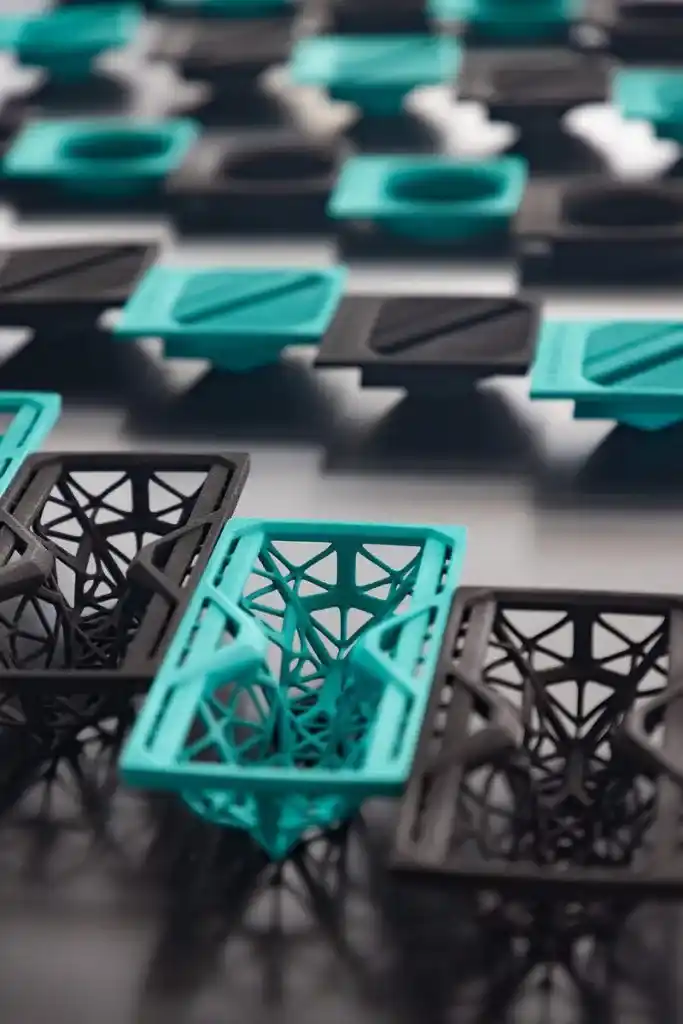
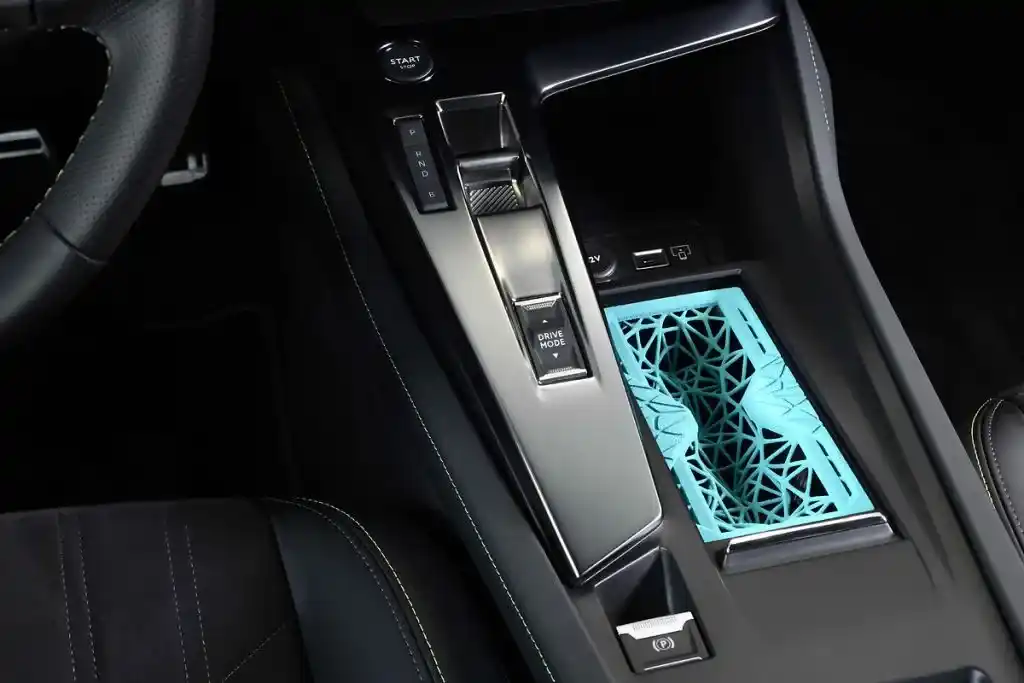
3D printed car accessory. Source: Peugeot
For example, French automaker Peugeot has been leveraging 3D printing technology to rapidly prototype and assess innovative interior designs. Their 3D printed interior components exhibit tailored geometry not feasible with conventional techniques.
User customization with 3D Printing
By using 3D printing, automotive manufacturers can create parts that are adapted to the specific needs or preferences of users. For example, they can create parts that have different sizes, shapes, or features to fit different body types or preferences.
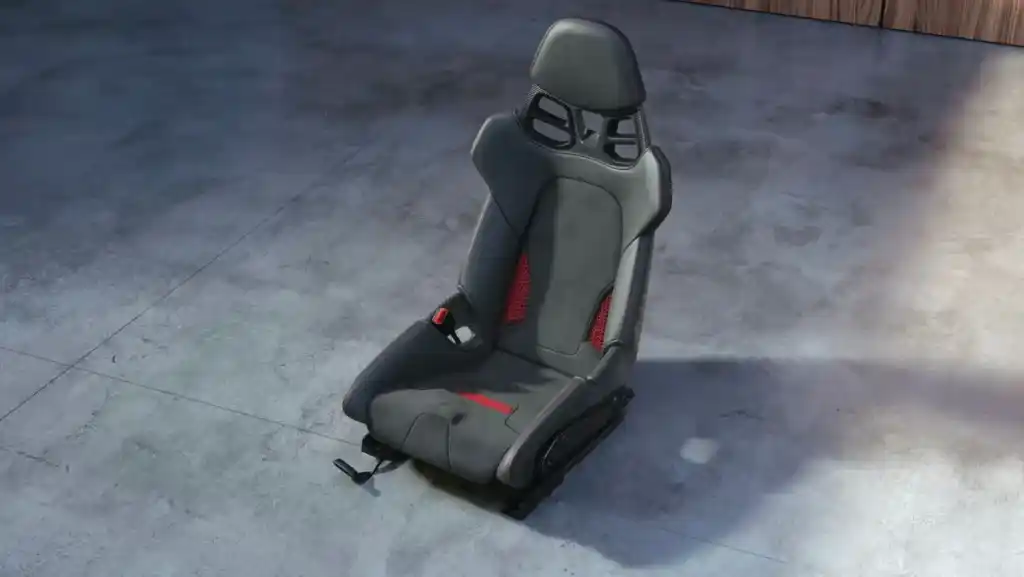
3D-print bodyform full bucket seat. Source: Porsche
One example of this is Porsche’s plan to expand seat customization beyond firmness and color by personalizing the seat to customer’s specific body contour. 3D printing remains the only technology that can enable this level of customization.
3D Printing Methods and Applications for Automotive Manufacturing
- Stereolithography (SLA) and Digital Light Processing (DLP): These vat photopolymerization techniques use ultraviolet light to selectively cure liquid resin into parts layer-by-layer. The high precision and smooth surface finish make SLA and DLP ideal for visual concept models and sand casting patterns for metal parts.
- Fused Deposition Modeling (FDM): FDM printers build parts by heating and extruding thermoplastic filament. Durable engineering-grade thermoplastics like ABS make FDM suitable for lightweight functional prototypes of interior trim, ductwork, and mounting components.
- Selective Laser Sintering (SLS): SLS uses a laser to fuse powdered nylon material into finished parts. The ability to produce durable, functional prototypes without supports makes SLS useful for ducts, brackets, and housings that require thermal stability.
- Selective Laser Melting (SLM): SLM uses a focused laser to melt and fuse metallic powder into fully dense components layer by layer. SLM’s exceptional accuracy and material properties enable direct metal printing of sturdy functional prototypes and production-quality metal parts.
- Reaction Injection Moulding (RIM): RIM is a plastic molding process that involves the mixing of two reactive liquid components (polyols and isocyanates) in a low-pressure mixing head, followed by injection into a mold cavity. RIM is commonly used to manufacture automotive bumpers and body panels, interior trim components like dashboard covers, door panels, and center consoles, and structural components.
The Future of Automotive Industry with 3D printing
As 3D printing technology continues advancing, expectations are for increased adoption by automakers to transform design and production. The Global Automotive 3D Printing Market size is expected to be worth around USD 15.8 Billion by 2032 from USD 2.2 Billion in 2022, according to Market.us.
Wider implementation for end-use parts is anticipated as 3D printing becomes faster and costs decline.
However, some challenges remain to be overcome before 3D printing sees mainstream use in high-volume automotive manufacturing:
- Print speed and throughput must improve for mass production scenarios. Hybrid manufacturing combining 3D printing and conventional methods can help address this.
- Material properties and performance requirements for structural and safety-critical components must meet stringent automotive standards through advances in metals, polymers and composites.
- Production costs need to decrease further to be competitive, especially for metal 3D printing. This is expected as additional competition drives prices lower.
- Design software and workflow integration is required for seamless design-to-manufacturing with 3D printing. Automated optimization tools can simplify adoption.
3D printing unlocks new design freedoms and customization opportunities while conventional techniques remain ideal for high volumes. Blending 3D printing’s flexibility with the efficiency of injection molding, stamping and casting will characterize the factories of tomorrow.
Conclusion
As 3D printing adoption accelerates, it will continue revolutionizing automotive design and manufacturing.
While initially used for prototyping, wider implementation for end-use production is expected as the technology advances. 3D printing provides the flexibility needed for the auto industry to offer on-demand customization while optimizing performance.
3D printing is not likely to fully replace conventional automotive manufacturing methods but rather complement them. Hybrid approaches maximizing the advantages of both will drive future production.
Unionfab: Fine-Tuned for the Future of Automotive Manufacturing
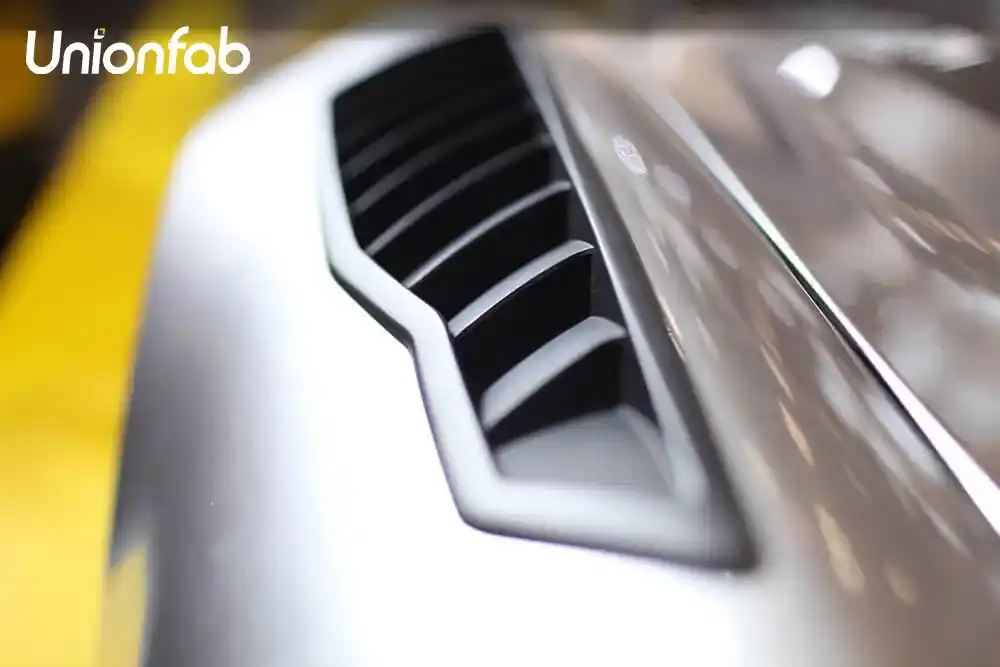

3D printed air duct for Mercedes-Benz. Source: Unionfab
Unionfab provides comprehensive 3D printing solutions to accelerate automotive manufacturing processes – from design to production.
Our capabilities for automotive customers include:
- Agile Prototyping – We 3D print concept models, tooling, and functional prototypes in days rather than weeks using the optimal technologies.
- Low-Volume Production – Our fleet of industrial 3D printers enables economical short run manufacturing aligned with automaker needs.
- Customization – Multi-material printing facilitates personalization and production of specialized parts.
With over 800 systems spread spanning across six factories, Unionfab delivers the capacity, expertise and technologies to accelerate automotive manufacturing initiatives across the product lifecycle.