Thingiverse is one of the most popular sites to download free 3D printer files. While nylon has become a popular material to use with 3D printers. 3D printing provides the added benefits of unlimited geometries, iteration and customization, and low-volume affordability.
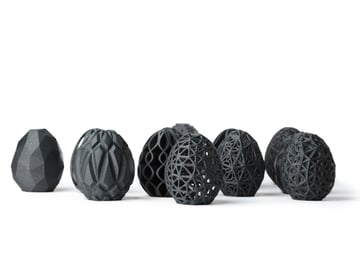
Thingiverse is renowned in the 3D printing world as a great site for finding free models. It features thousands of files, many of which were created by incredible creators and designers, so you’ll likely find something that suits your taste.
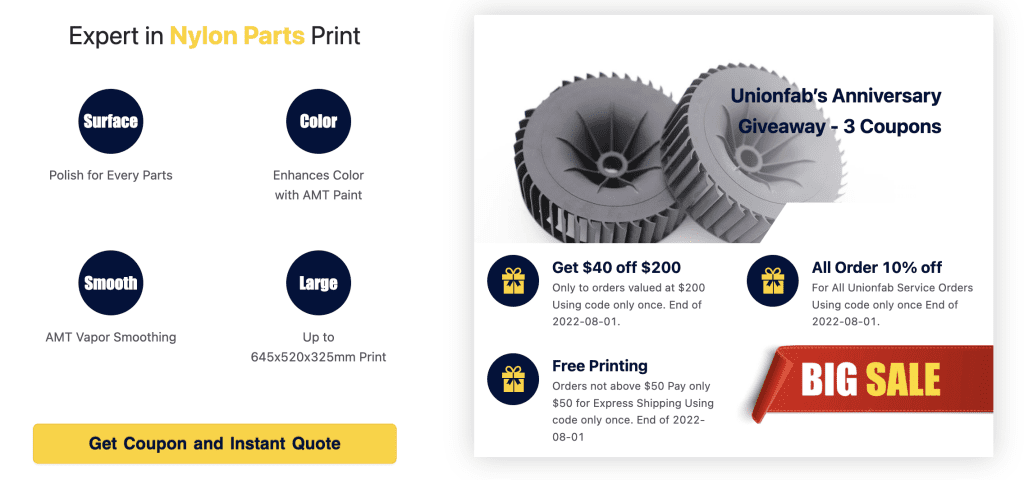
When it comes to 3D printing materials, Nylon has to be mentioned as one of the most popular materials for professional users. This can be attributed in large part to its popularity outside of 3D printing. Nylon has a wide range of applications thanks to its unique properties and the benefits of 3D printing mean that parts can be made on the fly easily and inexpensively.
UNDERSTANDING NYLON AS A MATERIAL
Chemical Composition
Nylon was first synthesized by DuPont, the American chemical company, in 1935. It developed the material for commercial usage and since then Nylon has become a common feature in numerous industries.
Nylon refers to a group of plastics known as polyamides. They are mostly semi-crystalline and generally very tough materials. It is found in many variants but the most common ones are Nylon 6, Nylon 6-6, and Nylon 12. It is a thermoplastic material, i.e., it becomes soft on heating or liquid when heated beyond its melting point and hardens on cooling. This process of heating and cooling can be carried out multiple times without significantly affecting its inherent chemical or mechanical properties.
Nylons can be easily blended with numerous other plastics to form composites, enhancing their performance parameters. This is widely done in automotive industries and some common composites in 3D printing are glass-filled nylon and carbon-fiber-filled nylon. Nylon is a versatile material and is suitable for almost all types of manufacturing operations like injection molding, extrusion, and additive manufacturing (in FDM, SLS & MJF).
NYLON IN 3D PRINTING
In the same way that nylon has become a go-to material in traditional manufacturing, nylon has become a popular material to use with 3D printers. 3D printing provides the added benefits of unlimited geometries, iteration and customization, and low-volume affordability.
Nylon’s flexibility and durability help in 3D printing parts with thin walls. Its low coefficient of friction with a high melting point makes it especially resistant to abrasion and enables it to be used in printing for parts such as functional interlocking gears.
Nylon exhibits mechanical properties comparable to ABS (another widely used material in traditional & additive manufacturing). ABS is defined by its strength but Nylon’s resistance to wear and fatigue makes it superior for applications requiring such properties.
Apart from the advantages, nylon has one major drawback that can often hamper its printing performance – hygroscopicity, i.e., its moisture absorption property. This property is detrimental in delivering predictable performance. But this same property helps nylon in easy post-processing with fabric dyes and spray paints thereby making it suitable for use in the printing of aesthetic (display) models.
There have been successful cases of a patient receiving a titanium pelvis implant, another getting a new titanium lower jaw. A motorcyclist patient whose face had been seriously injured in a road accident had it rebuilt with 3D printed parts.
Bioprinting allows for the 3D printing of artificial organs, helping solve organ failure issues in patients faster, important to both the patient and his/her family and to healthcare systems.
3D printed tissues have been developed for pharmaceutical testing as a cost-effective and ethical means of helping identify the side effects of drugs and validating safe dosages.
ADVANTAGES
➜ Mechanical Properties
➀ High impact resistance – Durable in situations where parts are constantly banging together or being dropped.
➁ Abrasion resistant – Nylon’s low coefficient of friction allows nylon to be used in applications with moving parts that would otherwise wear on each other
➂ Flexible – In thinner geometries nylon can be flexed repeatedly without fracturing
➜ Post-Processing: Nylon is hygroscopic and this property helps it to be easily post-processed by absorbing fabric dyes and spray paints.
DISADVANTAGES
➜ Hygroscopic: Nylon is hygroscopic, i.e., it absorbs moisture from the air which can affect its print quality and ultimately the part performance.
➜ Pre-Drying: Nylon should be pre-dried to remove any moisture it has absorbed. This requires extra effort, extra equipment, and extra time. And if the drying is insufficient, then the print shows
➜ Warping: Nylon is prone to warping and thus can distort the part.
Selective Laser Sintering
In 1989, the American C.R. Dechard developed the SLS technology, which uses powdered materials and is controlled by computer through laser sintering of the material, stacking layers until the final shape is formed.
SLS technology is currently used in high-end manufacturing applications and is concentrated in the foundry industry.
The following is a detailed description of the printing process using SLS technology. A layer of print material is first laid flat, scraped flat, heated to near the melting point and then selectively sintered using a CO2 laser at high definition. The model cannot be removed immediately after completion, it needs to cool for a few hours and then be removed once it has cooled completely.
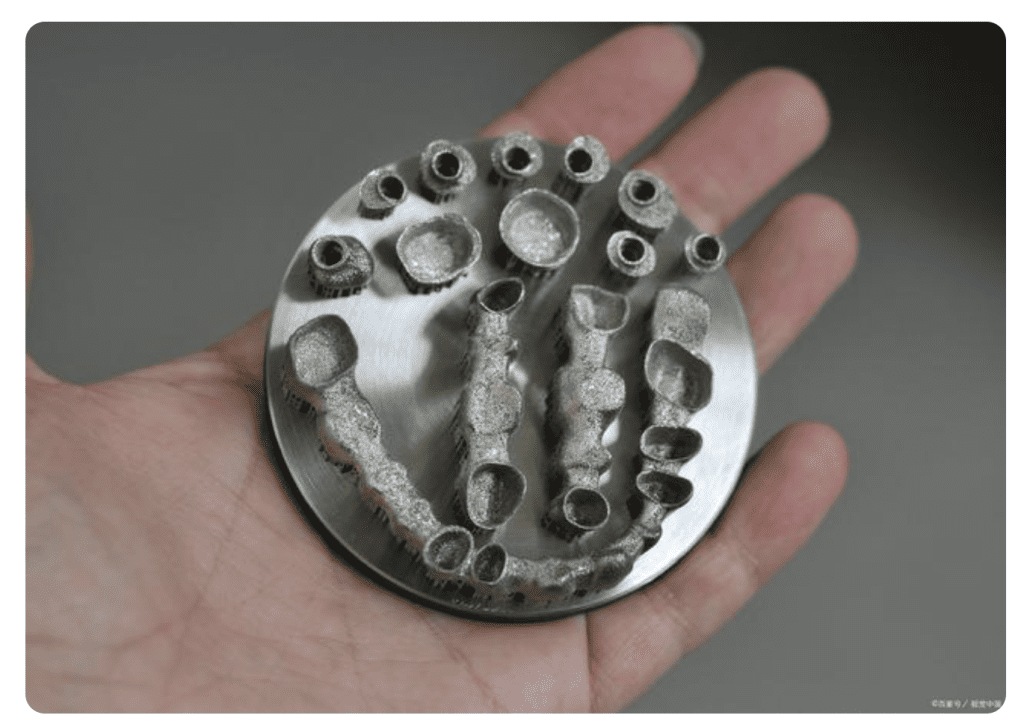
The operational steps are simple to say the least, but in fact the process requires many auxiliary processes and is technically difficult, the preparation alone is time consuming, although the printing speed is very fast, 3-4 cm per hour.
High-powered lasers are used in the printing process, which is expensive to manufacture and maintain, making it difficult to popularise for residential use.
The abundance of forming materials allows SLS technology to print not only metals, but also ceramics, polymer compounds, sand and other materials. Once printed, the un-sintered material can be reused and also acts as a support during the printing process.
Although SLS technology has many advantages, it also has disadvantages that are difficult to address. The laser sintering process produces toxic gases that can cause harm to people and pollution to the environment. To prevent danger, the sintering space has to be continuously filled with nitrogen gas.
The printed product is not very strong and easily deformed, and the surface is rough and requires subsequent processing, which makes it difficult to ensure the accuracy of the finished product.
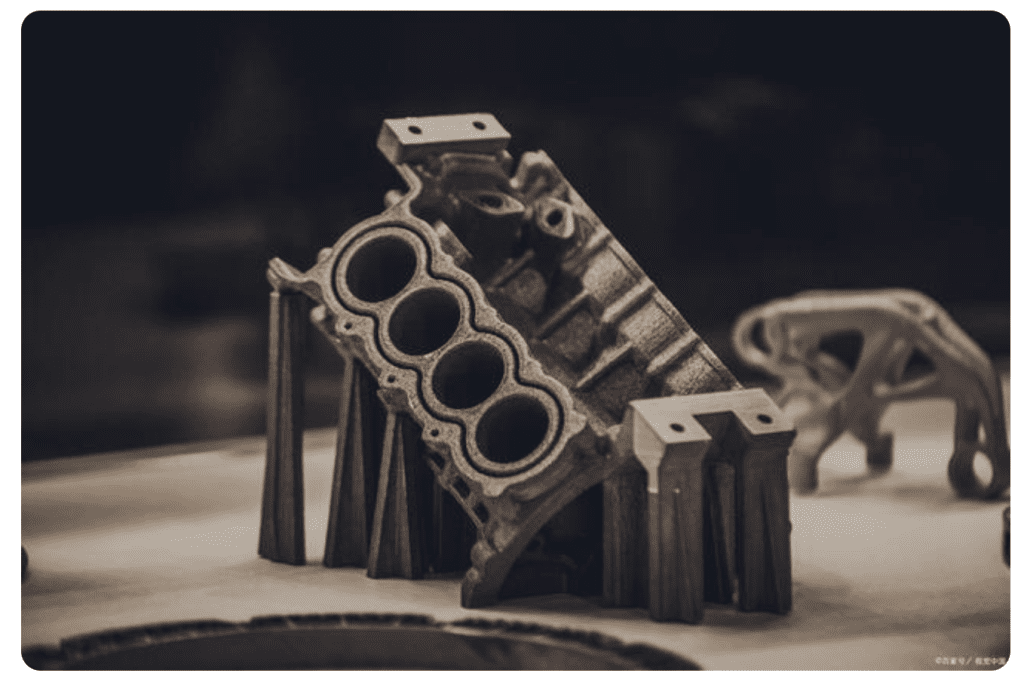